Chalco's aluminum brazing foil is a high-performance clad material engineered for advanced thermal systems. It supports vacuum brazing, Nocolok brazing, and controlled atmosphere brazing (CAB), offering excellent thermal conductivity, corrosion resistance, and consistent weldability.
With customizable multilayer structures—such as 4343/3003/7072 and 4045/3102—our foil is widely used in fin stock for automotive radiators, HVAC units, and battery cooling modules, as well as in headers, cold plates, and multi-layer heat exchanger components. The following product structure chart and category overview will help you better understand Chalco's brazing foil range and its key application types.
Brazing layer grade | Base grade | Temper | Coverage rate (%) | Thickness(mm) | Width(mm) | Plate length (mm) | Coil inner diameter (mm) | Coil outer diameter (mm) |
4A13 4A17 4A43 4A45 4045 4045 4047 4104 4343 |
3A11 3003 3003 6A02 6060 6082 6951 7A11 7072 |
O H12 H22 H14 H24 H24 H16 H26 |
3.0 ~ 25.0 | 0.050 ~ 6.000 | 7.0 ~ 1600.0 | ≤10, 000 |
75.0 150.0 200.0 250.0 300.0 400.0 500.0 505.0 |
2500.0 |
The order of alloy structure is "brazing layer/substrate layer", such as 4343/3003 | ||||||||
The 7072 grade is an anodic anti-corrosion layer, which is usually used as an outer layer in a three-layer or multi-layer structure. |
Aluminum brazing foil
-
Chalco's general-purpose aluminum brazing foil is designed for a wide range of standard thermal assemblies such as cold plates, headers, and clad panels. It offers stable brazing behavior, good thermal conductivity, and excellent dimensional control, making it suitable for various automotive, industrial, and power electronic applications.Quick Quote
Chalco single-side clad foil
Our single-sided composite brazing aluminum foil has good weldability and cost-effectiveness, and is suitable for heat exchange systems with low structural strength requirements and welding concentrated on one side.
The cooperation areas are extensive: condenser fins, headers, heat pipe brackets, and automotive water cooling structures.
Hot selling alloy combination includes:
- 4343/3003
- 4343/3102
- 4045/3003
- 4345/3003
- 4343/6951
Chalco double-side clad foil
The double-sided cladding structure is suitable for components that are welded on both sides at the same time, which improves the overall structural connection strength and is a common form of automotive heat exchanger structure.
Typical application areas: evaporator, multi-channel cooling structure, fuel cell cold plate, etc.
Hot selling alloy combination includes:
- 4343/3003/4343
- 4343/3102/4343
- 4345/3003/4345
- 4045/3003/4045
- 4343/3003/4045
- 4104/3003/4104
- 4045/3102/4045
Chalco brazing foil core material
Chalco can also supply high-strength core aluminum foil for customers' secondary coating, deep processing or high-strength structural parts production to meet internal composite, molding or intermediate layer manufacturing needs.
Typical application areas: brazing aluminum strip production, heat sink fins, guide vanes, cold plate support layers, etc.
Available alloys and structures:
- 3003 general brazing core
- 3003+Zn modified al core
- 3102 thermal core
- 6061 high strength core
- 6951 heat-resistant core
Customizable thickness of 0.07–0.25mm, O/H14/H24/H18 state; delivered in coils, supports pre-treatment such as degreasing, cleaning, and anode.
Fin stock brazing foil
-
Chalco's fin stock brazing foil is engineered for high-volume production of heat exchanger fins used in automotive radiators, HVAC systems, and EV battery cooling modules. With stable clad structures and excellent thermal conductivity, it ensures reliable performance in stamped fin assemblies requiring precise geometry, strong brazing joints, and long-term corrosion resistance.Quick Quote
- Suitable for corrugated/fish scale/serrated embossing process
- Support multi-layer composite design (double package/triple layer)
- High brazing compatibility, good fin integrity after welding
- With Zn corrosion protection or battery thermal management optimization structure
Recommended thickness range: 0.05–0.15 mm
Examples of typical alloy structures:
- 4343/3003
- 4343/3003/7072
- 4045/3102/7072
It can provide subsequent services such as coil cutting, cut-to-length cutting, surface treatment, oxidation cleaning, etc. to meet the requirements of batch automated fin stamping lines for material consistency and processability.
Chalco corrosion-resistant & high-performance brazing foil
-
For harsher service conditions, Chalco offers corrosion-resistant and high-performance brazing foils featuring multi-layer composite structures. These products are ideal for marine HVAC systems, battery cold plates, and fuel cell modules, where both long-term reliability and structural integrity under corrosion or stress are critical.Quick Quote
Typical application areas: automotive condensers and evaporators, ship refrigeration systems, new energy battery cooling modules, precision liquid cooling structural parts, industrial heat exchangers (high salt spray environment).
Hot selling alloy combination includes:
- 4343/3003/7072
- 4045/3003/7072
- 4343/3003+Zn/7072
- 4343/6061/7072
- 4343/6951/7072
- 4045/3102/7072
In addition to high-quality brazing foil, we also offer a variety of brazing materials, including brazing aluminum strip, filler rods, and welding wires, fully meeting your diverse needs across different brazing processes. Explore our brazing materials range and let us help enhance your production efficiency and welding quality.Quick Quote
Chalco brazing composite aluminum foil product technical parameters and performance indicators
To ensure the long-term stability of brazing aluminum foil in complex heat exchange structures and precision welding processes, Chalco strictly controls key properties such as thickness, tolerance, tensile strength, ductility and corrosion resistance. The following are the core technical parameters of representative brazing foil products, covering typical values of different cladding structures and core alloys, to support customers in efficient comparison in material selection and structural design.
The data in the table are based on YS/T 446 and GB/T standards, and combined with Chalco's independent test results, which are suitable for typical specifications of mass-produced products. We can provide higher-level performance customization solutions and third-party test reports according to customer requirements.
Chalco brazing aluminum foil coverage deviation
Coverage rate (%) | Coverage rate tolerance (%) |
3.0~6.0 | ±1.2 |
>6.0~8.0 | ±1.5 |
>8.0~13.0 | ±2.0 |
>13.0~25.0 | ±3.0 |
Chalco brazing aluminum foil thickness deviation
Thickness(mm) | ≤1000 mm width deviation | >1000~1320 mm width deviation | >1320~1600 mm width deviation |
0.050~0.100 | ±0.006 | ±0.006 | ±0.006 |
>0.100~0.200 | ±0.015 | ±0.015 | ±0.015 |
>0.200~0.400 | ±0.020 | ±0.030 | ±0.040 |
>0.400~0.700 | ±0.030 | ±0.040 | ±0.050 |
>0.700~1.000 | ±0.040 | ±0.050 | ±0.060 |
Chalco composite aluminum foil width deviation
Width range(mm) | Width tolerance (mm) |
7.0~100.0 | ±0.1 |
>100.0~300.0 | ±0.3 |
>300.0~1320.0 | ±1.0 |
Room temperature tensile mechanical properties of Chalco composites
Temper | Thickness(mm) | Tensile strength Rm (N/mm²) | Specified non-proportional elongation strength Rp0.2 (N/mm²) | Elongation after fracture A50mm (%) |
O | 0.050~0.100 | 95~160 | 35 | ≥6.0 |
>0.100~0.200 | 35 | ≥10.0 | ||
>0.200~1.300 | 35 | ≥18.0 | ||
H12 | 0.050~0.100 | 120~170 | 90 | ≥1.0 |
>0.100~0.200 | 90 | ≥3.0 | ||
>0.200~1.300 | 90 | ≥4.0 | ||
H22 | 0.050~0.100 | 120~170 | 80 | ≥2.0 |
>0.100~0.200 | 80 | ≥6.0 | ||
>0.200~1.300 | 80 | ≥6.0 | ||
H14 | 0.050~0.100 | 150~200 | 125 | ≥0.5 |
>0.100~0.200 | 125 | ≥1.0 | ||
>0.200~1.300 | 125 | ≥2.0 | ||
H24 | 0.050~0.100 | 150~200 | 115 | ≥1.0 |
>0.100~0.200 | 115 | ≥3.0 | ||
>0.200~1.300 | 115 | ≥3.0 | ||
H16 | 0.050~0.100 | 170~230 | 150 | ≥0.5 |
>0.100~0.200 | 150 | ≥1.0 | ||
>0.200~1.300 | 150 | ≥2.0 | ||
H26 | 0.050~0.100 | 170~230 | 140 | ≥1.0 |
>0.100~0.200 | 140 | ≥2.0 | ||
>0.200~1.300 | 140 | ≥3.0 | ||
H18 | >0.100~0.200 | ≥200 | 170 | ≥0.5 |
>0.200~6.000 | 170 | ≥1.0 |
Room temperature tensile mechanical properties of composite materials
Temper | Thickness(mm) | Tensile strength Rm (N/mm²) | Specified non-proportional elongation strength Rp0.2 (N/mm²) | Elongation after fracture A50mm (%) |
O | 0.050~0.100 | 95~165 | 35 | ≥6.0 |
>0.100~0.200 | 35 | ≥10.0 | ||
>0.200~1.300 | 35 | ≥18.0 | ||
H12 | 0.050~0.100 | 125~205 | 90 | ≥1.0 |
>0.100~0.200 | 90 | ≥2.0 | ||
>0.200~1.300 | 90 | ≥3.0 | ||
H22 | 0.050~0.100 | 125~205 | 80 | ≥2.0 |
>0.100~0.200 | 80 | ≥3.0 | ||
>0.200~1.300 | 80 | ≥7.0 | ||
H14 | 0.050~0.100 | 145~225 | 125 | ≥1.0 |
>0.100~0.200 | 125 | ≥2.0 | ||
>0.200~1.300 | 125 | ≥4.0 | ||
H24 | 0.050~0.100 | 145~225 | 115 | ≥2.0 |
>0.100~0.200 | 115 | ≥3.0 | ||
>0.200~1.300 | 115 | ≥5.0 |
Room temperature tensile mechanical properties of composite materials
Brazing layer: 4004, 4045, 4104, 4343
Matrix: 6A02, 6060, 6063, 6951
Temper | Thickness(mm) | Tensile strength Rm (N/mm²) | Specified non-proportional elongation strength Rp0.2 (N/mm²) | Elongation after fracture A50mm (%) |
O | 0.200~6.000 | ≤160 | 85 | 16.0 |
Room temperature tensile mechanical properties of composite materials for fins
Brand: 4A13, 4A17, 4A43, 4A45, 4004, 4045, 4104, 4343
Base: 3A11, 3003, 7A11
Temper | Thickness(mm) | Tensile strength Rm (N/mm²) | Specified non-proportional elongation strength Rp0.2 (N/mm²) | Elongation after fracture A50mm (%) |
H14 | 0.050–0.100 | 150–210 | 135 | ≥0.5 |
>0.100–0.200 | ≥1.0 | |||
H16 | 0.050–0.100 | 170–230 | 160 | ≥0.5 |
>0.100–0.200 | ≥1.0 |
Comprehensive brazing foil solutions for 6 major sectors by Chalco
As a key material in composite heat exchange structures, brazing aluminum foil is widely used in automotive thermal management, new energy battery cooling, rail transit HVAC, industrial refrigeration and air conditioning heat exchange, military and aviation thermal control systems, etc. According to different service environments and welding methods, customers have highly differentiated requirements for foil thickness, composite structure, solder alloy, anti-corrosion layer, thermal conductivity, etc.
Automotive heat exchangers
Chalco provides integrated brazing foil solutions for automotive heat exchangers, supporting both fin stamping and core structure bonding.Quick Quote
Aluminum fin stock: Used in radiator, condenser, and intercooler fins. Offers excellent embossing formability, corrosion resistance, and brazing compatibility.
Aluminum brazing foil: Applied in evaporators, multi-channel condensers, and cold plates. Delivers strong joint strength and long-term reliability under high pressure and corrosive environments.
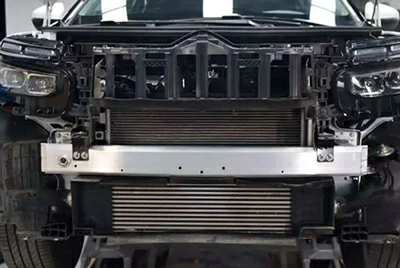
Chalco's proven supply of brazing foil & fin stock grades for automotive heat exchangers:
- 4343/3003/7072 clad brazing foil: Widely used in condensers and evaporators
- 4045/3102/7072 clad brazing foil: Ideal for internal circulation condensing systems
- 4343/6951/4343 clad brazing foil: High-strength, for intercoolers
- 4343/6061/7072 clad brazing foil: Heavy-duty engine cooling applications
- 4343/3003+Zn/7072 clad brazing foil: Enhanced corrosion resistance for coolers
- 4343/3003-H14 aluminum fin stock: For radiator and condenser fins
- 3003-H16/6951 aluminum fin stock: For intercooler fins and battery module fins
Product display:
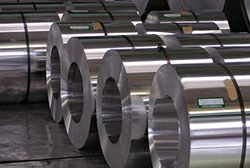
Composite aluminum brazing foil
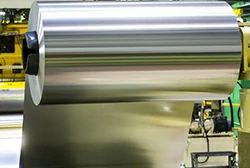
4343/3003-H14 Fin Stock Foil
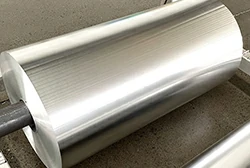
4045/3003 coil + spray coating pretreatment
New energy batteries and thermal control systems (battery cooling systems)
Chalco delivers advanced brazing foil solutions for EV battery cooling modules, integrating both precision fin stamping and multi-layer cold plate brazing.Quick Quote
Aluminum fin stock: Used for compact fins in battery module radiators and structural heat-dissipation channels. Offers thin-gauge consistency, good thermal conductivity, and post-brazing integrity.
Aluminum brazing foil: Applied in cold plates, battery side plates, and internal circulation structures. Enables strong bonding, leak-proof seals, and improved corrosion resistance under high-performance electric drive conditions.
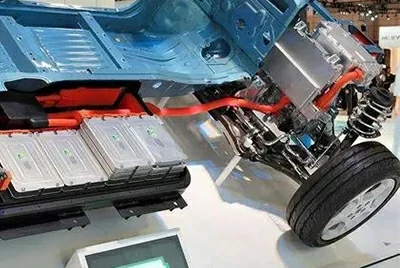
Chalco's proven supply of brazing foil & fin stock grades for battery cooling systems:
- 4343/3003+Zn/7072 clad brazing foil: For high-power cold plates with enhanced corrosion protection
- 4045/3102/7072 clad brazing foil: For lightweight battery module radiators
- 4343/6951/7072 clad brazing foil: Suitable for high-strength battery cooling structures
- 4343/6061/7072 clad brazing foil: High thermal conductivity + structural strength
- 4004/3003/7072 clad brazing foil: For large-size, multi-channel cold plates
- 3003-H16/6951 aluminum fin stock: Used in compact fins for battery module radiators
- 4343/3102-H18 fin stock foil: Optimized for integrated electric cooling channels
Product display:
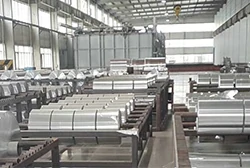
3003-H16/6951 Fin Stock Foil
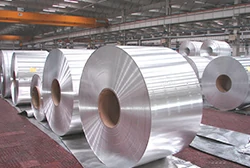
4045/3003/7072 Brazing Coil
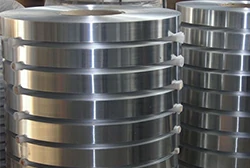
4343/3102/4343 Brazing Strip
HVAC & commercial cooling
Chalco offers comprehensive brazing foil solutions for HVAC and commercial cooling systems, supporting fin-type evaporators, condensers, and heat pump modules.Quick Quote
Aluminum fin stock: Used in condenser and evaporator fins of air conditioners and chillers. Provides excellent shape retention, brazing performance, and uniformity for high-speed stamping.
Aluminum brazing foil: Applied in headers, distribution pipes, and structural plates. Delivers strong sealing performance and reliable corrosion resistance for long-cycle HVAC operations.
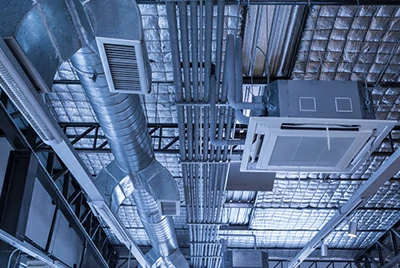
Chalco's proven supply of brazing foil & fin stock grades for HVAC & commercial cooling:
- 4045/3003/7072 clad brazing foil: For condensers and main HVAC heat exchange structures
- 4343/3102/7072 clad brazing foil: Designed for chiller fin structures and condensing modules
- 4343/3003/4343 clad brazing foil: Ideal for large evaporator plates in commercial HVAC
- 4004/3003/7072 clad brazing foil: Custom structure for heat pump units
- 4343/6951/7072 clad brazing foil: Suitable for large current distribution and header structures
- 3003-H16 aluminum fin stock: Standard for condenser/evaporator fins
- 4343/3003-H18 aluminum fin stock: For heavy-duty commercial air conditioning units
Product display:
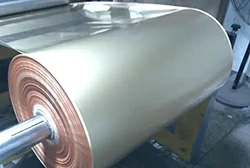
3003-H16 Fin Foil
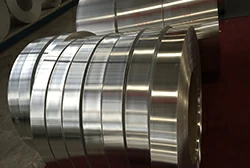
4343/3003/7072 Coil
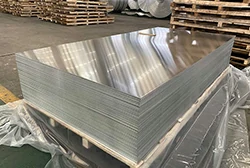
4343/3003/7072 Coil
Heavy machinery & rail systems
Chalco delivers robust brazing foil solutions for industrial machinery and rail cooling systems, engineered for large plate-fin assemblies under medium-to-high pressure conditions.Quick Quote
Aluminum fin stock: Used in engine oil coolers, onboard AC fins, and structural cooling units. Ensures excellent vibration resistance, formability, and thermal stability.
Aluminum brazing foil: Applied in plate cores, shells, and complex multi-channel joints. Provides superior joint strength, weld integrity, and reliability under harsh working environments.
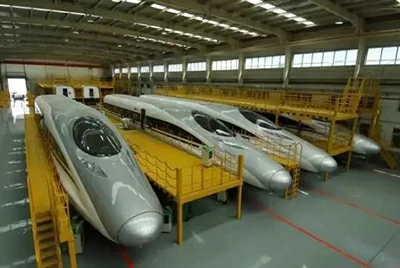
Chalco's proven supply of brazing foil & fin stock grades for heavy machinery & rail systems:
- 4343/6061/7072 clad brazing foil: High strength and weldability for heavy-duty vehicle coolers
- 4343/3003/7072 clad brazing foil: For air conditioning condensers in trains and buses
- 4045/3102/7072 clad brazing foil: Universal solution for high-throughput cooling modules
- 4343/6951/7072 clad brazing foil: Withstands vibration, ideal for machinery cooling components
- 4343/3102/4343 clad brazing foil: High welding strength for long-distance transport systems
- 3003-H16 aluminum fin stock: Standard option for large structural fins
- 6951-H24 aluminum fin stock: Reinforced fin material for industrial cooling platforms
Product display:
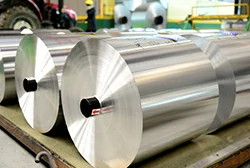
Large fin aluminum foil material
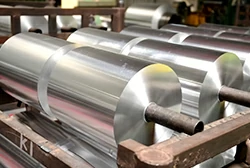
Multilayer plate-fin structure brazing coil
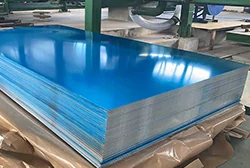
Structural plate + tube shell brazing plate combination
Marine cooling & anti-corrosion systems
Chalco offers high-corrosion-resistant brazing foil solutions for marine HVAC, offshore platforms, and ship engine cooling, built to withstand extreme salt spray and moisture conditions.Quick Quote
Aluminum fin stock: Used in marine AC fins and oil cooler fins. Features anti-corrosion layers and stable formability for long-term offshore operation.
Aluminum brazing foil: Applied in condenser cores, plate assemblies, and engine heat exchangers. Combines strong structural bonding with anodic protection for aggressive marine environments.
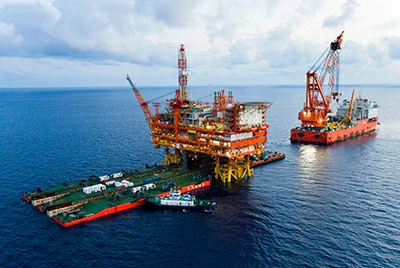
Chalco's proven supply of brazing foil & fin stock grades for marine cooling systems:
- 4343/3003/7072 clad brazing foil: For marine air conditioning condenser cores
- 4343/3102/7072 clad brazing foil: For offshore platform cooling and anti-corrosion exchangers
- 4343/6951/7072 clad brazing foil: Reinforced composite for modular marine cooling systems
- 4045/3003/7072 clad brazing foil: Lightweight multi-layer option for compact marine heat exchangers
- 4343/6061/7072 clad brazing foil: High-strength corrosion-resistant structure for ship engine bays
- 3003+Zn aluminum fin stock: Enhanced salt spray resistance for condenser fins
- 3003-H24/7072 aluminum fin stock: Clad-fin foil for marine and offshore HVAC modules
Product display:
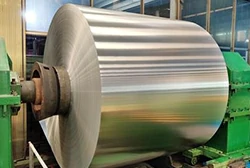
High corrosion resistant brazing coil (double-sided 7072)
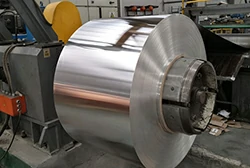
Anti-corrosion fin aluminum foil (3003+Zn)
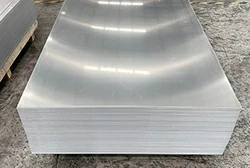
Brazing structural plates (composite cladding)
Three aspects to confidently choose Chalco brazing aluminum foil
As a source manufacturer of aluminum alloy composite materials, Chalco offers a fully integrated production chain for brazing aluminum foil, from casting, rolling, composite bonding, to heat treatment, cutting, testing, and packaging. All key processes are independently controlled, ensuring stable quality, fast delivery, and full traceability. We provide customized solutions to meet the strict requirements of global heat exchanger, power battery, and electronic thermal management industries.Quick Quote
1. Advanced composite rolling capability
Chalco supports single-side, double-side, and multi-layer structures, with widths from 7 mm to 1320 mm and thickness down to 0.0045 mm. Our high-precision control ensures thickness tolerance up to ±0.006 mm, suitable for cold plates, battery modules, and other demanding applications.
2. Clean & Precise production environment
Production is conducted in high-cleanliness environments, meeting standards for aerospace and electronic materials. This ensures excellent surface cleanliness, batch consistency, and product reliability.
3. Flexible customization & packaging
Chalco offers custom alloy design (e.g., Zn-modified, anti-corrosion, high thermal conductivity layers), cut-to-length or die-cut processing, and support for various tempers (O, H12, H14, etc.). Packaging is export-ready, with options for vacuum sealing, anti-static, moisture-proof, and wooden crate shipping for sea, air, or rail transport.
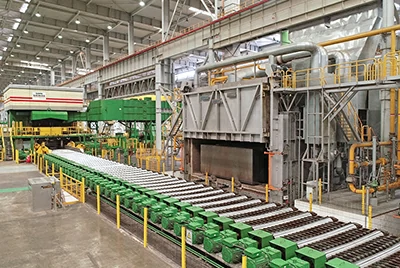
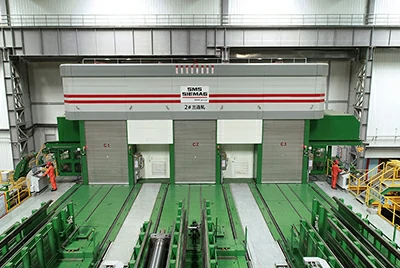
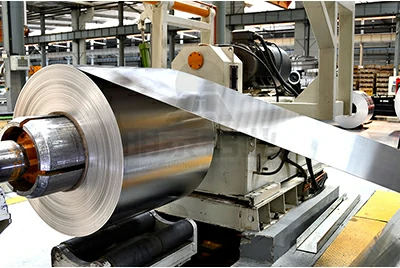
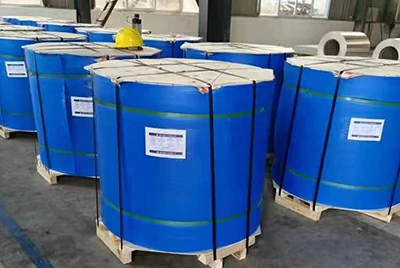
FAQ for purchasing Chalco Brazing Aluminum Foil
Does Chalco support customized service for brazing aluminum foil?
Yes, Chalco provides customized brazing aluminum foils in single-sided, double-sided, triple-layer and multi-functional composite structures. The alloy combination, coverage, thickness, width, roll diameter and surface pretreatment can be customized according to customer requirements to meet the process requirements of different application scenarios .
What is the typical thickness and width range for brazing foil?
The conventional thickness range is 0.05mm-0.30mm, and the width range is 10mm-1320mm. The ultra-thin structure can be as thin as 0.03mm, and it also supports precision slitting and fixed roll diameter delivery.
What typical brazing structures are suitable for automotive heat exchange systems?
The recommended structure is:
- 4343/3003/4343 (double cladding)
- 4343/3003/7072 (three-layer anti-corrosion structure)
- 4045/3102/7072 (high corrosion resistant composite)
- 4343/6951/7072 (high-strength core material structure)
These structures are widely used in condensers, evaporators, battery cold plates and other fields.
Does Chalco provide post-processing of brazing foils such as fin stamping?
We can provide supporting materials for fin processing. Some cooperation projects support primary processing services such as punching, forming, and punching. We can also provide recommendations and parameter support for composite brazing foils for fin stamping.
What are the main states of brazing aluminum foil? Can it be heat treated?
Common states of brazing aluminum foil include O, H12, H14, H16, H18, H22, H24, H26, etc. Most products are non-heat-treated strengthened alloys (such as 3003, 6951, etc.), and some core materials (such as 6061) can be heat-treated to improve strength.
Is brazing foil suitable for vacuum brazing, hydrogen brazing or salt bath brazing?
Chalco products are widely used in vacuum brazing and hydrogen shielded brazing. If there is a special atmosphere or heat source requirement (such as salt bath, induction brazing), it is recommended to specify the process environment in advance so that we can optimize the coverage, alloy layer thickness and diffusion control.
How to choose the alloy structure of brazing aluminum foil?
- Is an anti-corrosion layer required (such as 7072)?
- Soldering temperature and fluidity (such as 4343 vs 4045)
- Are there any core material strength requirements (such as 6951, 6061)
- Whether deep drawing, molding, bending and other processing requirements are required in the future
If you have more technical selection or project customization requirements, please click "Get a quote" at the bottom of the page to get one-on-one support and sample recommendations from engineers!
Chalco can provide you the most comprehensive inventory of aluminum products and can also supply you customized products. Precise quotation will be provided within 24 hours.
Get a quote