Welding, brazing, and soldering are all metal joining processes that use heat. But each method is different in how it works and where it's used.
Welding melts the base materials using high heat and often pressure. It's commonly used with metals and thermoplastics to form a strong, seamless bond.
Brazing melts only the filler metal—not the base materials. It's ideal for joining different types of metals without damaging the workpieces.
Soldering is similar to brazing but requires lower temperatures. It's mostly used in electronics, where precise, low-heat bonding is essential.
What is welding?
Welding is a manufacturing process that joins two or more parts together using high heat, high pressure, or both. The goal of welding is to create a strong bond between two metal pieces, enabling them to withstand various stresses and strains, such as in car bodies or airplane fuselages.
For welding to work, the two metals being joined must be similar in composition. For example, copper cannot be welded directly to steel.
The process requires extremely high temperatures to melt the metal and bond the parts together. Filler material is often used to fill gaps and ensure a complete connection.
When performed correctly, the strength of the weld should match that of the surrounding base material. However, excessive heat can alter the metal's properties, weakening the weld.
Instant QuoteThe four most common welding methods
- GMAW (MIG welding): Uses an arc between a metal filler electrode and the workpiece to melt the material, enabling fast and efficient automated welding, ideal for mass production.
- SMAW (Stick welding): Uses a coated electrode to create an arc that heats the metal, with the coating generating protective gas. Commonly used for structural welding and fieldwork.
- FCAW (Flux-cored arc welding): Continuously feeds filler wire with internal flux for protection, suitable for thick materials and high deposition welding, often used in heavy industries.
- GTAW (TIG welding): Uses a tungsten electrode and inert gas for protection, creating fine, clean welds. Ideal for thin materials and high-precision welding, such as stainless steel and aluminum.
Advantages of welding
- Creates stronger joints than brazing or soldering.
- Produces joints suitable for high-temperature applications.
- Capable of joining both thin and thick metal sheets (depending on the process type).
Disadvantages of welding
- Results in greater heat distortion and residual stress at the joint compared to brazing.
- Requires post-weld heat treatment to relieve residual stress (depending on application and process).
- Can only join similar base materials (applicable to most processes, but not all).
Chalco is a professional one-stop supplier of aluminum products and deep processing services, fully meeting customers' welding application needs.
If you have any questions about aluminum welding materials, processing techniques, or application solutions, feel free to contact us. Our team will provide you with professional answers and technical support.
Instant QuoteWhat is brazing
Brazing is a process that uses heat to melt a filler metal (brazing alloy) and, through capillary action, draws it into the joint gap, creating a permanent bond between the metal pieces.
The brazing temperature is above 450°C (840°F) but below the melting point of the base materials, so it does not melt the materials being joined.
The filler metal (brazing alloy) is a key material used in brazing to connect the metal parts, and its melting point must be lower than the base metal being joined.
Common brazing alloys include copper, silver, nickel, gold, aluminum, and cobalt, and they are typically supplied in the form of rods, sheets, rings, or paste.
According to the American Welding Society (AWS) classification, brazing alloys are identified by the letter "B", such as BCuZn for copper-zinc alloys. If the alloy is in rod form, it will have an "R" after the designation.
Flux in brazing plays a crucial role in the process. Its main functions include removing metal oxides formed during heating, improving wettability (helping the molten brazing material spread on the base material surface), and promoting capillary action to allow the filler metal to flow smoothly into the joint.
Flux is commonly available in various forms, including liquid, powder, paste, and sheet. It is important to note that excessive use of flux may lead to residue remaining in the joint, which can affect the bond strength and potentially cause leaks or failure.
We also offer a variety of flux products for our customers. Feel free to contact us for consultation and purchase.
Instant QuoteAdvantages of brazing
- Avoids melting the base material.
- Clean and tidy joints, no need for cleaning.
- Can join dissimilar metals and even non-metals.
- An economical method for combining materials with multiple components.
- Simple and easy to perform.
Application advantages of brazing
- High flexibility: Suitable for complex structures and precision components.
- Smooth surfaces: No need for secondary processing, ideal for products with high aesthetic requirements.
- Widely used in industry: Commonly used in HVAC, automotive, electronics, aerospace, jewelry, and hardware industries.
Popular brazing products
Chalco offers brazing wire, brazing rods, brazing sheets, brazing rings, composite brazing plates, and specialized fluxes, with support for custom sizes and alloy compositions.
Instant Quote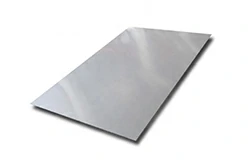
AL 4045 brazing plate/strip
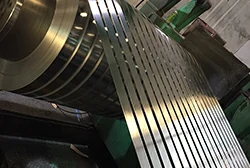
AL 4343 brazing alloy
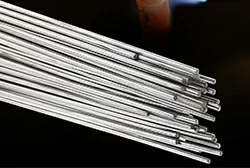
AL 4047 welding wire/brazing rod
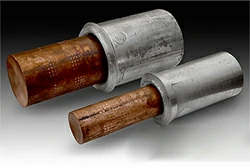
AL 718 aluminum-copper brazing rod
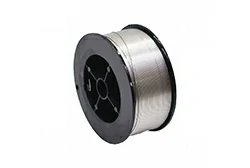
AL 822 brazing wire

Brazing ring
Brazing technology and equipment
Common brazing methods include:
- Flame brazing: Uses oxy-fuel gases like acetylene or propane for heating, ideal for on-site operations.
- Furnace brazing: Parts are heated in a brazing furnace, suitable for automated mass production.
- Induction brazing: Uses induction coils for precise, localized heating, offering high efficiency.
- Dip brazing: Components are immersed in a heated bath of flux and brazing material, ideal for mass brazing of aluminum parts.
Common equipment includes torches, brazing furnaces, induction heating systems, and chemical bath systems.
What is soldering?
Soldering is a low-temperature process that joins metal components by heating and melting a filler metal (solder) and introducing it into the joint to create a permanent bond.
The soldering temperature is below 840°F (approximately 450°C), much lower than welding and brazing, making it suitable for connecting heat-sensitive components. Once melted, the solder solidifies in the joint, forming the connection, which may or may not rely on capillary action.
Soldering can join a variety of metals, such as copper, brass, gold, silver, and iron, and is widely used in electronics, electrical, plumbing, and jewelry industries.
Compared to welding and brazing, the strength of a soldered joint is lower, but it offers good electrical conductivity, making it particularly common in printed circuit board (PCB) soldering.
Advantages of soldering
- Lower input power and processing temperature compared to welding and brazing.
- Capable of joining different base materials.
- Suitable for connecting thin-walled components.
- Minimal heat distortion and residual stress at the joint.
- No need for post-processing heat treatment.
Disadvantages of soldering
- Lower joint strength compared to welding and brazing, not suitable for load-bearing applications.
- Cannot be used for large parts.
- Not suitable for high-temperature applications.
- Flux may contain toxic components.
Soldering tools
- Soldering iron
- Solder and flux
- Wire cutters
- Desoldering pump
- Damp sponge
- Soldering station
- Safety glasses
Soldering vs. Welding
Soldering is classified by the American Welding Society (AWS) as a liquid-solid phase bonding process. The liquid phase refers to the melting of the filler metal, while the solid phase means that the base materials are not melted.
Unlike welding, soldering does not involve melting the workpieces. The key difference between soldering and welding is the heat source.
Soldering uses heat sources like torches, furnaces, induction heating, dip soldering, or resistance heating, with operating temperatures below 840°F (450°C). In contrast, arc welding uses electricity as the heat source, with temperatures reaching around 10,000°F (5,500°C).
Brazing vs. Welding
The American Welding Society (AWS) also classifies brazing as a liquid-solid phase bonding process. The liquid phase refers to the melting of the filler metal, while the solid phase means the base materials remain unmelted.
Unlike welding, brazing does not involve melting the workpieces. The main difference between brazing and arc welding is the heat source.
Brazing uses heat sources like torches, furnaces, induction, dip soldering, or resistance heating, with temperatures above 840°F (450°C).
Arc welding, however, uses electricity as the heat source, reaching temperatures of approximately 10,000°F (5,500°C).
Brazing vs. Soldering
The only difference between brazing and soldering lies in the temperature at which each process occurs.
Soldering is performed at temperatures below 840°F (450°C), while brazing takes place at temperatures above 840°F (450°C).
What do brazing, soldering, and welding have in common?
Cleaning metal parts: No matter which process you choose, success depends on starting with clean materials.
Heating the materials: All three methods require sufficient heat to form a strong bond between the parts.
Proper safety equipment: Protective eyewear, gloves, clothing, and helmets are essential for each process to ensure safety during operation.
Summary of differences between welding, brazing, and soldering
Strength
Welding: The joint is the strongest, typically stronger than the base material.
Brazing: The joint strength is weaker than welding but stronger than soldering, capable of withstanding some load.
Soldering: The weakest joint, typically used for electrical contacts, not suitable for load-bearing applications.
Temperature
Welding: Welding requires a temperature as high as 3800°C.
Brazing: Brazing requires a temperature between 450°C - 600°C.
Soldering: Soldering typically occurs at temperatures below 450°C.
Workpiece heating
Welding: Requires heating the workpiece to its melting point.
Brazing: The workpiece is heated but not beyond its melting point.
Soldering: Only the filler metal is heated, not the workpiece itself.
Mechanical property changes
Welding: Heating and cooling may change the mechanical properties of the base material.
Brazing: Has almost no effect on the mechanical properties of the base material.
Soldering: Does not change the mechanical properties of the base material.
Heat treatment
Welding: Usually requires heat treatment to eliminate any negative effects from the welding process.
Brazing: Does not require heat treatment.
Soldering: Does not require heat treatment.
Filler metals
Welding: Typically uses filler metals like steel, aluminum, and other materials.
Brazing: Uses low-melting-point filler metals such as silver, copper, or nickel alloys.
Soldering: Commonly uses lead-based or lead-free solder as filler material.
Primary applications
Welding: Widely used in structural and industrial applications, such as construction and automotive manufacturing.
Brazing: Suitable for HVAC, piping, automotive, jewelry, and particularly dissimilar metal connections.
Soldering: Commonly used in electronics, jewelry, and small piping connections.
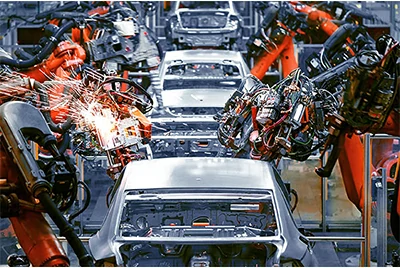
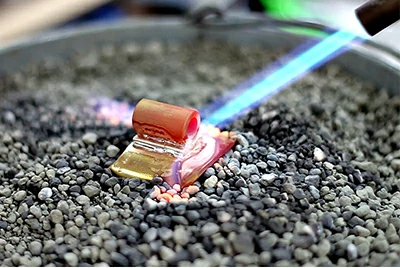
How to choose between brazing, welding, and soldering
Choosing the right joining process requires considering several factors, such as material type, joint strength requirements, process temperature, and application scenarios. Below are the characteristics and common uses of each process to help you make the best choice.
Material | Ideal Process | Why |
Steel | Welding or Brazing | Steel has high load-bearing strength, making it suitable for welding or brazing. |
Stainless Steel | Brazing or TIG Welding | Strong corrosion resistance and clean joints, ideal for brazing or TIG welding. |
Copper | Brazing or Soldering | Suitable for piping applications, without melting the base material, brazing or soldering is preferred. |
Aluminum | TIG Welding | Ideal for aluminum materials, providing clean joints and precise weld control. |
Electronics | Soldering | Low-temperature process that prevents component damage, ideal for electronic components. |
Chalco can provide you the most comprehensive inventory of aluminum products and can also supply you customized products. Precise quotation will be provided within 24 hours.
Get a quoteTechnical answers
Why choose brazing over welding?
Brazing offers more precise control, with cleaner joints compared to welding. It doesn't require secondary finishing, and the thermal distortion is also smaller.
Brazing forms a bond between metal pieces, whereas welding actually fuses the metals together.
What are the advantages of brazing over welding?
Compared to welding, brazing causes minimal thermal distortion and residual stress. It also doesn't require post-processing and can join different base materials.
Is welding hotter than brazing?
Brazing uses a torch, furnace, dip brazing, or resistance heating, with temperatures up to 450°C. Welding, on the other hand, uses electricity as a heat source, reaching temperatures above 5,500°C.
Can brazing be done without flux?
All brazing and welding applications require flux (or a controlled atmosphere in furnace brazing).
Which has the highest joint strength: brazing or soldering?
When a permanent connection needs to withstand high stress and temperature, welding should be chosen over brazing or soldering.
Welding fuses the base material, creating stronger joints compared to the surface-only bond formed by brazing or soldering.
Why is brazing used for bicycle frames instead of welding?
Unlike welding, brazing does not melt the components. This results in less heat applied to the frame parts, reducing distortion, stress, and changes to the material's physical properties.
Brazing requires less heat than welding, making it more energy-efficient.
Why is welding better than riveting?
Strength: Welded joints typically have strength equal to or greater than the base material itself. This is because welding fuses the materials together, forming a bond stronger than rivets.
If you encounter any product selection, processing challenges, or welding technical issues in your projects, feel free to leave a message or contact us below.
We are happy to engage in technical discussions, assist in solving practical problems, and provide efficient, feasible aluminum solutions.