We offer corrugated aluminum metal panels for roofing, flooring, and siding. Aluminum corrugated metal sheet is a tough material that is lightweight, weather-resistant, and suitable for many different uses.
As the industry leader in providing the best aluminum corrugated metal sheets, we are able to ensure customer satisfaction by producing metal sheets in almost any material and specification size. We offer a variety of different finishes that are sure to suit your preferences.
Why choose Chalco
Chalco is strictly controlled, with good weldability, strong corrosion resistance, bending resistance and compression resistance. The surface is smooth and clean when cut, and the surface treatment can present a rich choice of colors and textures.
Chalco is the source manufacturer of aluminum corrugated sheets with complete equipment and various specifications. Can be measured according to the required standard, customized cutting.We can fabricate, bend, shape, cut, shear, tear materials into any shape, size.Quick Quote
Chalco has a complete management system, accurate dimensions, and production standards comply with GB/T 3880-2005, B209-2020, JC/T 1074-2012, ASTM A1196-2020, ISO 9001, CE, SGS.
Popular aluminum corrugated panels
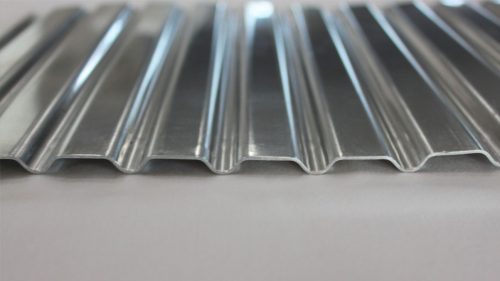
metal surface
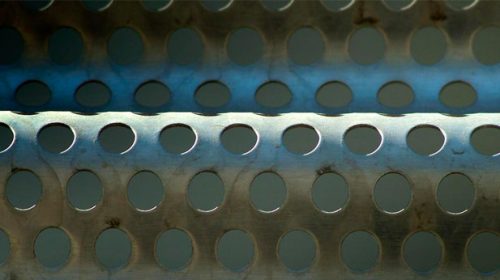
PERFORATED METAL
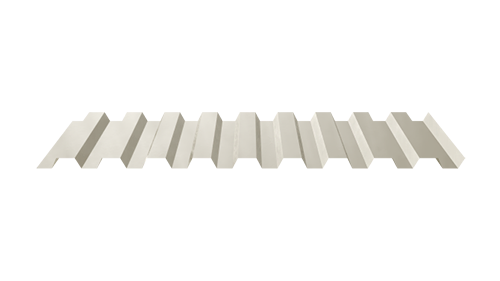
4″ BOX RIB
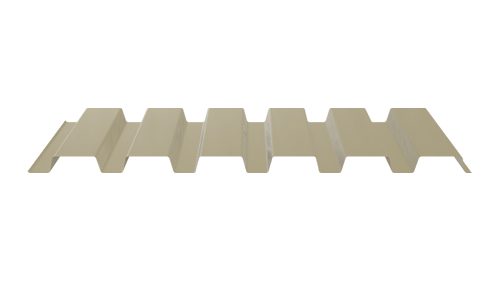
6″ BOX RIB
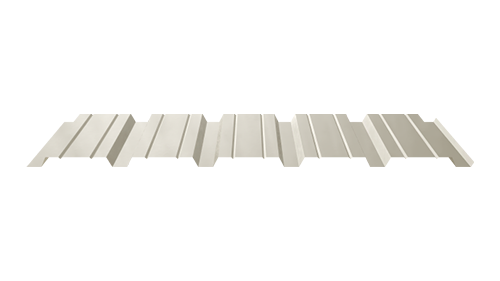
8″ BOX RIB
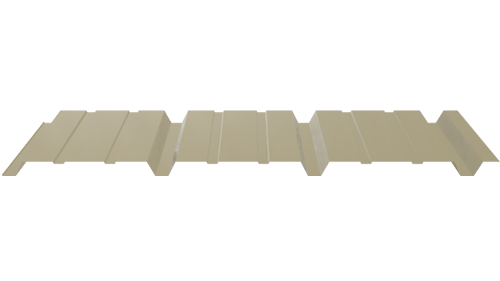
R-PANEL
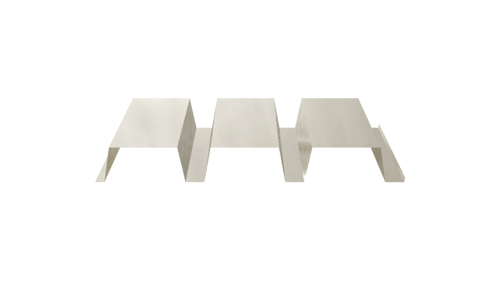
HARVEST PANEL
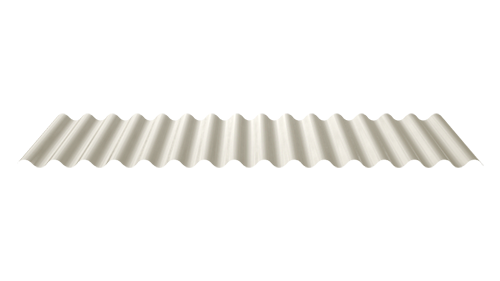
2.67″ X 3/4″
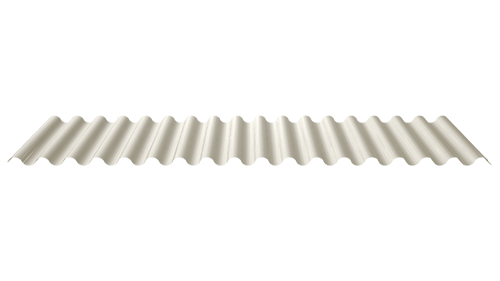
2.67″ X 7/8″
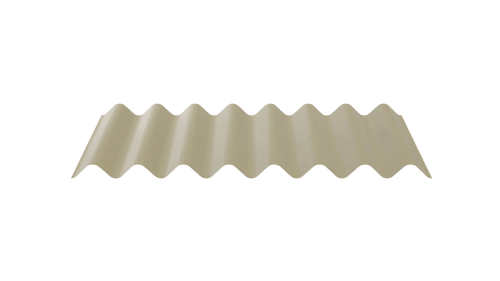
3″ X 1″
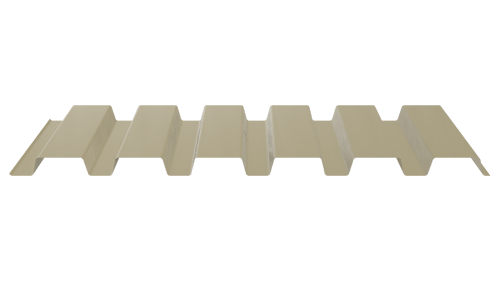
B-DECK
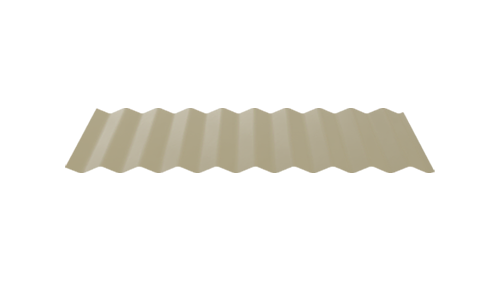
2.67″ X 1/2″
Roof Aluminum Corrugated Metal colors are available in two color charts
Standard Colors: These colors are in stock and available for quick delivery. There is no minimum order quantity.
Special order colors: Please allow 3-4 weeks for delivery.Quick Quote
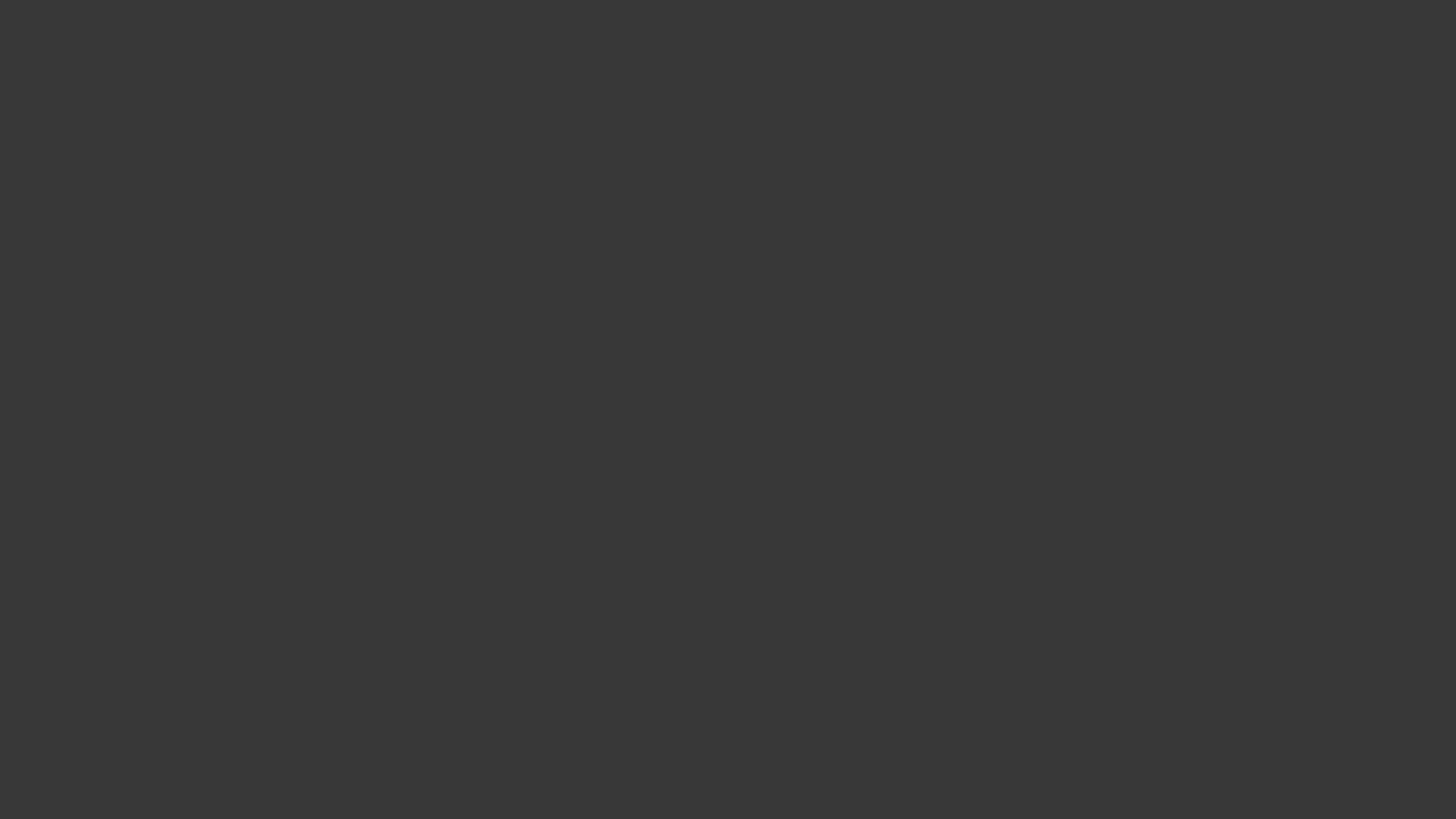
Charcoal Gray
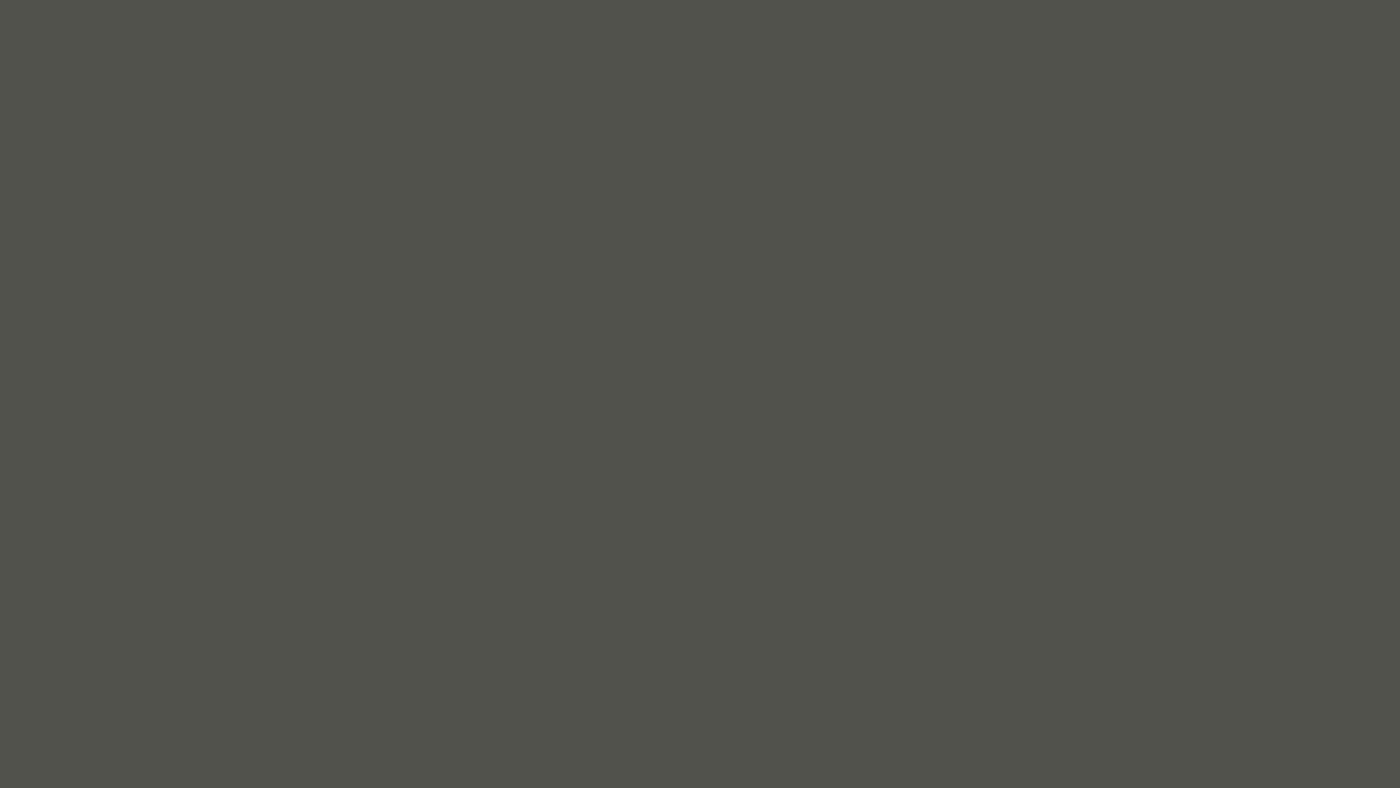
Dark Bronze
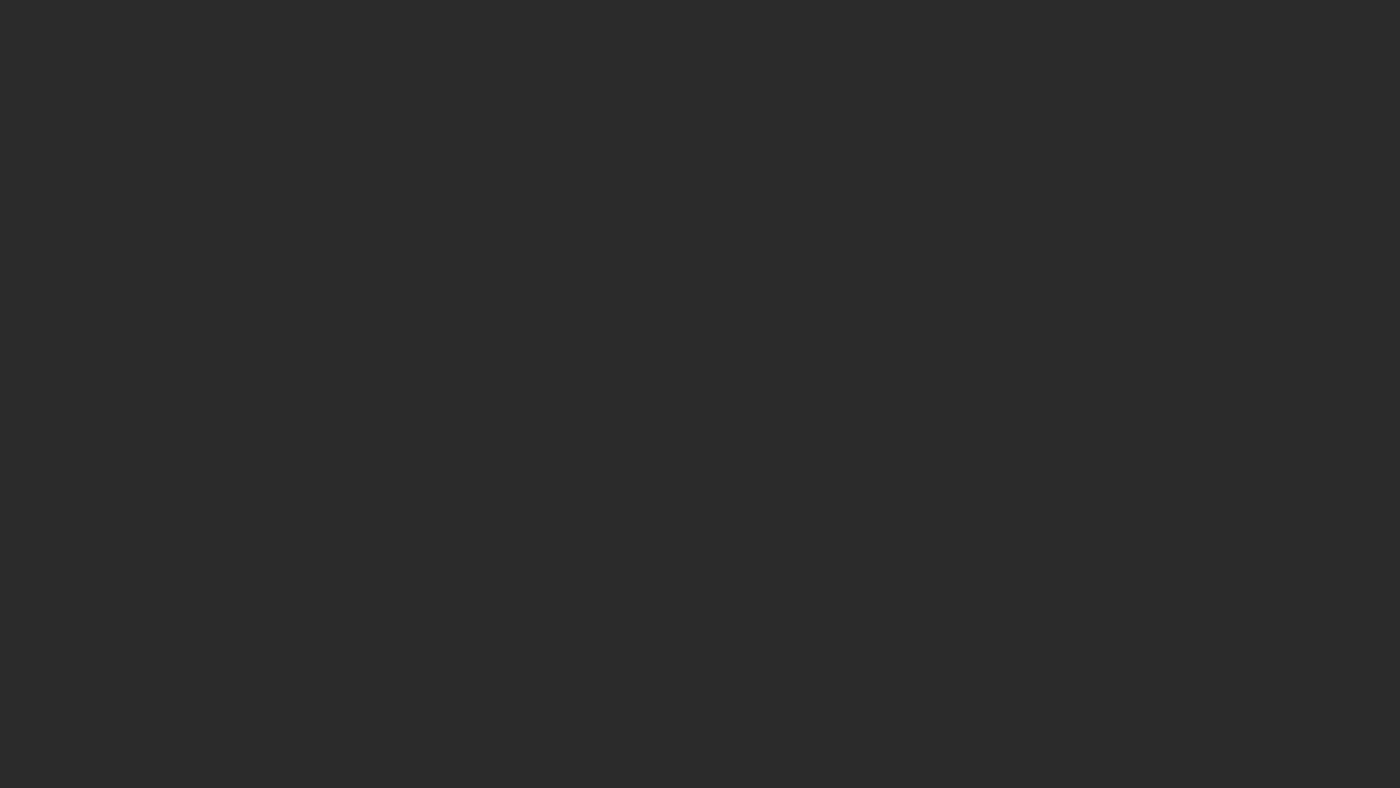
Matte Black
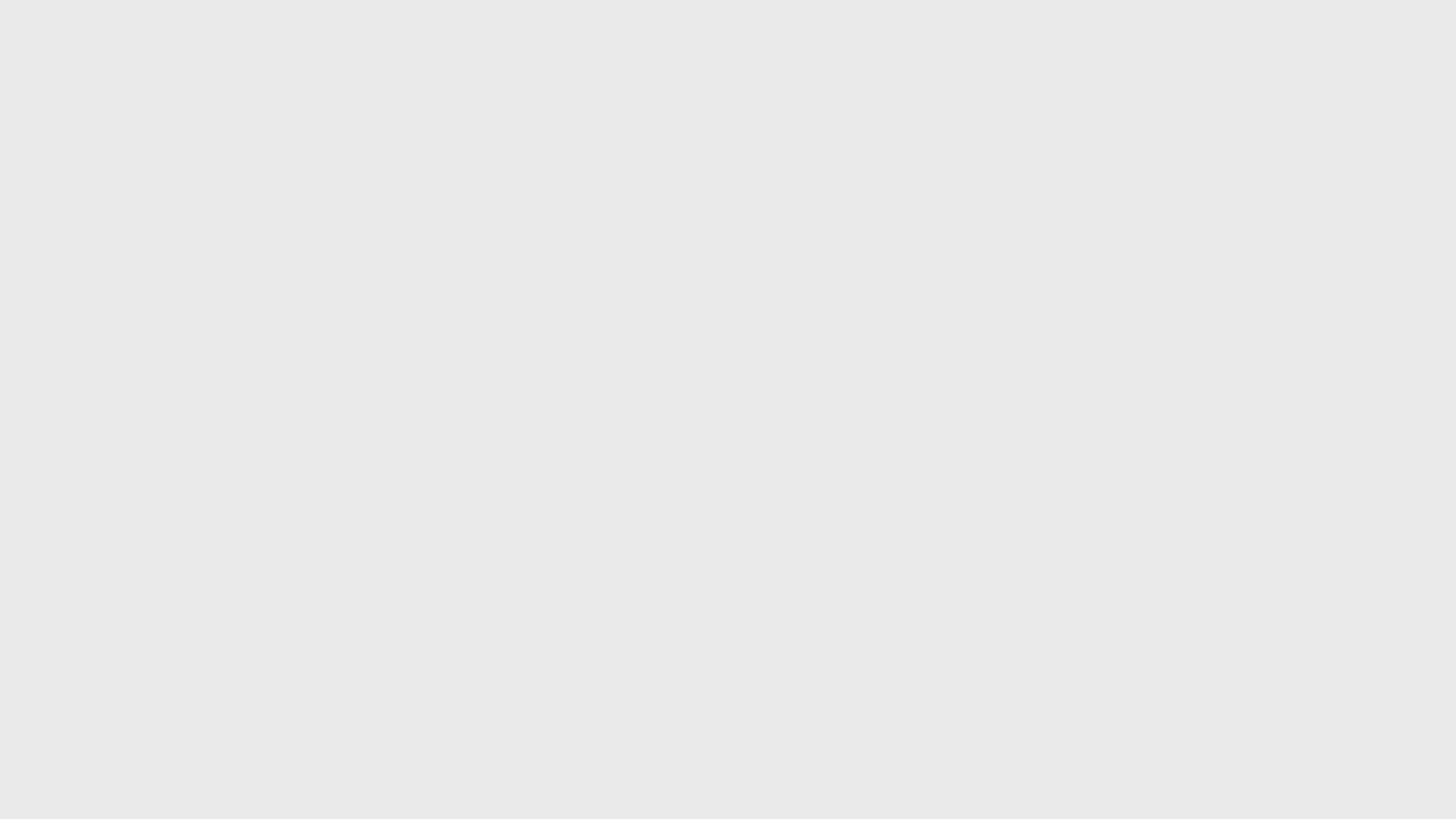
Regal White
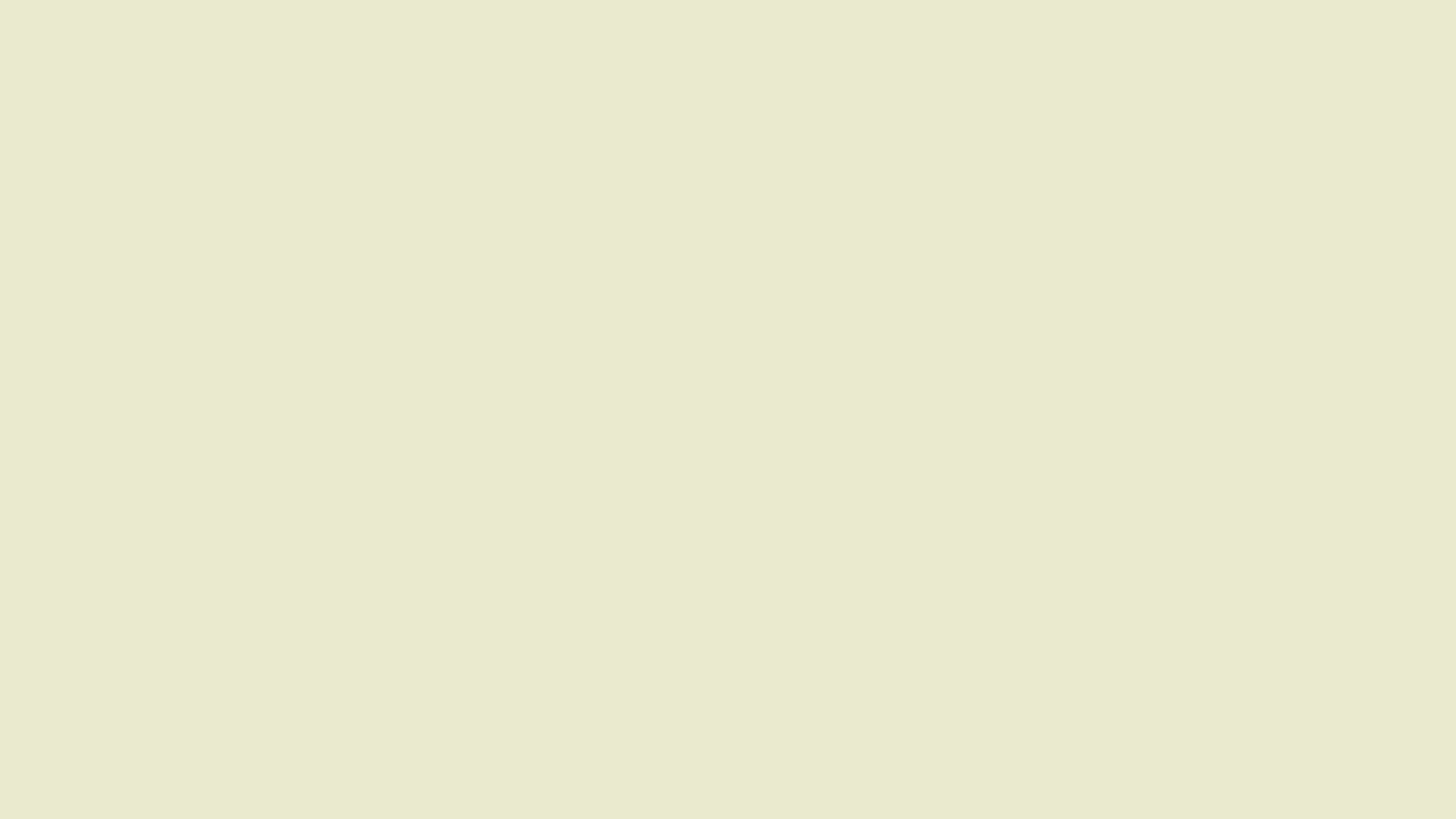
Almond
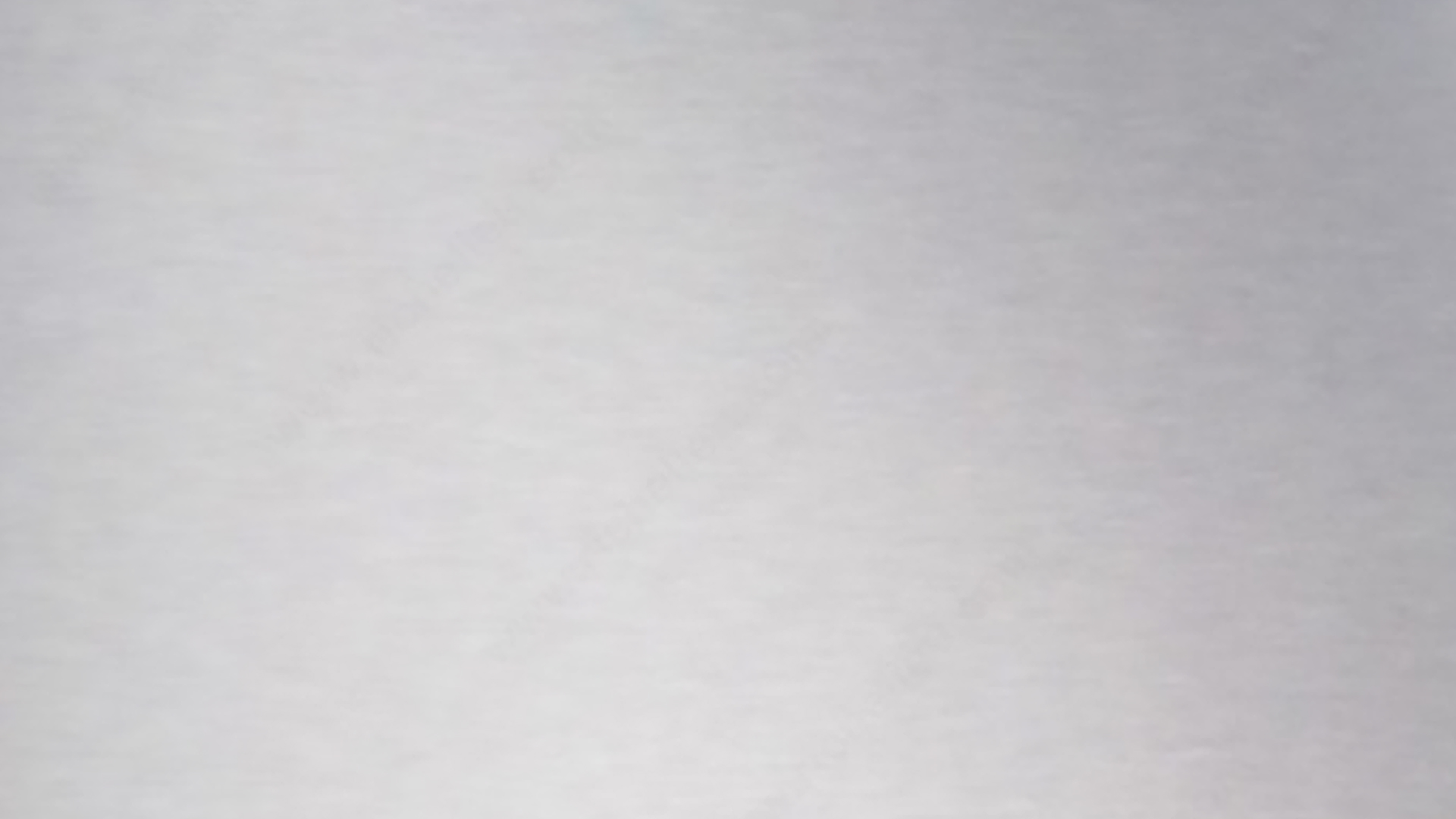
Aluminum – Mill Finish
Chemical composition of 1050 1060 1100 aluminum corrugated sheets
Alloy | 1050 | 1060 | 1100 |
Al | 99.5% | 99.6% | 90.00% |
Si | ≤0.25% | ≤0.25% | - |
Fe | ≤0.40% | ≤0.35% | - |
Cu | ≤0.06% | ≤0.06% | ≤0.20% |
Mn | ≤0.05% | ≤0.03% | ≤0.05% |
Ti | ≤0.03% | ≤0.03% | - |
V | ≤0.06% | ≤0.06% | - |
Si+Fe | - | - | ≤0.95% |
Surface treatment of 1050 1060 1100 aluminum corrugated sheets
Anti-corrosion coating
Can be applied on the surface of 1050, 1060, 1100 aluminum corrugated sheet, which can be painted, sprayed or sprayed with fluorocarbon, etc.
Electrophoretic coating
A uniform and durable coating is formed by attaching electrically charged paint particles to an aluminum sheet and curing them. This treatment can provide rich color options and high weather resistance.
Sand treatment
A rough surface texture can be created by sandblasting or mechanical grinding on the surface of 1050, 1060, 1100 aluminum sheet. This treatment is often used in interior decoration and design.
Anodization
1050, 1060, 1100 aluminum alloys can be oxidized to form an oxide film to increase the corrosion resistance and oxidation resistance of the surface.
Packaging, transportation and storage of 1050 1060 1100 aluminum corrugated sheets produced by Chalco
1050, 1060, 1100 Aluminum corrugated boards are packaged without oil or paper, and are simply packed in stacks.
The board stack should be wrapped with kraft paper, and tied tightly with nylon braid, and then tightly wrapped with asphalt paper, and then a layer of plastic film should be covered on the board stack, and the upper and lower ends of the board stack should be tightly nailed with box covers.Quick Quote
The height of each stack of corrugated boards should not exceed 500mm, and the gross weight of each stack should not exceed 2000kg.
Applications of 1050 1060 1100 aluminum corrugated sheets
Building decoration
1050, 1060, 1100 aluminum corrugated sheets can be used for building exterior walls, roofs, ceilings, facade decoration, etc. Its corrugated design increases the strength and rigidity of the surface while giving the building a unique appearance.
Home decoration
1050, 1060, 1100 aluminum corrugated sheets can be used for interior decoration, such as walls, ceilings, furniture, etc. Its gloss and finish provide visual aesthetics combined with ease of cleaning and durability.
Ship building
1050, 1060, 1100 aluminum corrugated plates are suitable for decks, hatch covers, hull decorations and other parts of ships. Its corrosion resistance and oxidation resistance can meet the challenges of marine environment.Quick Quote
Vehicle construction
In vehicle manufacturing, it can be used in body panels, interior trim panels, cargo box floors, and vehicle pedals.
Its light weight, corrosion resistance and strength make it one of the important materials in automobile manufacturing.
Advantages of 1050 1060, 1100 aluminum corrugated sheet produced by Chalco
Good processability
1050, 1060, and 1100 aluminum alloys have good machinability, are easy to bend, form and cut, and can meet the needs of different shapes and sizes.
Decorative
1050, 1060, and 1100 aluminum corrugated panels can be surface treated and painted to achieve rich color and texture options, making them more beautiful and diverse in appearance.
This makes it have certain decorative properties in architectural decoration and interior design.
Lightweight
1050, 1060, 1100 aluminum corrugated sheet has a lower density than other materials, such as steel, so it is very light.
Corrosion resistance
Aluminum has good corrosion resistance, so 1050, 1060, 1100 aluminum corrugated sheets have excellent corrosion resistance in wet, acidic or alkaline environments.
Environmental protection
Aluminum is a recyclable and reusable material, so 3003 aluminum corrugated panels have good environmental protection. It can reduce the consumption of natural resources and reduce environmental pollution.
The difference between the 1060 aluminum corrugated sheet produced by Chalco and the 3003 aluminum corrugated sheet
Surface color
Since 3003 aluminum contains about 1.0-1.8% manganese, the surface of untreated 3003 aluminum corrugated sheet will be gray. The 1060 aluminum is pure aluminum with bright color.Quick Quote
Hardness
The hardness of 3003 aluminum plate is generally between 30-35. Because the aluminum content of 1060 aluminum plate is as high as 99.60%, 1060 aluminum is about 10% softer than 3003 aluminum.