In aluminum alloy welding applications, TIG filler rods (Tungsten Inert Gas welding filler rods) are essential materials for achieving high-quality welds. Chalco specializes in the development and production of aluminum and aluminum alloy welding consumables, offering a stable supply of TIG-grade solid rods in various alloy grades, diameters, and customized packaging. Our products are widely used in high-precision welding scenarios across the aerospace, automotive, and industrial structural sectors.
What we offer is commonly referred to in the industry as aluminum filler rods or TIG rods, specifically designed for manual TIG (GTAW) welding processes. These rods provide excellent weldability, crack resistance, and corrosion resistance, and are especially compatible with 1xxx, 4xxx, 5xxx, and 6xxx series aluminum base materials.
Chalco aluminum filler rod product introduction
Product categories: Aluminum TIG Filler Rods; Meets AWS A5.10 / ISO 18273 and other international standards.
Suitable welding positions: Flat, Horizontal, Overhead, Vertical-Down, Vertical-Up (Filler rods can be used in all-position TIG welding with appropriate technique and joint preparation.)
Surface Finish: Bright, Cleaned, or Lightly Oxidized (Grey/Silver/White); Available in standard mill finish or brushed finish depending on alloy and storage condition
Common TIG filler rod alloys: Click to view [Alloy Details]
- 4043 / 4943 – For 6xxx series (e.g. 6061), excellent flow & crack resistance
- 5356 / 5556 – For 5xxx series (e.g. 5083), higher strength and corrosion resistance
- 4047 / 4643 – High silicon, for cast aluminum & shrinkage crack control
- 1050 / 1100 / 1070 – Pure aluminum, ideal for low-strength & corrosion-resistant joints
Popular diameters: Click to view [Product size and performance reference table]
0.9 / 1.1 / 1.2 / 1.6 / 2.4 / 3.2 / 4.0 / 4.8 mm (Custom sizes on request)
Packaging specifications:
- TIG cut lengths: 10 pcs/bundle, 1 lb / 5 lb / 10 lb per tube
- Industrial box: 2.5 kg, 5 kg, or custom weight per carton
- Moisture-proof and export packaging available upon request
Hot-selling aluminum filler rods for TIG welding—— most popular alloy grades
Chalco offers a full range of TIG filler rods designed for optimal performance across a variety of aluminum welding applications. Below are our most in-demand alloy grades, each carefully selected to meet the strength, fluidity, crack resistance, or anodizing compatibility required in your projects.
Whether you're working with structural 6xxx aluminum, marine-grade 5xxx alloys, or pure aluminum for corrosion-resistant components, our hot-selling TIG rods cover the key welding needs of industries worldwide. Choose the right alloy based on your material, application scenario, or post-weld treatment requirements:
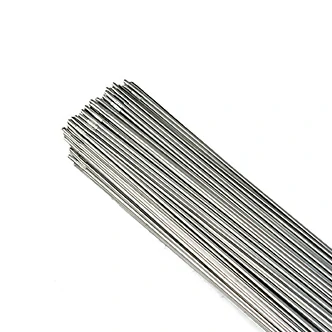
ER4043/ R4043 aluminum filler rod
ER4043 is a general-purpose aluminum TIG wire with silicon additives, offering good fluidity, crack resistance, and bright welds. It suits 6000 series alloys, supports heat treatment, and has higher tensile strength than ER5356.
Applicable welding positions: flat welding; horizontal welding; overhead welding; vertical welding downward; vertical welding upward
Tensile Strength (minimum requirement): 29 ksi
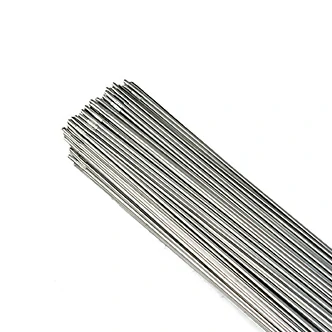
ER 5356 aluminum filler rod
ER5356 electrodes are popular aluminum TIG electrodes for general welding, ideal for 5000 series alloys and not heat treatable.
Applicable welding positions: flat welding; horizontal welding; overhead welding; vertical welding downward; vertical welding upward
Tensile Strength (minimum requirement): 38 ksi
-
4047 aluminum filler rod
High silicon content, good fluidity, suitable for reducing thermal cracking.
-
4943 aluminum filler rod
High strength and good toughness, suitable for structural welding.
-
4643 aluminum filler rod
High toughness and crack resistance, suitable for welding requiring high reliability.
-
4145 aluminum filler rod
High strength and corrosion resistance, suitable for aviation and automotive industries.
-
5556 aluminum filler rod
High strength and wear resistance, suitable for highly loaded structures.
-
5183 aluminum filler rod
Excellent corrosion resistance for marine and tank applications.
-
5554 aluminum filler rod
It has strong crack resistance and is specially used for welding chemical storage tanks and pipelines.
-
6061 aluminum filler rod
Easy to weld, widely used in general engineering fields.
-
6063 aluminum filler rod
It has excellent processing properties and is suitable for decorative and structural purposes.
-
1100 aluminum filler rod
Pure aluminum, soft and corrosion-resistant, suitable for low-strength welding.
-
1050 aluminum filler rod
High purity, good conductivity and corrosion resistance, suitable for welding with low strength requirements.
-
4009 aluminum filler rod
Suitable for special welding needs in high temperature environments.
-
4008 aluminum filler rod
High strength, corrosion resistance, for special applications.
-
5654 aluminum filler rod
Specially designed for hydrogen storage tanks, with excellent corrosion resistance.
-
2319 aluminum filler rod
High-strength alloy specially used in aerospace and military fields.
Not sure which filler rod suits your welding task? Chalco's technical team is ready to help you match the right alloy to your base material, welding position, and post-treatment process. Whether you need a standard ER4043 for 6061 structures or a high-performance rod like 4943 or 2319 for critical applications, we offer expert advice, sample support, and fast delivery. Contact us today to request data sheets, get a custom quote, or ask about our packaging and certification options.Quick Quote
Reference table: sizes and properties of Chalco aluminum filler rods
The following table lists the performance and parameters of the two most commonly used aluminum welding wires, ER4043 and ER5356, including typical welding current, voltage, welding speed, gas flow and other detailed information. If you need to know the performance parameters of other welding wires or have special requirements, please feel free to contact us!
4043 Aluminum filler material is a 5% silicon aluminum filler recommended for welding of 3003, 3004, 5052, 6061, 6063, and cast alloy such as 443, 355, 356 and 214.
Rod Diameter | Rod Length | Welding Current Designation | Tensile Strength (As Welded) | Series |
1/16 in | 36 in | DCEP | - | Super Glaze 4043 TIG |
1/16 in | 36 in | AC | 29 ksi | ER4043 |
3/32 in | 36 in | AC | 29 ksi | ER4043 |
3/32 in | 36 in | DCEP | - | Super Glaze 4043 TIG |
3/32 in | 36 in | AC | 29 ksi | ER4043 |
1/8 in | 36 in | AC | 29 ksi | ER4043 |
1/8 in | 36 in | DCEP | - | Super Glaze 4043 TIG |
1/8 in | 36 in | AC | 29 ksi | ER4043 |
5356 aluminum filler material is a 5% magnesium aluminum filler recommended for welding of 5050, 5052, 5083, 5356, 5454 and 5456.
Rod Diameter | Rod Length | Welding Current Designation | Tensile Strength (As Welded) | Yield Strength (As Welded) | Series |
1/16 in | 36 in | DCEP | 240 to 296 N/mm2 | 110 to 120 N/mm2 | Super Glaze 5356 TIG |
1/16 in | 36 in | AC | 38 ksi | Not Specified | ER5356 |
3/32 in | 36 in | DCEP | 240 to 296 N/mm2 | 110 to 120 N/mm2 | Super Glaze 5356 TIG |
3/32 in | 36 in | AC | 38 ksi | Not Specified | ER5356 |
1/8 in | 36 in | DCEP | 240 to 296 N/mm2 | 110 to 120 N/mm2 | Super Glaze 5356 TIG |
1/8 in | 36 in | AC | 38 ksi | Not Specified | ER5356 |
Filler rod selection guide by welding process and base material
To ensure optimal welding performance and long-term structural reliability, selecting the correct filler rod for your base aluminum alloy and welding application is critical. The chart below provides recommended alloy pairings based on the most common aluminum grades and typical welding scenarios.Quick Quote
Base Material / Alloy Series | Recommended Filler Rods | Notes & Typical Applications |
6061, 6063 (6xxx Series) | ER4043 / ER4943 | ER4043 for general use with excellent flow and crack resistance; ER4943 offers higher post-weld strength |
5083, 5052, 5454 (5xxx Series) | ER5356 / ER5556 | ER5356 for general marine/structural welding; ER5556 for enhanced strength and dynamic load resistance |
3003, 3004, 1100 (1xxx & 3xxx) | ER1100 / ER4043 | ER1100 for pure aluminum and excellent corrosion resistance; ER4043 improves crack resistance in fillet welds |
Cast Aluminum (A356, 319, 355) | ER4047 / ER4043 | ER4047 contains higher silicon for fluidity; ideal for cast repair and shrinkage control |
Heat-treated 6xxx components needing high strength | ER4943 | Improved mechanical properties over ER4043; suitable for structural and pressure applications |
Parts requiring color match after anodizing | ER5356 | Matches base metal color better than 4043; preferred for architectural and aesthetic welds |
Thin-walled components / tubes | ER4043 / ER4047 | Lower melting point, better flow, easier control for manual TIG welding |
- For anodizing applications, avoid 4043 as it produces a gray/black weld; use 5356 instead
- For structural welds requiring higher strength, 4943 is often a better choice than 4043
- For crack-prone castings, prioritize 4047 due to its superior silicon content and fluidity
- Always match filler rod chemistry as closely as possible with the base alloy family for best performance
Product advantages of Chalco aluminum TIG filler rods
Chalco TIG filler rods are engineered to deliver reliable performance across diverse welding tasks, from lightweight structures to corrosion-resistant assemblies. Our products are trusted by manufacturers in aerospace, automotive, marine, and industrial sectors for their outstanding mechanical and welding characteristics.Quick Quote
- High Weld Quality: Smooth arc, clean welds, low spatter, ideal for critical joints
- Excellent Corrosion Resistance: Suitable for marine, chemical, and outdoor environments
- Crack Resistance & Flowability:High-silicon alloys like 4043 / 4047 reduce thermal cracking
- Lightweight with Good Strength: Ideal for aerospace, automotive, and structural applications
- Anodizing Compatibility: Alloys like 5356 offer better post-weld color matching
- All-Position Welding: Usable in flat, vertical, horizontal, and overhead positions
Chalco aluminum TIG filler rod application fields & customer cases
Chalco's aluminum TIG filler rods are trusted by global manufacturers across aerospace, automotive, marine, rail, and industrial sectors. We support both standard production and project-specific customization, delivering real performance in demanding welding environments.Quick Quote
Aerospace
Application: Structural brackets, engine mounts, lightweight tubing assemblies
Case Highlight: Supplied ER4943 and ER4043 filler rods for a leading Chinese aerospace OEM, used in aircraft cabin structures and high-strength components.
Benefit: Superior strength-to-weight ratio and crack resistance under cyclic loading.
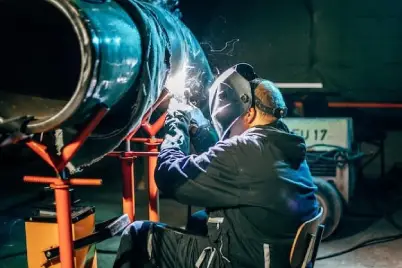
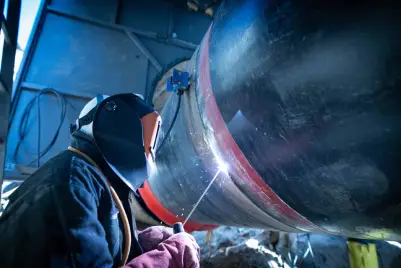
Automotive
Application: EV battery trays, fuel tanks, heat exchangers, structural brackets
Case Highlight: Long-term supply of ER5356 and ER5556 filler rods for Tier-1 automotive parts suppliers in Germany and South Korea.
Benefit: Enhanced corrosion resistance and fatigue durability for aluminum chassis parts.
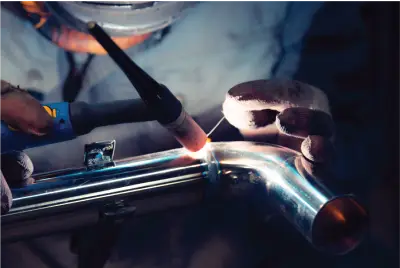
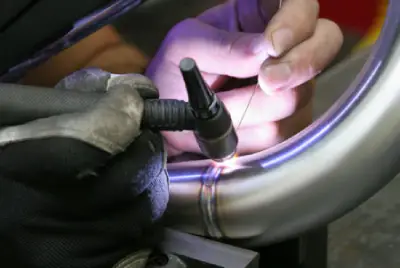
Marine & Offshore
Application: Hull panels, access ladders, offshore platforms, shipboard structures
Case Highlight: ER5183 and ER5356 filler rods used by shipyards in Southeast Asia for aluminum patrol boats and marine tanks.
Benefit: Reliable performance in saltwater environments with strong corrosion protection.
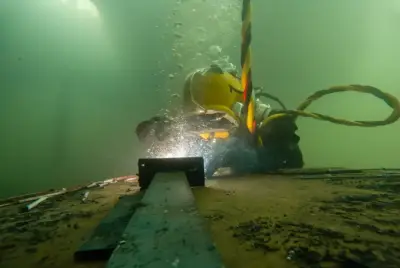
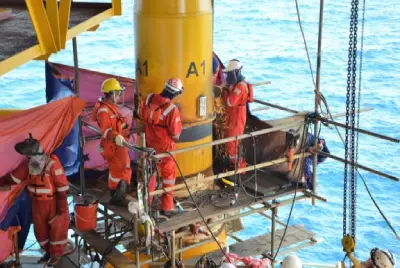
Rail Transportation
Application: Carriage panels, roof beams, equipment frames
Case Highlight: Partnered with rolling stock manufacturers to provide ER5356 and ER4043 rods for urban metro and high-speed train projects in Europe and China.
Benefit: Consistent weld quality on large aluminum panels with good appearance after anodizing.
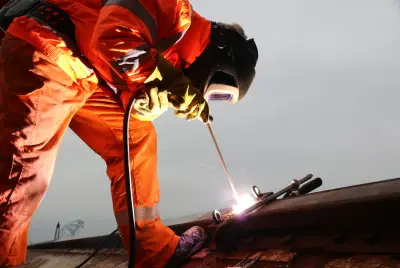
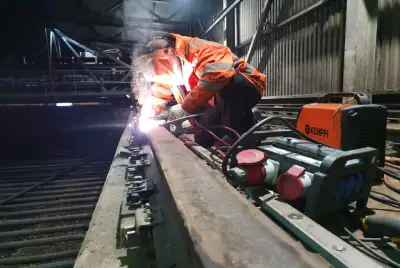
Industrial Equipment
Application: Housings, control cabinets, automation structures
Case Highlight: Delivered ER1100 and ER4047 rods to factory equipment OEMs in Japan and North America.
Benefit: High weldability and corrosion resistance for lightweight structural systems.
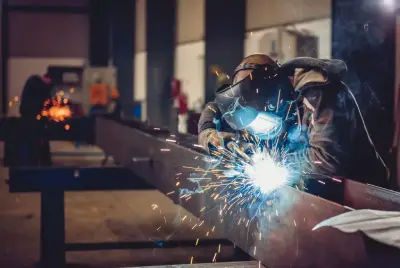
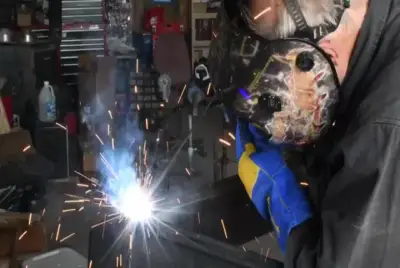
Architectural & Decorative
Application: Curtain wall panels, window frames, aluminum railings
Case Highlight: Supplied ER5356 rods to a facade system manufacturer for anodized aluminum structures in luxury hotel projects.
Benefit: Excellent weld seam appearance and perfect color match after anodizing.
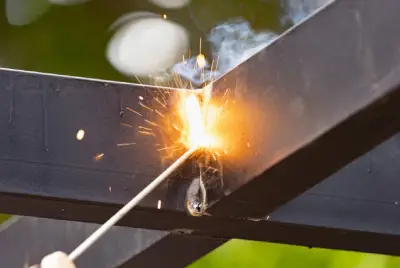
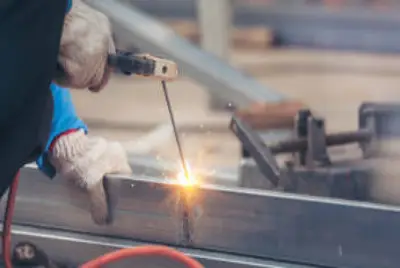
Complete welding solutions beyond filler rods
Chalco doesn't just supply TIG filler rods — we provide comprehensive aluminum welding material systems engineered for performance, consistency, and versatility across all welding methods.
TIG + MIG Wire System
For projects that require both TIG and MIG processes, Chalco offers matching alloy combinations of filler rods and ER-series MIG wires. Ensure seamless transition between manual and automated welding with unified chemistry and arc characteristics.
TIG Rod + Brazing Alloy
Need a solution for heat-sensitive or thin-walled parts? Pair TIG filler rods with our low-temperature brazing alloys to minimize thermal distortion while maintaining joint strength.
- Perfect for EV battery trays, heat exchangers, and HVAC components
- Available as solid rods or flux-cored variants
TIG Rod + Stick Electrode Core Wire
For operations involving both TIG and stick welding (SMAW), Chalco offers aluminum stick core wires precisely matched to our filler rod grades.
- Excellent for outdoor and heavy-duty field welding
- Available cores: ER4043, ER5356, ER5556
One Supplier, One System
Let Chalco support your full aluminum welding material needs — from rods to wires to brazing alloys. We'll help you build the right combination for your equipment, joint design, and environmental conditions. [Quick Quote] to configure your all-in-one welding solution.
Why choose Chalco as your aluminum TIG filler rod supplier
Full-process production capability: Chalco operates modernized production lines with in-house aluminum ingot melting, alloying, continuous casting, and precision rod drawing. Our integrated process ensures tight composition control and stable mechanical properties.
Advanced equipment for high precision: Equipped with high-speed wire drawing machines and automatic straightening & cutting systems, we ensure diameter tolerance within ±0.02 mm, optimized for smooth TIG feeding and consistent arc behavior.
Large-scale output with fast delivery: Monthly capacity exceeds 500 tons of aluminum filler rod, supporting both standard stock and custom alloy orders with short lead times and stable export supply.
Surface treatment & quality inspection: Products are processed through degreasing, anti-oxidation treatments, and online flaw detection to ensure surface cleanliness and welding stability.
Flexible packaging & export service: Standard 36” cut lengths; options for tube, box, or custom packaging Moisture-proof export cartons, pallet wrapping, and OEM labeling supported
Traceable materials & certifications: Alloy batches traceable from ingot to finished rod; documentation available: COA, MSDS, RoHS, REACH, CE
Global experience, one-Stop solution: Proven supply records across aerospace, automotive, shipbuilding, and industrial manufacturing; Chalco not only provides high-quality aluminum TIG filler rods, but also offers a complete portfolio of welding materials — including MIG wires, stick rod core wire, aluminum brazing rods, and TIG filler rods for stainless steel, copper, titanium, nickel, and other alloys — to support your full welding system.
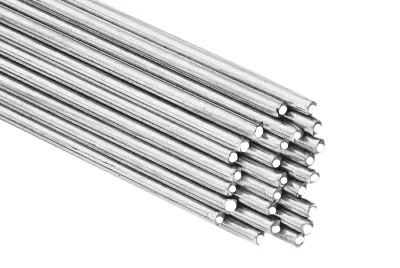
Aluminum brazing rod
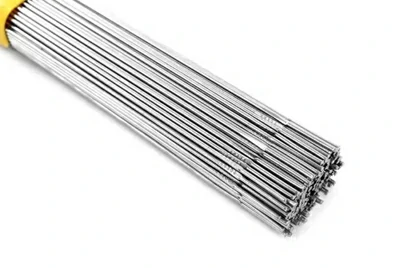
Low temperature welding rod
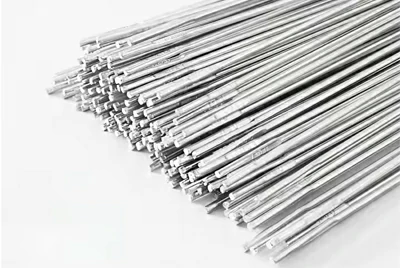
Zirconiated tungsten for aluminum
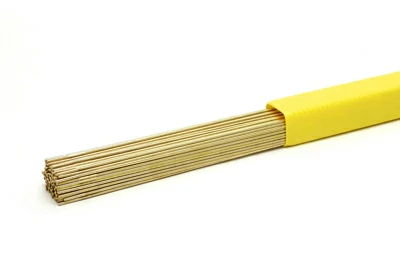
Aluminum gas welding rod
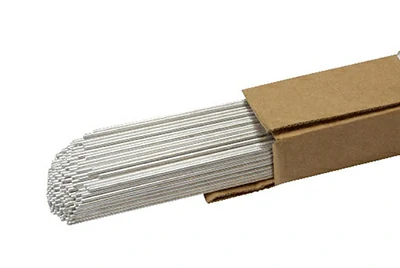
Oxyacetylene welding filler rod
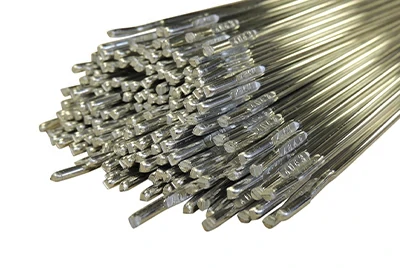
Flux-Cored Wire
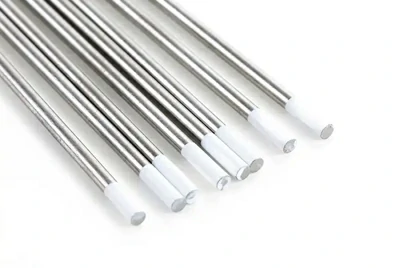
Stainless Steel TIG Welding Rods
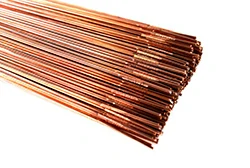
Mild Steel TIG Welding Rods
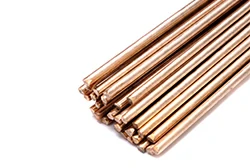
Bronze TIG Welding Rods
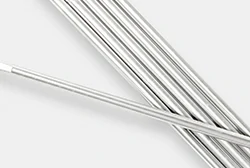
Nickel Alloy TIG Welding Rods
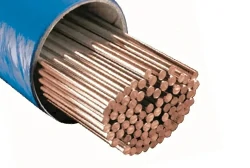
Copper TIG Welding Rods
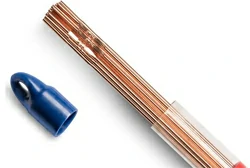
Alloy Steel TIG Welding Rods
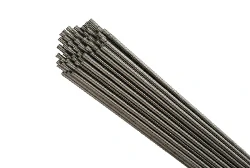
Titanium TIG Welding Rods
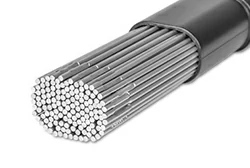
Cast Iron TIG Welding Rods
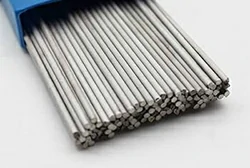
Magnesium TIG welding rods
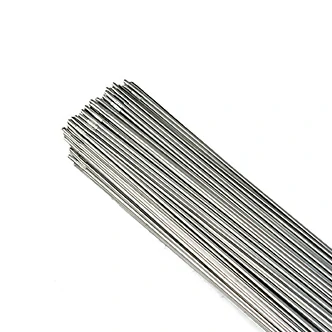
Aluminum stick rod core wire
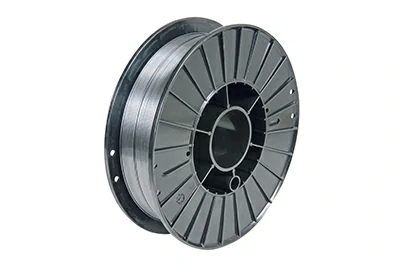
Aluminum welding wire
Knowledge center and FAQ for aluminum filler rod or TIG filler rod
Chalco aluminum filler rod welding position
Can Chalco filler rods be used on cast aluminum?
Yes, silicon-rich alloys such as ER4047 or ER4043 are ideal for welding aluminum castings due to their high fluidity and reduced hot-crack sensitivity.
Which alloy is best for anodized aluminum parts?
ER5356 is recommended for welds requiring a color match after anodizing. ER4043 may result in a dark gray weld zone.
How to properly store and handle aluminum filler metal?
Store rods in a dry, temperature-stable environment. Avoid rapid temperature shifts to prevent condensation. Use sealed packaging or original cartons for optimal protection.
What shielding gas should I use with aluminum TIG filler rods?
Pure Argon (99.99%) is standard. For thicker materials or improved penetration, Argon + Helium blends may be used.
Are Chalco TIG rods compatible with both AC and DCEP current?
Yes. Most aluminum TIG filler rods work well with AC current. Some rods also support DCEP (Direct Current Electrode Positive) in specific applications — please consult datasheets.
What equipment should I use to ensure smooth aluminum wire feeding?
Use a spool gun or push-pull system for MIG, U-groove rollers, nylon liners, and contact tips with slightly oversized apertures to reduce friction and ensure steady feed.
Can I order customized lengths or packaging for filler rods?
Yes. Chalco offers standard 36" TIG rods and supports custom diameters, lengths, and export packaging (tube/box/pallet) upon request.
Do your filler rods come with certification documents?
Absolutely. We provide COA, MSDS, RoHS, REACH, and CE certificates upon request.
What's the difference between TIG rod and MIG wire?
TIG rods are solid cut-length wires used for manual TIG (GTAW) welding. MIG wires come on spools and are continuously fed during MIG welding.
Are filler rod and TIG rod the same thing?
In most cases, yes. "Filler rod" is a general term, while "TIG rod" refers specifically to filler material used in TIG welding.
What does "ER” mean in filler rod designation?
ER” stands for Electrode or Rod. In TIG welding, the rod is fed manually, but the designation still follows AWS ER classifications (e.g., ER4043).
How to choose 4043 and 5356 filling rods
When welding 6XXX series aluminum or 5XXX series aluminum with less than 3% magnesium, 4043 and 5356 aluminum filler rods are both common choices. They both meet high shear strength requirements and provide excellent performance in most aluminum alloy welding applications. However, depending on the specific application requirements, they each have unique advantages in different scenarios.
4043 Aluminum Filler Rod is suitable for the following applications:
- It has excellent high temperature crack resistance when exposed to high temperature environment for a long time (above 150°F).
- Applications that wish to reduce the risk of termination and shrinkage cracking, provide more stable welds and reduce welding defects.
- Welding tasks that require high weld aesthetics can produce bright and clean weld appearance.
- Workpieces that are particularly sensitive to welding deformation can minimize the deformation problems caused by welding.
5356 Aluminum Filler Rod is suitable for the following applications:
- When welding 5XXX or 6XXX series aluminum, higher tensile strengths can be achieved for high strength requirements.
- The base material after anodizing treatment needs to have a good color match, and the weld should have excellent color consistency with the base material.
- In application scenarios that withstand dynamic loads, it provides higher ductility and toughness to ensure the reliability of the welded structure.
- In connection situations where higher shear strength is required, only one welding is required to achieve higher shear strength.
Classification | 4043 Aluminum Filler Rod | 5356 Aluminum Filler Rod | General scenarios |
Applicable Materials | 6XXX aluminum, 5XXX aluminum with less than 3% magnesium | 5XXX Aluminum, 6XXX Aluminum | 6XXX aluminum, 5XXX aluminum with less than 3% magnesium |
High temperature resistance | Suitable for high temperature environments (>150°F) | Not suitable for long-term high temperature environment | - |
Crack resistance | Reduced risk of termination and shrinkage cracking | - | - |
Weld seam aesthetics | Bright and clean welds | Good anodizing color matching | - |
Deformation resistance | Minimize welding deformation problems | - | - |
tensile strength | - | High tensile strength, suitable for high strength requirements | - |
Ductility and toughness | - | High ductility and toughness, suitable for structures subjected to dynamic loads | - |
Shear Strength | Multi-layer welding for high shear strength | High shear strength can be achieved with single-layer welding | For high shear strength requirements, both can be selected, but 5356 is more efficient |
Welding efficiency | Multi-layer welding to achieve high-strength connection | A single layer of welding can meet most strength requirements | - |
How to choose welding materials correctly
Material | Typical properties | Recommended application scenarios | Applicable process | Soldering temperature range (°C) |
Steel | High strength, low cost, good wear resistance; suitable for processing rusty or oxidized materials; wide range of applications. | Structural manufacturing: general machinery manufacturing and repair. | TIG welding, oxyacetylene welding | 1300–1500 |
Building: Steel frame structure. | ||||
Vehicles: welding of automotive parts. | ||||
Copper | It has excellent thermal conductivity and good corrosion resistance, and is suitable for connecting different metals (such as copper and copper, copper and brass). | Plumbing system: such as hot water pipes or cold-water pipe connections. | Silver brazing (15% or 2% silver copper brazing filler metal), oxyacetylene welding | 645–820 (Silver Brazing) |
Electrical equipment: used for the connection of electrical components. | ~1083 (copper melting point, close to welding) | |||
Silver | Low melting point, high fluidity, strong corrosion resistance; suitable for parts requiring high strength, precise fit, and beautiful weld appearance. | Precision manufacturing: HVAC, refrigeration equipment, marine equipment and other parts that require high sealing performance. | Silver brazing (45% silver brazing filler metal) | 640–680 |
Craft decoration: welding of metal products. | ||||
Aluminum | It is light in weight and has good electrical and thermal conductivity, but it requires high welding technology; high thermal conductivity means that heat input needs to be strictly controlled to avoid overheating or insufficient fusion. | Aerospace: aircraft parts and structural parts. | TIG welding (such as 5356 electrode), oxyacetylene welding (rare), argon arc welding | 600–660 (close to the melting point of aluminum alloy) |
Shipbuilding: welding of lightweight components. | ||||
Daily necessities: aluminum product repair. |
Chalco can provide you the most comprehensive inventory of aluminum products and can also supply you customized products. Precise quotation will be provided within 24 hours.
Get a quote