The aluminum heat exchanger is composed of aluminum tubes for heat exchangers passing cooling water and cooling fins for heat dissipation.
Aluminum tubes for heat exchangers are generally extruded and drawn from 1050, 1100, 3003, 5083, 6061, 6063 aluminum tube to play the role of heat dissipation and cooling.
The choice of alloy depends on factors such as the specific application, operating conditions and required properties such as strength, corrosion resistance and thermal conductivity.Quick Quote
Aluminium finned tube for heat exchanger
The aluminum finned tube process is a labor-intensive process. It adopts the form of a base tube covered with an aluminum tube. (The base tube can be carbon steel or stainless steel) is extruded by a machine to form fins. The base of the fins is closely attached to the outer wall of the tube. Together, the length is from 0.5 meters to 6 meters.
It meets the demand for the length of the steel-aluminum finned tube, thus solving the trouble of re-cutting caused by improper length during use.
The specifications of aluminium finned tube for heat exchanger
- Fin material alloy: 1050, 1060, 1070, 1100, 5052, 6063
- Fin pitch: Min. 1.5mm
- Fins per pitch(Density) : 4-12
- Fin segments: 12, 16, 24 fins or as per your design
- Fin height: Max. 16.5mm
- Fin thickness: 0.4mm average
- Base tube OD: Max 2”(50.8mm)
All sizes of aluminum finned tubes
All dimensions (inches) and specifications of aluminum finned tubes are available upon your request.Quick Quote
Tube OD | Fin Height | Fin Thickness | Fins per Pitch(Density) |
5/8 | 3/8, 1/2 | .015/.016/.020 | 4, 5, 6, 7, 8, 9, 10, 11, 12 |
3/4 | 3/8, 1/2, 5/8 | .015/.016/.020 | 4, 5, 6, 7, 8, 9, 10, 11, 12 |
1 | 3/8, 1/2, 5/8 | .015/.016/.020 | 4, 5, 6, 7, 8, 9, 10, 11 |
1 1/4 | 3/8, 1/2, 5/8 | .015/.016/.020 | 4, 5, 6, 7, 8, 9, 10, |
1 1/2 | 3/8, 1/2, 5/8 | .015/.016/.020 | 4, 5, 6, 7, 8, 9, 10, 11 |
1 3/4 | 3/8, 1/2, 5/8 | .015/.016/.020 | 4, 5, 6, 7, 8, 9, 10 |
2 | 3/8, 1/2, 5/8 | .015/.016/.020 | 4, 5, 6, 7, 8, 9, 10 |
Classification of aluminum finned tubes
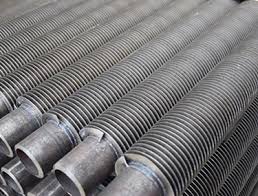
High frequency welded finned tube
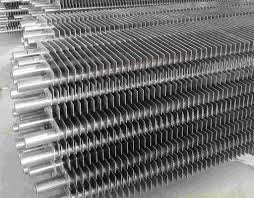
Square-finned tube
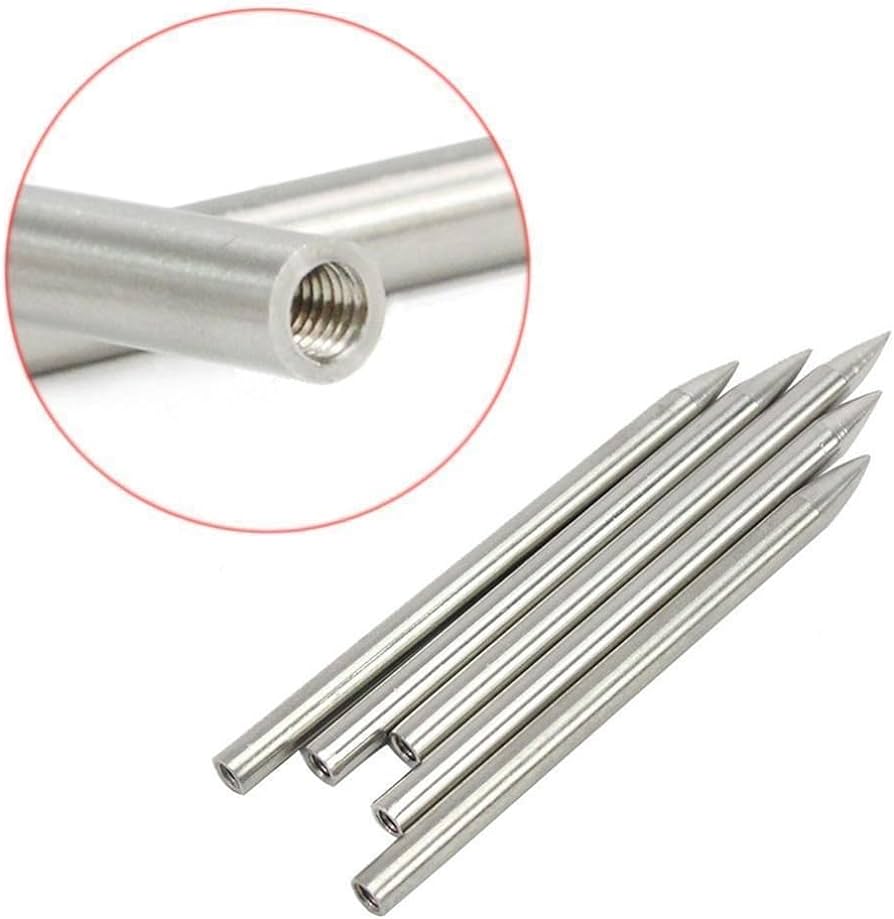
Needle tube
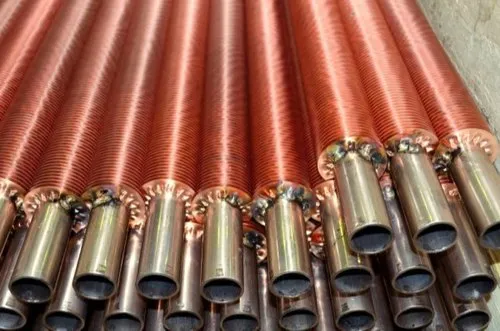
Laser welded finned tubes
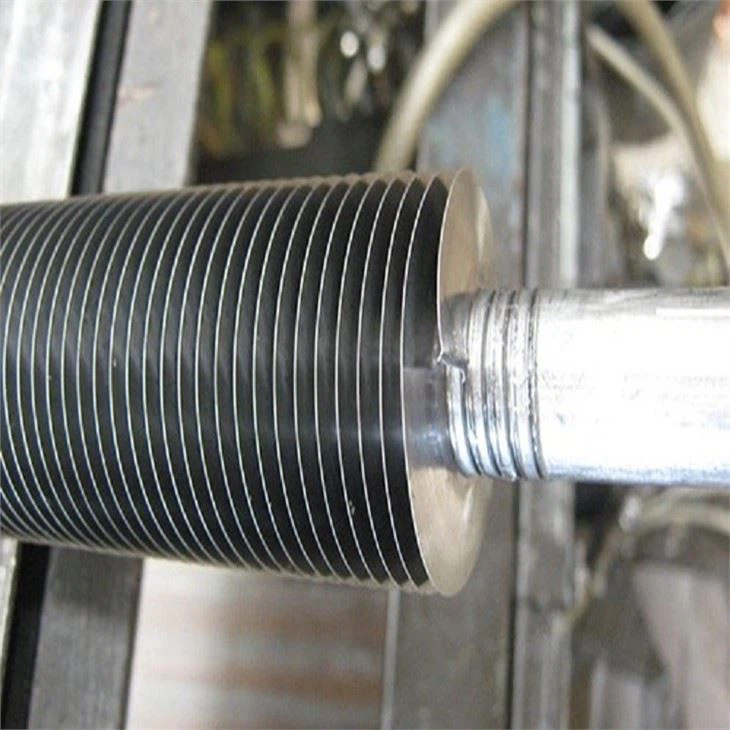
Inlaid finned tube
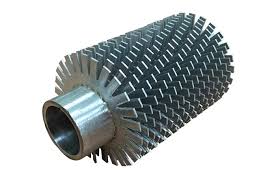
DR extruded high finned tube
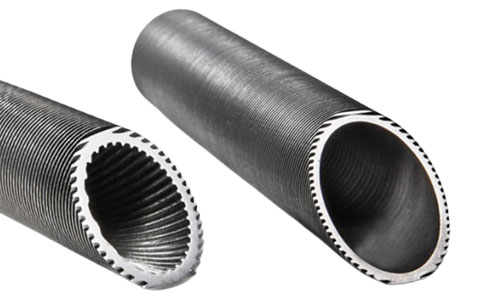
Low-finned tube
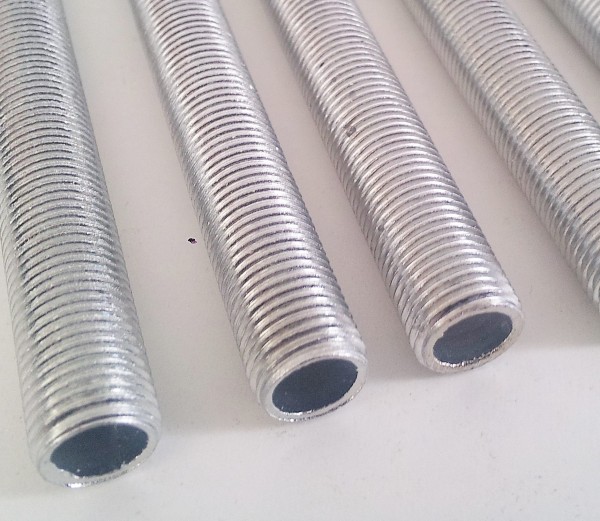
Threaded tube
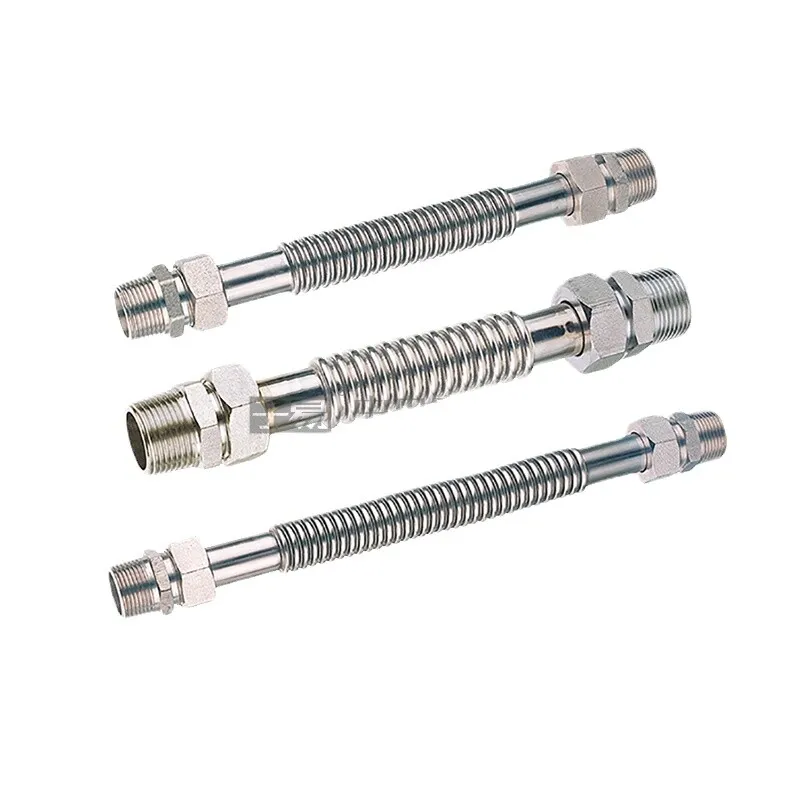
Wave joint tube
can create specific finned tubes for your needs like intergral turbulator finned tubes or double tube construction finned tubes.
The performance characteristics of aluminium finned tube for heat exchanger
Aluminum finned tubes have the characteristics of tight combination, small thermal resistance, good heat transfer performance, high strength, small flow loss, strong anti-corrosion performance, not easy to deform in long-term cold and hot conditions, and long working life.Quick Quote
The application of aluminium finned tube for heat exchanger
Aluminum finned tubes are mainly used in air coolers and air heaters in petrochemical, electric power, papermaking, tobacco, building heating and other industries, and air heaters in spray drying systems for vegetable eggs and starch in the food industry.
The advantages and characteristics of aluminum finned tubes in application is that aluminum finned tubes are formed in parallel with aluminum alloy plates and aluminum tubes at one time.Quick Quote
Aluminum Inner-grooved tubes for heat exchanger
Aluminum internally grooved tubes, also known as internally-grooved tubes, are a lightweight and cost-reducing solution for air conditioning heat exchangers and are an attractive alternative to copper tubes.
Internal grooves can be straight or spiral. The height of the inner groove ranges from 0.05 to 0.3mm. The higher the groove, the better the heat transfer performance. Aluminum internally grooved tubes are widely used in heat exchangers in domestic and commercial air conditioning systems.
The specifications of aluminum inner-grooved tubes for heat exchanger
Alloy grade:
1000 series, such as 1050, 1060, 1070, 1070A, 1100, etc.
3000 series, such as 3003, AA003H, etc.
Type: Straight inner-grooved tubes, Helical inner-grooved tubes
Outer diameter: Φ5.0-Φ16 mm
Bottom wall thickness: 0.4-2.0mm
Tooth height: 0.05-0.35 mm
Addendum angle: 30-135 (degree)
Helical Angle: 0-25 (degree)
Tooth Number: 20 to 70 (tooth)
All sizes of aluminum internally grooved tubes
All dimensions (inches) and specifications of aluminum internally grooved tubes are available upon your request.Quick Quote
Tube OD | I.D | Bottom Wel Thickness Tw | Fin Groove Depth Hf | Total Wall Thickness Tw | Apex Angle | Helix Angle | Number Of Tooth |
5.00 | 4.30 | 0.20 | 0.15 | 0.35 | 40 | 18 | 40 |
7.00 | 6.34 | 0.23 | 0.10 | 0.33 | 40 | 15 | 65 |
7.08 | 6.06 | 0.25 | 0.18 | 0.43 | 40 | 18 | 50 |
7.94 | 7.08 | 0.25 | 0.18 | 0.43 | 40 | 18 | 50 |
9.52 | 8.72 | 0.28 | 0.12 | 0.40 | 53 | 15 | 65 |
12.70 | 11.50 | 0.35 | 0.25 | 0.60 | 53 | 18 | 70 |
14.00 | 12.82 | 0.37 | 0.22 | 0.59 | 52 | 16 | 75 |
15.87 | 14.37 | 0.40 | 0.30 | 0.70 | 25 | 15 | 68 |
16.00 | 14.70 | 0.40 | 0.25 | 0.65 | 10 | 1 | 110 |
The performance characteristics of aluminum inner-grooved tubes for heat exchanger
- High heat transfer efficiency
- Low material cost
- Easy to form and bend
- Light weight
- Strong corrosion resistance
- High recycling value
- High precision
- High surface quality
The application range of aluminum inner-grooved tubes for heat exchanger
The Aluminum inner-grooved tubes for heat exchanger are mainly used in household air conditioners, freezers, refrigerators, automotive air conditioner tubes, automotive solar energy, etc.Quick Quote
Precision drawn aluminum tubes for heat exchangers
High-precision drawn aluminum tubes, also known as aluminum cold-drawn tubes, are widely used in heat exchangers. These include aluminum round tubes, internal threaded tubes, seamless collector tubes, old drawn aluminum tubes, seamless tubes, etc.
The main alloys for drawn aluminum tubes, capillary tubes, peanut tubes, etc., are 1070, 3003/3103, and 6063.
The specification of precision drawn aluminum tubes for heat exchangers
Alloy grade:
3000 series, such as 3003, 3103
5000 series, such as 5052, 5049, 5086
6000 series, such as 6063, 6061
Temper: O, H12, H14, H18, H34, H112, T4, T6, T83, etc.
Round tube outer diameter: 4mm-90mm
Round tube wall thickness: 0.3mm-5mm
Popular precision drawn aluminum tubes
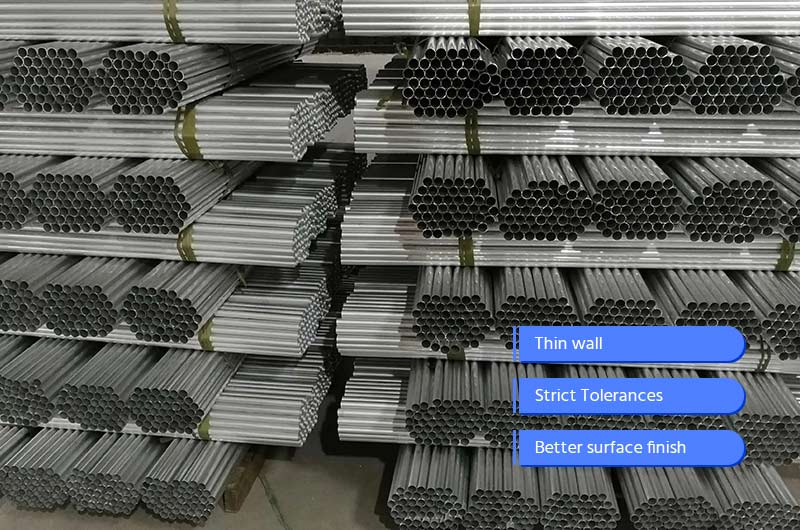
cold-drawn-aluminum-tube
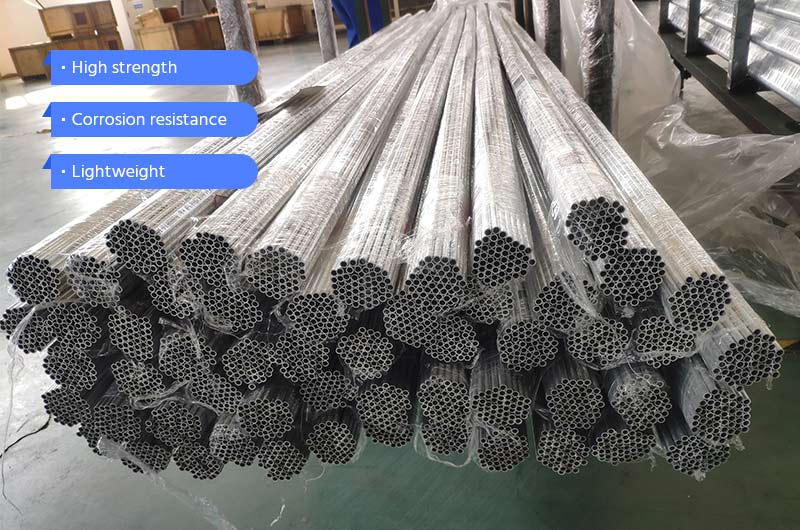
2024-aluminu-tube
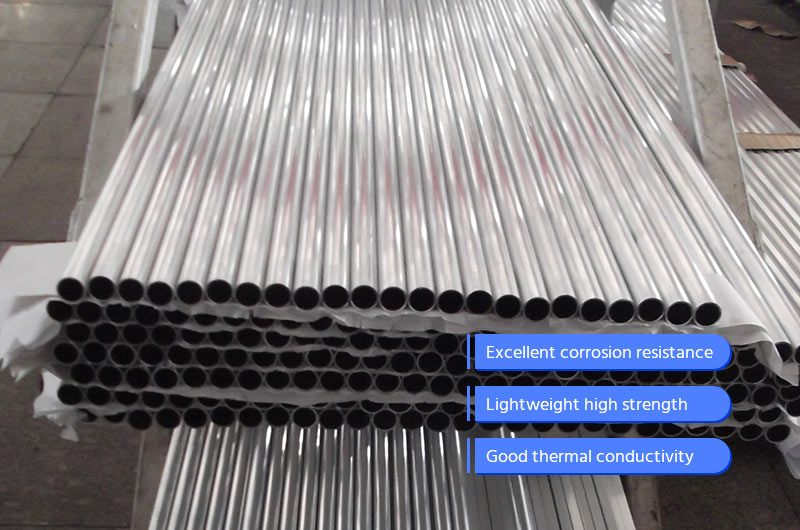
3003-seamless-tube
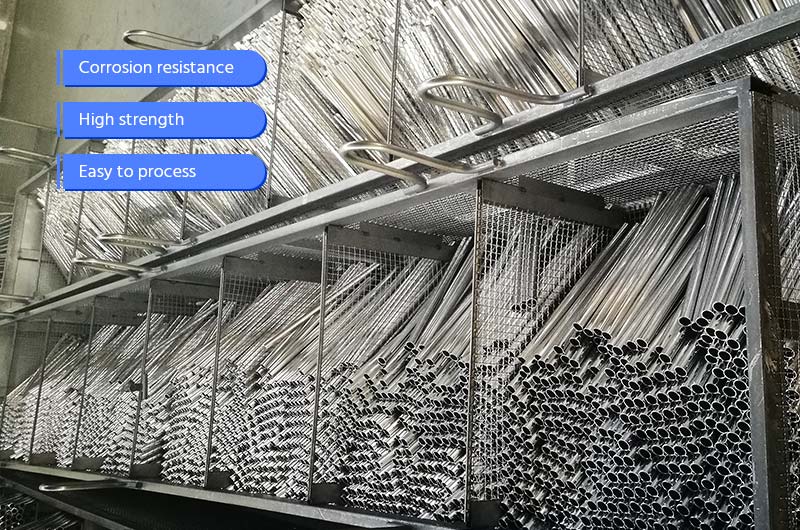
5052-aluminum-tube
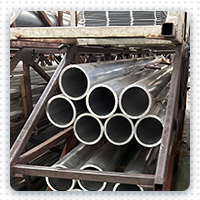
6061-aluminum-tube
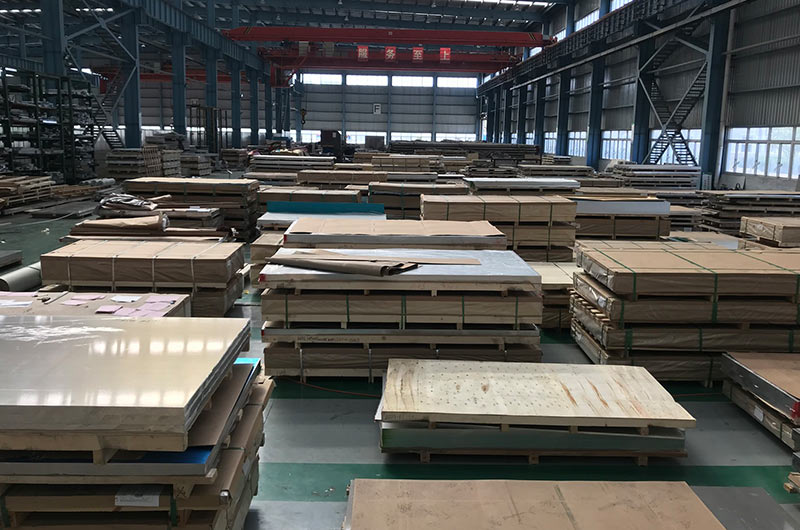
7075-aluminum-tube
All in-stock products are available for retail with no minimum order quantity. After confirming the order, customs clearance and shipment can be completed within one week.
As an original manufacturer, we carry out large-scale one-stop production. The price of aluminum pipes of the same quality is 10% lower than the market price.
The performance characteristics of precision drawn aluminum tubes for heat exchangers
- Light weight
- Good thermal conductivity and electrical conductivity
- Good corrosion resistance
- Good forming and bending performance
- Compliance with ROHS standards
- High recycling value
- Small deviation range
- High surface quality
- TS 16949 certification
The application range of aluminum precision drawn tubes for heat exchanger
Automotive air conditioners, civil air conditioners (condensers, evaporators, heat exchangers).Quick Quote
Micro-channel aluminum tubes for heat exchangers
This flat rectangular extruded tube, also known as a multi-port extruded tube, is made of multiple channels. These channels help increase heat transfer through a higher surface area/volume ratio
Microchannel tubes are available in a variety of sizes and alloys to ensure optimal performance for the required application. They can be delivered coated, ready for assembly and oven brazing.
The specification of micro-channel aluminum tubes for heat exchangers
Alloy grade:
1000 series, such as 1100, 1050, 1060, 1070, 1100
3000 series, such as 3102, 3003
Temper: H112 etc.
Width: 6mm-40mm Height: 0.8mm-8.0mm
Wall thickness: above 0.12
Number of holes: 2-35
Coating Material: Pre- Flux Coating, NOCOLOK Si Flux Coating, Zinc Coa
Thickness of zinc spraying: 5g/㎡-15g/㎡
Thickness of flux coating: 8g/㎡-25g/㎡
Free Samples: Yes, we can provide free sample
What kinds of Aluminum Micro-channel Tube do we have?
- Aluminium Micro-channel Tube
- Aluminium Multi-Port Tube
- Parallel Flow Aluminium Flat Tube
- Zinc-coated Aluminum Tube
- Pre-Flux Coated Aluminium Tube
- Si Flux Coated Aluminum Tube
- Large Multi-channel Tube(width range 50-200mm)
- Double Row Joint Multi-channel Flat Tube
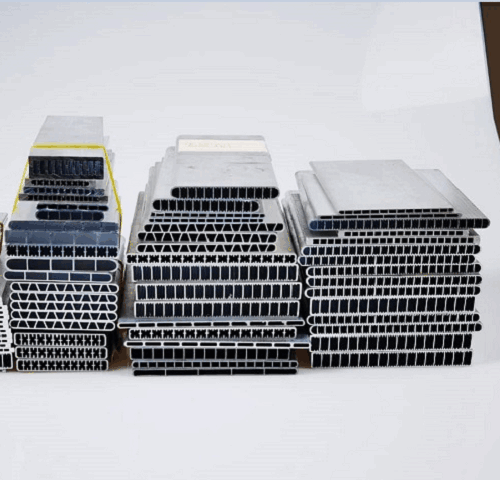
Aluminum Extrusion Micro Channel tube
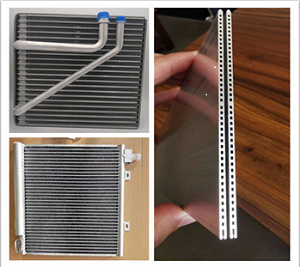
Aluminum Micro Channel Oil-Cooling Tube
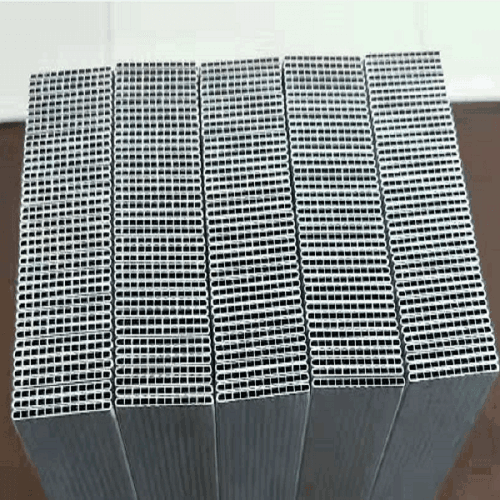
Aluminum Microchannel Condenser Tube
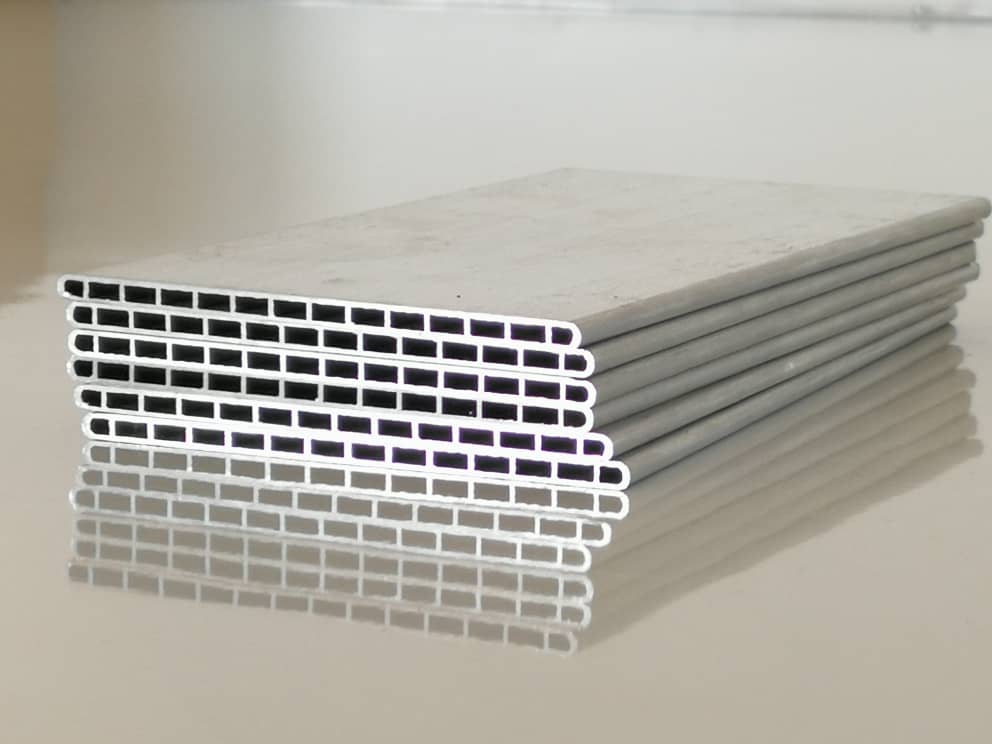
High Performance Harmonica Aluminum Tube
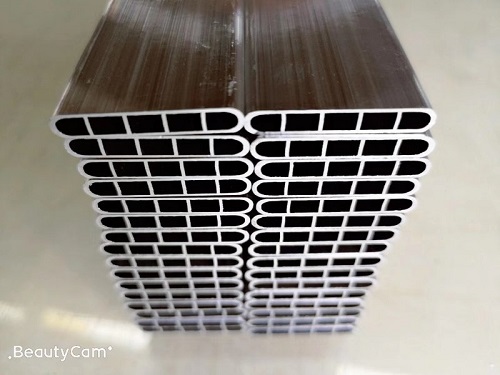
Micro channel aluminum flat tube
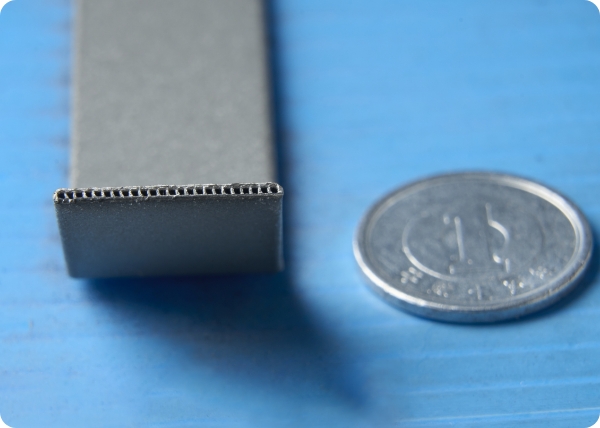
Extremely Small Micro Channel Tube
The performance characteristics of Micro-channel Tube for heat exchangers
- Good thermal conductivity
- Low material cost
- Light weight
- Strong anti-corrosion
- High precision
- High surface finish
The application range of micro-channel aluminum tubes for heat exchangers
- Refrigerators
- Air conditioners
- Condensers
- Freezers
- Evaporators
- Gas ovens
- Car radiators
- Heat exchanger
- HVAC and R systems
- Infrared detectors
- Microelectronics
- Power and process industries
- Aerospace
- Bioengineering
- Powerful laser mirrors
Aluminum flat tube for heat exchangers
Aluminum brazed heat exchangers are widely used in automotive air conditioning systems. Typically, such heat exchangers are made from flat tubes with multiple independent channels in cross-section, forming a serpentine or parallel flow geometry.
In these heat exchangers, multiple louvered corrugated fins are inserted into the gaps between flat tubes. Due to their high performance, some companies are beginning to use extruded brazed aluminum heat exchangers in heating, ventilation and air conditioning applications.Quick Quote
The specifications of aluminum flat tube for heat exchangers
Brazing layer: 4343, 4045
Core layer: 7072 anti-corrosion
Forming: high frequency welding
Temper: H14
Composite rate: 10±2
Specifications: according to customer requirements
The performance characteristics of aluminum flat tube for heat exchangers
- Light weight
- Easy to weld
- Good corrosion resistance
- Good pressure resistance
- Compliance with ROHS standards
- High recycling value
- Small deviation range
- High surface quality
The usage of aluminum flat tube for heat exchangers
Radiator aluminium flat tubes are mainly used in parallel flow condensers, automotive water tanks, and new energy vehicles.Quick Quote
Why choose Chalco?
We have more than 30 years of experience in supplying aluminum brazing composite materials for heat exchangers, intercoolers, air-conditioning condensers and evaporators, and aluminum tubes for various heat exchangers. Now we have become a world famous enterprise in the market of rolled aluminum and aluminum tubes for heat exchangers.
We have a complete set of domestic advanced R&D, testing and analysis instruments for aluminum brazing composite materials and aluminum tubes for various heat exchangers. These provide guarantee for the efficiency of new product research and development, and accelerate the transformation of scientific and technological achievements. In addition, our R&D&innovation and verification capabilities can help enhance the competitiveness of customers by saving time and costs for new product development and marketing.
We have passed the IATF16949 certification required by the automotive industry, the AS9100 certification required by the aviation industry, and the DNV BV LR ABS RINA CCS certification required by the shipbuilding industry.
The Chalco brand stands for quality, delivery and a solid reputation. With leading technology and globally competitive products, we can continue to develop together with our customers in the future.Quick Quote