Aluminum welding wire is a solid alloy wire designed for automatic wire feeding systems (MIG/TIG), offering faster welding speeds than stick welding rods used in SMAW (Shielded Metal Arc Welding) and better cost efficiency than TIG filler rods (Gas Tungsten Arc Welding). With less manual work required, it is ideal for automated and high-volume production. High-quality welding wire is essential for achieving strong, clean welds.
Chalco aluminum welding wires—including 4043, 5356, 5556, 5183, and other alloys—are certified to ISO 9001 and IATF 16949 and meet AWS A5.10 and ISO 18273 standards. Chalco also provides full documentation such as COA, MSDS, COC, and RoHS to ensure customers' confidence in product quality. This strict quality control ensures excellent welds with minimal spatter, making them widely used in automotive, shipbuilding, rail, and other industries.
Chalco aluminum welding wire product introduction
Alloy series: 4043, 5356, 5556, 5183, 4643, 4943, 4047, 5554, 1100 Click to [alloy detail]
Welding Methods: MIG (manual/automatic/flux-cored), TIG with automatic wire feed
Welding Positions: flat, horizontal, vertical (up/down), overhead
Surface Finish: bright silver, brushed, optional anti-oxidation coating
Common Diameters: 0.030" (0.8mm), 0.035" (0.9mm), 0.045" (1.2mm), 1/16" (1.6mm), 3/64" (1.2mm), 5/64" (2.0mm), etc.
Wire Condition/Tolerance: F temper; ISO 544 h9 ±0.02mm
Packaging: 0.5kg, 1kg, 5kg, 15kg spools; 300mm/400mm cores; custom large spools (50-250kg) and packaging tailored to MIG torch systems
Chalco hot-selling welding wire products and base material compatibility
To meet the diverse welding needs of different aluminum base alloys, Chalco offers a wide range of aluminum welding wires covering Al-Si, Al-Mg, and their modified series. Whether for welding 6xxx series structural components or high-strength, corrosion-resistant joints in the 5xxx series, Chalco wires deliver precise compatibility in terms of strength, flowability, crack resistance, and anodized surface appearance.
Top choice for welding: 4043 and 5356 —— Best-selling aluminum welding wires
- 4043 aluminum welding wire
Compatible base alloys: 6xxx series aluminum (e.g., 6061, 6063)
Welding system: GMAW/MIG (manual, automatic, robotic); shielding gas: pure argon or Ar-He mix
- 5356 aluminum welding wire
Compatible base alloys: 5xxx series (e.g., 5052, 5083, 5454, 5356), also suitable for 6xxx series
Welding system: GMAW/MIG (manual, automatic); shielding gas: pure argon
Alloy | Si (%) | Fe (%) | Cu (%) | Mn (%) | Mg (%) | Cr (%) | Zn (%) |
4043 | 4.5–6.0 | ≤0.80 | ≤0.30 | ≤0.05 | ≤0.05 | — | ≤0.10 |
5356 | ≤0.25 | ≤0.40 | ≤0.10 | 0.05–0.20 | 4.5–5.5 | 0.05–0.20 | ≤0.10 |
- Lower melting point, good weld pool flow
- Strong resistance to hot cracking
- Less spatter, smooth and neat weld bead
- Weld bead can be anodized gray or dark gray
- High weld strength and load capacity
- Excellent corrosion resistance, ideal for marine environments
- Good weld metal ductility, better crack resistance than standard Al-Mg wires
- Weld bead color close to base metal, good for decorative use
4643 aluminum welding wire– ideal match for anodized color consistency
4643 aluminum welding wire is an Al-Si-Mg alloy offering the fluidity of 4043 with improved anodizing color match, ideal for visible structural welds.
Compatible base alloys: 6xxx series aluminum with anodizing requirements (e.g., 6061, 6063)
Welding systems: Suitable for conventional and robotic MIG wire feeding systems
Element | Si | Fe | Cu | Mn | Mg | Zn | Ti | Be |
Range % | 3.6–4.6 | ≤0.80 | ≤0.10 | ≤0.05 | 0.10–0.30 | ≤0.10 | ≤0.15 | ≤0.0008 |
4943 aluminum welding wire – upgraded 4043 for higher strength welding
4943 aluminum welding wire is an Al-Si-Mg-Zr alloy offering upgraded strength over 4043 with excellent fluidity and crack resistance, ideal for high-strength 6xxx series welds.
Compatible base alloys: 6xxx series heat-treated aluminum alloys (e.g., 6061-T6)
Welding systems: Standard/automatic MIG systems; pure argon shielding gas recommended
Element | Si | Fe | Cu | Mn | Mg | Others | Al (balance) |
Range % | ~5.5 | ≤0.80 | ≤0.10 | ≤0.15 | — | — | Remainder |
5183 aluminum welding wire – marine-grade high strength and corrosion resistance
5183 aluminum welding wire is a high-magnesium alloy providing superior weld strength and seawater corrosion resistance, preferred for marine and structural applications.
Compatible base alloys: High-strength 5xxx series (e.g., 5083, 5456, 5056)
Welding systems: MIG welding (manual, automatic); shielding gas: pure argon
Element | Si | Fe | Cu | Mn | Mg | Cr | Zn | Ti |
Range % | ≤0.40 | ≤0.40 | ≤0.10 | 0.50–1.00 | 4.3–5.2 | 0.05–0.25 | ≤0.25 | ≤0.15 |
5556 aluminum welding wire – military-grade strength and fatigue resistance
5556 aluminum welding wire is a high-strength Al-Mg alloy offering superior fatigue resistance and stability for demanding structural welding tasks.
Compatible base alloys: High-strength 5xxx series (e.g., 5086, 5456, 5083)
Welding systems: Compatible with standard, automated, and high-load MIG systems
Element | Si | Fe | Cu | Mn | Mg | Cr | Zn | Ti |
Range % | ≤0.25 | ≤0.40 | ≤0.10 | 0.50–1.0 | 4.7–5.5 | 0.05–0.20 | ≤0.25 | ≤0.20 |
4047 aluminum welding wire – high-silicon wire for superior sealing and flow
High-silicon aluminum alloy with excellent flow and airtight welds, ideal for casting repair and precision sealing applications.
Compatible base alloys: Aluminum castings (e.g., A356), specialty alloys, heat exchanger substrates
Welding systems: MIG automatic feed and precision equipment; pure argon shielding gas recommended
Element | Si | Fe | Cu | Mn | Mg | Zn | Al (balance) |
Range % | 11–13 | ≤0.80 | ≤0.30 | ≤0.15 | ≤0.10 | ≤0.20 | Remainder |
5087 Aluminum Welding Wire – Zirconium-enhanced alloy for superior corrosion resistance and flexibility
High-strength aluminum welding wire with ~4.5% magnesium and zirconium for grain refinement. Offers excellent corrosion resistance, good bendability, and reduced hot cracking sensitivity.
Compatible base alloys: Select 5xxx, 6xxx, 7xxx series such as 5083, 6082, 7005, 7020...
Applications: Shipbuilding, storage tanks, high-speed trains, automotive...
Element | Si | Fe | Cu | Mn | Mg | Cr | Zn | Ti |
Range % | ≤0.25 | ≤0.40 | ≤0.05 | 0.70–1.10 | 4.5–5.2 | 0.05–0.25 | ≤0.25 | ≤0.15 |
5754 Aluminum Welding Wire – high-magnesium alloy with excellent strength and corrosion resistance
Aluminum welding wire with about 3% magnesium, offering moderate strength and good corrosion resistance.
Compatible base alloys: 3% magnesium cast and wrought alloys and 5xxx series wrought alloys, plus some 6xxx series
Applications: Suitable for various structural and corrosion-resistant aluminum welding needs
Element | Si | Fe | Cu | Mn | Mg | Cr | Zn | Ti |
Range % | ≤0.40 | ≤0.40 | ≤0.10 | ≤0.50 | 2.6–3.6 | ≤0.30 | ≤0.20 | ≤0.15 |
More optional aluminum alloy and welding wire alloy customization services
Beyond standard 4043 and 5356 alloys, Chalco offers a broad range of aluminum and specialty welding wires to meet diverse needs—whether for corrosion resistance, high-strength welds, anodizing color match, casting repair, conductivity, or aerospace use. We also support custom alloy development and supply select non-aluminum wires like aluminum bronze, copper, and nickel-aluminum for multi-metal applications.
- 1100 al welding wire
1100 is a pure aluminum welding wire for 1050, 1060, and 1070 alloys, offering good ductility and conductivity—ideal for low-strength joints, electrical parts, and decorative welds.
- 6061 al welding wire
Though mainly used as base material, 6061 is also available as welding wire for specific self-welding or custom jobs requiring precise composition match with the base metal.
- 5554 al welding wire
A medium-strength aluminum-magnesium wire for welding 5454 and 5554 alloys, commonly used in fuel tanks, marine parts, and other corrosion-resistant applications.
- Aluminum bronze welding wire
Offers excellent corrosion resistance and strength; used for repairing copper alloy parts like pumps and valves, and for copper-aluminum transition joints.
- Copper alloy welding wire
Suitable for welding copper, copper alloys, and copper-stainless steel; known for great conductivity in electrical, thermal, and precision applications.
- Nickel-aluminum welding wire
Resistant to high temperatures and corrosion; ideal for surfacing and structural repairs in power plants, nuclear facilities, and wear-prone alloy parts.
- Titanium welding wire
Excellent strength-to-weight ratio, corrosion resistance, and high-temperature performance; suitable for aerospace, chemical processing, and marine applications.
- Al-Mg-Sc welding wire
Enhanced strength, toughness, and weldability through rare earth element modification; ideal for demanding structural and automotive applications.
- Wire+arc additive manufacturing wire
High purity and consistent feed characteristics ensure reliable performance in additive manufacturing; suitable for prototyping and lightweight structural components.
If you cannot fully match the existing welding wire products in your actual project, please contact Chalco's technical team for customized solutions or recommended alternative alloys.
Instant QuoteGuide for choose the welding wire according to the base metal
Base metal | 7003 | 6061 6063 6101 | 5086 5083 5056 | 5154 5454 | 5052 | 5005 | 2219 | 2014 2017 | 3004 | 1200 | 1100 3003 | 1070 1050 |
1070 1050 | 5356 (2)(4)(5) | 4043 (5)(7) | 5356 (2) | 5356 (2)(4)(5) | 4043 (2)(5) | 1100 (1)(4)(5) | 4145 (4)(5) | 4145 | 4043 (2)(5) | 1200 (1)(4)(5) | 1100 (1)(4)(5) | 1070 (1)(4)(5) |
1100 3003 | 5356 (2)(4)(5) | 4043 (5)(7) | 5356 (2) | 5356 (2)(4)(5) | 4043 (2)(5) | 1100 (1)(4)(5) | 4145 (4)(5) | 4145 | 4043 (2)(5) | 1200 (1)(4)(5) | 1100 (1)(4)(5) | |
1200 | 5356 (2)(4)(5) | 4043 (5)(7) | 5356 (2) | 5356 (2)(4)(5) | 4043 (2)(5) | 1100 (1)(4)(5) | 4145 (4)(5) | 4145 | 1200 (1)(4) | 1200 (1)(4)(5) | ||
3004 | 5356 (2)(4) | 4043 (2) (3) (5)(7) | 5356 (2) | 5356 (2)(3)(4)(5) | 4043 (2)(3)(4)(5) | 5356 (2)(3)(4) | 4145 (4)(5) | 4145 | 5356 (2)(3)(4) | 1200 (1)(4)(5) | ||
2014 2017 | 4145 | 4145 | 4145 (8) | 4145 (8) | ||||||||
2219 | 4043 (5) | 4043 (5)(6) | 4043 (5) | 4043 (5) | 4043 (5)(6) | 2319 (4)(5)(6) | ||||||
5005 | 5356 (2)(3) | 4043 (2) (3) (5)(7) | 5356 (2) | 5356 (2)(3) | 5356 (2)(3)(4)(5) | 5356 (2)(3)(4)(5) | ||||||
5052 | 5356 (2)(3) | 4043 (2) (3) (5)(7) | 5356 (2) | 5356 (2)(3) | 5356 (2)(3)(4) | |||||||
5154 | 5356 (2)(3) | 5356 (2)(3)(4) | 5356 (2)(3) | 5356 (2)(3) | Remark:; (1) can adopt 1100 or 1200 (2) can adopt 5356.5556 or 5183; (3) can adopt 5654 or5554; (4) according to usage can adopt4043; (5) can adopt 4047; (6) can adopt 4145; (7) adopt 5356 when apears chromatic abberation after anodic process; (8) can adopt 2319 | |||||||
5086 5083 | 5356 (2) | 5356 (2) | 5356 (2) | |||||||||
6061 6063 | 5356 (2)(3) (4)(5) | 4043 (2) (3) (5) | ||||||||||
7003 | 5356 (2) |
Chalco aluminum welding wire products technical parameters and implementation standards
Chalco aluminum welding wire products weld mechanical properties (reference value) | |||
Alloy | Tensile strength (MPa) | Yield strength (MPa) | Elongation (%) |
4043 Weld | 170–190 | 90–110 | 6–10 |
5356 Weld | 250–280 | 110–130 | 11–18 |
4943 Weld | 230–260 | 130–150 | 10–14 |
5183 Weld | 270–300 | 130–160 | 10–16 |
5556 Weld | 280–310 | 150–180 | 8–12 |
The weld performance varies with the thickness of the base material, welding process and heat treatment status. The above are reference values for standard test plate tests. |
Aluminum Welding Wire Key Process Parameters Reference Table | |||||||
Welding Wire Model | Typical Diameter (mm) | Recommended Current Range (A) | Recommended Voltage Range (V) | Wire Feed Speed (m/min) | Shielding Gas | Welding Method | Main Application Areas |
ER4043 (Al-Si) | 0.8 / 1.0 / 1.2 | 90 - 180 | 18 - 22 | 4.5 - 9.0 | 100% Ar | MIG / TIG | Thin aluminum sheets, automotive, electronics |
ER5356 (Al-Mg) | 0.8 / 1.0 / 1.2 | 100 - 200 | 19 - 23 | 5.0 - 9.5 | 100% Ar or Ar+He mix | MIG / TIG | Marine equipment, corrosion-resistant structures |
ER5183 (Al-Mg) | 1.0 / 1.2 / 1.6 | 150 - 280 | 20 - 24 | 6.5 - 12.0 | 100% Ar or Ar+He mix | MIG / TIG | Shipbuilding, high-strength structures |
ER5556 (Al-Mg) | 1.0 / 1.2 | 120 - 220 | 19 - 23 | 5.5 - 10.0 | 100% Ar | MIG / TIG | Thick plate welding, pressure vessels |
ER1100 (Al-99.0%) | 0.8 / 1.0 | 70 - 140 | 17 - 21 | 3.5 - 7.5 | 100% Ar | MIG / TIG | General purpose aluminum welding |
Shielding Gas and Arc Transfer Modes Table | ||
Shielding Gas Type | Arc Transfer Mode | Description |
100% Ar | Pulsed Spray Transfer | Good weld appearance, suitable for thin plate welding |
Ar + 25% He | Spray Transfer | High heat input, suitable for thick plate and high-strength welding |
Ar + 5-10% CO₂ | Globular Transfer | Stable droplet transfer, high welding efficiency, wide applicability |
Packaging Specifications and Certifications Table | |
Packaging Specifications | Various options: 5 kg / 15 kg / 20 kg, etc. |
Product Standards | AWS A5.10 — American standard for aluminum alloy welding wire (ER series grades) |
ISO 18273 — International standard for aluminum welding filler materials (AlSi, AlMg naming) | |
GB/T 10858 — Chinese standard for aluminum and aluminum alloy welding wire | |
Documentation Support | COA, MSDS, ROHS, REACH, CE and other document support |
Customization Capability | Alloy composition adjustment and packaging customization available |
Chalco aluminum welding wire products implementation standards | |
AWS A5.10 | American standard aluminum alloy welding wire standard (ER series grade) |
ISO 18273 | International aluminum welding filler material standards (naming methods such as AlSi, AlMg, etc.) |
GB/T 10858 | China Aluminum and Aluminum Alloy Welding Wire Standards |
Can provide: COA, MSDS, ROHS, REACH, CE and other document support. |
Compatible Equipment, Typical Operating Parameters & Welding Methods
Chalco aluminum welding wires are engineered for superior performance across a range of welding processes, including MIG, TIG, pulse MIG, and high-speed welding. They are compatible with leading equipment systems such as Lincoln, Fronius, and Panasonic, ensuring stable performance in both manual and automated operations.
- MIG Welding: Our solid wires offer smooth feedability, low spatter, and excellent arc stability, making them ideal for manual and robotic MIG welding. Compatible with pure argon or argon-helium shielding gases.
- TIG Welding: Chalco wires feature consistent wire diameter and clean surface finish, enabling precise control and high-quality welds in automatic TIG wire feeding systems.
- Pulse MIG Welding: Our products perform well under pulsed current, delivering improved bead appearance, reduced heat distortion, and enhanced weld integrity.
- High-Speed Welding: Designed for high-efficiency production lines, Chalco aluminum wires support stable arc characteristics and consistent deposition rates at elevated travel speeds.
Welding method | Recommended welding wire type | Alloy Recommendation | Applicable instructions |
MIG welding | Aluminum solid wire (MIG Solid Wire) | 4043, 5356, 4943 | Mainstream configuration for conventional industrial applications, suitable for welding 6 series and 5 series aluminum alloys |
Automated MIG welding | High-precision solid welding wire (Robotic Grade Wire) | 4043, 4943, 5183 | It has higher requirements on welding wire consistency and is suitable for batch welding and welding robots. |
Flux core MIG welding | Flux-Cored Aluminum Wire | Special composite alloys (such as customized 4045 base) | A small amount of welding is used in a gas-free environment or in special locations. It is not a mainstream product. |
TIG automatic wire feeding system | Precision controlled wire feeding aluminum welding wire (for TIG automatic system) | 4043,5356 | Suitable for automatic TIG process, coiled aluminum wire can be used when there is a special control system |
SMAW manual welding | Non-wire products → Use aluminum welding rod/Stick Electrode | E4043, E5356, etc. |
Typical operating parameters (for groovewelding) | |||||||
Base Metal Thickness (mm) | Welding Position | Weld Spacing (mm) | Welding Pass | Wire Diameter (mm) | Current (A) | Voltage (V) | Argon Flow (cfh) |
1.6 | F | None | 1 | 0.8 | 70-110 | 15-20 | 25 |
1.6 | F | 2.4 | 1 | 0.8 | 70-110 | 15-20 | 25 |
2.4 | F, V, H, O | None | 1 | 0.8-1.2 | 90-150 | 18-22 | 30 |
2.4 | F, V, H, O | 3.2 | 1 | 0.8-1.2 | 110-130 | 18-22 | 30 |
3.2 | F, V, H | 0-2.4 | 1 | 0.8-1.2 | 120-150 | 20-24 | 30 |
3.2 | F, V, H, O | 3-16 | 1 | 0.8-1.2 | 110-135 | 19-23 | 30 |
5 | F, V, H | 0-1.6 | 1F, 1R | 0.8-1.2 | 130-175 | 22-26 | 35 |
5 | F, V, H | 0-1.6 | 1 | 1.2 | 140-180 | 23-27 | 35 |
5 | O | 0-1.6 | 2F | 1.2 | 170-175 | 23-27 | 60 |
5 | F, V | 2.4-5 | 2 | 1.2-1.6 | 140-185 | 23-27 | 35 |
5 | H, O | 5 | 3 | 1.2 | 130-175 | 23-27 | 60 |
6.5 | F | 0-2.4 | 1F, 1R | 1.2-1.6 | 175-200 | 24-28 | 40 |
6.5 | F | 0-2.4 | 2 | 1.2-1.6 | 185-225 | 24-29 | 40 |
6.5 | V, H | 0-2.4 | 3F, 1R | 1.2 | 165-190 | 25-29 | 45 |
6.5 | O | 0-2.4 | 3F, 1R | 1.2 | 180-200 | 25-29 | 70 |
6.5 | F, V | 3.2-6.5 | 2-3 | 1.2-1.6 | 175-225 | 25-29 | 60 |
6.5 | O, H | 1-4 | 4-6 | 1.2-1.6 | 170-200 | 25-29 | 60 |
10 | F | 0-2.4 | 1F, 1R | 1.6 | 225-290 | 26-29 | 50 |
10 | F | 0-2.4 | 2F, 1R | 1.6 | 210-275 | 26-29 | 50 |
10 | V, H | 0-2.4 | 3F, 1R | 1.6 | 190-220 | 26-29 | 55 |
10 | O | 0-2.4 | 6F, 1R | 1.6 | 200-250 | 26-29 | 80 |
10 | F, V | 6.5-10 | 1 | 1.6 | 210-290 | 26-29 | 50 |
10 | O, H | 10 | 8-10 | 1.6 | 190-260 | 26-29 | 80 |
20 | V, H, O | 0-1.6 | 8F, 1R | 1.6 | 240-300 | 26-30 | 80 |
20 | F | 0-1.6 | 3F, 1R | 1.6 | 270-330 | 26-30 | 80 |
20 | V, H, O | 0-1.6 | 6F, 0R | 1.6 | 230-280 | 26-30 | 80 |
F = Flat Position V = Vertical Position H = Horizontal Position O = Overhead Position For 5XXX series welding wires, select the highest and lowest current and voltage specified; For 1XXX and 4XXX series welding wires, select the lower current and higher voltage. |
Typical operating parameters (for fillet welding and lap welding) | |||||||
Base Metal Thickness (mm) | Welding Position (1) | Weld Pass | Electrode Diameter (mm) | Direct Current (2) (A) | Arc Voltage (2) (V) | Argon Flow Rate (cfh) | Welding Speed (ipm/pass) |
2.4 | F, V, H, O | 1 | 0.8 | 100-130 | 18-22 | 30 | 24-30 |
3.2 | F | 1 | 0.8-1.2 | 125-150 | 20-24 | 30 | 24-30 |
3.2 | V, H | 1 | 0.8 | 110-130 | 19-23 | 30 | 24-30 |
3.2 | O | 1 | 0.8-1.2 | 115-140 | 20-24 | 40 | 24-30 |
5 | F | 1 | 1.2 | 180-210 | 22-26 | 30 | 24-30 |
5 | V, H | 1 | 0.8-1.2 | 130-175 | 21-25 | 35 | 24-30 |
5 | O | 1 | 0.8-1.2 | 130-190 | 22-28 | 45 | 24-30 |
6.5 | F | 1 | 1.2-1.6 | 170-240 | 24-28 | 40 | 24-30 |
6.5 | V, H | 1 | 1.2 | 170-210 | 23-27 | 45 | 24-30 |
6.5 | O | 1 | 1.2-1.6 | 190-220 | 24-28 | 60 | 25-30 |
10 | F | 1 | 1.6 | 240-300 | 26-29 | 50 | 18-25 |
10 | V, H | 3 | 1.6 | 190-240 | 24-27 | 50 | 24-30 |
10 | O | 3 | 1.6 | 200-240 | 25-28 | 85 | 24-30 |
20 | H, V | 4-6 | 1.6 | 260-310 | 25-20 | 70 | 24-30 |
20 | O | 10 | 1.6 | 275-310 | 25-29 | 85 | 24-30 |
F = Flat Position V = Vertical Position H = Horizontal Position O = Overhead Position For 5XXX series welding wires, select the highest and lowest current and voltage specified; For 1XXX and 4XXX series welding wires, select the lower current and higher voltage. |
Chalco's technical team can provide one-to-one alloy recommendation services and welding process support based on your base metal composition, welding equipment and process requirements. In addition, Chalco provides alloy customization and technical consultation to help customers optimize welding results based on base metal type, welding method, and equipment setup.
Instant QuoteChalco aluminum welding wire application industry and cooperation field
Chalco aluminum welding wire is widely used in many high-precision and high-strength welding industries, covering transportation, energy equipment, structural manufacturing, precision electronics and other fields. With high-quality alloy ratio, stable dimensional control and large-scale supply capabilities, we have provided welding wire materials and supporting technical services to many global customers.
Automobile manufacturing: used for MIG process scenarios such as body structure welding, battery trays, aluminum wheels, cooling modules, etc., compatible with manual and automatic welding lines.
Rail transit: Applied to the welding of high-strength aluminum structures such as the main frame of the vehicle body, supporting structure, chassis connectors, etc., meeting the requirements of lightweight and durability.
Shipbuilding and offshore equipment: welding of hulls, bulkheads, decks and aluminum alloy truss structures, using highly corrosion-resistant welding wire alloys such as 5183/5356.
Building and industrial structures: Applied to various structural parts such as aluminum brackets, railings, curtain wall systems, casings, etc., taking into account both appearance and structural performance.
New energy and energy storage systems: such as electric vehicle battery boxes, battery trays, heat exchangers, electric drive modules and other MIG automatic welding structures.
General industrial equipment manufacturing: Suitable for aluminum welding and repair operations such as conveying systems, mechanical frames, and equipment connection systems.
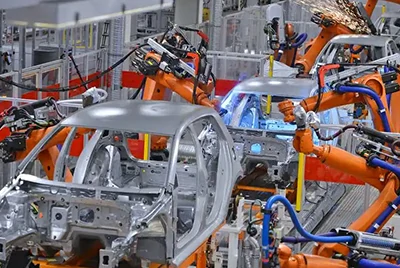
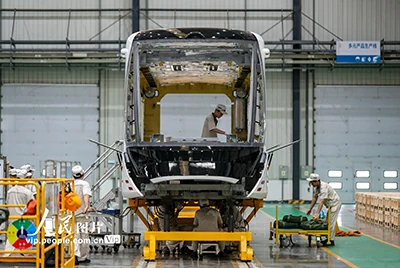
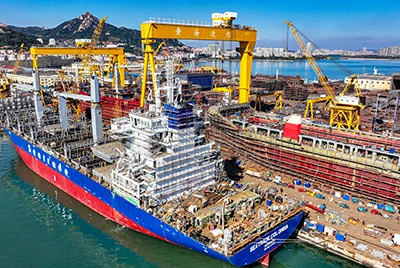
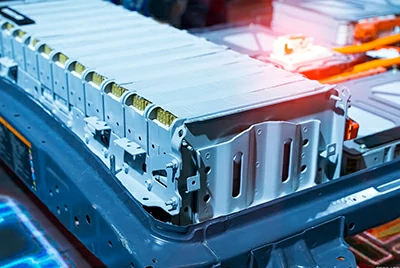
Core advantages of Chalco aluminum welding wires
- Uniform alloy composition ensures consistent weld strength and corrosion resistance.
- Tight wire diameter control guarantees stable feeding and welding accuracy.
- Neat, tangle-free coiling supports high-speed robotic welding.
- Multiple packaging options fit manual, automatic, and robotic welding systems.
- Full range of alloy choices including 4043, 5356, 4943, 5183, and 5556.
- Export-ready with fast customs clearance and global delivery support.
Why choose Chalco as your aluminum welding wire supplier
- Complete in-house manufacturing ensures batch consistency and stable product performance.
- Precision wire drawing from 9.5mm rod to below 0.8mm fits both manual and automated MIG systems.
- Advanced surface treatment with online lubrication, degreasing, and anti-tangle coiling.
- Supports alloy customization with tight diameter control up to ±0.02mm tolerance.
- Wide packaging options from 0.5kg to 250kg to suit various welding setups.
- Full certification support including COA, MSDS, RoHS, and REACH for global compliance.
Chalco not only provide high-quality aluminum welding wire, but also are committed to creating a one-stop welding project solution for you, including aluminum welding wire (Welding Wire), aluminum filler rod (Filler Rod), aluminum welding rod (Stick Welding Rod) and welding technical support, to comprehensively improve your welding efficiency, structural reliability and engineering delivery guarantee.
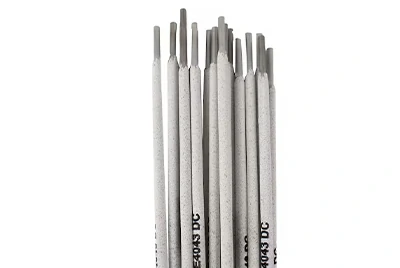
Aluminum welding wire purchasing suggestions and FAQs
What is the difference between welding wire, welding rod and filler rod? Can they be used interchangeably?
Among aluminum welding materials, welding wire, stick welding rod and filler rod have similar appearances, but their uses, structures and processes are completely different and cannot be directly interchanged:
Name | Whether it comes with a medicated skin | How to use | Is it conductive? | Typical Applications |
Welding Wire | ❌No drug skin | Automatic wire feeding system (MIG/TIG) | ✅ | Industrial structure welding, high efficiency and continuous operation |
Stick Welding Rod | ✅With medicated skin | Manual Metal Arc Welding (SMAW) | ✅ | Maintenance/field construction, where gas is not available |
Filler Rod | ❌No drug skin | Manual wire feeding for TIG welding | ❌ | Precision welding, thin plates, small parts butt joint |
For other brazing welding product needs, please click [Aluminum filler rod][Aluminum brazing material] to view product details
Which welding wire alloy is suitable for welding 6061 aluminum alloy?
Commonly recommended are ER4043 (AlSi5) or upgraded version 4943. If higher strength requirements are required or heat treatment is required after welding, 4943 is recommended.
Which welding wire should I choose when welding 5083 or 5052?
ER5356 is recommended; if the structure is subject to heavy loads or is in a marine/highly corrosive environment, ER5183 or ER5556 may be selected.
How to choose welding wire diameter?
Usually selected according to the thickness of the parent material:
- <3mm: Use 0.8mm or 1.0mm
- 3–6mm: Use 1.2mm
- 6mm or thick plate welding: When using 1.6mm automatic welding/robot welding, it is recommended to use precision-wound large-diameter stable welding wire.
What wire packaging specifications does Chalco support?
Support 0.5kg / 1kg / 2kg / 5kg / 7kg / 15kg / 20kg / 250kg barrels. The reels can be made of plastic shaft, steel shaft or customized core.
Can you provide technical documents such as COA, MSDS, ROHS, etc.?
Yes. All welding wire products can be shipped with:
- COA (Composition Analysis)
- MSDS (Safety Data Sheet)
- RoHS/REACH (Environmental Compliance)
- Third-party test report (on demand)
Which wire feeders are compatible with Chalco aluminum welding wire?
- Universal MIG welding wire feeding system (Lincoln, Fronius, ESAB, OTC, etc.)
- Automated welding workstation, robotic welding arm
- TIG welding machine with wire feed module
Can you customize special alloys or wire specifications?
Of course. Chalco provides customized alloy development services, including composition fine-tuning, special ratios, composite structures, and non-standard wire diameter customization, supporting sample verification and batch supply.
If you have further questions about alloy matching, equipment adaptation or welding process, please contact our technical team and we will provide you with quick response and material recommendations.
Chalco can provide you the most comprehensive inventory of aluminum products and can also supply you customized products. Precise quotation will be provided within 24 hours.
Get a quote