During high-speed fighter jet maneuvers, spacecraft re-entry, and prolonged aircraft operation, materials face extreme challenges—overloads, thermal shocks, and long-term fatigue. These demands require materials that are lightweight, strong, durable, and corrosion-resistant.
7075 aerospace aluminum excels under such conditions. Strengthened mainly by zinc and treated with precipitation hardening (T6, T73), it achieves near-steel strength (up to 570 MPa) while being about 60% lighter. This makes it ideal for critical components like fighter jet fuselage frames, landing gear supports, and rocket booster casings. From F-22 and F-35 jets to SpaceX Falcon 9 and NASA spacecraft, 7075 is a key material in modern aerospace structures.
However, not all 7075 aluminum meets aviation-grade standards. Impurities in melting or inadequate NDT and fatigue testing can cause failure to pass certifications like NADCAP or AS9100, making such materials unsuitable for extreme conditions.Welcome to contact
As a dedicated supplier, Chalco provides aerospace-grade 7075 products—plates, bars, tubes, profiles, and forgings—fully compliant with AMS, ASTM, and MIL standards. Backed by AS9100, ISO9001, and NADCAP certifications, Chalco ensures reliable quality that meets the high demands of aerospace strength, weight reduction, and fatigue resistance.
- View the Standard Requirements for Aerospace-Grade 7075 Aluminum
- Learn More About Chalco's Aerospace Aluminum Supply Capabilities
Why 7075 Has Become a Core Material in the Aerospace Industry?
Material selection in aerospace is extremely stringent—aircraft operate under high-speed flight, high-G overload, extreme temperature fluctuations, long-term fatigue stress, and harsh humidity and corrosion environments. These demanding conditions place almost "harsh" requirements on structural materials.
7075 aluminum alloy, with zinc as its primary alloying element and small additions of magnesium and copper, achieves outstanding strength and toughness through precipitation hardening treatments. The following four key properties are why it is so favored in the aerospace industry:
-
Lightweight: Reducing Weight to Improve Range and Fuel Efficiency
Approximately 60% lighter than steel, enabling aircraft weight reduction and significant fuel savings.
Lighter and more cost-effective than titanium alloys, making it a more economical choice for certain structural parts.
For every 1 kg reduction in structural weight, an aircraft can save several hundred liters of fuel annually.
-
Strength and Stiffness: Withstanding High G-Forces, Vibrations, and Flight Loads
In the T6 temper, it offers tensile strength up to 570 MPa and yield strength around 505 MPa, approaching the level of some medium-carbon steels.
Excellent modulus of elasticity and stability allow it to endure sharp maneuvers, vibrations, and impact loads.
Components like wing spars, keels, and landing gear support structures often use 7075-T6, significantly improving stiffness and safety margins.
-
Durability: Fatigue and Corrosion Resistance for Long-Term Reliability
T73 temper uses over-aging treatment to reduce stress corrosion cracking risk, extending component service life.
Can withstand up to 10⁶–10⁷ fatigue cycles (depending on load conditions), minimizing crack initiation under alternating high loads.
Frequently used in critical areas like landing gear structures, fuel lines, and external skin brackets, where both fatigue and corrosion resistance are crucial.
-
Machinability: Meeting Precision Manufacturing Needs While Reducing Costs
Suitable for CNC machining, stamping, extrusion, and riveting, with faster processing speeds and lower tool wear than titanium.
Tolerances can be controlled within ±0.02 mm, offering high dimensional stability for precision components.
Reduces the need for post-machining and finishing, helping aerospace manufacturers shorten production cycles.
Easier to machine than titanium alloys, while maintaining sufficient strength—ideal for engine parts, structural components, and cabin assemblies.
Not All 7075 Aluminum Can Be Used in Aerospace: Industrial-Grade vs. Aerospace-Grade 7075 Aluminum
While 7075 aluminum inherently offers high strength and lightweight characteristics, the key to its suitability for extreme environments lies in the level of melting purity, grain control, and non-destructive testing (NDT). Only those products that meet strict certifications like AMS, MIL, and AS9100, and achieve specific mechanical benchmarks, can truly be classified as aerospace-grade 7075 aluminum.
Industrial-Grade 7075 Aluminum | Aerospace-Grade 7075 Aluminum | |
Standard Certifications | General ASTM, EN standards | AMS, MIL, AS9100 certifications |
Strength Requirements | For general structural parts | Meets specific tensile strength, yield strength, and toughness requirements |
Fatigue Resistance | No mandatory requirement | Passes over 10⁶ fatigue cycles, reducing crack risks |
Corrosion Resistance | No special treatment needed | Clad aluminum or T73 over-aging treatment greatly improves stress corrosion resistance |
Tolerance Control | General precision, ±0.05~0.1 mm | Aerospace-grade precision, within ±0.02 mm |
Impurity Control | No special requirement | Impurities < 0.05%, requires NADCAP-certified NDT |
It is clear that industrial-grade 7075 aluminum only meets the needs of general structural applications, while aerospace-grade 7075 aluminum—used in high-G force aircraft—must meet much stricter standards in material purity, mechanical performance, and testing protocols.
Standards & Certifications Required for Supplying Aerospace-Grade 7075 Aluminum
To meet the high reliability and safety standards of aerospace components, suppliers must pass a series of rigorous quality systems and inspection certifications. Chalco has currently obtained the following:
- ISO 9001 – Certification for Quality Management Systems (QMS)
- ISO 14001 – Certification for Environmental Management Systems
- AS9100 – Certification for Aerospace Quality Management Systems, applicable to the manufacturing of aircraft and spacecraft products
- NADCAP HT – NADCAP accreditation for Heat Treatment, ensuring the consistency and reliability of thermal processes
- NADCAP NDT – NADCAP certification for Non-Destructive Testing (such as ultrasonic and X-ray inspections)
These certifications are not just constraints on Chalco's production process—they also require that critical processes such as internal defect detection, fatigue testing, and corrosion resistance verification be completed before materials leave the factory. This ensures that every batch of aerospace-grade 7075 aluminum can withstand environments with high strength and high fatigue load requirements.
To supply 7075 aluminum alloy products for aerospace use, it is also mandatory to comply with a range of aerospace aluminum standards. Below is a list of 7075 aluminum materials provided by Chalco that meet aviation-grade standards:
Sheet & Plate | Bar | Tube | Extrusions | Forgings |
ASTM B209 AMS-QQ-A-250/12 AMS-QQ-A-250/13 AMS4044 AMS4045 AMS4046 AMS4048 AMS4049 AMS4078 |
ASTM B211 AMS-QQ-A-225/9 AMS4122 AMS4123 AMS4124 AMS4186 AMS4187 |
ASTM B210 ASTM B241 AMS-QQ-A-200/11 AMS-WW-T-700/7 AMS4078 |
ASTM B221 AMS-QQ-A-200/11 AMS-QQ-A-200/15 AMS4154 AMS4166 AMS4167 AMS4168 AMS4169 |
AMS4126 AMS4131 AMS4141 AMS4147 AMS4149 AMS4139 AMS4310 AMS4311 AMS4323 |
In addition, Chalco has successfully passed material audits and certifications from major aerospace companies including Airbus, SAFRAN, Boeing, and Klin Aviation, demonstrating a proven track record of stable and reliable delivery capabilities in real-world projects.
Chalco's Supply Capabilities of Aerospace-Grade 7075 Aluminum
Chalco has accumulated extensive experience in the field of aerospace aluminum materials, with multiple internationally advanced production lines and a rigorous quality control system. Our product portfolio fully covers the following forms and specifications:
Rolled Products
Utilizing high-precision rolling technology, Chalco supplies both bare (Bare) and clad (Alclad) versions to meet the requirements of aircraft skin, fuselage structures, and high-strength components. Various tempers such as T6, T651, and T73 are available to accommodate different strength and corrosion resistance needs. Maximum width reaches 3800 mm, supporting customized production of large-format aerospace materials.
-
7075
Aluminum Sheet
Type: Bare, Alclad
Thickness: 0.3–12 mm
With: ≤2650 mm
Length: ≤10000 mm
-
7075
Aluminum Sheet
Thickness: 12–300 mm
With: ≤3800 mm
Length: ≤20000 mm
Rods and Bars
Produced via extrusion, stretching, or forging, 7075 aluminum bars offer extremely high yield strength and fatigue resistance, making them ideal for wing spars, landing gear support structures, and engine components.
-
7075 aluminum
round bar
Diameter: 5-350mm
Length: ≤6000m
-
7075 aluminum
square bar
Diameter: 5*5-200*200mm
Length: ≤6000m
-
7075 aluminum
hexagon bar
Size: 5-200mm
Length: ≤6000m
Tubes
Chalco offers extruded, cold drawn, and seamless 7075 aluminum tubes in a wide range of dimensions with precision tolerance control up to ±0.02 mm. These are widely used in aerospace hydraulic systems, fuel lines, and high-strength structural supports.
-
7075 extruded
aluminum tube
OD: 5-420mm
WA: 2-50mm
Length: ≤6000m
-
7075 cold drawn
tube
OD: 5-220mm
WA: 0.5-10mm
Length: ≤6000m
-
7075 seamless aluminum
tubee
OD: 10-300mm
WA: 2-20mm
Length: ≤6000m
Extrusions
Chalco supplies T-profiles, angles, U-channels, box profiles, and custom cross-sections. These are used in cockpit rails and aerospace structural frames, supporting complex shapes and tailored extrusion needs.
-
7075 aluminum flat bar
Width: 10-200mm
Height: 2-50
Length: ≤6000m
-
7075 Aluminum box profile
OD: 5*5-200*200mm
WA: 0.5-10mm
Length: ≤6000m
-
7075 Aluminum oval extrusion
Major Axis: 10-250mm
Minor Axis: 5-100mm
WA: 0.3-60mm
Length: ≤6000m
-
7075 Angle Aluminum
Size: 12-200mm
WA: 3-12mm
Length: ≤6000m
-
7075 Aluminum T bar
Width: 20-300mm
Height: 10-100mm
WA: 2-15mm
Length: ≤6000m
-
7075 Aluminum U Channel
Thickness: 1/16", 3/32", 1/8", 3/16", 1/4"
Length: ≤6000m
Forgings
Chalco has advanced forging capabilities to produce 7075 forged bars, tubes, rings, flanges, and blocks for landing gear, turbine supports, and airframe structures, ensuring strength, reliability, and formability.
-
7075 Forged Bar
Diameter 1: ≤800 mm
Length 1: ≤2000 mm
Diameter 2: 800–2000 mm
Length 2: ≤1500 mm
-
7075 Forged Tube
OD: ≤830mm
WA: 90mm
Length: ≤1800m
-
7075 Forged Ring
Quenched OD: ≤2500 mm
Non-quenched OD: ≤4000 mm
Height: 500 mm
Weight: ≤5T
-
7075 Forged Block
Width: ≤2000 mm
Height: ≤500 mm
Length: ≤7000 mm
Weight: ≤9T
-
7075 Forged Disc
Diameter: ≤2500 mm
Thickness: ≤400 mm
Weight: ≤5T
-
7075 Forged Flange
Diameter: ≤1500mm
Thickness: 10mm - 150mm
We offer pre-stretching, solution heat treatment, and aging treatments in various tempers based on customer requirements. Additional post-processing services such as cutting, sampling, and surface treatments are also available.
Want to know about lead times, minimum order quantities, or pricing? Feel free to contact us for a detailed discussion.
Are You Looking for an Aluminum Supplier?
If you need a professional aluminum supplier to provide you with high-quality, cost-effective aluminum, we will be your best choice.
Why Choose Chalco for Aerospace-Grade 7075 Aluminum?
- Full Product Range – From 7075 aluminum sheets, plates, bars, tubes, extrusions, to forgings, Chalco offers a one-stop solution to meet all your aerospace aluminum needs, saving both time and effort.
- Strict Quality Control – Fully AS9100, ISO9001, and NADCAP certified. Each batch undergoes ultrasonic and X-ray non-destructive testing to ensure internal soundness and structural integrity.
- Fast Delivery Capability – Common specifications of sheet, plate, bar, and tube are available in stock. Custom orders can be scheduled for rapid production, with lead times as short as a few weeks.
- Expert Technical Support – We offer guidance on alloy selection, machining optimization, and surface treatment, and assist with sample preparation, fatigue testing, and third-party certification when needed.
- Trusted by Top Aerospace Companies – We have hands-on supply experience with leading clients such as Collins Aerospace, HS Marston Aerospace, Alinabal, Inc., and Batam Aero Technic, delivering proven value in real-world projects.
Backed by years of expertise in aerospace materials, Chalco provides alloy selection and heat treatment advice during the early stages of your project, ensures on-time delivery and quality throughout production, and supports you with validation and maintenance in the later phases. Our end-to-end solution gives you peace of mind from start to finish.
Specific Applications of 7075 Aluminum Alloy in Aerospace
Thanks to its high strength, lightweight nature, and excellent fatigue resistance, 7075 aluminum alloy is widely used in critical structural components of aircraft such as wings, fuselages, landing gear, engines, cabins, and propellers. Each section of an aircraft has different material requirements, making the correct selection of 7075 aluminum forms—such as sheets, bars, tubes, or forgings—crucial.
Wing Structure
The wing is the primary load-bearing structure of an aircraft, subjected to aerodynamic loads, gravity, and lift. 7075 aluminum is a top choice for main wing structures due to its exceptional strength and fatigue resistance.
- Spar – Recommended: 7075-T6/T651 forged or extruded bar with tensile strength up to 570 MPa. Withstands high-frequency vibration and repeated bending, extending service life.
- Skin – Use 7075 Alclad Sheet for superior corrosion resistance in high-altitude, low-temperature, and humid conditions. Common thickness: 0.8–3.0 mm; customizable per aircraft model.
- Ribs – Typically machined from 7075-T651 aluminum plate via CNC. Easy to shape with tight tolerance control (±0.02 mm), maintaining airfoil stability and distributing aerodynamic loads.
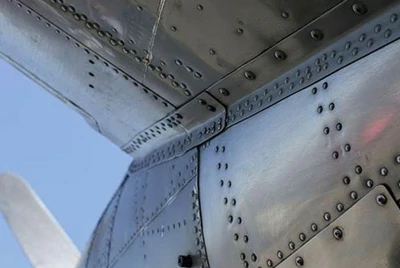
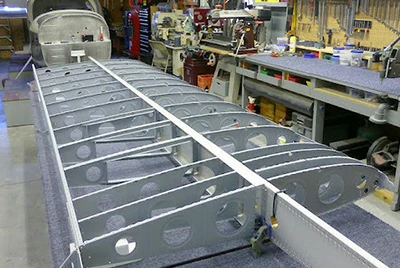
Fuselage
As the central load-bearing structure connecting wings, tail, and landing gear, the fuselage demands high structural strength, impact resistance, and fatigue life. 7075 aluminum is widely used in its framework and skin supports due to its strength-to-weight ratio.
- Keel Beam – Main fuselage load beam. Uses 7075-T6 forgings for superior strength and stiffness.
- Bulkheads & Stringers – Made from 7075 extruded profiles (T6 temper), capable of withstanding hundreds of thousands of load cycles without fatigue cracking. Excellent impact toughness absorbs shocks during flight and landing.
- Skin Supports – Prefer 7075-T7351 aluminum plate to enhance stress corrosion cracking (SCC) resistance. Ideal for skin-contact zones in corrosive environments (e.g., salt spray, humidity).
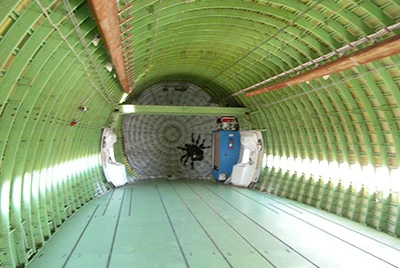
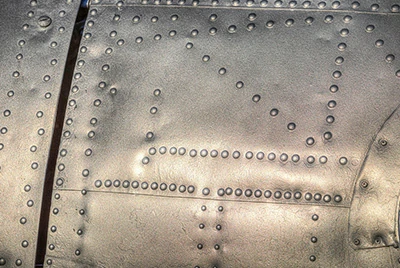
Landing Gear
Landing gear absorbs heavy impact forces during takeoff and landing. It requires ultra-high strength, toughness, and fatigue resistance. 7075 aluminum alloy is a preferred material for supporting and connecting elements.
- Landing Gear Struts – Commonly use 7075-T6511 extruded bars with yield strength over 500 MPa. Excellent shock resistance improves landing gear life cycle.
- Bearing Housings – Made from 7075-T7652 forgings, providing long fatigue life under high stress and vibration. T76 tempers offer a balance of strength and corrosion resistance, reducing maintenance needs.
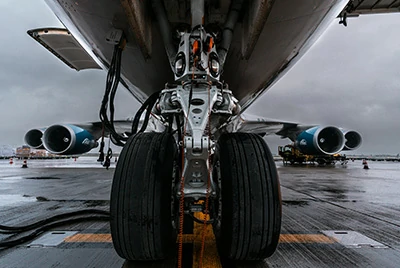

Engine Components
Aircraft engines operate under high temperatures, vibration, and rotational forces. Materials must have excellent strength, fatigue resistance, and thermal stability. 7075 aluminum is commonly used in non-critical engine support parts.
- Engine Mounts – Manufactured from 7075-T6 extruded profiles, strong enough to absorb vibration from fast-spinning engines while reducing overall weight. Easy to CNC-machine into complex shapes.
- Turbine Housing Supports – Recommend 7075-T7351 plates to improve corrosion resistance under stress. Excellent dimensional stability in high-heat environments, suitable for precision engine components.
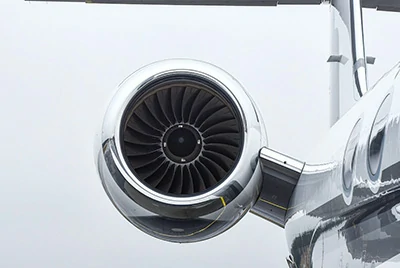
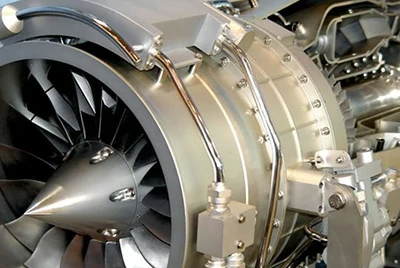
Aircraft Cabin & Interior
Aircraft cabin structures need to be lightweight, durable, and dimensionally stable. 7075 aluminum alloy offers high strength and machinability, making it suitable for interior components.
- Seat Tracks – Made from 7075-T6 extruded profiles to reduce equipment weight while maintaining impact toughness. Meets safety standards and emergency detachment tests.
- Instrument Panel Frame – Uses 7075-T7351 plates, which resist corrosion in humid or fluid-exposed environments. High rigidity keeps instruments stable despite vibration.
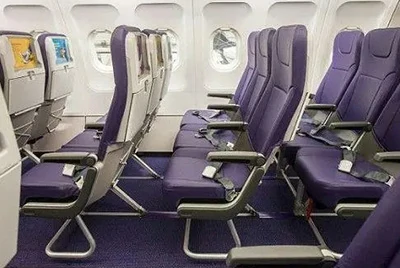
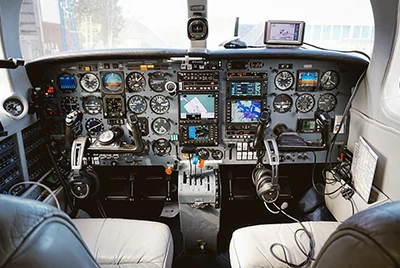
Propeller & Avionics
Propeller hubs and avionics mounts require strength, vibration resistance, and shock durability. The high stiffness and lightweight of 7075 aluminum make it ideal for these applications.
- Propeller Hubs – Commonly use 7075-T6 extruded bars, offering high stiffness and shock resistance. Withstand centrifugal force during high-speed rotation and maintain structure during pitch changes.
- Avionics Mounts – Recommended: 7075-T73 aluminum plate for long-term vibration environments. Resists stress corrosion cracking, balances weight savings with structural reliability, and suits avionics and sensor mounting.
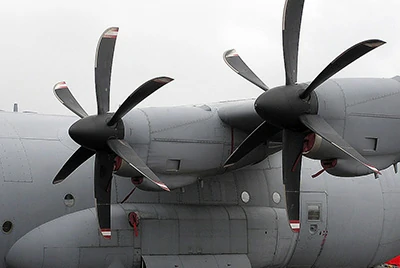
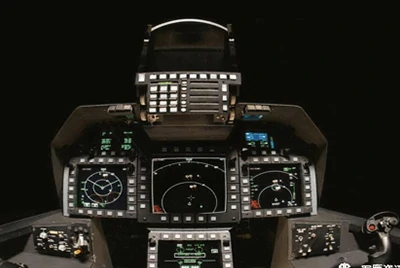
Overview of 7075 Aluminum Applications in Aircraft Systems
Aircraft Section | Application Area | Recommended Temper | Key Advantages |
Wing Structure | Spars, Skins, Ribs | T6 / T651 / T73 | High strength, fatigue resistance, lightweight |
Fuselage Structure | Keel beams, Skin frames, Stringers | T6 / T651 / T7351 | Structural stability, impact resistance, corrosion resistance |
Landing Gear | Struts, Load shafts, Bearing housings | T6511 / T76 | High load capacity, shock resistance, long fatigue life |
Engine Components | Mounts, Turbine housing supports | T6 / T7351 | Heat resistance, vibration tolerance, machinability |
Aircraft Cabin & Interiors | Seat tracks, Dashboards, Cargo supports | T6 / T73 | Lightweight, corrosion resistance, low maintenance |
Propellers & Avionics | Propeller hubs, Electronic mounts, Antennas | T6 / T73 | High rigidity, vibration resistance, dimensional stability |
By utilizing 7075 aluminum alloy in targeted applications across various aircraft components, manufacturers can achieve a better balance between weight reduction, durability, and safety. Depending on specific load conditions and service environments, choosing the right product form (sheet, bar, tube, extrusion, or forging) and the appropriate temper (T6, T651, T73, T76, etc.) can help aircraft attain:
- Higher fuel efficiency
- Longer service life
- More reliable and safer flight performance
Now that we've outlined the performance requirements for 7075 aluminum in different aircraft sections, how does this alloy perform in real-world top-tier aerospace engineering projects? The following case studies provide the answer.
Real-World Applications of Aerospace-Grade 7075 Aluminum in Leading Aviation Projects
F-22 Raptor Stealth Fighter
The aircraft’s primary load-bearing fuselage frame utilizes 7075-T651 aluminum, certified to MIL-DTL-32262A. With a tensile strength ≥ 570 MPa, it achieves 15% weight reduction compared to titanium alternatives. A hard anodized surface treatment enhances stealth performance by reducing radar signature.
SpaceX Falcon 9 Rocket – LOX Tank Support Truss
The liquid oxygen tank’s structural trusses are made from 7075-T7351, offering 450 MPa yield strength at -183°C. This configuration passed NASA SPC-100 pressure cycling tests and reduced weight by 20% compared to 6061 aluminum.
NASA Space Shuttle Orbiter – Cargo Bay Hinges
Constructed with 7075-T73, these hinges withstood 5, 000-hour salt spray testing without corrosion. Though 10% lower in strength than T6, the material significantly improved stress corrosion resistance, extending the shuttle’s orbital service life.
Boeing 787 Wing Leading Edge – Bird Strike Reinforcement
Reinforcement ribs made from 7075-T76 passed FAA regulation §25.571: survived 1.8 kg bird impact at 900 km/h with <3 mm deformation (at specific angles). The ribs also assist in lightning strike protection for composite structures.
Mitsubishi A6M "Zero" Fighter
The world’s first mass-produced aircraft to use 7075 aluminum (then called "Extra Super Duralumin") extensively. Its fuselage skin was only 0.8 mm thick, contributing to a takeoff weight of just 1.68 tons. However, the lack of corrosion protection led to high failure rates under tropical combat conditions.
These cases clearly demonstrate that 7075 aluminum alloy has been thoroughly validated in top-tier aerospace programs such as the F-22, Falcon 9, NASA space shuttle, and Boeing 787, proving its value in delivering high strength, lightweight performance, and durability under extreme conditions.


Chalco is more than just a supplier—we offer aerospace-grade 7075 aluminum that complies with AMS, ASTM, and MIL standards, backed by AS9100, ISO9001, and NADCAP certifications. We maintain long-term partnerships with world-renowned aerospace companies, delivering reliable, high-quality, and customized aluminum solutions to global manufacturers.
Contact Us for a Custom 7075 Aluminum Solution
Chalco not only delivers top-quality aerospace aluminum, but also provides tailored solutions including material selection, heat treatment, and component processing. We assist you through all phases—from R&D to certification compliance. Have questions or a project in mind? Get in touch today.
Chalco can provide you the most comprehensive inventory of aluminum products and can also supply you customized products. Precise quotation will be provided within 24 hours.
Get a quote