For customers who need aluminum products with strength, processability, and welding ability, aluminum alloy 2014 is an excellent choice. It is a precipitation hardening alloy that can maintain strength after heat treatment. The unique characteristic of 2014 alloy makes it widely used in the fields of aerospace and military industry.
Chalco is the aluminum supplier for Collins Aerospace, Boeing (Boeing), Airbus (Airbus) and other aerospace companies, and has passed the AS9100 certification required by the aviation industry. Aerospace grade aircraft aluminum extrusions profile are produced according to AMS 4153, ASTM-B221, UNS A92014, QQ-A-200/2 etc. specifications. Other specification such as ABS, ASNA, LN, Werkstoff, NTA, DAN, AIR can send email to consult. Welcome contact
Specifications of Chalco aluminium alloy 2014 aerospace extrusion
Alloy | 2014 |
Temper | T3, T6, T8, T651, T6511, etc. |
Production method | extrusion, cold drawn |
Surface treatment | Anodizing, plating, painting/coating, polishing, sanding, chemical etching, etc. |
Open Profile dimensions | Min 4mm*3mm, Max.850mm*50mm. |
Closed profiles dimension | Min.6.35mm*1mm, Max. 573mm*10mm. |
Section area | 0.2-90cm2 |
Wall thickness | 1-100mm |
Outline size | 10-530mm |
Profile length | Maximum 28m (standard 6000mm) |
Extrusion Type | Dimension range (inches) | Wall thickness range (inches) |
2014 aluminum round tube | 1-10 | 0.125-0.75 |
2014 aluminum square tube | 1-8 | 0.125-0.5 |
2014 aluminum rectangular tube | 1*2-8*12 | 0.125-0.5 |
2014 aluminum angle | 1*1-8*8 | 0.125-0.5 |
2014 aluminum T-profile | 1*1-6*6 | 0.125-0.5 |
2014 aluminum U-profile | 1*0.5-6*2 | 0.125-0.5 |
2014 extruded aluminum round bar diameter | Φ0.20-8.0 | - |
2014 extruded aluminum square bar diameter | 0.20-8.0 | - |
2014 extruded aluminum flat bar specifications | Thickness: 0.006-1.6 Width: 0.4-8.0 | - |
2014 extruded aluminum hexagonal bar diameter | 0.2-8 | - |
It should be noted that the specifications of aluminum profiles also include requirements for their shape and surface treatment. The specific requirements can be determined according to the application field and specification standards. Consult Chalco business, we can provide mold opening and customization service according to customer drawings.Quick Quote
Chalco 2014A industrial aerospace grade aluminium extrusion profile
2014 round bars/tubes: used in aircraft for structural components such as support rods, connecting links, and small accessories, providing strength and lightweight properties.
2014 square/rectangular bars: ideal for constructing aircraft frameworks, cabin windows, and other rectangular components, offering shape and strength for robust structures.
2014 t-shaped profiles: applied in aerospace for components that require support and connections, like interior structures and certain connectors.
2014 l-shaped profiles: commonly used in aircraft for internal support components, trays, and fixations, ensuring stability and strength.
2014 round tubes: employed in aerospace for cabin ducts, sensor mounts, and other components requiring space and fluidity.
Custom profiles: tailored to specific aerospace needs, these customized 2014 aluminum profiles meet unique design requirements for aircraft structures, connectors, and cabin components.
Chemical composition of Chalco 2014A aerospace aluminum alloy
Chemical Element | % Present |
Si | 0.15-1.2 |
Fe | 0.7 |
Cu | 3.9-5.0 |
Mn | 0.40-1.2 |
Mg | 0.20-0.8 |
Ti | 0.15 |
Cr | 0.10 |
Zn | 0.25 |
Other (Each) | 0.0-0.05 |
Aluminium (Al) | Balance |
Mechanical properties of Chalco 2014 aerospace high quality extrusion
Density | 2.8g/cm3 (0.1018lb/in3) |
Young's modulus | 73 Gpa (11 Msi) |
Electrical conductivity | 34% to 50% IACS |
Ultimate tensile strength | 190-480 Mpa (28-70 ksi) |
Thermal conductivity | 130-190 W/m-K |
Thermal expansion | 23 μm/m-K |
Poisson's ratio | 0.33 |
Melting point | 510C / 950F |
Product features of Chalco 2014 aviation aluminum alloy extrusion
2014 Aluminum Alloy is a copper based alloy that exhibits very high strength and excellent machinability in certain tempered conditions. It is not suitable for soldering as it tends to crack. It has poor corrosion resistance, which is why it is often clad with pure aluminum. When exposed and used in environments exposed to the weather, it requires a coat of paint to reduce the risk of corrosion.
- High mechanical strength
- Excellent fatigue resistance
- Excellent machinability
- Protective coating required to avoid corrosion
Other hot selling aerospace aluminum extrusion profile products in Chalco
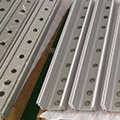
2024 aerospace profile
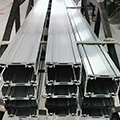
2219 aerospace profile
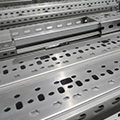
6061 aerospace profile
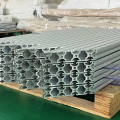
6063 aerospace profile
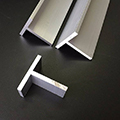
7050 aerospace profile
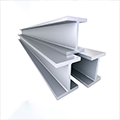
7075 aerospace profile
FAQ for purchasing 2014 aluminum extrusion
Q: What is the typical production process for Chalco aluminum alloy 2014 (UNS A92014) extrusion?
A: Chalco aluminum alloy 2014 extrusion primarily employs the extrusion process, where the aluminum material is extruded to create profiles of various cross-sectional shapes.
Q: What factors may influence the price of 2014 aluminum alloy?
A: The price of 2014 aluminum alloy can be influenced by market demand, raw material costs, production processes, and the complexity of extruded profiles.
Q: Does Chalco have the extrusion or drawing production capacity for 2014 aluminum alloy profiles?
A: Chalco has the capability for extrusion, which is commonly used in the production of 2014 aluminum alloy profiles. We can provide profiles of various cross-sectional shapes.
Q: Can 2014 aluminum alloy profiles undergo surface treatments such as anodizing or painting?
A: Yes, 2014 aluminum alloy profiles can undergo various surface treatments, including anodizing, painting, and other methods, depending on your specific requirements and applications.
Q: Are Chalco's 2014 aluminum alloy profiles suitable for aerospace applications?
A: Yes, Chalco's 2014 aluminum alloy profiles are commonly used in the aerospace industry due to their high strength and corrosion resistance. They are employed in applications like aircraft structural components and other aerospace parts.
Chalco can provide you the most comprehensive inventory of aluminum products and can also supply you customized products. Precise quotation will be provided within 24 hours.
Get a quote