We are a technologically advanced manufacturer specializing in aluminum alloy anodizing, known for our high-quality products. With extensive experience, we have compiled a list of 14 common defects in aluminum alloy anodizing.Quick Quote
1. Thin film in hanging material causes light coloring, even no coloring
Main Cause: Loose binding of material or loosening after alkali etching, leading to poor contact between material and conductor rod.
Solution: Tighten the binding wire further with pliers after alkali etching.
2. Partial burn of oxidation film results in blackening
Main Cause: Poor contact between aluminum parts and conductor rod or insufficient contact area, unclean film on conductor rod, or short circuit between anode and cathode.
Solution: Improve contact and eliminate anode-cathode contact.
3. Dark film layer
Main Cause: Issues with alloy composition, interruption of current during oxidation, low electrolyte concentration, high oxidation voltage, poor pretreatment.
Solution: Improve ingot quality if it's a material issue, or strengthen pretreatment if it's a treatment issue. Adjust electrolyte content, sulfuric acid concentration, and appropriately reduce voltage.
4. Fingerprints appearing
Main Cause: Touching the anodized film with fingers during operation.
Solution: Wear clean gloves and avoid touching with fingers as much as possible.
5. Poor corrosion resistance
Main Cause: High concentration of sulfuric acid, aluminum ion content exceeds 20g/L.
Solution: Maintain sulfuric acid concentration between 150-200 g/L. Consider replacing 1/2-3/4 bath fluid if aluminum ion exceeds 20 g/L.
6. Yellowing
Definition: Impurities mixed in the oxide film cause the film to turn yellow.
Phenomenon: The color tone changes when this film is used for electrolytic coloring.
Causes: Iron, silicon, etc., in the electrolyte or alloy material mix into the film.
Countermeasures: Reduce the concentration of iron, silicon, etc., in the alloy and electrolyte. Optimize anodizing conditions.
7. Overlapping
Definition: Abnormal film formation due to material overlapping during oxidation.
Phenomenon: Can see the imprint of overlapped profiles, sometimes can see partial rainbows (interference color).
Causes: Possible abnormal contact due to dense arrangement of aluminum materials during electrolysis.
Countermeasures: Maintain appropriate binding spacing, tighten fixtures, remove deformed fixtures, and do not hang deformed, bent profiles.
8. Accumulated gas (air pockets)
Definition: The gas produced during electrolysis or the air used for stirring remains in the gaps or corners of the material.
Phenomenon: The film is very thin or non-existent at the gaps or corners of the material, and it cannot obtain uniform color during electrolytic coloring.
Causes: Unsuitable hanging angle or material shape affects gas and air retention.
Countermeasures: Use hanging angles and loading methods that allow gas to escape easily.
9. Black spots
Definition: Black or white spots appear after anodizing due to the local precipitation of β’ intermediate phase.
Causes: The belly button material undergoes rapid cooling and reheating, leading to the precipitation of the intermediate phase (Mg2Si).
Countermeasures: Suppress reheating with cooling fans and reduce the thermal conductivity of the materials in contact with extruded materials.
10. Powdering (powdery film)
Definition: White powder forms on the surface of the film after anodizing.
Phenomenon: After anodizing, the film appears powdery and opaque.
Causes: Long-time electrolysis in high temperature, high concentration electrolyte, or long-time immersion after electrolysis.
Countermeasures: Lower electrolyte concentration and temperature, reduce aluminum ion content, and shorten immersion time.
11. Short circuit (electric corrosion, melting film, sparking)
Definition: Material dissolves partially due to contact with the electrode during electrification.
Phenomenon: The material and the electrode short-circuit, and part of the material dissolves due to excessive current.
Causes: Material and electrode contact, or a short circuit occurs through fallen profiles.
Countermeasures: Improve arrangement, prevent material sway, remove fallen materials, and adjust electrode spacing.
12. Poor electrolysis (poor electrification)
Definition: Poor conductive contact during anodizing, different from the set current value, almost no film is generated.
Phenomenon: Sometimes rainbows (interference color) can be seen on both sides, and normal electrolytic coloring cannot be performed.
Causes: Interruption of electrolysis due to power outage, power supply failure, deteriorated, contaminated fixtures.
Countermeasures: Strengthen management of fixture joints, increase contact area, and confirm set current values.
13. Milky white
Definition: Impurities mixed in the anodized film, causing the film structure to differ and appear milky white.
Phenomenon: The film lacks transparency and turns white.
Causes: High-temperature electrolytic treatment, short hot water wash time, poor extrusion conditions, fluctuations in the content of silicon, iron, manganese, etc.
Countermeasures: Normalize anodizing treatment conditions, normalize water wash conditions, confirm set current values, and adjust alloy components.
14. Film burns (burns)
Definition: During anodizing treatment, the local current density is too high, forming a burn-like appearance.
Phenomenon: During anodizing treatment, the local concentration of current increases the temperature, and the film thickness increases, becoming whitened and powdery.
Causes: Insufficient contact area, too close proximity between electrode and material, etc., leading to locally high current density.
Countermeasures: Ensure appropriate contact point area, improve electrode configuration, increase bath fluid circulation, ensure uniformity, set appropriate current density, and optimize process conditions, especially determining the content of aluminum ions.Quick Quote
Popular anodized products
Anodized aluminum is a truly versatile material that can be used to create a wide variety of products. Its durability, corrosion resistance, and attractive appearance make it a popular choice for many different applications.Quick Quote
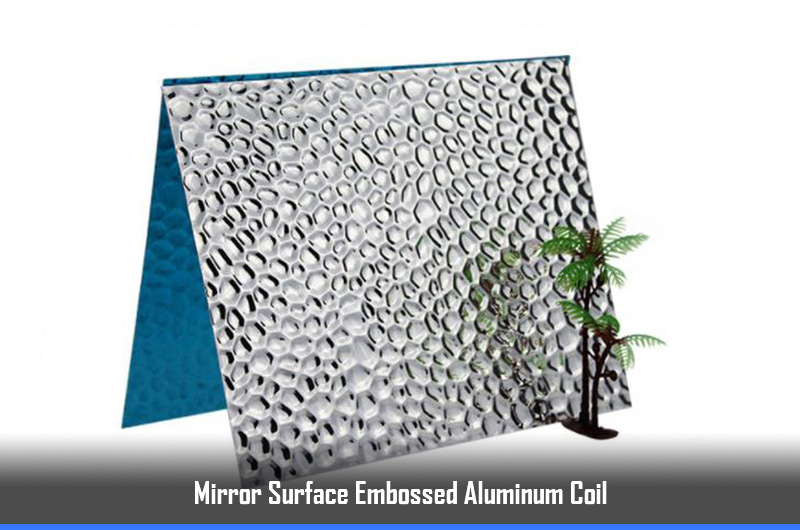
stucco-embossed-coil

aluminum-in-kitchen
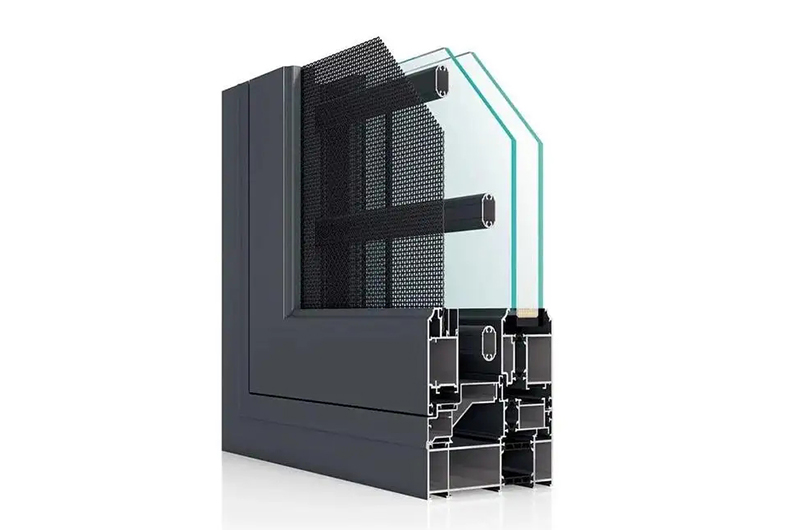
aluminum-profile-door-window
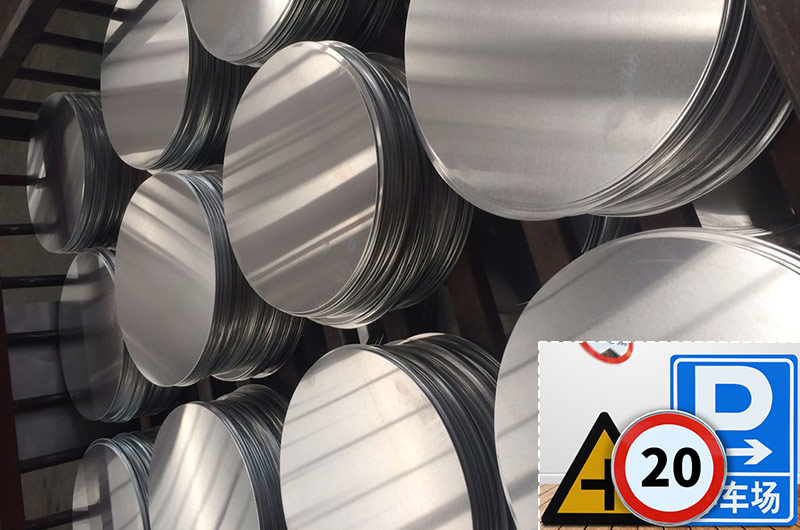
aluminum-sign-blank
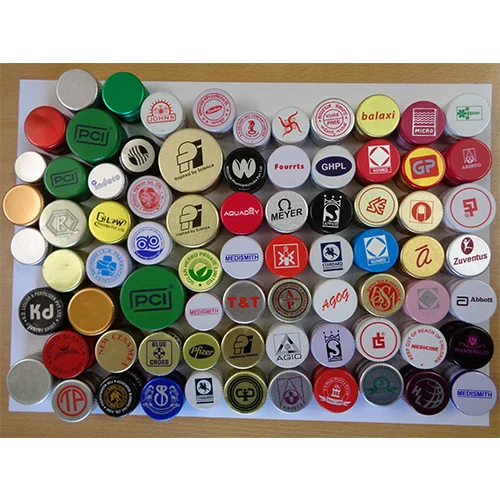
8011-cap
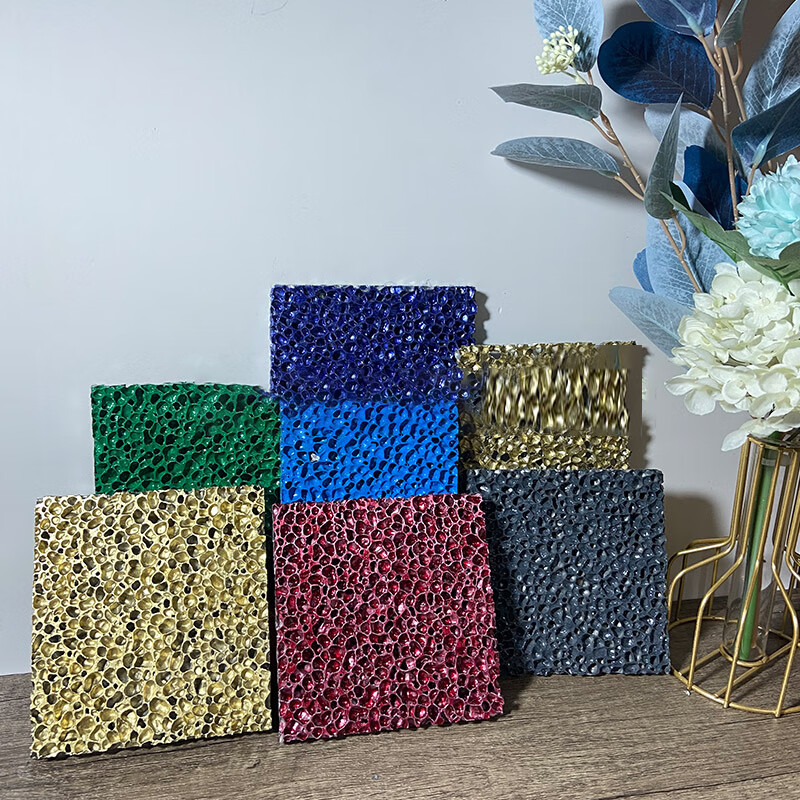
porous-foam-sheet-plate
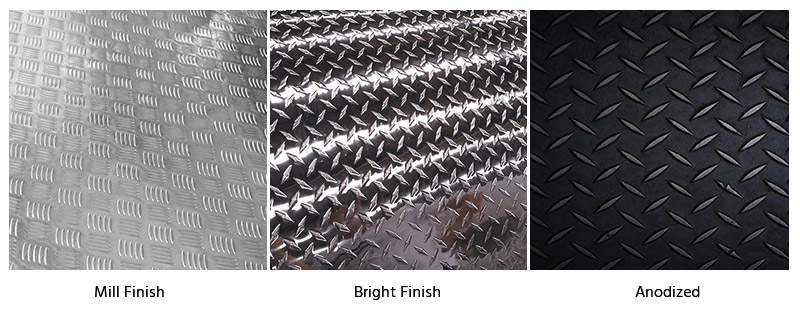
tread-checkered-plate
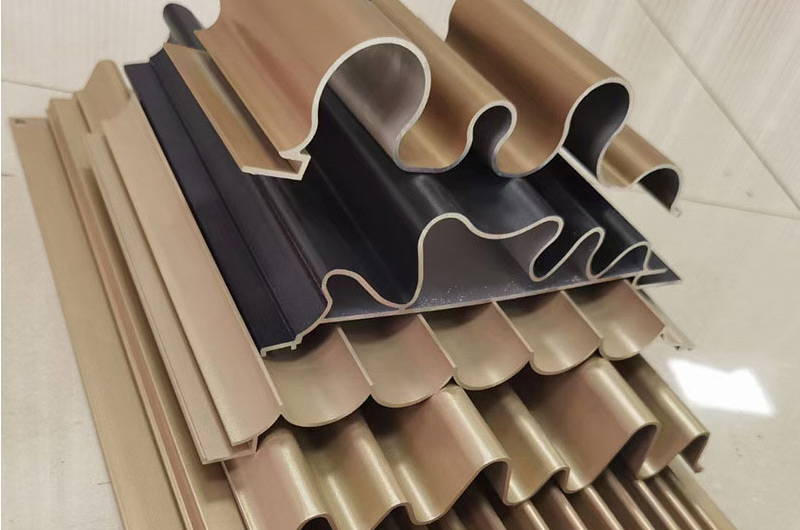
corrugated-sheet
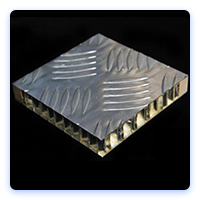
aluminum-honeycomb-plate
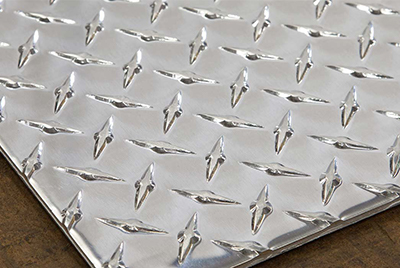
diamond-plate
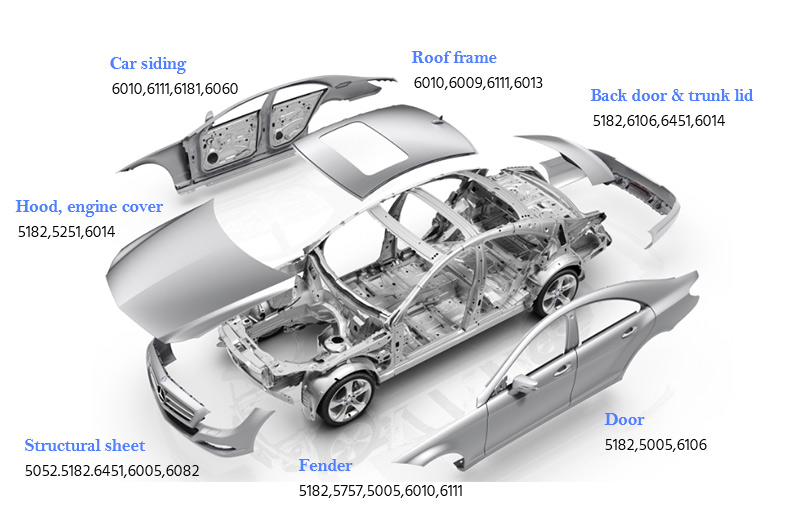
auto-body-aluminum-panel
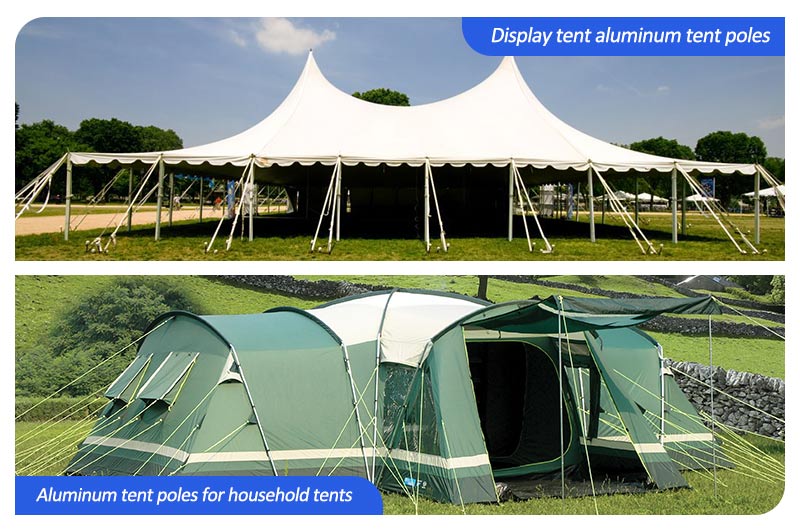
tent-pole