Chalco Aluminum is committed to providing high-quality aluminum tube products. Our aluminum tubes are of various types, covering a variety of specifications and alloys, suitable for various industries such as construction, aviation, and automobiles.
We have tens of thousands of tons of aluminum tubes in stock, accurate quotations, fast delivery, and personalized customization services to meet the various needs of customers.
Specifications of aluminum tubes
By shape: square tube, round tube, embossed tube, profiled tube, globe aluminum tube.
Aluminum tube types: seamless aluminum tube, thin-walled aluminum tube, extruded tube, Ordinary aluminum tube, precision aluminum tube, cold drawn aluminum tube, precision drawn aluminum tube, forged tube.
Chemical treatment: Oxidation, electrophoretic coating, fluorocarbon coating, powder coating, wood grain transfer printing.
Mechanical treatment: mechanical drawing, mechanical polishing, sandblasting.
Surface treatment of aluminum tubes: anodizing, polishing, painting, coating.
Additional services: cutting, welding, punching, bending.
Applicable standards: ASTM B429, ASTM B241, EN 755-2, EN 573-3, EN 754-8, NMX-H-004, NMX-H-065
Popular stock sizes of aluminum tubes
We can customize aluminum tubes of various sizes and specifications. Of course, if you need stock, please contact customer service to update the latest stock list.Quick Quote
Imperial Units Aluminum Tube
Item Size & Description | Weight / Ft. | Length Size | Processing Services |
1/4 OD x .035 wall x .180 ID | 0.03 lb/ft | 12 ft | Cutting, punching, bending, wall expansion, etc. |
3/8 OD x .035 wall x .305 ID | 0.10 lb/ft | 12 ft | Cutting, punching, bending, wall expansion, etc. |
1/2 OD x .049 wall x .402 ID | 0.10 lb/ft | 12 ft | Cutting, punching, bending, wall expansion, etc. |
5/8 OD x .065 wall x .495 ID | 0.14 lb/ft | 12 ft | Cutting, punching, bending, wall expansion, etc. |
3/4 OD x .125 wall x .500 ID | 0.30 lb/ft | 24 ft | Cutting, punching, bending, wall expansion, etc. |
7/8 OD x .065 wall x .745 ID | 0.25 lb/ft | 12 ft | Cutting, punching, bending, wall expansion, etc. |
1 OD x .250 wall x .500 ID | 0.70 lb/ft | 12 ft | Cutting, punching, bending, wall expansion, etc. |
1-1/8 OD x .125 wall x .875 ID | 0.50 lb/ft | 12 ft | Cutting, punching, bending, wall expansion, etc. |
1-1/4 OD x .125 wall x 1.00 ID | 0.53 lb/ft | 24 ft | Cutting, punching, bending, wall expansion, etc. |
1-3/8 OD x .125 wall x 1.125 ID | 0.80 lb/ft | 12 ft | Cutting, punching, bending, wall expansion, etc. |
1-1/2 OD x .250 wall x 1.00 ID | 1.16 lb/ft | 12 ft | Cutting, punching, bending, wall expansion, etc. |
1-5/8 OD x .250 wall x 1.125 ID | 1.25 lb/ft | 12 ft | Cutting, punching, bending, wall expansion, etc. |
1-3/4 OD x .250 wall x 1.25 ID | 1.38 lb/ft | 24 ft | Cutting, punching, bending, wall expansion, etc. |
2 OD x .250 wall x 1.50 ID | 1.62 lb/ft | 24 ft | Cutting, punching, bending, wall expansion, etc. |
2-1/4 OD x .250 wall x 1.75 ID | 1.85 lb/ft | 24 ft | Cutting, punching, bending, wall expansion, etc. |
2-1/2 OD x .750 wall x 1.00 ID | 4.85 lb/ft | 12 ft | Cutting, punching, bending, wall expansion, etc. |
3 OD x .500 wall x 2.00 ID | 4.65 lb/ft | 24 ft | Cutting, punching, bending, wall expansion, etc. |
3-1/2 OD x .250 wall x 3.00 ID | 3.00 lb/ft | 24 ft | Cutting, punching, bending, wall expansion, etc. |
3-3/4 OD x .125 wall x 3.50 ID | 1.67 lb/ft | 24 ft | Cutting, punching, bending, wall expansion, etc. |
4 OD x .125 wall x 3.75 ID | 1.80 lb/ft | 24 ft | Cutting, punching, bending, wall expansion, etc. |
5 OD x .125 wall x 4.75 ID | 2.50 lb/ft | 24 ft | Cutting, punching, bending, wall expansion, etc. |
6 OD x .750 wall x 4.50 ID | 14.55 lb/ft | 24 ft | Cutting, punching, bending, wall expansion, etc. |
8 OD x .750 wall x 6.50 ID | 20.09 lb/ft | 24 ft | Cutting, punching, bending, wall expansion, etc. |
10 OD x .250 wall x 9.50 ID | 9.00 lb/ft | 24 ft | Cutting, punching, bending, wall expansion, etc. |
12 OD x .250 wall x 11.50 ID | 10.84 lb/ft | 12 ft | Cutting, punching, bending, wall expansion, etc. |
12 OD x 2.00 wall x 8.00 ID | 73.90 lb/ft | 10 ft | Cutting, punching, bending, wall expansion, etc. |
Schedule-aluminum-pipe
Schedule pipe is a pipe system classified by wall thickness standards. The larger the number, the thicker the wall thickness. We have common Schedule standards in stock, Sch 5, Sch 10, Sch 20, Sch 40, Sch 80, Sch 120.Quick Quote
Item Size & Description | Sch | Length Size |
.75″ sch 80 Aluminum Pipe | 80 | Customizable, cutting |
1.5″ sch 40 Aluminum Pipe | 40 | Customizable, cutting |
1.5″ sch 80 Aluminum Pipe | 80 | Customizable, cutting |
1.25″ sch 40 Aluminum Pipe | 40 | Customizable, cutting |
1.00″ sch 40 Aluminum Pipe | 40 | Customizable, cutting |
1.00″ sch 80 Aluminum Pipe | 80 | Customizable, cutting |
.5″ sch 40 Aluminum Pipe | 40 | Customizable, cutting |
.5″ sch 80 Aluminum Pipe | 80 | |
.25″sch 40 Aluminum Pipe | 40 | Customizable, cutting |
.125″ sch 40 Aluminum Pipe | 40 | Customizable, cutting |
.125″ sch 80 Aluminum Pipe | 80 | Customizable, cutting |
2.5″ sch 40 Aluminum Pipe | 40 | Customizable, cutting |
2.5″ sch 80 Aluminum Pipe | 80 | Customizable, cutting |
2.00″ sch 40 Aluminum Pipe | 40 | Customizable, cutting |
2.00″ sch 80 Aluminum Pipe | 80 | Customizable, cutting |
3.5″ sch 80 Aluminum Pipe | 80 | Customizable, cutting |
3.00″ sch 40 Aluminum Pipe | 40 | Customizable, cutting |
3.00″ sch 80 Aluminum Pipe | 80 | Customizable, cutting |
.75″ sch 40 Aluminum Pipe | 40 | Customizable, cutting |
.375″ sch 40 Aluminum Pipe | 40 | Customizable, cutting |
4.00″ sch 40 Aluminum Pipe | 40 | Customizable, cutting |
4.00″ sch 80 Aluminum Pipe | 80 | Customizable, cutting |
5.00″ sch 40 Aluminum Pipe | 40 | Customizable, cutting |
6.00″ sch 40 Aluminum Pipe | 40 | Customizable, cutting |
6.00″ sch 80 Aluminum Pipe | 80 | Customizable, cutting |
8.00″ sch 40 Aluminum Pipe | 40 | Customizable, cutting |
Metric Aluminum Tube Sizes
Item Size & Description | Outside Diameter | Length Size |
8mm x 1.5mm Aluminium Tube | 8mm | Customizable, cutting |
10mm x 1mm Aluminium Tube | 10mm | Customizable, cutting |
10mm x 2mm Aluminium Tube | 10mm | Customizable, cutting |
12mm x 2mm Aluminium Tube | 12mm | Customizable, cutting |
15mm x 2mm Aluminium Tube | 15mm | Customizable, cutting |
20mm x 2mm Aluminium Tube | 20mm | Customizable, cutting |
25mm x 2mm Aluminium Tube | 25mm | Customizable, cutting |
30mm x 2mm Aluminium Tube | 30mm | Customizable, cutting |
30mm x 3mm Aluminium Tube | 30mm | Customizable, cutting |
30mm x 5mm Aluminium Tube | 30mm | Customizable, cutting |
40mm x 3mm Aluminium Tube | 40mm | Customizable, cutting |
40mm x 5mm Aluminium Tube | 40mm | Customizable, cutting |
50mm x 1.5mm Aluminium Tube | 50mm | Customizable, cutting |
50mm x 3mm Aluminium Tube | 50mm | Customizable, cutting |
60mm x 3mm Aluminium Tube | 60mm | Customizable, cutting |
60mm x 5mm Aluminium Tube | 60mm | Customizable, cutting |
Popular Aluminum Tube Alloy Series
1000 series aluminum tube
The common alloy of 1000 series aluminum tube: 1050, 1060, 1070.
1 series aluminum is industrial pure aluminum. It has high plasticity, corrosion resistance, electrical conductivity, thermal conductivity and other characteristics.
2000 series aluminum tube
The common alloy of 2000 series aluminum tube: 2014, 2017, 2024, 2A12, 2219, 2A11, 2A14, 2A50.2 series aluminum alloy has good machinability and good performance of contact welding, spot welding and roll welding. However, the performance of electric arc welding and gas welding is poor.
It is applied to occasions requiring high strength and hardness (including high temperature), such as aircraft heavy, forgings, thick plates and extruded materials, wheels and structural elements, first stage fuel tank of multistage rocket and spacecraft parts, truck frame and suspension system parts, etc.
-
2024-aluminum-round-tube
OD: 0.20"-29.37"
Wall: 0.01"-3.94"
Length: customizable
High strength and light weight
-
2024-aluminum-square-tube
OD: 0.20"-20"
Wall: 0.02"-2"
Length: customizable
High strength and light weight
3000 series aluminum tube
It is used for processing parts with good formability, high corrosion and weldability.
-
3003 aluminum tube
OD: 0.125"-0.25"
Wall: 0.025"-0.065"
Length: customizable
excellent corrosion resistance, processing capabilities
-
3003 Cold Drawn (Rolled)
Seamless Tubes
OD: 10-120mm
Wall: 0.5-25mm
Length: 1000-40000mm
good thermal conductivity and electrical conductivity
4000 series aluminum tube
4032 aluminum tubes are widely used in the automotive industry and aerospace due to their high strength and wear resistance. 4047 aluminum tubes are very useful in brazing and welding due to their low melting point and good fluidity, while 4147 aluminum tubes have a place in construction, chemical industry and electrical engineering due to their high heat resistance and corrosion resistance.
5000 series aluminum tube
The common alloy of 5000 series aluminum tube: 5052, 5083, 5086, 5154, 5454, 5456.
5000 series aluminum tube is Al-Mg alloy, which is the most widely used rust-proof aluminum. The alloy has high strength, especially high fatigue strength, strong plasticity, good corrosion resistance, good weldability, poor machinability, and can be polished.
-
5052 O H112 Tubing
OD: 0.125"-13.701"
Wall: 0.02"-1.772"
Length: customizable
low and medium pressure hydraulic systems, fuel lines
-
5083 Aluminum Pipe
OD: 6.693"-9.055"
Wall: 0.394"
Length: customizable
excellent welding characteristics, outstanding corrosion resistance
-
5086-aluminum-pipe
OD: 0.54"-12.75"
Wall: 0.09"-0.69"
Length: customizable
High strength and high corrosion resistance
6000 series aluminum pipe
6000 series aluminum tube is a high-quality aluminum alloy product produced through heat treatment and pre-stretching process. It has many characteristics of magnesium-silicon alloy, excellent processing performance, excellent weldability and electroplating, good corrosion resistance, high toughness, no deformation after machining, dense material without defects, easy to polish, easy to color, excellent oxidation effect and other excellent characteristics.Quick Quote
-
6060 Aluminum Tube
OD: 1-1000mm
Wall: 0.1-100mm
Length: customizable
Excellent machinability
-
6061 Aluminum Tubing
OD: 0.709"-23.622"
Wall: 0.197"-3.937"
Length: customizable
Workability and excellent welding performance
-
6061 T6 Aluminum
Square Tubing
OD: 0.5"-8"
Wall: 0.065"-0.787"
Length: customizable
Easy to process, excellent welding performance
-
6063 T5 T6 Extruded
Aluminum Tubing
OD: 0.236"-23.622"
Wall: 0.039"-0.394"
Length: customizable
Corrosion resistant, easy to heat treat, anodize and weld
-
6063-aluminum-square-tube
OD: 0.394"-7.874"
Wall: 0.039"-0.236"
Length: customizable
Excellent corrosion resistance and processing properties
-
6082-aluminium-tube
OD: 0.236"-6"
Wall: 0.028"-0.5"
Length: customizable
Excellent corrosion resistance
7000 series aluminum pipe
7000 series aluminum alloy is a heat-treatable aviation super-hard aluminum alloy with good wear resistance, extremely high strength and resistance to exfoliation corrosion and stress corrosion cracking. It is commonly used in structural parts such as aircraft extrusions, free forgings and die forgings.
-
7075 Aluminum Tubing
OD: 0.906"-9.843"
Wall: 0.049"-1.575"
Length: 1500-4000mm
low and medium pressure hydraulic systems, fuel lines
We also have aluminum tubes available in other grade and sizes. Feel free to inquire for more information.Quick Quote
Applications of Aluminum Tubes & Pipe
Aerospace Applications Aluminum Tubes
Aluminum aircraft tubing is a type of high-strength, lightweight, and corrosion-resistant aerospace-grade aluminum alloy tubing widely utilized in the aerospace industry. The product standards include AMS 4083, AMS 4086, AMS 4087, and AMS 4088.
With excellent quality, Chalco is a supplier of aerospace aluminum materials to renowned companies like Boeing and Airbus, including Collins Aerospace.
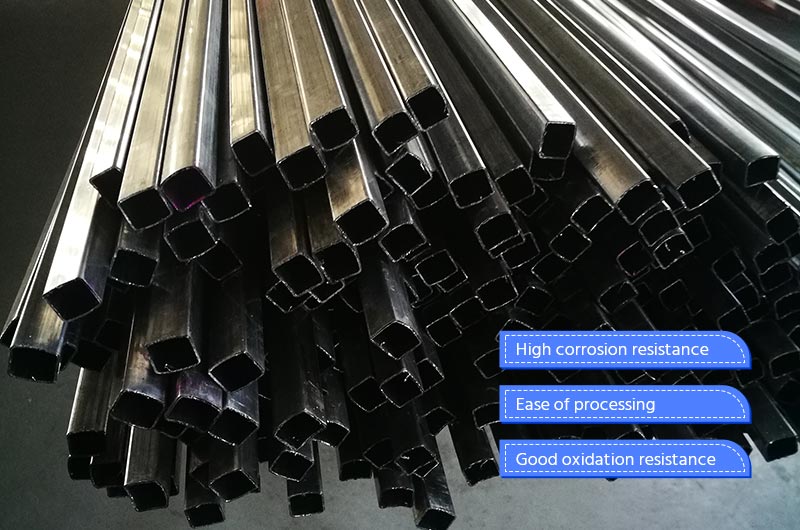
1100 Aerospace Aluminum Tube
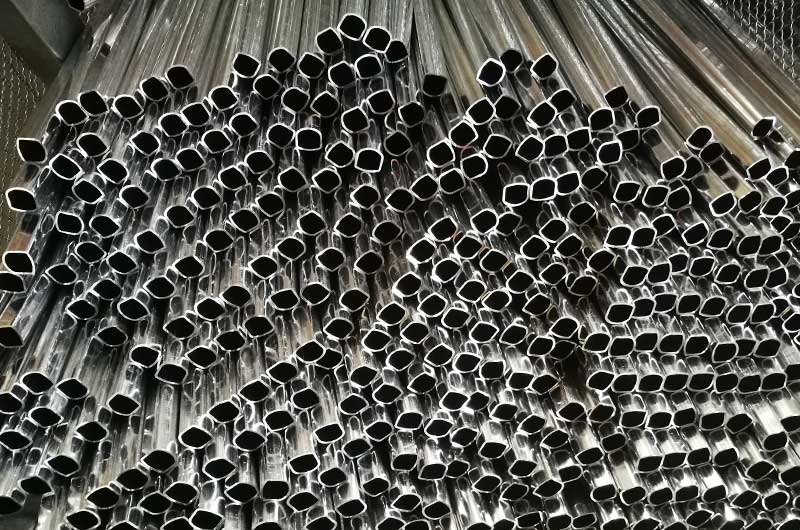
3003 Aircraft Aluminum Tube
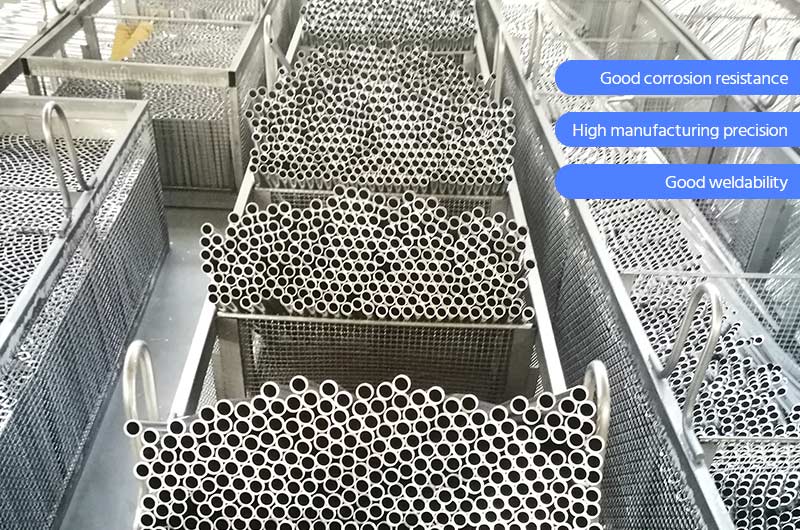
AMS 6061 Aluminum Tube
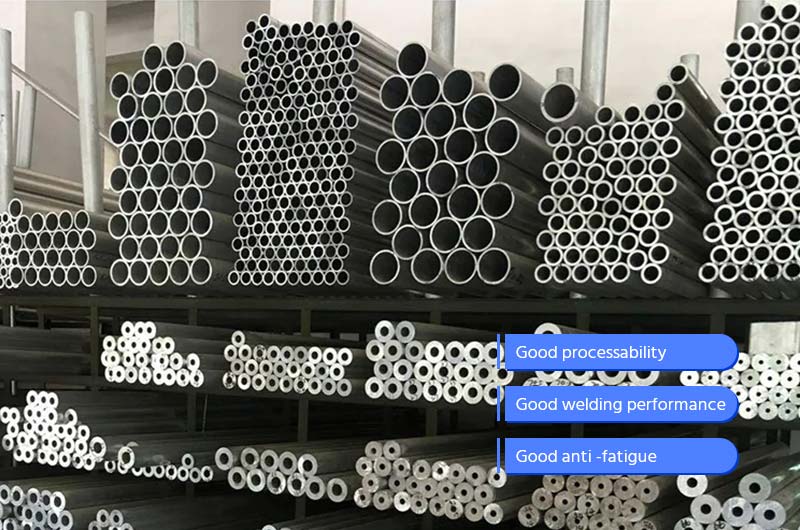
5083 Aerospace Aluminum Tube
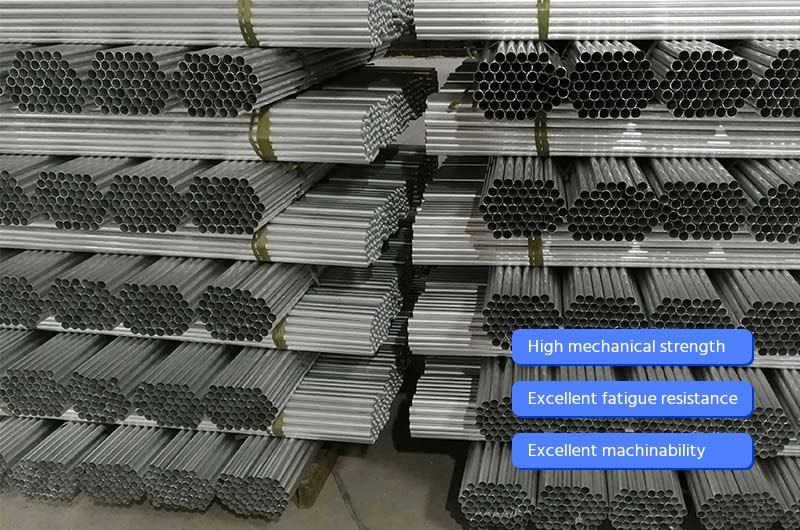
2014A Aerospace Aluminum Tube
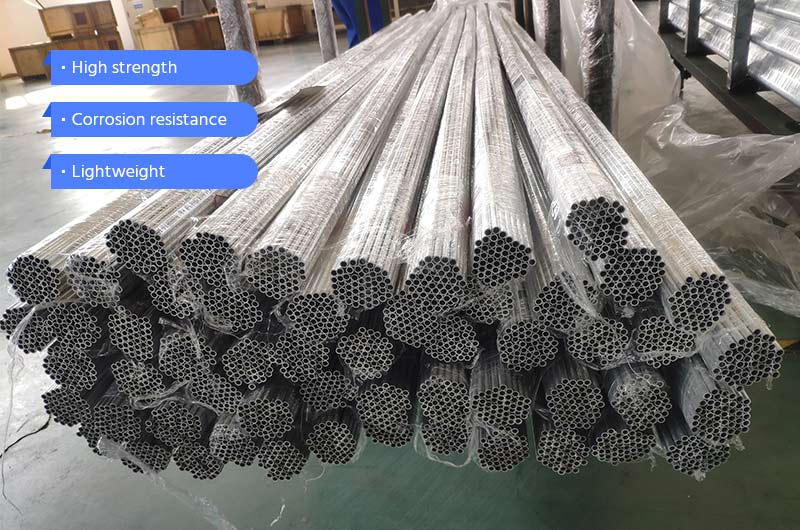
2024 Aircraft Aluminum Tube
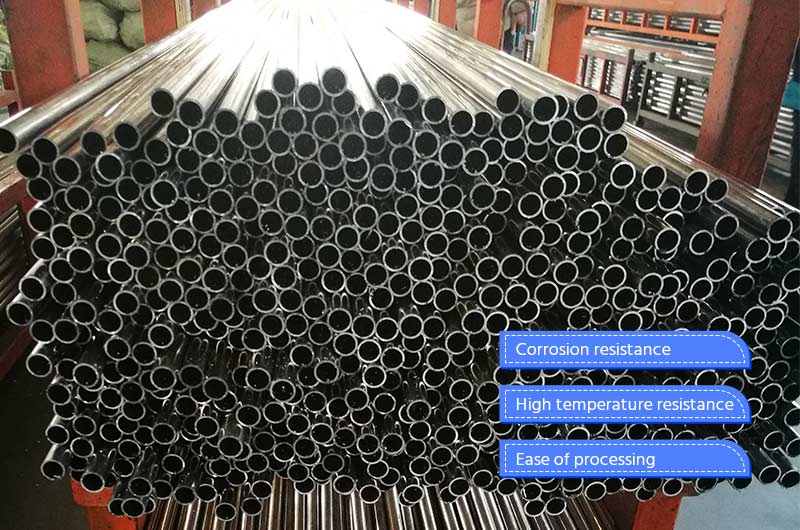
2219 Aircraft Aluminum Tube
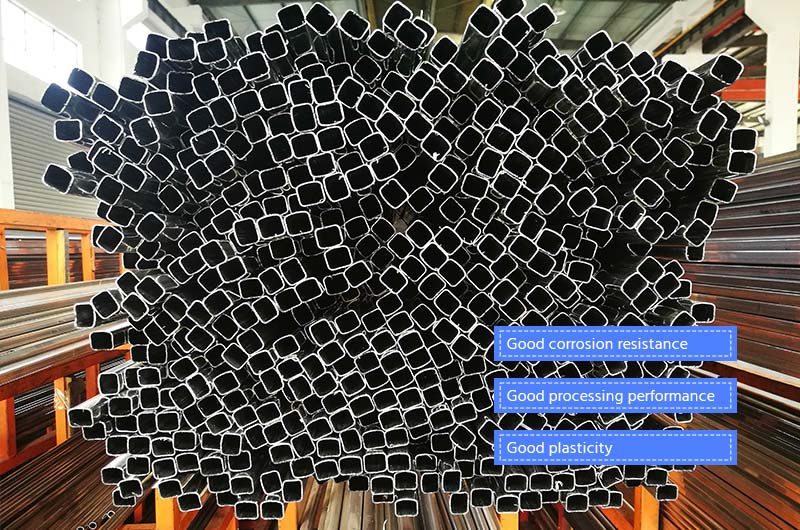
5251 Aircraft Aluminum Tube
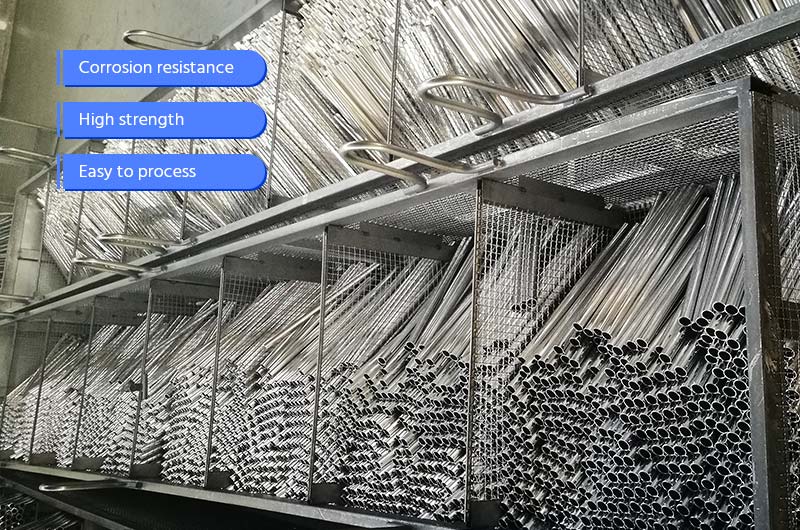
5052 Aircraft Aluminum Tube
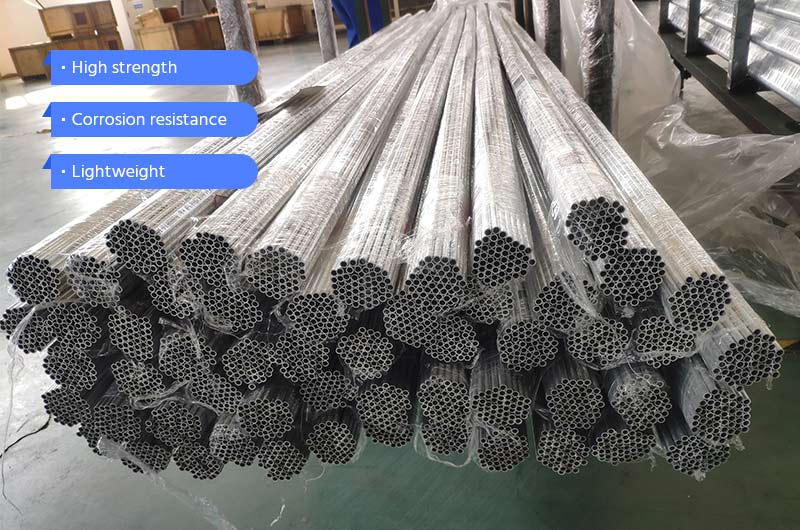
5083 Aircraft Aluminum Tube
Aluminum tubes for marine and automotive
Chalco, a diversified aluminum products manufacturer, provides high-performance aluminum tubes for shipbuilding, automotive, cycling, heat exchangers, and more, offering lightweight, corrosion-resistant solutions with alloys such as 5083, 6061, 5052, 7005, and 3003, supporting technological innovation and sustainability across various industries.
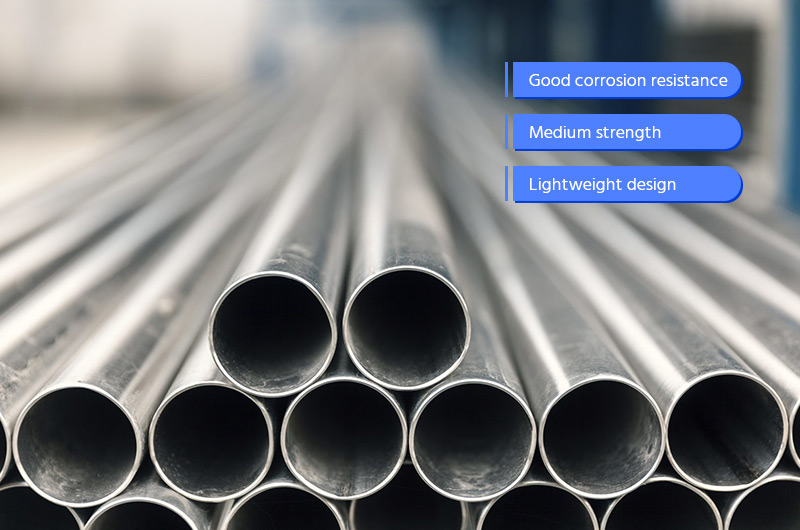
6063 Oil Tanker Aluminum Tube
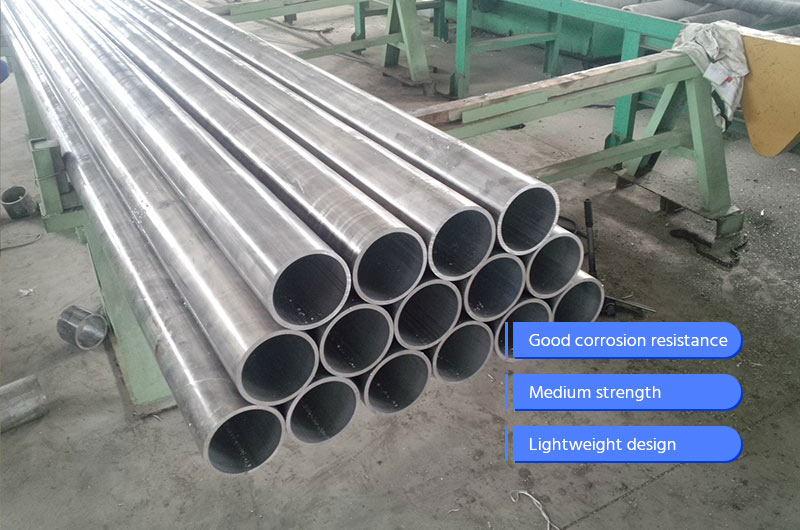
6061 Oil Tanker Aluminum Tube
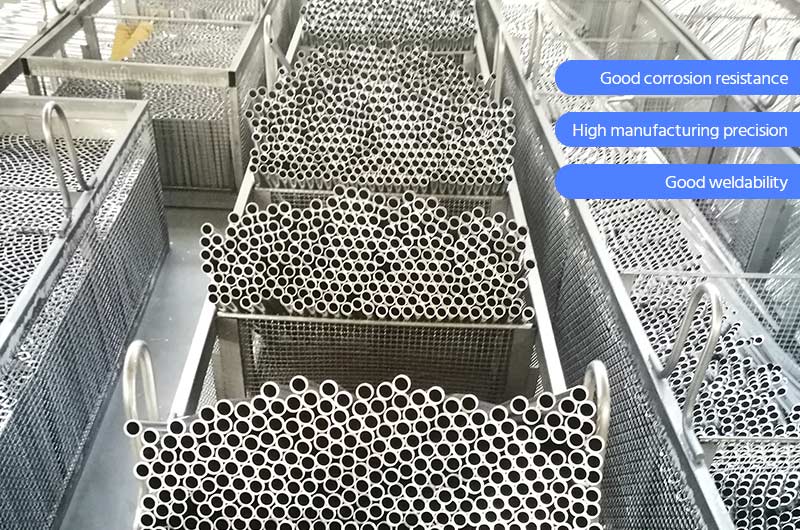
AMS 6061 Aluminum Tube
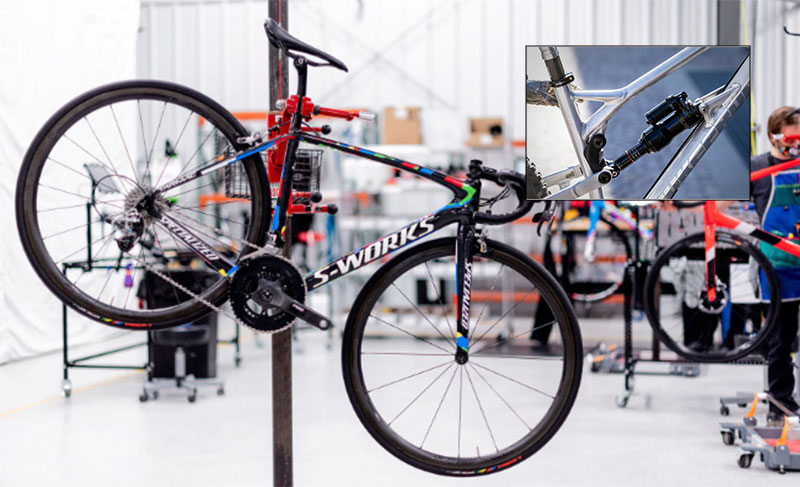
6061 Aluminum Tube for Bicycle
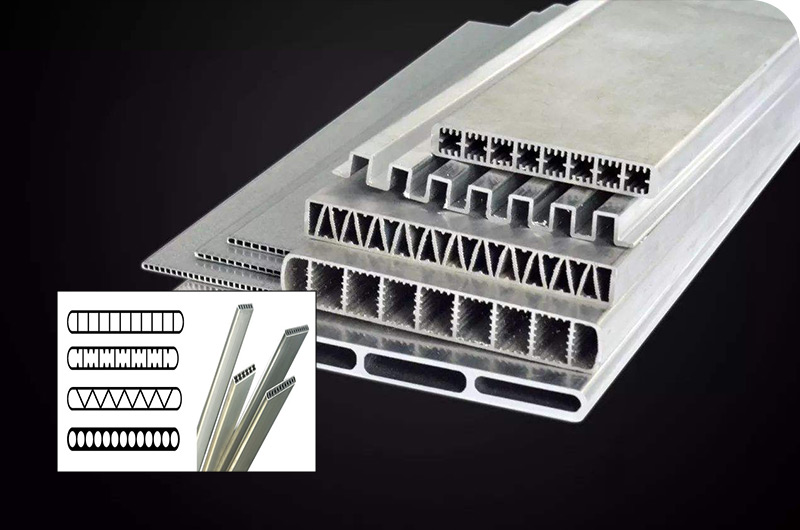
Tubes for Heat Exchanger
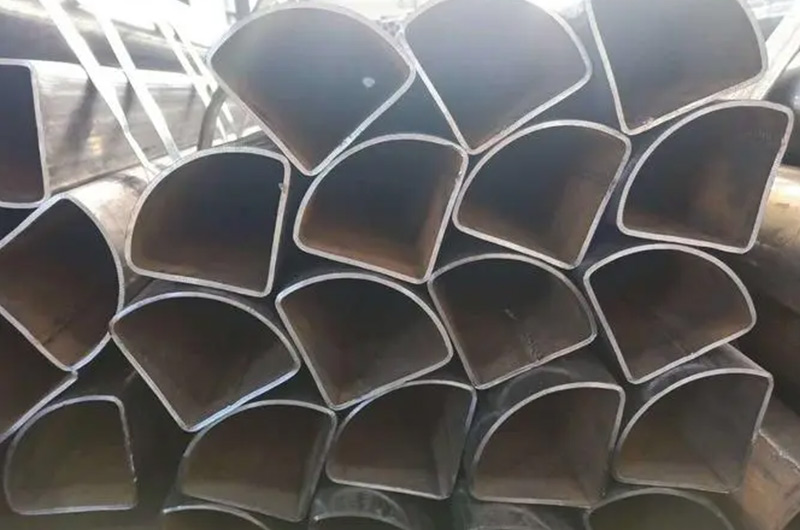
Missile-launcher-tube
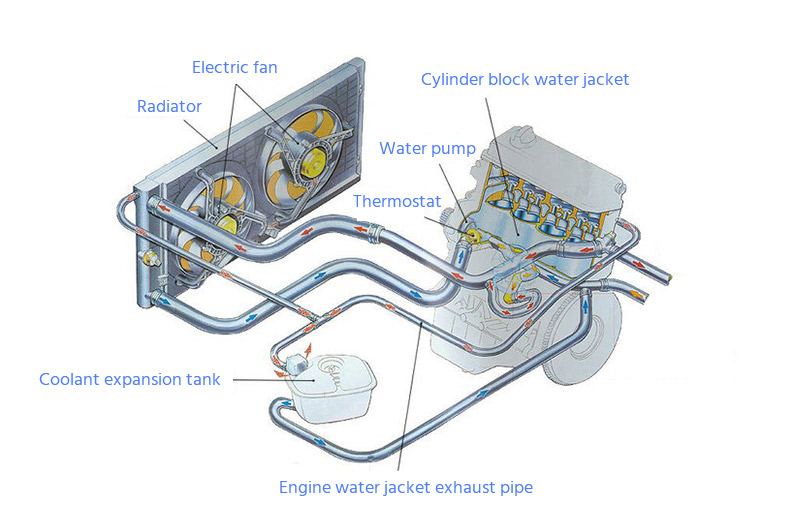
Auto-welded-tube
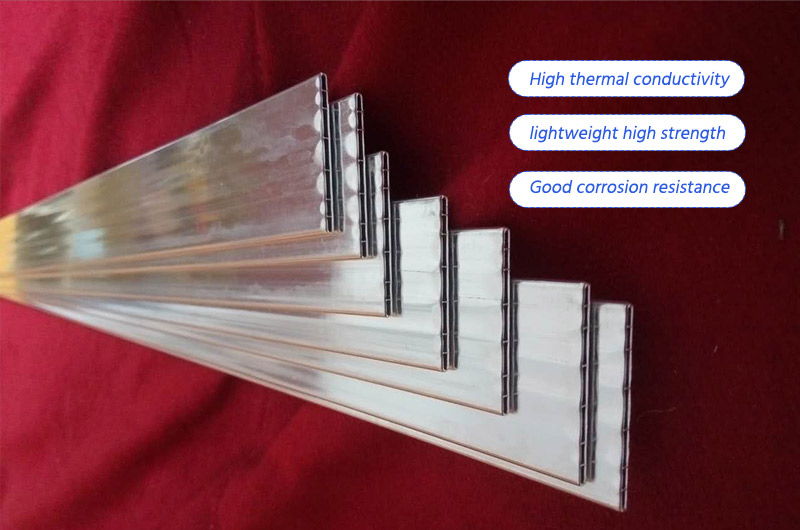
Auto-micro-channel
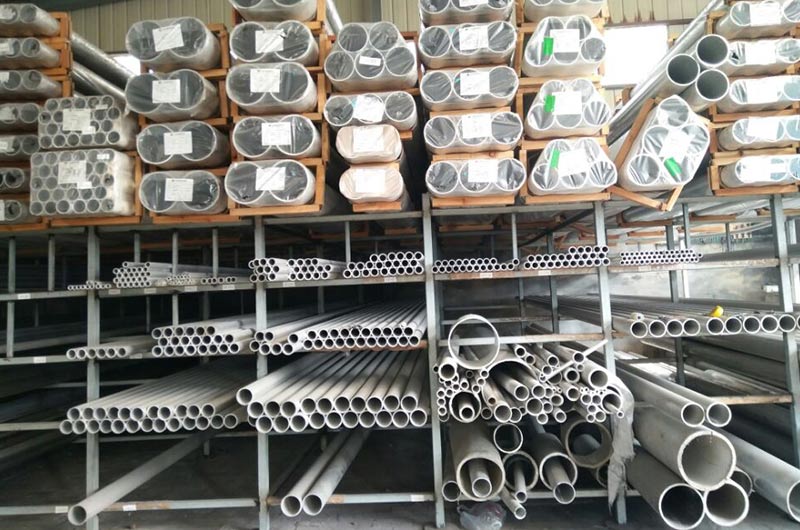
3003-auto-tube
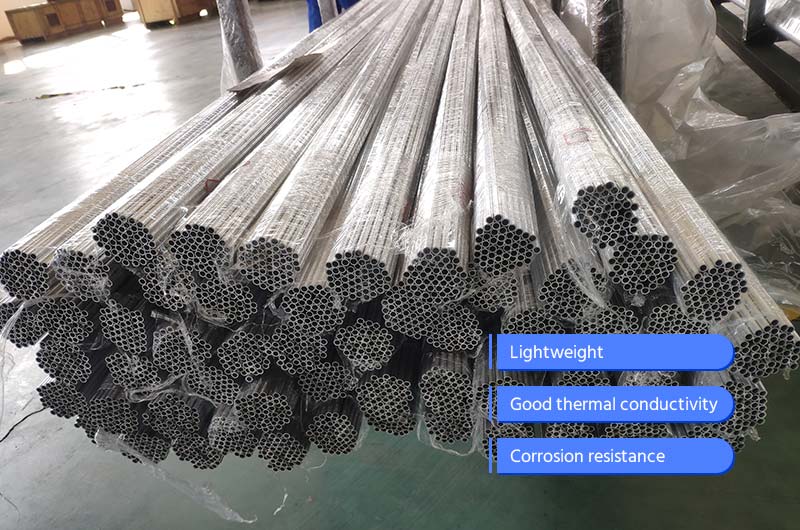
1100-auto-tube
Electric aluminum tube
Chalco tubular aluminum busbar products cover popular alloy series such as 1350, 1060, 1070, 3003, 6061, 6063, and 6101, with strong conductivity and corrosion resistance. After anodizing, they can adapt to various outdoor environments.
The product is delivered in a tubular structure, with straight body, smooth and flat surfaces, and no defects such as cracks, wrinkles, twists, etc. Compared with other shapes of busbars, they are lighter in weight, larger in cross-sectional area, stronger in load-bearing capacity, and more convenient to install.Quick Quote
-
Electrical-aluminum-bus-pipe
Chalco tubular aluminum busbar products cover popular alloy series such as 1350, 1060, 1070, 3003, 6061, 6063, and 6101, with strong conductivity and corrosion resistance. After anodizing, they can adapt to various outdoor environments.
Strong conductivity Corrosion resistance Straight body
Special Size Aluminum Tubes
Chalco specializes in a diverse range of aluminum products, including cold-drawn tubes, extra-large diameter aluminum tubes (500mm-1528mm), ultra-hard wear-resistant cylinder tubes, spiral welded tubes, tent poles, streetlight poles, and gas cylinder tubes.Quick Quote
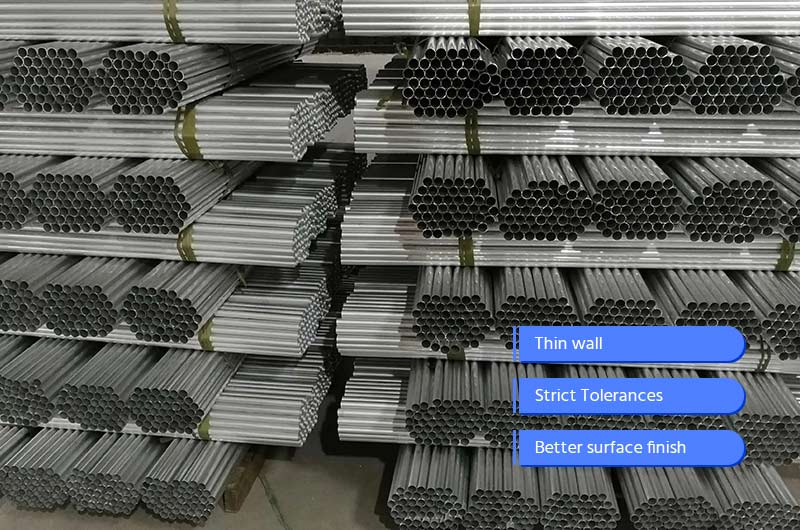
Cold Drawn Aluminum Tubing
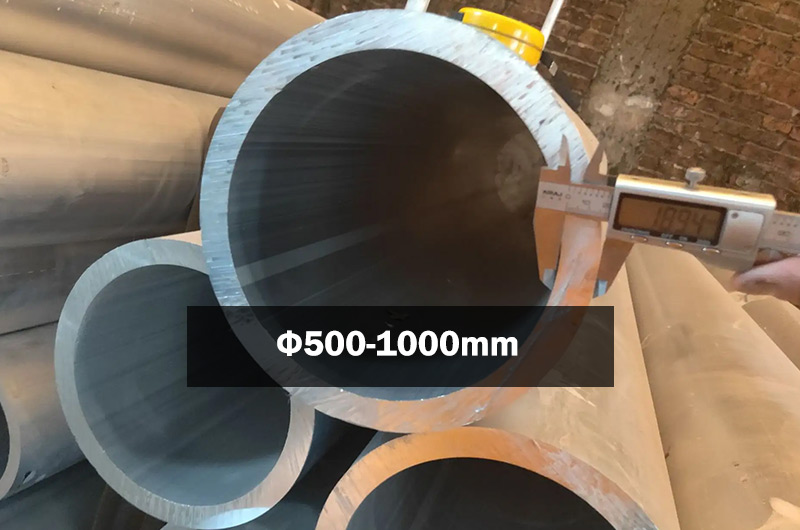
Large Diameter Aluminum Pipe
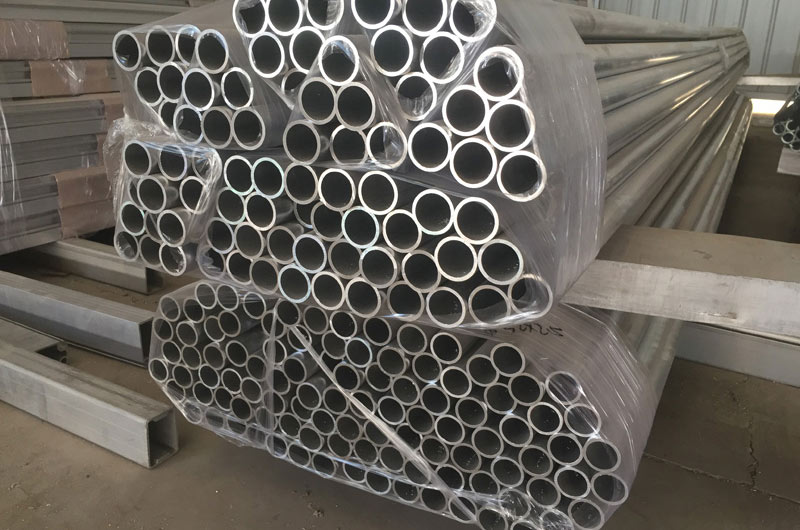
SCH40/SCH80 Aluminum Tube
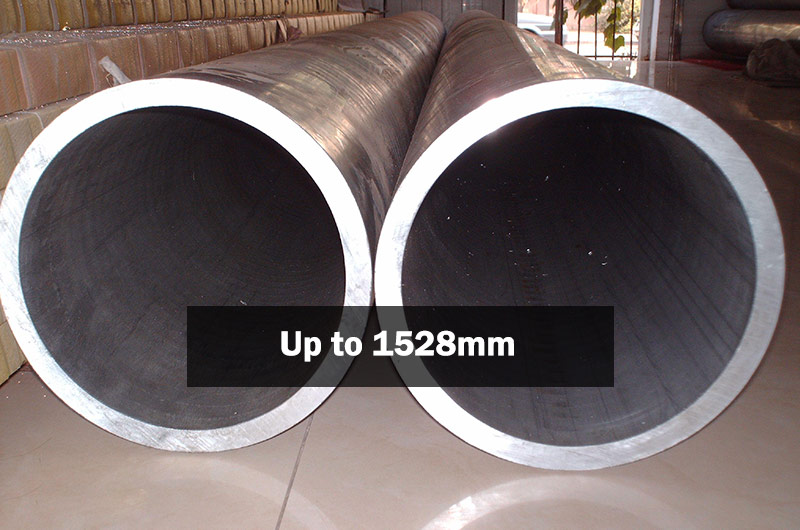
Large Diameter Aluminum Pipe
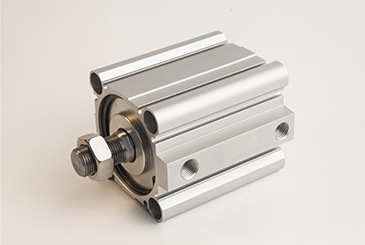
Pneumatic-cylinder-tube
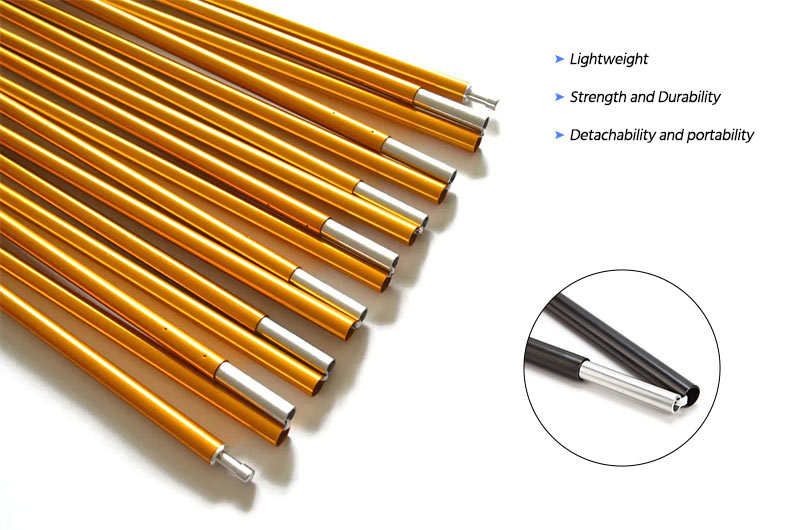
Tent-pole
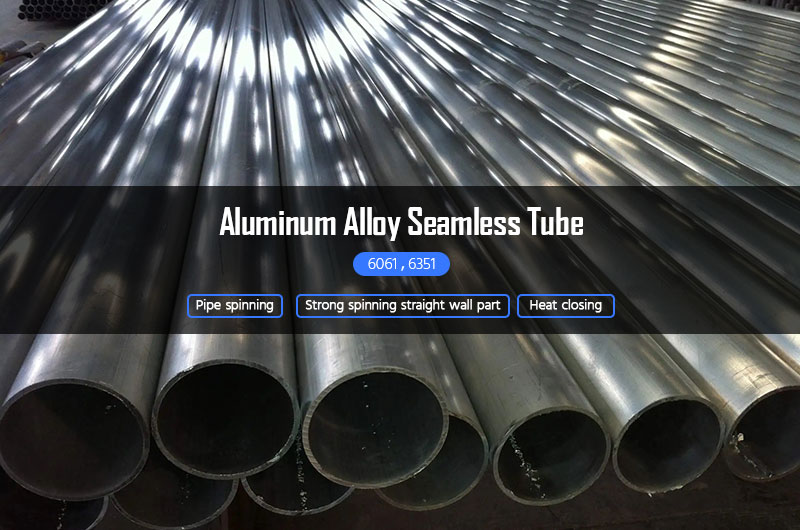
Aluminum-gas-cylinder-tube
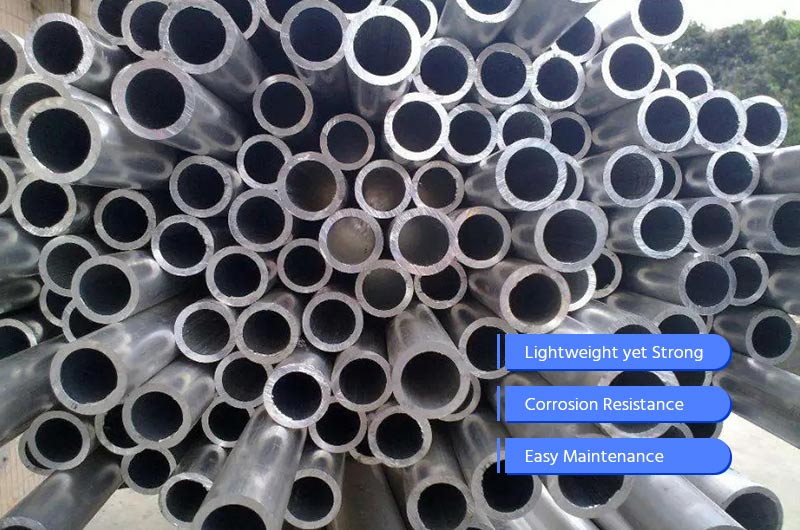
Street-light-aluminum-pole
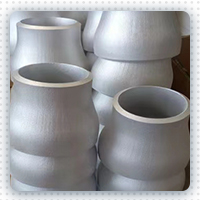
Apiral-welding-pipe Max. Φ1580mm
How to manufacture high quality aluminum tubes?
Three main factors of aluminum tube bending
1. Formability
Some aluminum alloys, such as 3000, 5000 and 6000 series, have higher formability than other aluminum alloys, making them good bending materials.
2. High precision
Like other metals, aluminum will appear "work hardening" during bending. This means that it will become stronger and stronger when formed. However, if ratio of radius to pipe thickness is too small, the material will be over machined and more likely to lose efficacy.
3. Rate of elongation, flexibility
Percentage of elongation is a way of describing the difference between the yield strength of a metal and its ultimate tensile strength. Yield strength is the point at which an aluminum alloy can be bent and no longer restored to its original shape. The greater the difference between these strengths, the better the formability of the alloy.
Aluminum tubes have excellent bending properties and are suitable for various complex pipeline design and installation requirements.
Brazing and welding of aluminum pipe
Low temperature operation: The brazing operation temperature of aluminum tubes is low, which reduces the thermal impact on the material.
Strong connection: The aluminum tube joints after brazing have high strength and durability, suitable for long-term use.
High strength: The aluminum tube after welding maintains high strength and durability, suitable for various applications with high strength requirements.
The difference between seamless aluminum tubes and seamed aluminum tubes
From the production point of view: seamless aluminum tubes are produced by reverse extrusion machines, the processing technology is relatively complex and the cost is high. Seamed aluminum tubes are extruded by forward extrusion machines, which are fast to produce and low in cost.
From the surface: high-frequency welds of straight or spiral lines can be seen inside the seamed aluminum tubes. The wall thickness of seamless aluminum tubes is relatively thick, and there are no welds inside.
In terms of performance: seamless aluminum tubes have better pressure resistance and uniform texture than seamed aluminum tubes. The chemical composition and mechanical properties of the weld part of the seamed aluminum tube will change slightly. If it is a bent tube, it is recommended to use seamless aluminum tubes, and seamed aluminum tubes are prone to cracking.
In terms of function: seamless aluminum tubes can be used in important parts such as water stamping, air hydraulics, machined parts, grinding sleeves, etc. Seamed aluminum tubes are generally used as structural supports.
Advantages of purchasing Chalco aluminum tube pipes
- Chalco is the source factory of aluminum pipes and can provide you with extremely low factory prices.
- Chalco stocks aluminum tubes in various sizes, with a minimum order quantity of one tube, and can guarantee delivery within a week.
- Aluminum tubes can be cut according to customer requirements or ordered separately from molds
- Chalco can send free aluminum tube samples
Chalco can provide you the most comprehensive inventory of aluminum products and can also supply you customized products. Precise quotation will be provided within 24 hours.
Get a quote