Aluminum foil is not only a kitchen product, but is also widely used in key areas such as packaging, thermal management and industrial protection. There are many terms in the market, such as "ultra-thin aluminum foil", "flexible aluminum foil", "household foil", "heavy-duty foil", "lunch box foil", "hydrophilic foil", "composite foil", etc., which often confuse users.
This article uses thickness as the core dimension to construct a systematic aluminum foil classification framework, covering ultra-thin foils below 9 μm (thinnest 4.5μm) to structural thick foils above 100 μm. We will analyze representative products, typical applications, and common surface/composite treatments one by one to help engineers, purchasers, and product designers make accurate selections.
- Ultra-Thin Foil (4.5–9 μm)
- Flexible Foil (10–20 μm)
- Ultra-Thick Foil (81–200 μm)
- Laminated Foil (Multi-Layer Composite Structures)
- Chalco capacity for aluminum foil providing
Ultra-thin aluminum foil (4.5–9 μm)
Ultra-thin aluminum foil usually refers to aluminum foil products with a thickness in the range of 6-9 microns (0.006-0.009 mm). It has extremely high flexibility, light weight and excellent ductility, and is widely used in high-barrier flexible packaging, precision packaging and multi-layer composite structures.
Chalco has advanced ultra-thin foil rolling technology and has successfully developed ultra-thin aluminum foil with a thickness as low as 0.0045 mm, refreshing the industry's manufacturing limits and meeting the needs of extreme lightweight and high-precision packaging.
This type of product usually uses soft pure aluminum alloys such as 1235-O, 8079-O, 8011-O, etc., and has excellent composite properties, printability and die-cutting processing performance. It is an ideal substrate for high-end packaging and functional film materials.
PTP foil | 6–7 μm
Specially used for the blister structure of pharmaceutical tablets, it has good moisture-proof, oxygen-proof and light-proof properties to ensure stable drug efficacy.
It is often used in conjunction with PVC/PP heat seals for heat seal adhesive coating and dry composite processing, and is suitable for high-speed pharmaceutical packaging lines.
Cigarette inner liner | 6–9 μm
Used for the inner lining of cigarette packaging, compounded with paper to enhance air tightness and aroma retention, and improve the high-end packaging texture.
Common treatments include printing, varnish, corona treatment or hydrophilic layer, suitable for high-speed die-cutting and embossing processes.
Candy / Tea wrapping foil | 7–9 μm
Used for wrapping candies, tea bags, chocolates and other foods. It has good flexibility and formability and is easy to fold and fit.
It supports color printing, moisture-proof lamination, punching and pre-cutting, and is suitable for personalized packaging and automated processing.
Foil paper wrapping film | 8–9 μm
As the outer structure of wine bottle caps, label sleeves, etc., it combines the barrier properties of aluminum foil and the stiffness of paper.
It is often compounded with kraft paper or cardboard, and can be subjected to surface treatments such as varnish, corona, hot stamping, embossing, etc.
Lamination foil layer | 8–9 μm
As the aluminum layer in PET/PE and other film structures, it improves barrier properties, light-shielding properties and heat-sealing properties.
Widely used in roll film, sealing film, tape lining, supporting glue coating, corona treatment and anti-static treatment.
Ultra-thin foil for brazing / Brazing laminate foil
Some ultra-thin aluminum foils can be compounded with 4343/7072 alloys as aluminum brazing structural materials for heat exchangers, ensuring welding quality and thermal conductivity.
Widely used in heat exchange systems of passenger cars, commercial vehicles and engineering machinery.
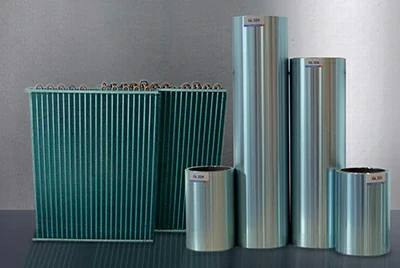
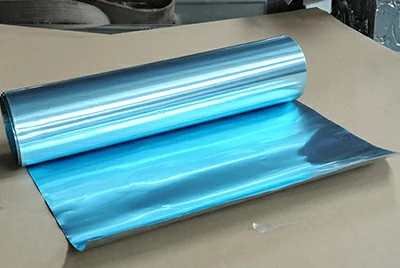
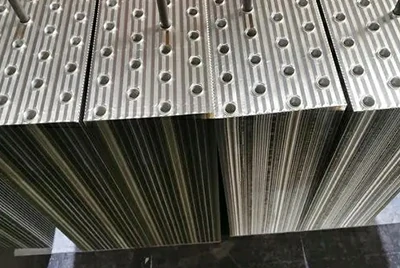
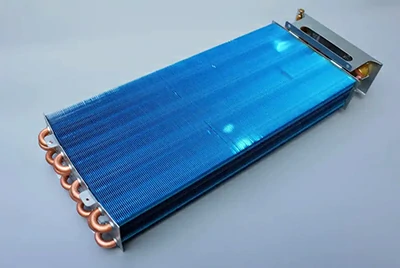
Flexible aluminum foil (10–20 μm)
Flexible aluminum foil is a medium-thin aluminum foil with a thickness between 10-20 microns (μm). It has good ductility, wrapping and processing compatibility. It is the main product in food packaging, pharmaceutical packaging, household baking and industrial lamination structures.
This type of foil is usually made of pure aluminum such as 1235, 8011, 8079 or soft alloys (O/H18 and other tempers). It supports a variety of coil and die-cut forms and is suitable for high-speed lamination, heat sealing and printing processes.
It is widely used in flexible composite films, brazing structural parts, aluminum foil lunch box covers and daily aluminum products. It is the thickness range with the largest output and the widest demand in the aluminum foil industry.
Household aluminum foil | 10–15 μm
It is widely used in household scenarios such as kitchen baking, food preservation, heating and packaging, and has good thermal conductivity and formability.
It supports embossing, oil-proof and anti-sticking treatments, and can be made into stretch sheets, cut rolls, folding boxes and other forms.
Food-grade packaging foil | 11–18 μm
Used for mid-to-high-end packaging of cooked food, dairy products, cakes, etc., providing reliable water vapor and grease isolation protection.
It is often used for color printing and composite paper/PET/PE layer processing, and is suitable for automatic heat sealing and roll film packaging lines.
Pharmaceutical blister or strip foil | 13–20 μm
It is suitable for the packaging of tablets, powders and granules, meeting the medical requirements of non-toxicity, barrier and moisture-proof.
The surface can be processed into a printed layer, heat sealant pre-coated or anodized coating, and is compatible with a variety of sealing materials.
Aluminum foil sealing film/ cover foil | 12–18 μm
As the sealing layer of lunch boxes, beverage bottles, yogurt cups, etc., it has the properties of easy tearing, oil resistance and heat sealing.
Supports punching, pattern embossing, PE/PP heat sealing layer lamination, and can achieve peelable structure.
Printed decorative foil | 12–16 μm
It is suitable for scenes such as chocolate, moon cakes, and gift box packaging, and has both packaging functions and decorative visual effects.
It can perform pattern processing such as gold and silver printing, electrochemical aluminum treatment, varnish/matte layer coating, etc.
Air conditioner foil
Air conditioner foil is mainly composed of alloys such as 8011-O and 1100-O, the thickness is usually 0.09-0.15 mm, with strong flexibility, good ductility and excellent thermal conductivity.
It is commonly used in the manufacture of fins for air-conditioning heat exchangers (Evaporator/Condenser), and can be treated with hydrophilic/hydrophobic/anti-corrosion coatings.
Suitable for heat exchange devices such as HVAC systems, car air conditioners, refrigerator condensers, etc.
Flexible brazing foil
Flexible brazing foil is often used as the middle layer aluminum foil of multi-layer brazing composite structure (such as 7072/4343 alloy composite structure), which needs to have excellent weldability and rolling accuracy.
It is used in brazing processes such as plate-fin heat exchangers, automobile cooling systems, and air-conditioning pipeline headers.
Suitable for automatic lamination, continuous welding and vacuum brazing processes.
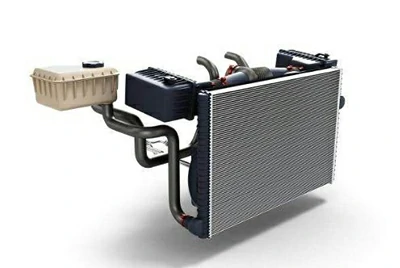
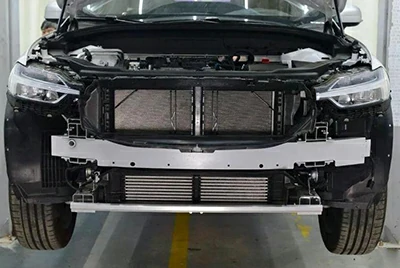
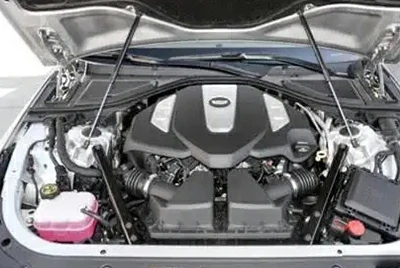
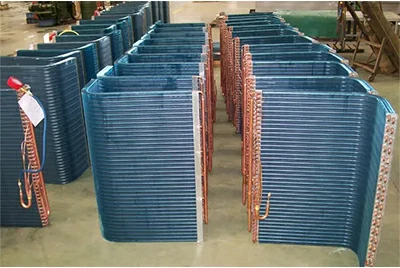
Heavy-duty aluminum foil (26–40 μm)
Heavy-duty aluminum foil generally refers to medium-thick aluminum foil with a thickness ranging from 26–40 microns (μm). It has higher tear resistance, support and forming stability, and is suitable for load-bearing, pressure-resistant, high-temperature protection and industrial structure applications.
Common alloys of this thickness level include 8011, 3003, 1235, 5052, etc., and the states include O, H18, H24, etc. Anodic, electrophoretic, embossing, and anti-sticking treatments can be performed according to the application.
It is widely used in baking trays, lunch box covers, barbecue packaging, industrial linings, automotive/thermal management structures and composite insulation systems, which can meet the deformation requirements and have basic structural strength.
Heavy-duty household foil | 26–30 μm
High-strength baking, grilling, and refrigeration packaging for home/commercial kitchens that resists tearing and breakage.
It supports anti-stick, embossing and re-rolling processing, and is suitable for heating in multiple scenarios such as microwave and oven.
Aluminum container foil | 30–35 μm
Aluminum container foil is used for disposable lunch boxes and food trays, it has the characteristics of good rigidity, strong formability and fast thermal conductivity.
It can be heat-sealed and anodized, and is suitable for standardized batch usage scenarios such as airline meals and fast food chain packaging.
Heat-seal lid foil
The common thickness of heat seal lid foil is 30-40 μm, with a coating layer structure, which can be heat-sealed with PP, PE, and PET cup bodies.
Suitable for yogurt lids, food box seals, aluminum-plastic sealing films for medical powders, etc. Supports embossing and anti-tear treatment.
Industrial heavy packaging foil | 30–40 μm
Used in industrial occasions such as high-strength article wrapping, transportation protection, and building structure lining.
It supports embossing, oil-proof, anti-corrosion coating and other treatments, and is suitable for large equipment packaging or engineering composite materials.
Aluminum foil for automotive heat barrier | 30–40 μm
Used in thermal management structures such as engine hoods, battery bottoms, exhaust systems, etc., with excellent heat reflectivity and corrosion resistance.
It supports composite glass fiber cloth, hot-pressed foam, and fire-retardant coating, and is the key aluminum layer in the multi-layer structure.
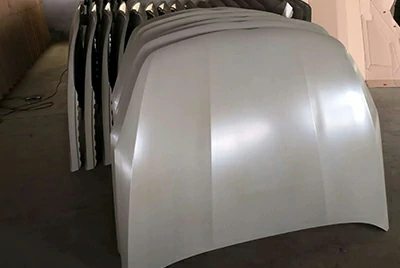
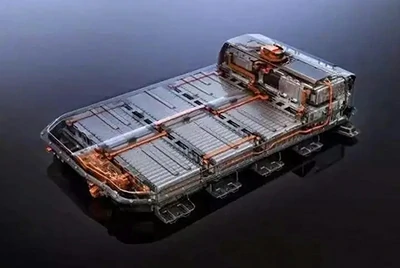
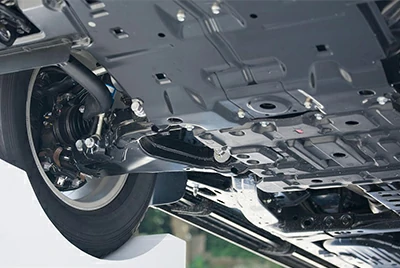
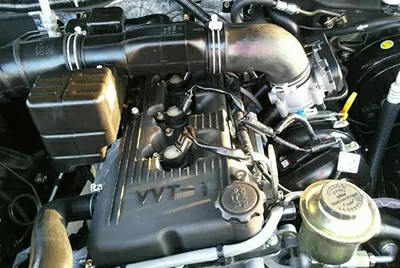
Ultra-Thick Aluminum Foil (81–200 μm)
Ultra-thick aluminum foil refers to high-strength structural aluminum foil with a thickness of more than 81 μm (up to 200 μm), which has excellent compression resistance, support, heat resistance and barrier properties. This type of product has gone beyond the scope of conventional aluminum foil and is widely used in structural composites, industrial equipment coatings, thermal management systems, building fire protection and military equipment.
Commonly used alloys include 3003, 8011, 1100, 5052, 1060, 8011A, etc., supporting O, H18, H24, H22 and other states. Anodizing, coating, and fire retardant treatment can be performed as needed. Some products have entered the field of aluminum strips or foils.
Heat reflective/insulating foil | 100–200 μm
Heat reflective or insulation foil is used in thermal shielding systems for automobiles, rail transit and industrial equipment, with high reflectivity and high temperature resistance.
It is often compounded with glass fiber cloth and foam layer, and supports anode, electrophoresis and fire retardant coating treatment.
Structural laminate foil | 100–150 μm
Structural laminated foil is used as the core aluminum layer in multi-layer composite materials to provide rigidity and structural support, such as honeycomb aluminum foil core material.
It is widely used in building insulation boards, aviation lightweight panels, and bulkhead composite structures, and supports punching, gluing, and anodizing.
EMI/RFI electromagnetic shielding foil | 81–120 μm
It is used as a conductive and anti-interference functional layer in the fields of communications, electronics, and electricity.
Supports anti-static, conductive film composite, and carbon black coating treatments to meet the protection needs of sensitive equipment.
Industrial wrapping foil | 90–150 μm
Suitable for large machinery and equipment, cable/pipeline covering, with corrosion resistance, tear resistance and weather resistance.
It supports treatments such as gluing, oil-resistant and moisture-proof coatings, and can be supplied in rolls or sheets.
Structural brazing foil
Structural brazing foil is used for brazing of industrial plate heat exchangers or heavy-duty thermal structures, thickness is typically 100–150 μm.
Combining 7072 cladding with 3003 core material can achieve high strength brazing connection.
It is typically used in engineering machinery, industrial refrigeration, energy equipment and other industries.
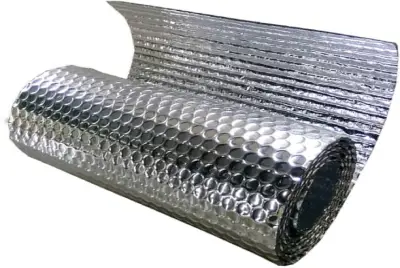
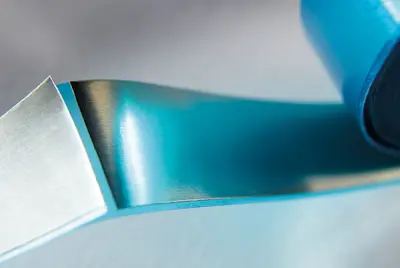
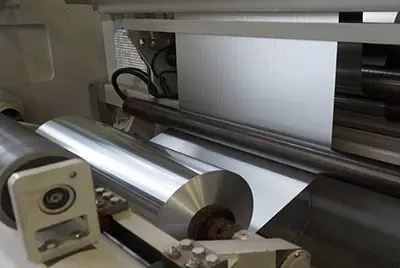
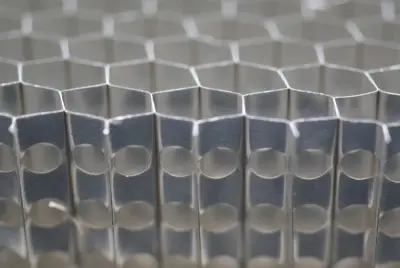
Laminated aluminum foil
Multilayer composite aluminum foil is a structural functional material formed by thermal compounding, gluing or co-extrusion lamination with plastic film, foam, paper, glass fiber cloth and other materials using aluminum foil as the base material. It has excellent barrier properties, mechanical strength, heat sealing properties and processing adaptability, and is widely used in high-performance application scenarios such as industrial packaging, thermal management systems, electronic EMI protection, and building insulation.
Chalco supports aluminum foil thickness of 6-50 μm, and the total composite thickness can reach 2.0 mm. It can customize a variety of structural stacking and provide multiple delivery forms such as rolls, sheets and die-cut parts.
Aluminum + PET/BOPP laminated foil
Compounding aluminum foil with PET, BOPP and other film materials is suitable for food packaging, label film, heat-sealing gasket, etc.
It has the characteristics of strong barrier properties, good printability, high heat-sealing compatibility, and supports anti-static, oil-proof and moisture-proof treatment.
Aluminum + foam laminated foil
Composited with PE/XPE foam layer, it is used for building insulation, car thermal management, air conditioning ducts, etc.
It provides light weight, flexibility, heat insulation and reflective properties, and supports processing methods such as cutting, punching, and hot pressing.
Aluminum + paper laminated foil
Thermally laminated with kraft paper or white cardboard, used for sealing film, outer packaging, label backing and other structures.
It combines stiffness, beauty and environmental protection, and is suitable for printing, corona, coating, die-cutting and other processes.
Aluminum + bubble or foam sheet
It is made of double-layer bubble film or EPE foam sheet for cold chain packaging, roof reflective film, and transportation buffer layer.
It has functions such as high reflection, buffering and energy absorption, pressure resistance and folding resistance, and supports customized thickness and multi-layer structure.
Aluminum + glass fiber/woven fabric
Compounded with glass fiber cloth or woven cloth, it is widely used in industrial flame retardant cloth, cable sheath, fire curtain, etc.
It has high temperature resistance, flame retardancy, tear resistance and UV resistance, and is suitable for protective layers in complex environments.
Multi-layer laminated foil
It can combine PET + aluminum + foam / paper / heat seal layer and other three-layer or multi-layer structures for multifunctional composite materials.
It meets the integrated requirements of barrier + buffer + heat sealing + printing, and is suitable for highly integrated systems such as electronics, cables, and construction.
Holographic laminated foil
The aluminum foil is thermally laminated with the holographic PET film, and the surface presents a dynamic grating pattern, which has good decorative and anti-counterfeiting effects.
It is often used in high-end candy packaging, gift box covers, cigarette labels and other fields, and can be customized with a variety of patterns and optical effects.
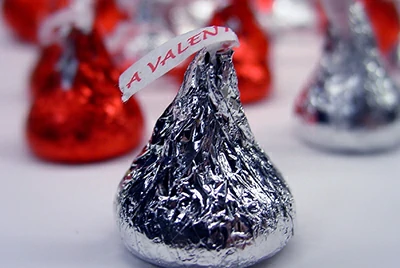
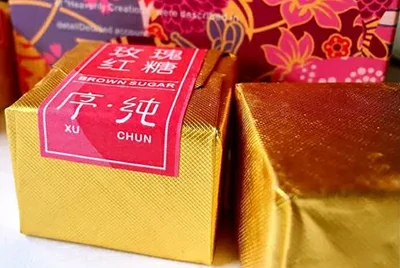
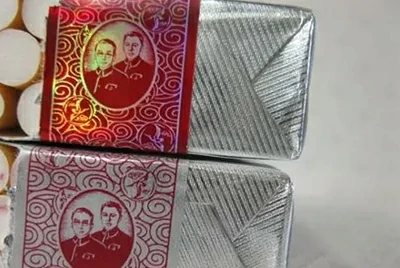
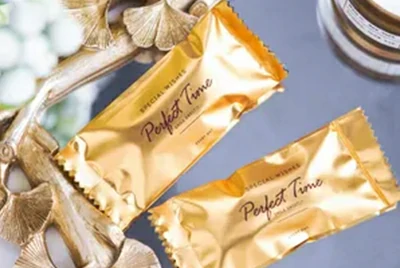
Chalco aluminum foil production and customization capabilities
Chalco has the full-process aluminum foil manufacturing capability covering aluminum ingot casting → hot rolling → cold rolling → foil rolling → surface treatment → multi-layer composite → precision cutting, which can meet the different performance and application requirements from ultra-thin packaging foil to structural composite foil. We can provide customized structural design, stable batch delivery and various packaging forms according to customer project requirements, and widely serve the fields of food, medicine, thermal management, construction, electronics, industrial protection, etc.
Adaptation alloy and temper
- Pure aluminum series: 1100, 1145, 1235, 1350
- For packaging/container: 8011, 8079, 8006
- Function/Structure: 3003, 5052, 8011A, 1060, 4343, 7072
- Temper support: O, H14, H18, H22, H24, H26 and other soft and hard states and coated brazing layer structure
Thickness range and production capacity advantages
Aluminum foil thickness range: 6 μm – 200 μm
Multilayer composite structure: total thickness up to 2.0 mm
Wide width capability: conventional width 200 – 1500 mm
Ultra-wide foil roll capacity: supports continuous production of wide coils up to 1850 mm and above, suitable for high-speed coating lines and large-format lamination applications.
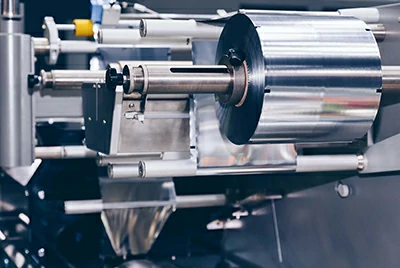
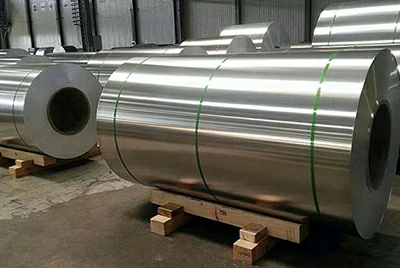
Surface treatment and special processes
- Anodizing/ Electrophoretic coating/ Corona treatment/ Degreasing and cleaning
- Color printing/ hot stamping/ embossing/ spraying/ varnish treatment
- Bright Finish: Highly reflective aluminum foil, suitable for labels, candy packaging, wine packaging, visual enhancement purposes
- Holographic Lamination: supports thermal lamination of aluminum foil and patterned holographic film to achieve dynamic light effects and anti-counterfeiting functions
- Hydrophilic/hydrophobic/anti-corrosion coating: suitable for the use of air conditioning fin foil and structural protection foil
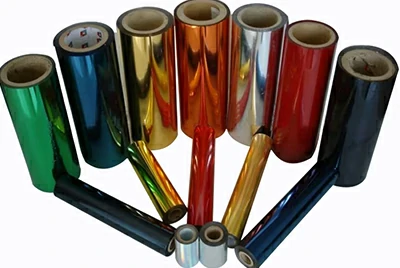
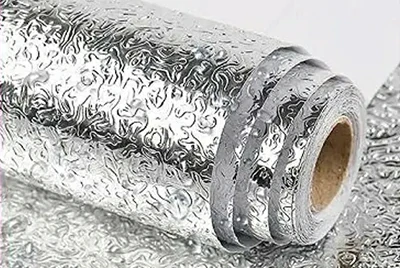
Multi-layer composite and structural processing capabilities
Dry lamination, heat seal lamination, adhesive lamination, self-adhesive layer, fireproof film, foam layer, kraft paper and other structural combinations
Can form double-layer/tri-layer/quintuple-layer/multi-layer structured foils to meet comprehensive performance requirements such as barrier properties + support properties + heat sealing properties + appearance
Common structures: Al + PET/BOPP, Al + Paper, Al + Foam, Al + Fiberglass, Al + Hot-seal Film, etc.
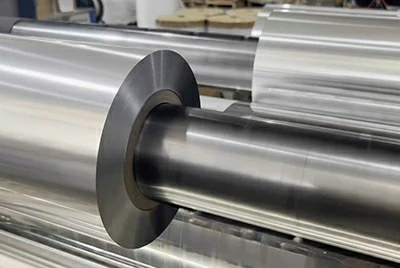
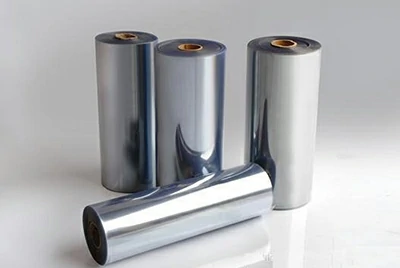
Precision slitting and delivery form
Support multiple delivery methods such as roll material/cut-to-length pieces/die-cut parts/punched films
Cutting error control: ±0.5 mm
Pre-processing support: punching, embossing, anti-sticking, anti-static, etc.
Packaging: Anti-oxidation vacuum packaging + moisture-proof film + corrugated box / export wooden box, suitable for international transportation and automated factory loading
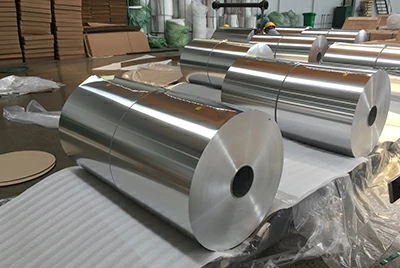
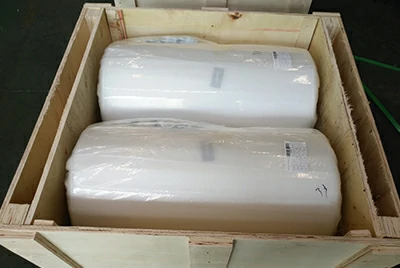