Introduction to aluminum processing
Aluminum processing, using plastic processing methods to process aluminum ingots into materials, the main methods are rolling, extrusion, stretching and forging. Aluminum products have been serialized, and can produce eight types of products, including plates, strips, foils, pipes, bars, profiles, wires and forgings (free forgings, die forgings).Quick Quote
Aluminum processing is divided into deformation processing and casting processing.
Deformation processing is specifically divided into two methods of extrusion and calendering.
- The products made by extrusion process are called extruded profiles, mainly including architectural profiles and industrial profiles.
- The products made by the calendering process are called plates, strips and foils, which mainly include various aluminum plates, strips and foils.
Casting processing: through die-casting, the raw aluminum is processed into various precision aluminum alloy castings and precision sheet metal.
Aluminum processing process
According to the force and deformation mode (stress and strain state) of the workpiece during the deformation process, aluminum and aluminum alloy processing can be divided into rolling, extrusion, drawing, forging, spinning, forming processing (such as cold stamping, cold deformation , deep drawing, etc.) and deep processing, etc.
Rolling of aluminum
Rolling is a plastic deformation process in which the ingot is pulled into the rotating rolls by friction, and the cross-section is reduced, the shape is changed, the thickness is thinned and the length is increased by means of the pressure exerted by the rolls. According to the different direction of roll rotation, rolling can be divided into longitudinal rolling, cross rolling and skew rolling.
Extrusion of aluminum
Extrusion is to put the ingot into the extrusion cylinder, apply pressure to the metal through the extrusion shaft, make it extrude from the die hole of a given shape and size, and produce plastic deformation to obtain the required extrusion product processing methods. The direction of metal flow is different during extrusion. Extrusion can be divided into forward extrusion, reverse extrusion and joint extrusion.
Drawing of aluminum
Drawing is a stretching machine (or drawing machine) that pulls aluminum and aluminum alloy blanks (wire blanks or tube blanks) out of a mold of a given shape and size through clamps, causing them to undergo plastic deformation to obtain the required processing methods of tubes, rods, profiles and wires. According to the variety and shape of the products produced, stretching can be divided into wire stretching, pipe stretching, bar stretching and profile stretching. Pipe drawing can be divided into empty drawing, drawing with core head and drawing with swimming core head. The main elements of drawing processing are drawing machine, drawing die and drawing reel. According to the stretching mode, stretching can be divided into single-mode stretching and multi-mode stretching.Quick Quote
Forging of aluminum
Forging is a processing method in which a forging hammer or a press (mechanical or hydraulic) exerts pressure on aluminum and aluminum alloy ingots or forging blanks through the hammer or indenter to cause plastic deformation of the metal. Aluminum alloy forging has two basic methods: free forging and die forging. Free forging is to forge the workpiece between flat anvils (or type anvils); die forging is to place the workpiece in a die of given size and shape, and then apply pressure to the workpiece for forging deformation to obtain the required die forging .
Aluminum casting
In aluminum processing, casting involves pouring molten aluminum into pre-designed molds, which solidifies upon cooling to form aluminum castings. This method is suitable for producing complex shapes or large quantities of aluminum products.
It is characterized by its complexity, low cost, and high production efficiency, making it widely used in industries such as automotive, aerospace, and construction. Choosing the right casting process is crucial for ensuring product quality and reducing production costs.
Production of aluminum plate, sheet
The continuous production process of aluminum sheet and strip includes steps such as melting, casting, homogenization, hot rolling, cold rolling, intermediate annealing, final annealing, finishing, inspection, and packaging. Through these steps, aluminum ingots or alloys are processed into aluminum sheets and strips of various specifications.
Furthermore, the production process of aluminum sheet and strip can be adjusted according to different requirements, such as adding coating or plating processes, to meet the special needs of different users.Quick Quote
Common applications of aluminum sheet products
- Aerospace, aircraft skin, fuselage, wings, landing gear, etc.
- Architecture, building curtain walls, roofs, doors, windows, suspended ceilings, etc.
- Transportation, automobile body, ship deck, train carriage, etc.
- Electronics, electronic component housings, radiators, circuit boards, etc.
- Packaging, food packaging, beverage cans, medicinal packaging, etc.
Popular aluminum sheet products
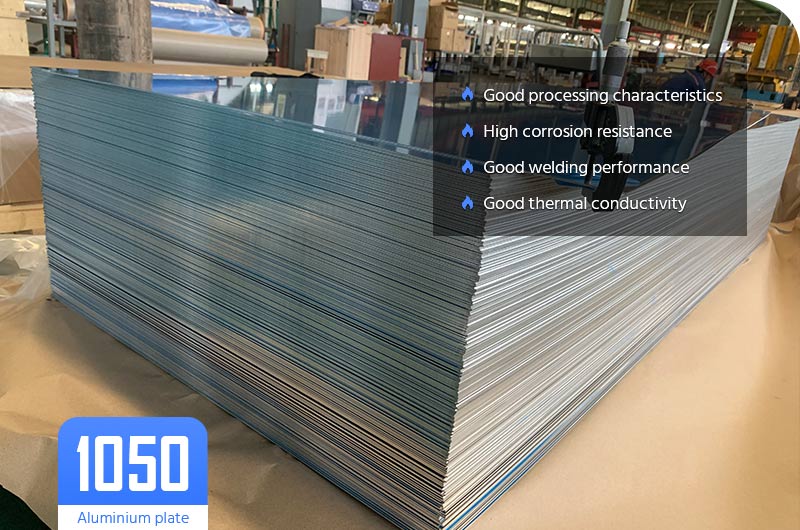
1050-aluminum-sheet
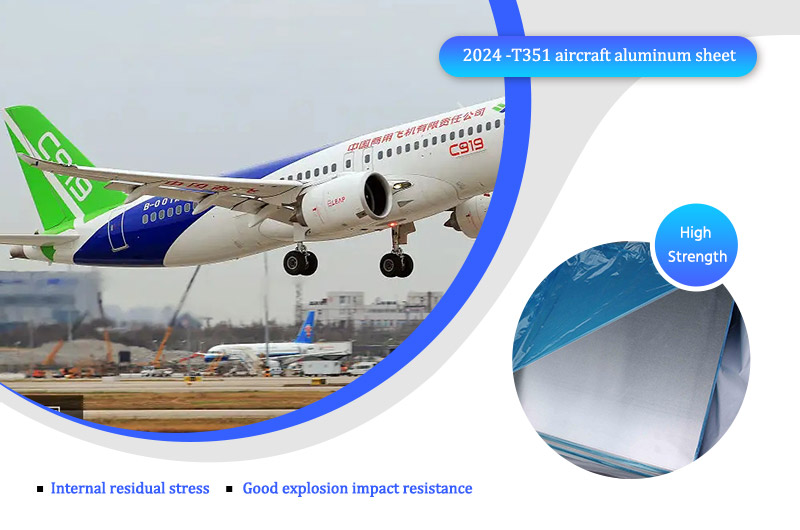
2024-aluminium-sheet
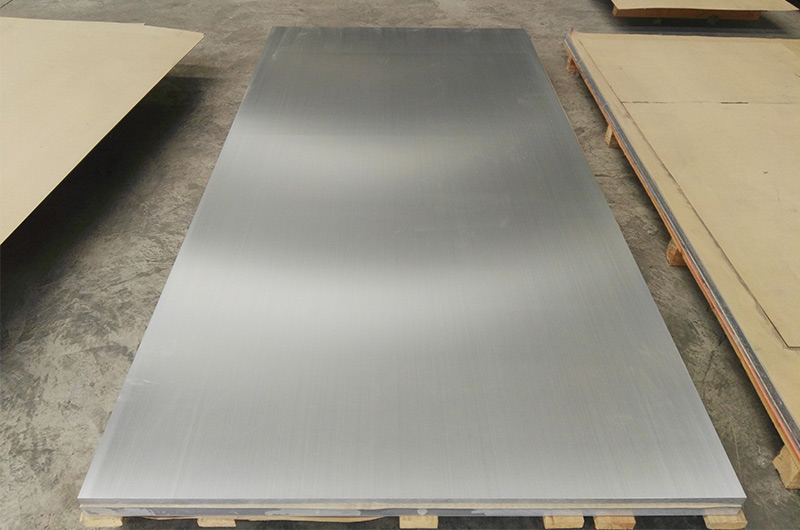
2219-aluminum-plate
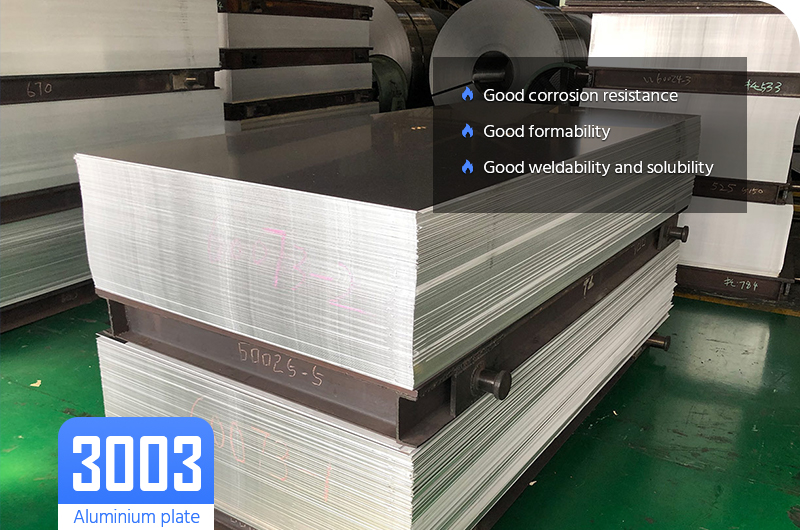
3003-aluminium-sheet
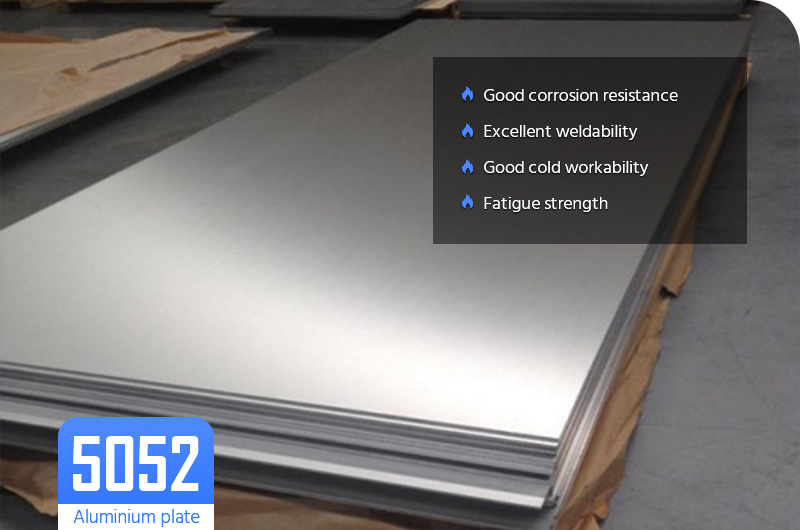
5052-aluminum-sheet
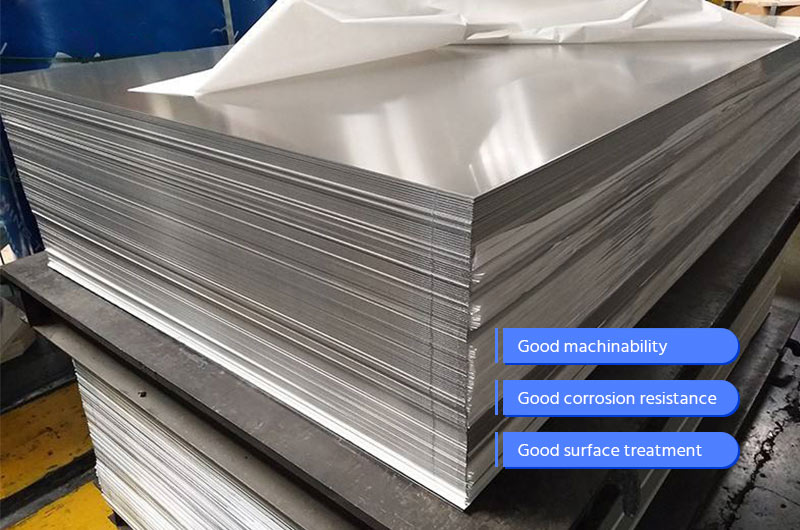
6063-aluminum-sheet
Production of aluminum tubes, bars and profiles
The production of aluminum pipes, rods, and profiles usually involves hot extrusion to make billets, and then rolling (or stretching), finishing and heat treatment to make finished products. It can also be directly made into finished products by hot extrusion. Now it has been developed from short ingot to long ingot extrusion. According to the extrusion force of the extruder, the ingot with uniform diameter is used to extrude various Profiles, pipes, and products can reach a length of more than 60 meters. After being stretched and straightened, they are cut to the required length.
Aluminum building profiles are made of aluminum-magnesium-silicon alloys. After anodic oxidation and coloring treatment, this kind of product forms various color oxide films on the surface, with good corrosion resistance. The doors and windows made by this building profile are beautiful and durable, and have good sealing performance. In addition to hot extrusion, methods such as cold extrusion, isothermal extrusion, residue-free extrusion, and hydrostatic extrusion have also been developed.Quick Quote
Common applications of aluminum profiles products
- Construction: doors, windows, curtain walls, frames, decorative profiles, roofs, suspended ceilings, railings, etc.
- Transportation: automobile body, train carriage, ship deck, aircraft skin, fuselage, wing, etc.
- Electronics: radiators, casings, conductive strips, circuit boards, electronic component casings, etc.
- Machinery: Machine tool guide rails, frames, structural parts, hydraulic cylinders, bearings, etc.
- Furniture: chair legs, table legs, frames, decorative pieces, etc.
Popular aluminum profiles products
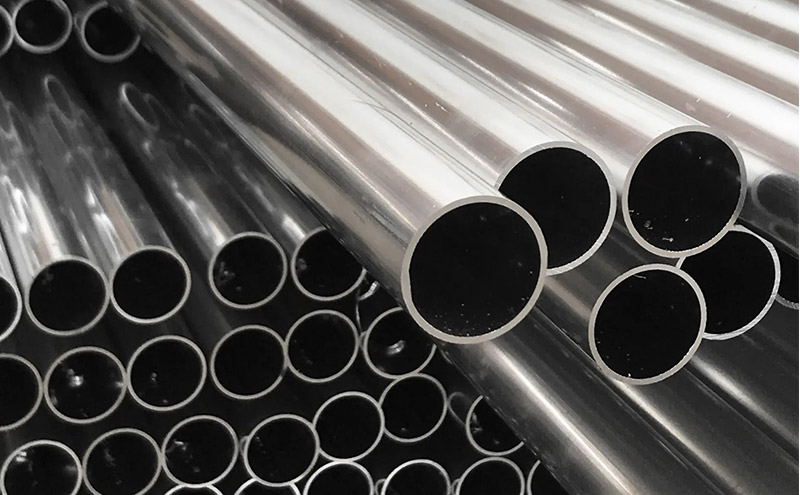
2024-aluminum-tube
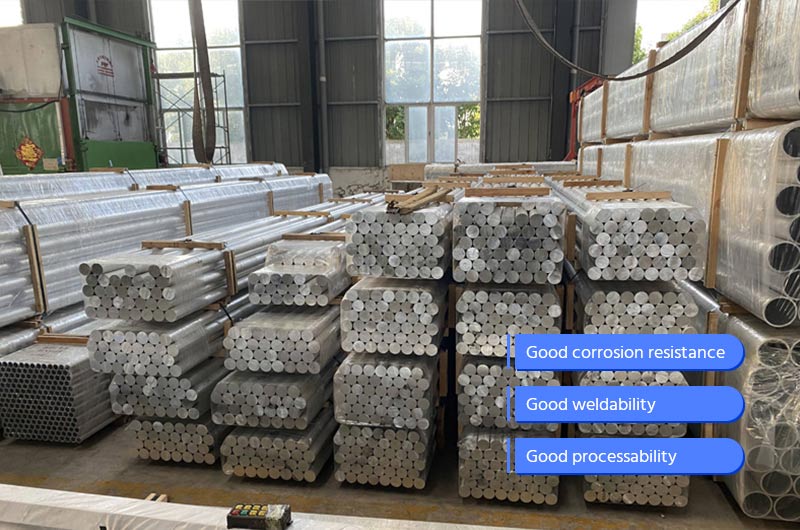
5083-aluminum-bar
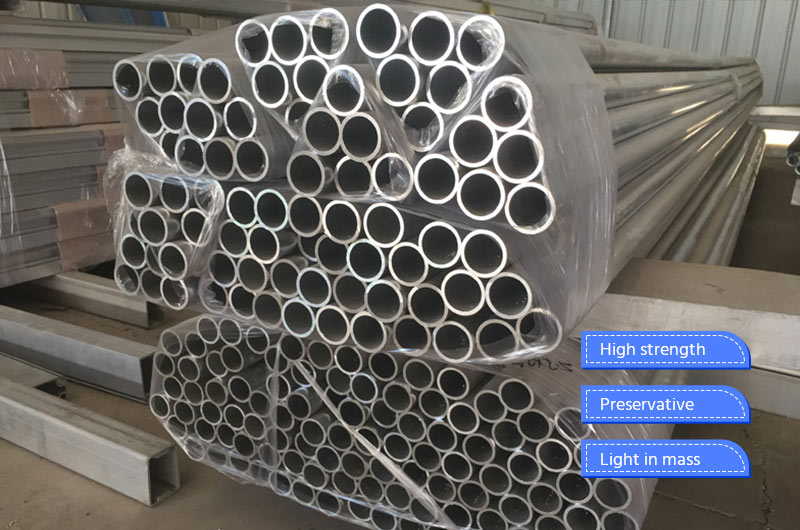
6061-aluminum-tube
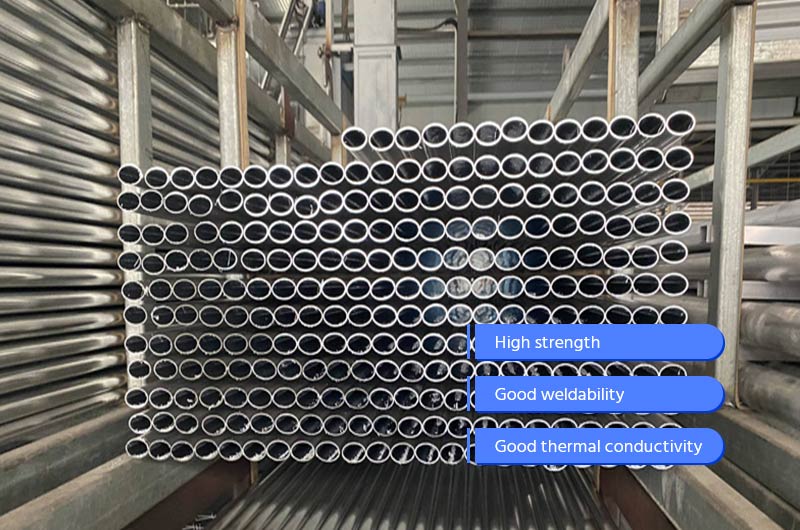
6063-aluminum-tube
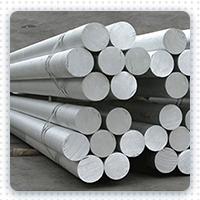
7075-aluminium-rod
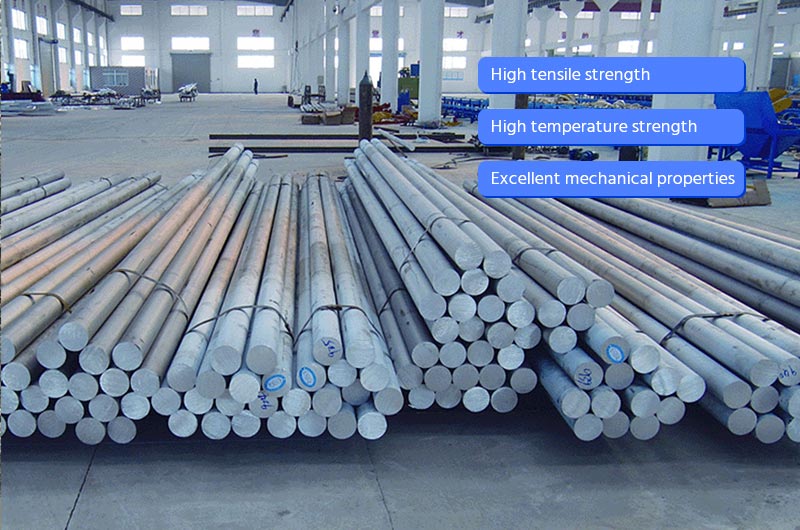
7050-aluminum-bar
Aluminum foil production
Aluminum foil is produced by belt production in minimum thickness up to 0.0025mm and width up to 1800mm. Aluminum foil rolling is rolling without roll gap, and the rolls are always in a state of elastic flattening. During rolling, the thickness of the foil can be controlled by adjusting the rolling force, rolling speed and controlling the tension.
Aluminum foil can be divided into industrial aluminum foil and packaging aluminum foil. The chemical composition of industrial aluminum foil is relatively pure, and the thickness is 0.005-0.2mm. It is mainly used as capacitors, heat insulation materials, and moisture-proof materials in the electrical and electronic industries. Packaging aluminum foil thickness is generally 0.007- 0.1mm. There are flat foil, printed foil, colored printed foil and paper-mounted aluminum foil and other products, mainly used as packaging materials for food, tea, cigarettes, etc.
Plate and strip production adopts flat roll rolling, and the basic processes are hot rolling, cold rolling, heat treatment and finishing. Cold rolling is often carried out at room temperature. Through cold rolling, thinner sheets and strips with precise dimensions, smooth surfaces and flat surfaces can be obtained, and work-hardened sheets and strips with specific mechanical properties can be obtained.Quick Quote
Common applications of aluminum foil products
- Food packaging, food bags, food boxes, tea packaging, candy packaging, chocolate packaging, etc.
- Tablet packaging, pill packaging, injection packaging, infusion bags, etc.
- Cosmetic packaging, cosmetic bags, cosmetic boxes, etc.
- Cigarette packaging, cigarette linings, etc.
- Capacitor dielectric, capacitor leads, etc.
- Building roofs, building walls, building insulation materials, etc.
- Interior decoration, furniture decoration, wallpaper, etc.
Popular aluminum foil products
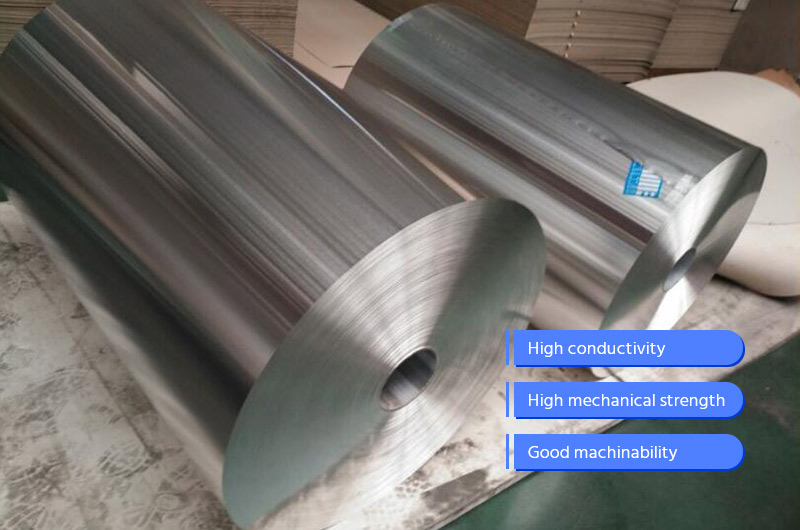
capacitor-foil
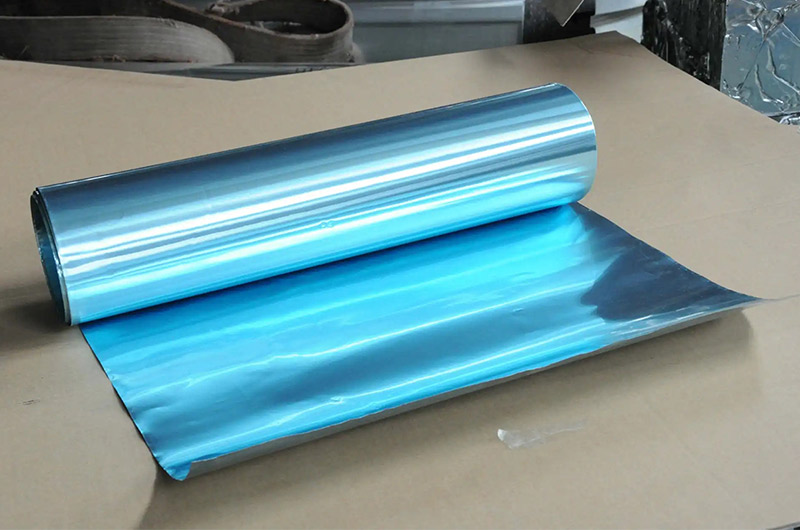
coated-aluminum-foil
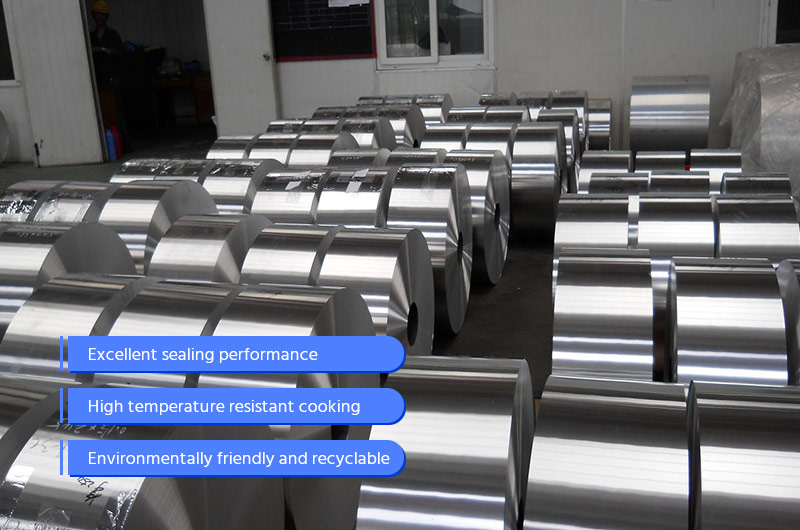
pet-food-container-foil
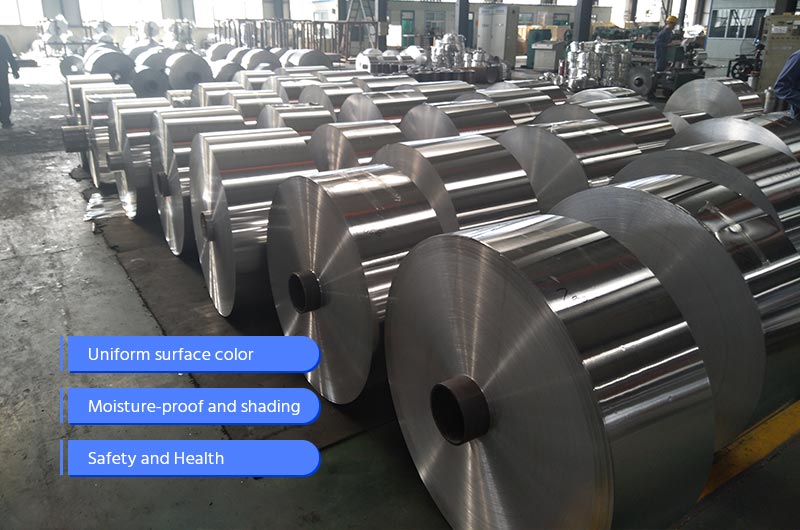
heat-seal-foil
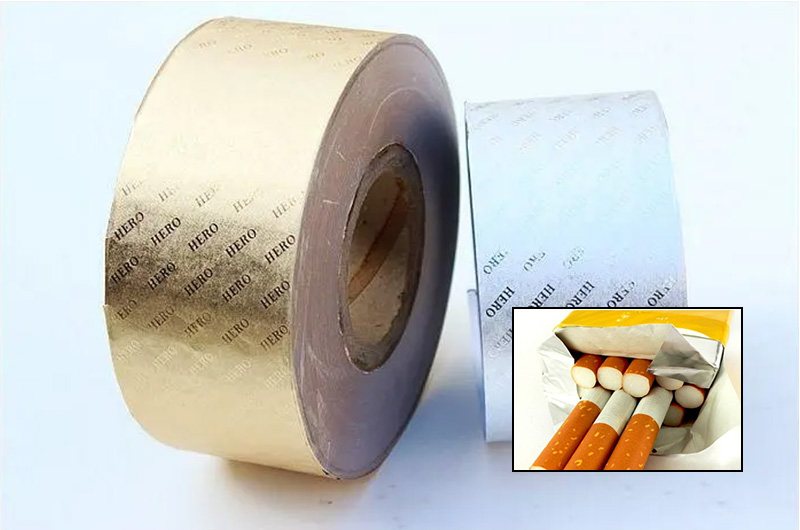
cigarette-packaging-foil
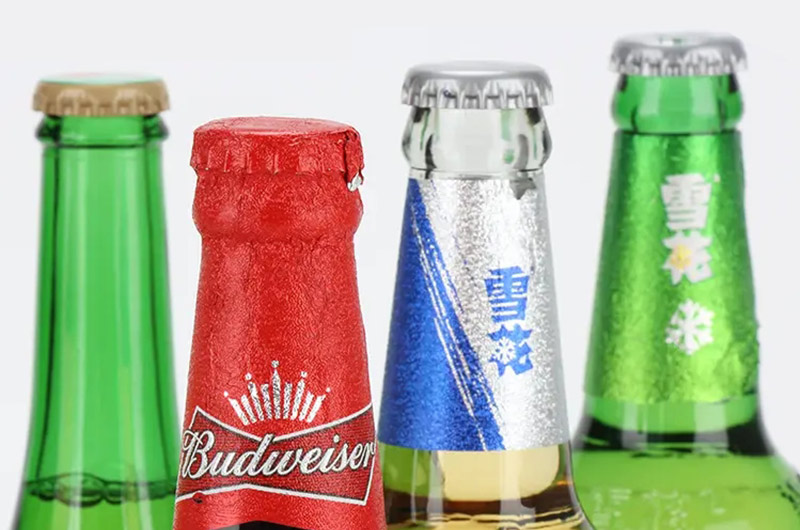
aluminum-foil-for-beer-label
Aluminum wire production
Aluminum is mainly produced by stretching process. Products include rivet wire, welding rod and wire. Billets are produced by extrusion, rolling or continuous casting and rolling. The extrusion method produces the billet, which has greater flexibility and better product performance. The rolling method and the continuous casting and rolling method are suitable for the production of billets of a single alloy variety, and the production efficiency is high.
Common applications of aluminum wire products
- Power cables: transporting electrical energy.
- Communication cables: transmitting information.
- Building Wiring: Indoor and Outdoor Wiring.
- Electronic components: leads of capacitors, resistors, inductors.
- Packaging materials: cigarette packaging, food packaging.
- Others: daily necessities, medical equipment.
Popular aluminum wire products
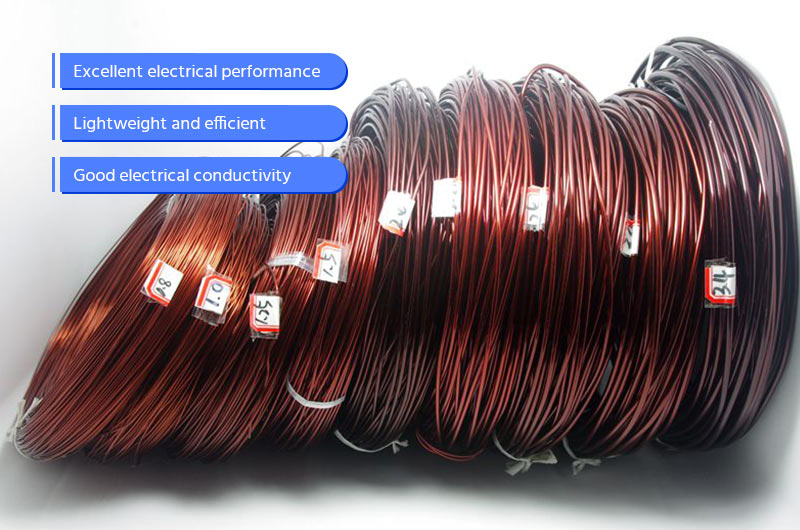
enameled-magnet-wire
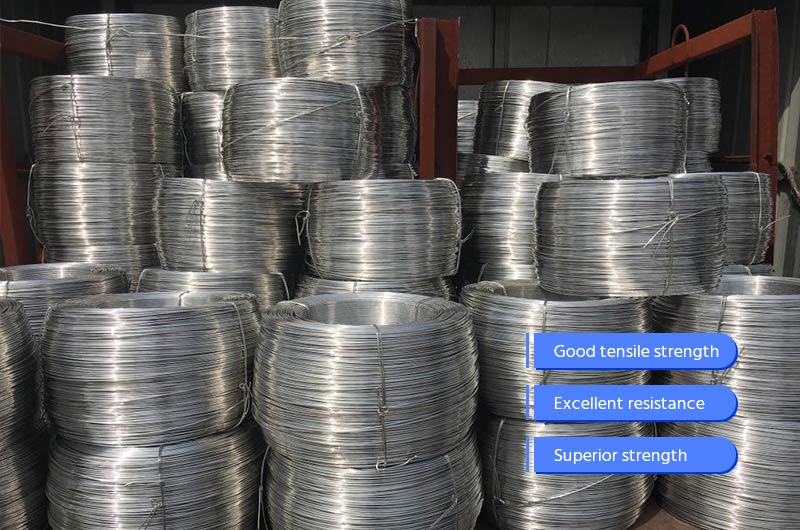
intermediate-strength-wire
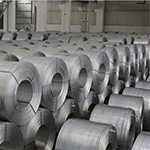
aluminum-conductor-wire-rod
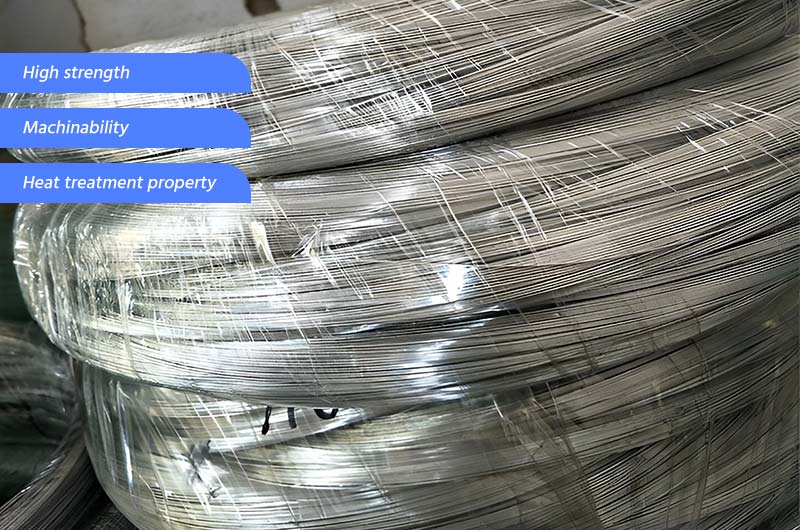
2024-aluminum-wire
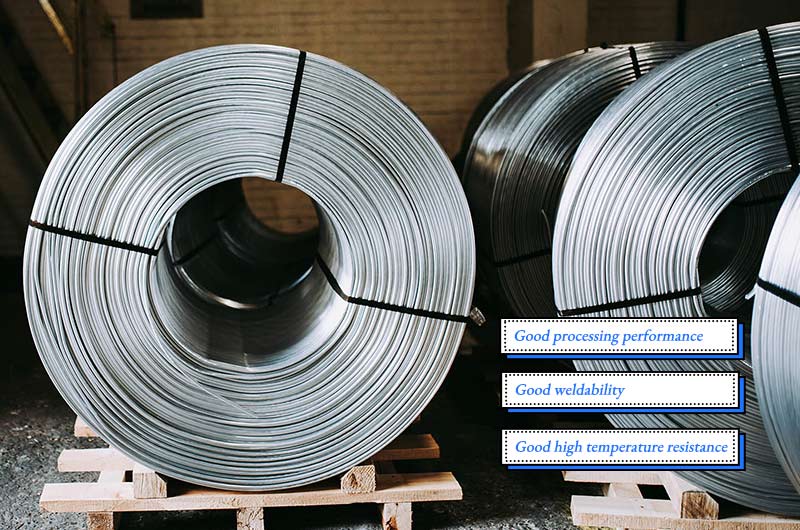
6061-wire
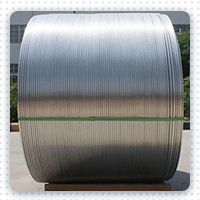
6101-wire
Aluminum forging production
Aluminum is mainly used in aircraft and machine building. Forgings are divided into free forgings and die forgings, and the blanks are cast and extruded blanks. The largest die forging hydraulic press is 70, 000 tons, and the projected area of the largest forging is 4.5 m2. The critical deformation rate of aluminum alloy is about 5-15%. In order to avoid the formation of coarse grains, the deformation rate of die forging should generally be greater than 15%. In order to reduce uneven deformation, multi-directional free forging is often used.Quick Quote
Common applications of aluminum forging products
- Aerospace: aircraft fuselage, wings, landing gear, engine components, etc.
- Automotive: wheels, suspension system components, steering knuckles, engine components, etc.
- Machinery: machine tool components, robot components, hydraulic cylinders, bearings, etc.
- Electronics: radiators, casings, conductive strips, circuit boards, etc.
- Construction: doors, windows, curtain walls, frames, decorative profiles, etc.
Popular aluminum forging products
Processing of aluminum and aluminum alloy
Aluminum and aluminum alloy processing can be divided into hot processing, cold processing and warm processing.
Thermal processing of aluminum
Thermal processing refers to the plastic forming process of aluminum and aluminum alloy ingots above the recrystallization temperature. During thermal processing, the billet has high plasticity and low deformation resistance, and products with large deformation can be produced with equipment with small capacity. Common aluminum alloy thermal processing methods include hot extrusion, hot rolling, hot forging, hot upsetting, liquid die forging, semi-solid forming, continuous casting and rolling, continuous casting and rolling, continuous casting and extrusion, etc.Quick Quote
Cold working of aluminum
Cold working refers to the plastic forming process completed below the temperature that does not produce recovery and recrystallization. The essence of cold working is the combined process of cold working and intermediate annealing. Cold processing can produce final products with smooth surface, precise size, good structure and performance, and can meet different performance requirements. The most common cold processing methods are cold extrusion, cold upset forging, cold rolling of pipes, cold drawing, cold rolling of strips and foils, cold stamping, cold bending, spinning, etc.
Warm processing of aluminum
Warm working is a plastic forming process between cold and hot working. The main purpose of warm working is to reduce the deformation resistance of metals and improve the plastic properties (workability) of metals. The most common warm working methods are warm extrusion, warm rolling, warm upsetting, etc.
Aluminum adopts different processing methods according to the specific use requirements. The main processing methods include hot processing, cold processing, solution heat treatment, aging treatment, annealing treatment, etc. According to different processing methods, the TEMPER of aluminum processing products can be summarized as follows:
Other plastic forming methods for aluminum
Aluminum have also researched and developed a variety of new aluminum processing methods, which are mainly:
- Pressure casting forming methods, such as low, medium and high pressure forming, extrusion forming, etc.
- Semi-solid forming methods, such as semi-solid rolling, semi-solid extrusion, semi-solid drawing, liquid die forging, etc.
- Continuous forming methods, such as continuous casting and extrusion, high-speed continuous casting and rolling, conform continuous extrusion, etc.
- Composite forming methods, such as lamination rolling method, multi-billet extrusion method, etc.
- Deformation heat treatment, etc.
Among aluminum alloy processing materials, rolled materials (plates, strips, strips, foils) and extruded materials (tubes, rods, shapes, wires) are the most widely used and the largest output.