In industries such as aerospace, military equipment, rail transit, and high-end automotive manufacturing, materials must meet demanding standards for strength, durability, and lightweight performance. 7075 aluminum forgings have become an ideal solution for these sectors due to their steel-like strength, outstanding fatigue resistance, and excellent corrosion resistance.Welcome to contact
- Tempers: 7075-T6, 7075-T652, 7075-T73, 7075-T7352, 7075-T74, 7075-T7452
- Standards: ASTM B247, AMS 4126, AMS 4131, AMS 4141, AMS 4147, AMS-A-22771
- Certifications: AS9100, ISO 9001, ISO 14001, NADCAP HT, NADCAP NDT, IATF 16949
Tempers of 7075 Aluminum Forgings
7075 aluminum alloy is a heat-treatable, high-strength alloy. Different tempers directly affect its mechanical properties, corrosion resistance, and machinability. According to end-use requirements, 7075 aluminum forgings can be supplied in T6, T652, T73, T7352, T74, and T7452 tempers. Each offers a distinct balance of strength, toughness, and corrosion resistance.
-
7075-T6 Aluminum Forging | High Strength for Load-Bearing Parts
Solution heat treated + artificially aged (120°C × 24h) to achieve maximum strength. Tensile strength up to 510 MPa, though lower in toughness and moderate in corrosion resistance. Best for high-load, impact-resistant structures.
Typical Applications: Landing gear components, structural frames, racing suspensions, precision mold bases
ASTM B247 AMS 4126 AMS-A-22771 -
7075-T652 Aluminum Forging | Stress Relief for Enhanced Stability
Based on T6, with Hot Isostatic Pressing (HIP) to eliminate residual casting stress. Mechanical properties are similar to T6, but offers superior dimensional stability, suitable for parts requiring precision machining.
Typical Applications: Satellite structures, engine mounts, missile launch units, CNC precision parts
ASTM B247 AMS 4310 AMS 4147 -
7075-T73 Aluminum Forging | Corrosion Resistance with Reduced Strength
Long-duration over-aging (160°C × 48h) lowers strength to gain excellent stress corrosion cracking (SCC) resistance, ideal for humid, marine, or aerospace environments.
Typical Applications: Wing joints, missile casings, ship structures, high-speed rail load frames
ASTM B247 AMS 4131 -
7075-T7352 Aluminum Forging | SCC Resistance + High Toughness
Built on T73 with added cryogenic treatment to further enhance corrosion resistance. Slightly lower strength than T73 but better fracture toughness. Suited for extreme conditions with prolonged stress and humidity.
Typical Applications: Aircraft landing gear, offshore platforms, crane arms, mining machinery
AMS 4141 AMS 4147 -
7075-T74 Aluminum Forging | Balance of Strength & Corrosion Resistance
Intermediate aging for moderate strength and improved corrosion resistance. Offers a middle ground between T6’s strength and T73’s corrosion resistance.
Typical Applications: Missile parts, UAV frames, rail suspensions, armored vehicle structures
ASTM B247 AMS 4311 -
7075-T7452 Aluminum Forging | Military & Aerospace Use
Built on T74 with additional cold treatment to boost fatigue performance, impact resistance, and dimensional stability. Ideal for high-shock, high-vibration environments.
Typical Applications: Fighter aircraft parts, armored protection components, engine housings, heavy lifting systems
AMS 4323 AMS 4141
Mechanical Properties of 7075 Aluminum Forgings
Temper | Tensile Strength (MPa) | Yield Strength (MPa) | Elongation (%) |
7075-T6 | 510–538 | 434–476 | 5–8 |
7075-T73 | 505 | 435 | 13 |
7075-T7352 | 462–538 | 372–462 | 3–9 |
The temper condition of 7075 aluminum forging directly determines its strength, toughness, and corrosion performance. Selecting the appropriate temper ensures long-term performance under extreme conditions:
- Need maximum strength? → Choose T6 or T652
- Need corrosion resistance? → Choose T73 or T7352
- Need strength + corrosion resistance? → Choose T74
- Military/Aerospace grade? → Choose T7452
Chalco offers the full range of 7075 aluminum forging heat treatments, with custom tempering options to ensure optimal performance tailored to your specific applications. Quick Quote
7075 Aluminum Forging Product Categories
Due to its ultra-high strength, excellent fatigue resistance, and outstanding machinability, 7075 aluminum forging is widely used in aerospace, defense, and rail transit industries. Based on application needs, 7075 aluminum forgings are available in various forms, including forged rings, bars, plates, discs, blocks, tubes, flanges, and custom-shaped forgings. Each category differs in size range, production process, and mechanical properties.
7075 Forged Aluminum Plates
-
Formed using open-die forging or multi-directional press forging, combined with isothermal forging technology, these plates offer reduced residual stress and enhanced dimensional stability. Ultrasonic inspection per ASTM B594 ensures uniformity and internal integrity.Quick Quote
Tempers: 7075-T6, T652, T73, T7352, T74
Standards: ASTM B247, AMS 4126, AMS 4131, AMS 4141, AMS 4147, AMS-A-22771
Thickness: 20 – 300 mm
Surface Roughness: Ra 3.2 – 6.3 μm (as-forged)
Product Types
- 7075 Thick Forged Plate
- 7075 Lightweight Plate
- 7075 Armor Forged Plate
Features
- Enhanced mechanical strength over rolled plates via open-die forging + heat treatment
- Uniform grain structure across thickness, eliminating delamination risks
- Improved corrosion resistance suitable for high-humidity and salt-spray environments
Typical Applications
- Aerospace: Aircraft skin reinforcement frames, satellite structural parts
- Defense: Ballistic armor plates, military electronic enclosures
- High-End Manufacturing: Vacuum chambers for semiconductors, precision mold base plates


7075 Forged Aluminum Bars
-
Chalco utilizes 50MN–100MN high-tonnage forging equipment, employing open-die and radial forging to ensure dense internal structures and consistent mechanical properties across all directions. For ultra-long bars, spray quenching is applied to reduce residual stress, followed by cold sizing to achieve precision tolerances up to H9 class.Quick Quote
Tempers: 7075-T6, T652, T73, T7352, T74, T7452
Standards: ASTM B247, AMS 4126, AMS 4131, AMS 4141, AMS 4147, AMS-A-22771
Size 1: Diameter ≤ 800 mm, Length ≤ 2000 mm
Size 2: Diameter 801–2000 mm, Length ≤ 1500 mm
Weight: ≤ 5T
Concentricity: ≤ 0.1 mm/m
Product Types
- 7075 Aerospace Forged Bar
- 7075 Precision Robotic Shaft
- 7075 Hydraulic Piston Rod
Key Features
- Axially aligned grain structure improves longitudinal fatigue strength by 20–30% over rolled bars
- Suitable for high-load, high-precision uses in aerospace, defense, and rail transit
- Available in ultra-long, large-diameter bars (up to 12m), ideal for oversized components
Typical Applications
- Aerospace: Helicopter rotor shafts, landing gear struts
- Defense: Missile structural components, armored vehicle parts
- Rail: Drive shafts for high-speed trains
- Precision Machinery: Input shafts for robotic harmonic reducers, hydraulic piston rods


7075 Forged Aluminum Tubes
-
Chalco produces 7075 forged tubes using mandrel elongation or extrusion forging, enhanced by rotary swaging for uniform wall thickness. Inner surfaces can be honed or electropolished to achieve roughness as low as Ra ≤ 0.8 μm, ideal for high-precision piping systems.Quick Quote
Tempers: 7075-T6, T652, T73, T7352, T74
Standards: ASTM B247, AMS 4126, AMS 4131, AMS 4141, AMS 4147, AMS-A-22771
Outer Diameter: ≤ 830 mm
Wall Thickness: ≤ 90 mm
Length: ≤ 1800 mm
OD-to-Wall Ratio: 5:1 to 50:1
Ovality: ≤ 0.5% OD
Product type:
- 7075 Hydraulic Tubing
- 7075 Racing Roll Cage Tubing
- 7075 Thin-Walled Tubing
Key Features
- High strength and lightweight, ideal for structural components under high pressure or mechanical load
- Wall thickness tolerance up to ±0.5 mm, suitable for aerospace and racing industries
- Pressure-tested per ASME B31.3 to ensure structural integrity
Typical Applications
- Aerospace: Aircraft hydraulic oil pipelines
- Motorsports: Roll cage structures for racing cars
- Scientific Equipment: Vacuum beamline pipes in particle accelerators


7075 Forged Aluminum Rings
-
Chalco utilizes 50MN–80MN heavy-duty hydraulic forging equipment to produce rings with high density, no porosity, and no inclusions, ensuring reliability under extreme conditions. Large-diameter rings undergo multi-pass heating with cumulative deformation up to 80%. For custom-shaped rings (e.g., L- or T-section), stepwise rolling is applied.Quick Quote
Tempers: 7075-T6, T652, T73, T7352, T74, T7452
Standards: ASTM B247, AMS 4126, AMS 4310, AMS 4311, AMS-A-22771
Outer Diameter (Quenched): ≤ 2500 mm
Outer Diameter (Unquenched): ≤ 4000 mm
Height: ≤ 500 mm
Weight: ≤ 5T
Minimum Wall Thickness: ≥ 15 mm
Radial-to-Axial Deformation Ratio: Typically 1:0.3–0.6
Concentricity: ≤ 0.1% D (Aerospace-grade)
Product type:
- 7075 Rolled Forged Ring
- 7075 Aluminum Bearing Rings
- 7075 Large-Diameter Rings
- Ring rolling process ensures excellent toughness, fatigue resistance, and high-temperature performance
- Seamless forging guarantees uniform internal structure and enhanced mechanical strength
- Ideal for extreme environments: high-speed rotation, elevated temperatures, or corrosive media
Typical Applications
- Aerospace: Rocket tank flanges, satellite support rings, engine sealing rings
- Rail Transit: Turbine housings, high-speed train wheels
- Renewable Energy: Main bearing housings for wind turbines
- Nuclear Power: Reactor pressure vessel sealing rings


7075 Forged Aluminum Flanges
-
Chalco manufactures 7075 forged flanges using closed-die forging, with bolt holes pre-formed during forging to minimize post-processing. A machining allowance of 0.3–0.5 mm is reserved on sealing surfaces to ensure high-precision fit.Quick Quote
Tempers: 7075-T6, 7075-T73
Standards: ASTM B247, AMS 4126, AMS 4310, AMS 4311, AMS-A-22771
Diameter: ≤ 1500 mm
Thickness: 10 mm – 150 mm
Flatness Tolerance: ≤ 0.05 mm/100 mm
Product type:
- 7075 Pipe Flange
- 7075 Hydraulic Flange
- 7075 High-Pressure Flange
Key Features
- Exceptional strength and sealing performance, suitable for high-pressure, high-temperature applications
- Neck radius ≥ 3t (t = neck thickness), improving fatigue life under dynamic loads
- Manufactured in accordance with ASME B16.5 for high-precision sealing reliability
Typical Applications
- Aerospace: Propellant pipeline connections in spacecraft
- Marine Engineering: Pressure flanges in deep-sea exploration modules
- Industrial Equipment: End caps for ultra-high-speed centrifuges


7075 Forged Disc/Pancake
-
Chalco produces 7075 forged discs using open-die upsetting, ensuring continuous metal flow and enhanced mechanical properties. Ideal for high-stress applications, the discs offer isotropic strength. Optional ultrasonic inspection complies with ASTM E317 to detect internal flaws.Quick Quote
Tempers: 7075-T6, T652, T73, T7352, T74
Standards: ASTM B247, AMS 4126, AMS 4131, AMS 4141, AMS 4147, AMS-A-22771
Diameter: ≤ 2500 mm
Thickness: ≤ 400 mm
Weight: ≤ 5T
Key Features
- Isotropic mechanical properties, reducing directional strength variations (anisotropy index ≤ 1.1)
- High strength and fatigue resistance, suitable for extreme operating environments
- Optimized grain size (ASTM 8–10), ensuring stability and reliability of machined parts
Typical Applications
- Gear Blanks: Planetary gears, synchronizer rings
- Turbine Rotors: Blanks for gas turbines, missile engine rotors
- Sealing Covers: High-pressure end caps for nuclear reactors


7075 Forged Block/Ingot
-
Chalco utilizes multi-directional forging to increase material density and reduce internal porosity in 7075 forged blocks. Ideal for CNC machining, these blocks can be customized to near-net shapes to reduce material waste. Compared to cut plates, they can save 15–30% in raw material costs.Quick Quote
Tempers: 7075-T6, T652, T73, T7352, T74
Standards: ASTM B247, AMS 4126, AMS 4131, AMS 4141, AMS 4147, AMS-A-22771
Length: ≤ 7000 mm
Width: ≤ 2000 mm
Height: ≤ 500 mm
Weight: ≤ 9T
Length-to-Width Ratio: ≤ 3:1
Key Features
- High density (≥ 2.81 g/cm³) with porosity < 0.2%
- Excellent for 5-axis CNC machining, providing a stable and precise base
- Optimized grain flow orientation improves overall strength and fatigue performance
Typical Applications
- Mold Base: High-precision stamping molds, forging die blocks
- Heavy Machinery Base: Jaw crusher seats in mining equipment
- Aerospace & Automotive Components: Complex surface parts via multi-axis machining


7075 Forged Shaft
-
Chalco applies radial forging combined with localized upsetting to ensure axial grain continuity and improved torsional strength, which is 18–25% higher than that of machined shafts. Hollow shafts are produced via mandrel elongation, reducing weight and machining costs. For stepped shafts, segmented forging is used with temperature differential controlled within ±20°C.Quick Quote
Tempers: 7075-T6, T652, T73, T7352, T74
Standards: ASTM B247, AMS 4126, AMS 4131, AMS 4141, AMS 4147, AMS-A-22771
Max Length: ≤ 7000 mm
Max Diameter: ≤ 800 mm
Weight: ≤ 8T
Typical Applications
- Marine Propeller Shafts
- Main Shafts for Ultra-Speed Centrifuges
- Electric Racing Car Drive Axles


7075 Forged Gear Blank
-
Chalco uses precision closed-die forging to produce gear blanks with continuous grain flow along the tooth surface, reducing cutting volume while enhancing mechanical strength. Pre-formed tooth profiles allow for fine finishing (0.5–1 mm allowance), and optimized fillet radii (ASTM Grade 7) improve fatigue strength.Quick Quote
Tempers: 7075-T6, T652, T7352
Standards: ASTM B247, AMS 4126, AMS 4147, AMS-A-22771
Dimensions: Customizable per customer requirements
Key Features
- Surface hardness up to HV600 after nitriding, significantly improving wear resistance
- Reduces material usage by 40% and shortens production cycle by 60% compared to full machining
Typical Applications
- Helicopter Main Gearbox Gears
- Differential Bevel Gears for Electric Vehicles


7075 Forged Housing
-
AChalco employs isothermal forging (dies preheated to 400°C) to ensure both strength and dimensional stability in thin-walled housings. Reinforcing ribs are directly forged to minimize post-processing. Flatness can reach ≤ 0.1 mm/100 mm, and surface roughness Ra ≤ 1.6 μm, eliminating the need for secondary finishing.Quick Quote
Tempers: 7075-T6, T652, T7352
Standards: ASTM B247, AMS 4126, AMS 4147, AMS-A-22771
Dimensions: Customizable per client drawings
Typical Applications
- Aerospace Engine Accessory Casings
- Missile Seeker Head Housings
- Industrial Robot Wrist Enclosures
- Radar Waveguide Housings (Deep Thin-Walled Structures)


7075 Custom-Shaped Forgings
-
7075 custom-shaped forgings are engineered for complex structures, high-load conditions, and extreme environments, widely used in aerospace, defense, and precision machinery. Given their intricate geometries, Chalco employs advanced techniques such as isothermal forging, multi-directional die forging, and localized reinforcement forging to ensure high strength, fatigue resistance, and dimensional accuracy.Quick Quote
Custom Forging Types
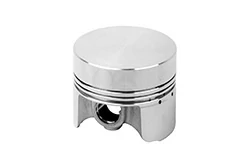
7075 Forged Piston
For heavy-duty aerospace diesel engines and high-performance racing engines
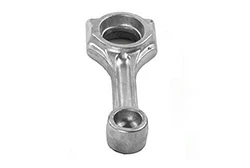
7075 Forged Connecting Rod
50% lighter than steel rods, with 40% higher fatigue limit
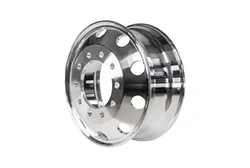
7075 Forged Wheel Hub
Mold forged and heat-treated for racing and military off-road applications
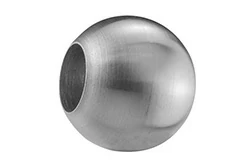
7075 Hollow Variable-Section Forgings
Isothermal + flow forming for missile fins, spacecraft frames
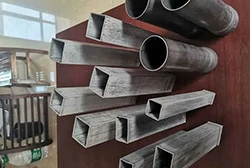
7075 Thin-Walled Deep-Cavity Forgings
Precision closed-die forging for radar waveguides and optical housings
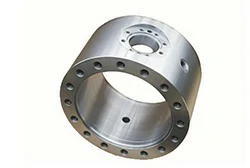
7075 Forged Valve Body
One-piece multi-channel forging for aerospace propulsion and deep-sea hydraulic systems
7075 Forging Production Capabilities Overview
Forging Method | Product Type | Max Weight | Max Dimensions |
Open-Die Forging | Forged Block / Plate | ≤9T | Length ≤ 7000 mm, Width ≤ 2000 mm, Height ≤ 500 mm |
Forged Disc | ≤5T | Diameter ≤ 2500 mm | |
Forged Ring | ≤5T | OD ≤ 2500 mm (quenched), ≤ 4000 mm (non-quenched), Height ≤ 500 mm | |
Forged Bar | ≤5T | Ø 200–800 mm, Length ≤ 2000 mm; Ø 801–2000 mm, Length ≤ 1500 mm | |
Forged Shaft | ≤8T | Length ≤ 7000 mm, Ø ≤ 800 mm | |
Backward Extrusion | Forged Tube | OD ≤ 830 mm, ID ≤ 650 mm, Length ≤ 1800 mm | |
Closed-Die Forging | Standard Parts | - | PVA ≤ 3.0 ㎡ (Diameter ≤ 1950 mm) |
Complex Forgings | - | PVA ≤ 1.5 ㎡ (Diameter ≤ 1400 mm) |
Chalco provides complete 7075 aluminum forging solutions, including custom heat treatment, precision machining, and surface finishing tailored to high-end applications in aerospace, military, and transportation industries.
Need expert material selection or a quote? Contact us today to find your ideal 7075 forged solution.
Are You Looking for an Aluminum Supplier?
If you need a professional aluminum supplier to provide you with high-quality, cost-effective aluminum, we will be your best choice.
7075 Forged Aluminum vs 6061 Forged Aluminum: How to Choose the Right Alloy for Your Application?
In the field of aluminum forgings, 7075 forged aluminum and 6061 forged aluminum are two of the most widely used materials. They differ significantly in strength, corrosion resistance, machinability, and cost. Choosing the right alloy starts with understanding their properties and suitable applications.
Comparison Criteria | 7075 Forged Aluminum | 6061 Forged Aluminum |
Main Alloying Elements | Aluminum-Zinc-Magnesium-Copper | Aluminum-Magnesium-Silicon |
Tensile Strength | 83, 000 psi (572 MPa) | 45, 000 psi (310 MPa) |
Yield Strength | 74, 000 psi (510 MPa) | 40, 000 psi (276 MPa) |
Brinell Hardness | 150 HB | 95 HB |
Elongation at Break | 10% | 12% |
Shear Strength | 48, 000 psi (330 MPa) | 31, 000 psi (214 MPa) |
Thermal Conductivity | 130 W/m·K | 170 W/m·K |
Weldability | Poor – prone to cracking | Excellent – suitable for welded structures |
Machinability | Moderate – requires high-performance tooling | Excellent – ideal for CNC and manual machining |
Corrosion Resistance | Low (requires surface treatment in T6 temper) | Excellent – ideal for outdoor applications |
Cost | Higher | Lower |
When to Choose 7075 Forged Aluminum?
7075 forged aluminum is ideal for applications requiring extremely high strength and fatigue resistance. It's widely used in aerospace, military, motorsports, and precision machinery, especially in high-impact and high-load environments.
Recommended Scenarios
- Applications requiring 50–80% more strength than 6061
- Components subject to intense friction or impact (e.g., firearms, race car parts)
- Where lightweight and rigidity are critical (e.g., aerospace, defense systems)
- High-temperature or high-pressure environments (e.g., turbines, space components)
When to Choose 6061 Forged Aluminum?
6061 forged aluminum is known for its excellent corrosion resistance, good weldability, and machinability, making it ideal for general structural applications where extreme strength is not required.
Recommended Scenarios
- Components requiring extensive machining (easy to CNC)
- Assemblies that require welding (excellent weldability)
- Cost-sensitive projects
- Parts used in humid or marine environments (superior corrosion resistance)
How to Select the Right Aluminum Forging?
- Choose 7075 forged aluminum if your project requires maximum strength, lightweight, and you’re able to manage higher costs.
- Choose 6061 forged aluminum for better weldability, machinability, and cost-effectiveness.
- For parts exposed to wet or corrosive environments, 6061 is the more suitable option.
- For components under high load and cyclic fatigue (e.g., aerospace, military, racing), 7075 is the optimal choice.
You Can Also Explore Other Forged Aluminum Products Offered by Chalco
From custom aerospace forgings to high-performance structural components, Chalco provides a comprehensive range of aluminum forging solutions to meet the demands of your specific application.
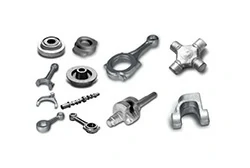
2618 Aluminum Forgings
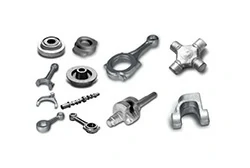
4032 Aluminum Forgings
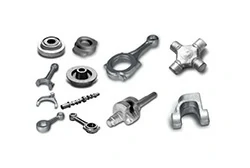
6061 Aluminum Forgings
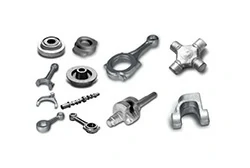
6082 Aluminum Forgings
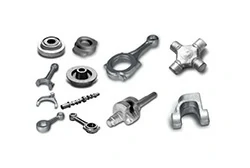
7050 Aluminum Forgings
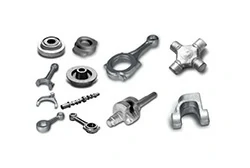
7175 Aluminum Forgings
Chalco can provide you the most comprehensive inventory of aluminum products and can also supply you customized products. Precise quotation will be provided within 24 hours.
Get a quote