Forgings play a vital role in engines, gearboxes, chassis, and suspensions, offering superior strength, dimensional stability, and fatigue resistance—especially for new energy and high-performance vehicles. Compared to castings and welds, forgings ensure higher reliability under high-speed, high-torque conditions.
Chalco specializes in aluminum, titanium, and steel forgings, offering full-process services from free/die forging to CNC finishing, supporting custom parts like crankshafts, flanges, and drive shafts.
Engine system forging application—— high thermal strength and precision connection of power core support
As the vehicle's "heart, ” engine components face high temperatures, pressure, and require fatigue resistance, thermal stability, and corrosion resistance. Forgings are ideal for key support, sealing, and transmission parts due to their strength and structural integrity.
Contact us now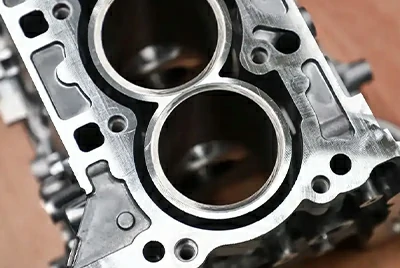
Chalco excels in precision forging, offering free forging, die forging, and closed die forging processes combined with advanced heat treatment and ±0.05mm CNC machining. These capabilities enable us to meet the stringent demands of powertrain systems for lightweight design, high strength, and thermal stability. Our aluminum and titanium forgings are trusted by leading manufacturers across gasoline, diesel, and hybrid platforms worldwide.
Based on extensive application experience and proven performance, Chalco is proud to recommend the following alloy grades and solutions for this field:
- 2618-T6
- 2219-T87
- 6061-T651
- 7075-T73
- 2024-T4
- 4032-T6
- Ti-6Al-4V (TC4)
- Ti-6242
- Gr.2 (TA2)
Application module | Typical forging parts | Functional description |
Cylinder system | Cylinder liner reinforcement ring, cylinder body connection flange, main bearing cap forging | Ensure high temperature and high pressure sealing and structural rigidity |
Crankshaft system | Crankshaft forging blanks, balance block forgings | Provides power output to the rotating core |
Piston connecting rod assembly | Connecting rod forgings, piston pin seat, small end bushing support ring | Withstand reciprocating impact loads to ensure high-frequency stability |
Valve system | Valve spring seat, rocker arm forging, camshaft support | Precisely control the air flow, wear-resistant and heat-resistant |
Turbocharger system | Turbine casing connecting ring, rotor support shaft, boost channel connecting forgings | Improve air intake efficiency and adapt to high temperature and high-pressure environment |
Other auxiliary structures | Water pump bearing ring, oil pump drive shaft, engine front cover connecting flange | Supports precise operation of engine auxiliary subsystems |
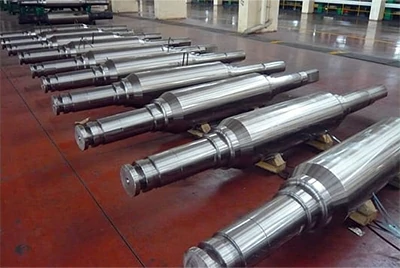
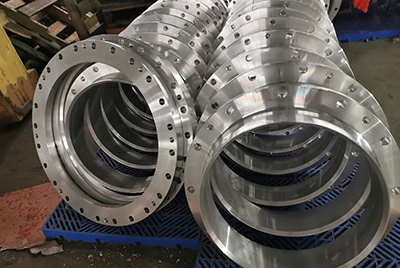
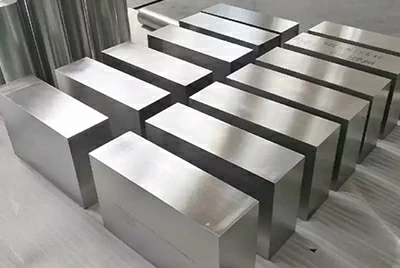
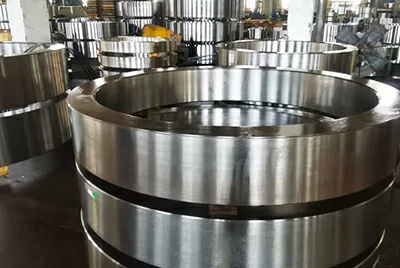
Drive system forgings – engineered for high-speed transmission and torque impact
Modern vehicles demand greater reliability and efficiency from transmissions and drive systems. Key components like automatic transmission gears and electric drive shafts face high torque, impact loads, and frequent speed changes, requiring excellent material strength, dimensional accuracy, and heat treatment quality.
Contact us now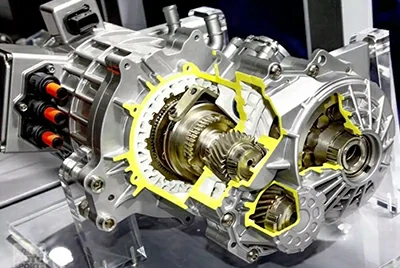
Chalco provides high-strength forging solutions for drive systems, covering aluminum alloy lightweight drive shafts to titanium alloy connection flanges. We can free forge shafts up to Ø2100mm and 12m long, using processes like toothed pre-forging, spiral flange structures, and hollow shaft forging. These capabilities ensure high performance, consistency, and adaptability for diverse applications.
Based on proven experience and customer needs, Chalco recommends the following alloy grades and solutions for this field:
- 7075-T73
- 2024-T6
- 6061-T651
- 6082-T6
- 7050-T7451
- 2014-T6
- Ti-6Al-4V (TC4)
- TA2 (Gr.2)
- Ti-6Al-2Sn-4Zr-2Mo
Application module | Typical forging parts | Functional description |
Automatic/manual transmission system | Planetary gear shaft, synchronizer ring forgings | Precise transmission and wear adaptation under high speed load |
Differential and main reduction gear | Differential case forgings, spindle gear connecting shaft | High torque load, low noise operation, high tooth line consistency requirements |
Drive axle and half shaft system | Hollow half-shaft forgings, flange output shaft | Withstand torsional impact, high requirements for lightweight design, complex structure |
Electric drive axle system | Motor output shaft, gear transition connecting ring | Stable structural support in high-speed rotation and high-efficiency transmission systems |
Coupling and transmission middle section structure | Universal joint connection forging block, middle section connection ring | Flexible connection solutions for different displacement angles and impact loads |
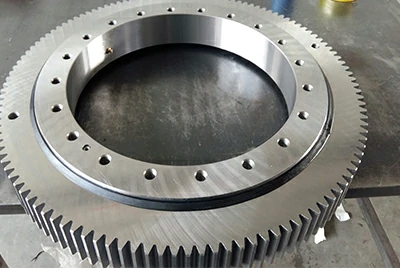
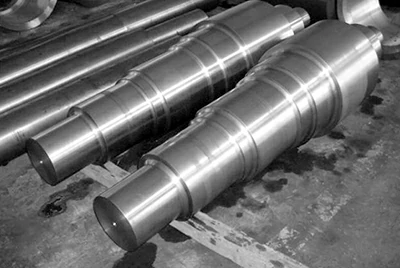
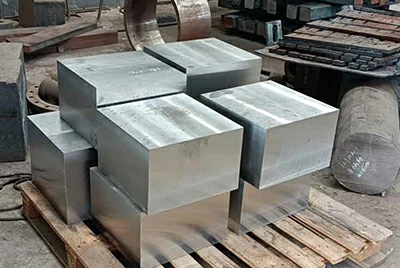
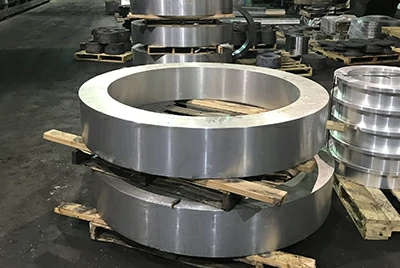
Chassis and suspension system forging applications — forging solutions that support rigidity and dynamic response
The chassis and suspension connect the vehicle to the road, requiring strength, toughness, and lightness. Forgings are essential, especially in high-performance, commercial, and off-road vehicles, where control arms, flanges, and shock absorber supports demand superior fatigue life and impact resistance.
Contact us now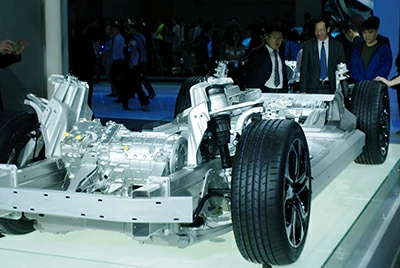
Chalco provides precision forging solutions using aluminum and titanium alloys, supporting the development and mass production of complex curved control arms, thin-walled structural parts, and large support shafts. Our expertise helps customers enhance both vehicle handling and structural reliability.
Based on extensive experience and application needs, Chalco recommends the following alloy grades and solutions for this segment:
- 7075-T6
- 6061-T651
- 2024-T4
- 6082-T6
- 7475-T61
- 2014-T6
- Ti-6Al-4V (TC4)
- TA2 (Gr.2)
- Ti-6Al-2Sn-4Zr-2Mo
Application module | Typical forging parts | Functional description |
Front/Rear Suspension System | Upper and lower control arm forgings, shock tower connector | Ensure suspension geometry rigidity, absorb impact, and improve handling performance |
Axle connection system | Connecting flange, steering knuckle support ring | Ensure the connection stiffness and dynamic stability between the axle and the suspension system |
Subframe connected to stabilizer bar | Subframe forgings, stabilizer bar connecting ears | Achieve stable connection and force balance between the body structure and suspension system |
Suspension struts and connecting sleeves | Pillar forging sleeve, adapter forging shaft | Meet the requirements of shock absorption response and dimensional consistency under high-frequency vibration |
Electric suspension system | Electric control connector, induction flange | Actively adjust with the electronic control system to improve driving comfort |
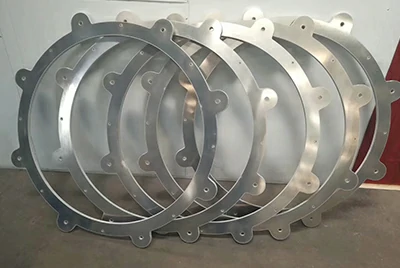
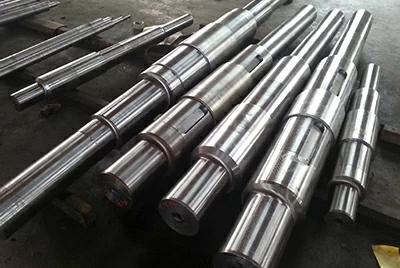
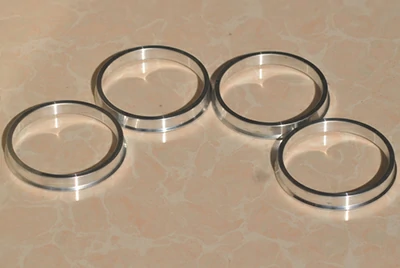
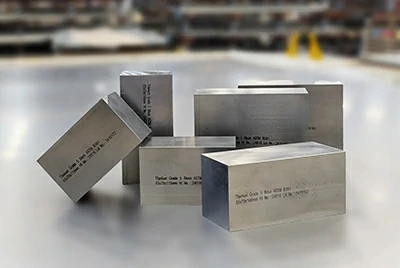
Brake systems and safety parts – high-strength with redundant design
During high-speed driving and braking, brake systems and safety parts endure extreme loads, requiring high material strength, thermal stability, and dimensional accuracy. Forgings are vital in components like brake discs, caliper brackets, energy absorption structures, and cabin frame connections due to their superior fatigue resistance and crack control.
Contact us now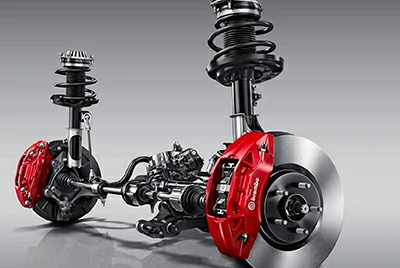
Chalco customizes large high-strength forging plates, high-precision symmetrical brackets, and various connection kits designed for complex stress conditions. Our solutions fully meet automotive active and passive safety system requirements for strength, impact resistance, thermal stability, and geometric accuracy, helping improve vehicle safety and braking performance.
Based on proven applications and customer needs, Chalco recommends the following alloy grades and solutions for this field:
- 6082-T6
- 7075-T73
- 6061-T651
- 7475-T61
- 2014-T6
- 2024-T4
- Ti-6Al-4V (TC4)
- TA2 (Gr.2)
- Ti-6Al-2Sn-4Zr-2Mo
Application module | Typical forging parts | Functional description |
Braking system core structure | Brake disc base forgings, caliper bracket forgings | Anti-thermal decay and balanced force distribution ensure braking efficiency and system life |
High-strength connection structure | Brake master cylinder base, brake lever connecting flange | High-strength rigid docking to meet safety requirements under sudden high loads |
Cabin frame support | absorbing structural forgings , seat rail bases | Effectively absorb impact force in a collision and maintain the stability of the vehicle structure |
Safety cabin structure | A/B column connection forging ring, anti-collision beam bracket forging | Improve impact resistance and overall collision safety to ensure occupant safety |
Smart brake system connection | Electronically controlled brake flange, electric drive brake bracket | Meet the higher requirements of autonomous driving brake modules on size and dynamic response |
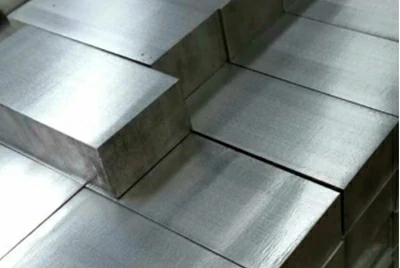
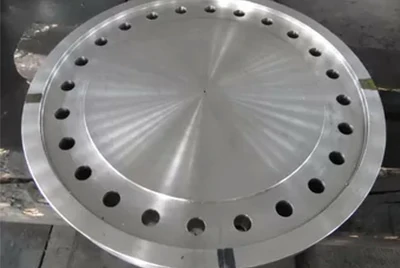
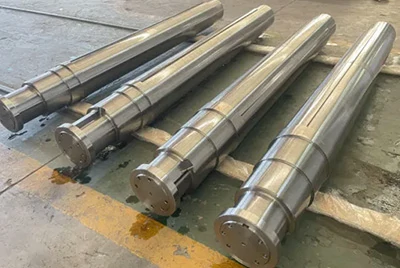
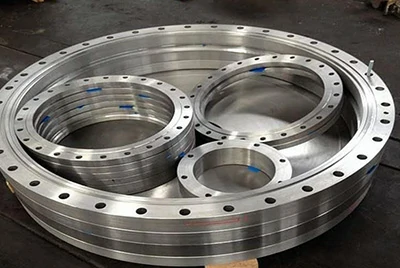
Forgings in vehicle structure and cabin connection – balancing lightweight and strength
Vehicle structural and cabin connection forgings support the rigid frame and link key components, enhancing torsional rigidity, collision safety, and assembly efficiency. Compared to welds or castings, forgings offer better fatigue life, consistency, and strength-to-weight ratio—ideal for complex, load-critical connections.
Contact us now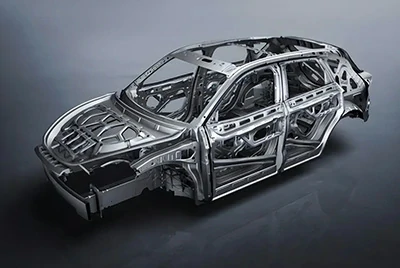
Chalco offers a full range of aluminum and titanium alloy structural forgings, covering applications from main and sub-frame flanges, suspension tower connecting rings, to battery compartment reinforcements. We provide integrated high-precision forging and CNC processing, helping customers enhance structural performance and platform assembly efficiency.
Based on extensive experience and customer needs, Chalco recommends the following alloy grades and solutions for this segment:
- 6082-T6
- 6061-T651
- 7075-T73
- 7050-T7451
- 2024-T3
- 7475-T61
- TA2 (Gr.2)
- TC4 (Ti-6Al-4V)
- TC6 (Ti-6Al-2Mo-1.5Cr)
Application module | Typical forging parts | Functional description |
Front and rear longitudinal beam connection structure | Longitudinal beam end flange, structural connecting ring, force transmission support block | Supports front and rear suspension and collision energy absorption frame |
Subframe and cabin support | Subframe connecting plate, body frame ring | Improve chassis rigidity and module layout stability |
Battery compartment structure connection module | Battery pack side wall connecting ring, battery bracket support | Commonly used in electric platforms, meeting strength and lightness requirements |
connection area between bottom plate and cabin | Floor structure frame flange, center channel support forgings | Enhance the vehicle's torsional performance and improve the collision structure's response capability |
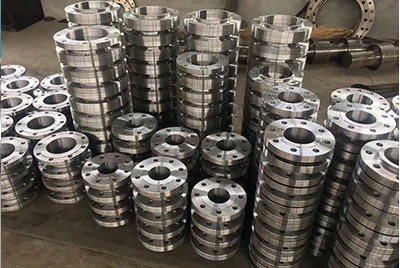
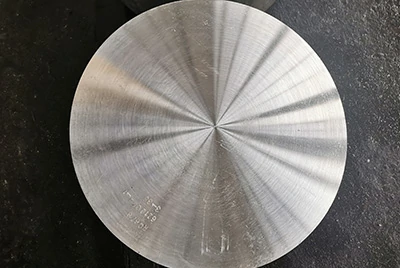
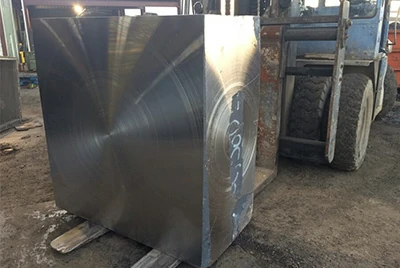
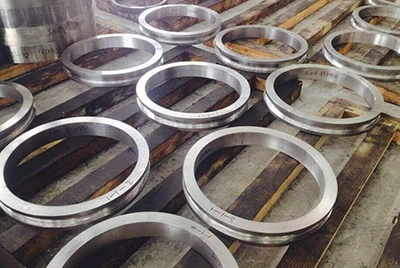
Drive systems for new energy vehicles – lightweight, thermally stable solutions for high power density
As new energy vehicles focus on efficiency and lightweight, key parts like rotor shafts, flanges, and motor brackets demand higher strength, thermal conductivity, and dimensional stability. Forgings are preferred in high-speed, high-torque conditions for their consistency and fatigue strength.
Contact us now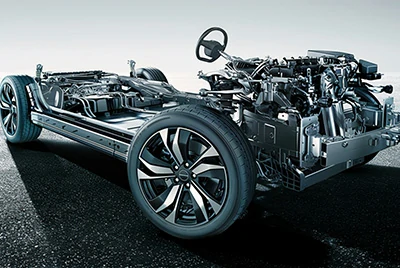
Chalco is dedicated to delivering high-performance aluminum and titanium alloy forgings for electric drive systems. We support customization of high-strength, thermally conductive alloys, complex hollow structures, and integrated processing to meet diverse needs for precision, lightweight design, and thermal stress management.
Based on extensive experience and customer demands, Chalco recommends the following alloy grades and solutions for this field:
- 2618-T61
- 6082-T6
- 6061-T651
- 2024-T3
- 7075-T73
- 2014-T6
- Ti-6Al-4V (TC4)
- Ti-3Al-2.5V (Gr.9)
- Ti-6Al-6V-2Sn
Application module | Typical forging parts | Functional description |
Electric drive motor spindle system | Rotor forging shaft, hollow drive shaft, precision spline shaft | High-speed rotation, strong torque transmission, thermal stability control |
Shell and mounting connection area | Motor housing connection flange, mounting ring, positioning ring | Precise positioning, resistance to thermal expansion and contraction, modular assembly |
Cooling and thermal management structure | Cooling rings, heat conducting brackets, hollow support forgings | High thermal conductivity requirements, assisting in cooling the structure |
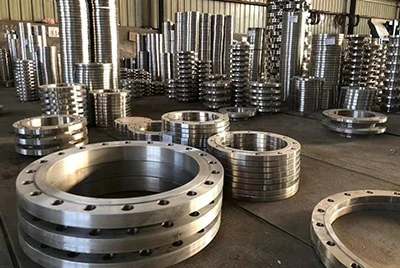
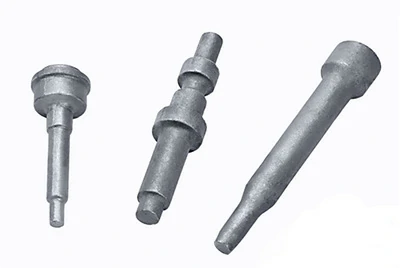
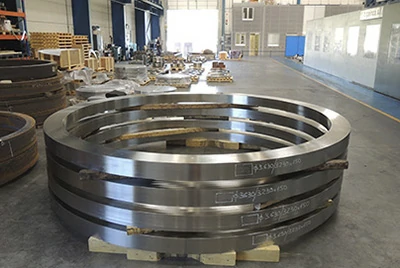
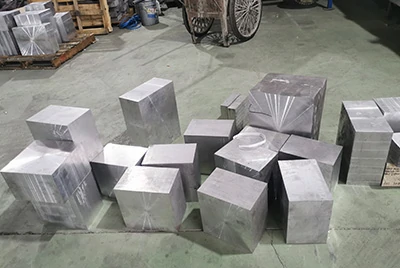
Chalco energy & power forging manufacturing capabilities & supporting services
Focusing on the three core demands of "lightweight + high performance + high efficiency", Chalco has built a complete manufacturing closed loop covering free forging, die forging, finishing, heat treatment and quality inspection delivery. Whether it is traditional fuel vehicles or new energy vehicle power and structural parts, we can provide high-strength, precise size, traceable and high-quality forging solutions.
Efficient die forging capability + lightweight structure customization support
Multi-station die forging system: suitable for flexible batch production of conventional parts such as gears, shafts, and connecting plates, with an annual production capacity of millions;
Automation support: loading and unloading automation + mold quick change system to improve manufacturing cycle and process response speed;
Lightweight and high-strength alloy support: 6061, 7075, 2024, 5083 and other aluminum alloys can realize the integrated forming of complex components such as stepped shafts and ribbed shells;
Mold development and simulation capabilities: proprietary mold design + CAE simulation forming to shorten customer customization development cycle.
Overview of standard forging product types:
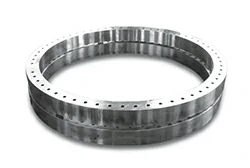
Forged Ring
Used for sealing connections, fuselage section reinforcement, fuel tank interfaces
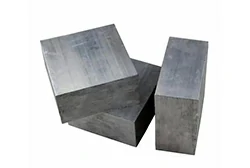
Forged Block
High-strength support, bracket anchor point, control system carrier
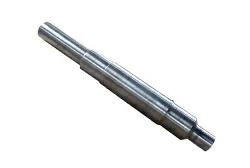
Forged Shaft
Landing gear struts, control shafts, transmission systems
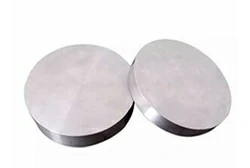
Forged Disc
Engine flange, tail nozzle connection, wheel rim structure
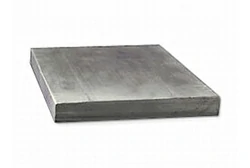
Forged Plate
Bulkheads, support panels, structural reinforcements
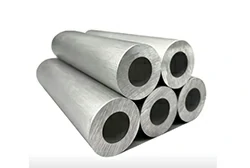
Forged Tube
Fuel pipe interface, cooling system accessories, support insulation sleeve
Integration of heat treatment and finishing capabilities to meet multi-condition assembly requirements
Perfect heat treatment system: support aluminum alloy T6, T651, T73, O state control, titanium alloy annealing, tempering, β treatment and other heat treatment processes;
Heat treatment uniformity ±3℃: Exclusive heat treatment path design based on component stress distribution;
Complete finishing equipment: equipped with CNC vertical/horizontal turning, drilling, milling, tapping and other multi-process processing centers;
High dimensional control accuracy: The controllable tolerance of disks and shafts is ±0.03mm, which is suitable for large-scale stable delivery and automated inspection of terminal assembly lines.
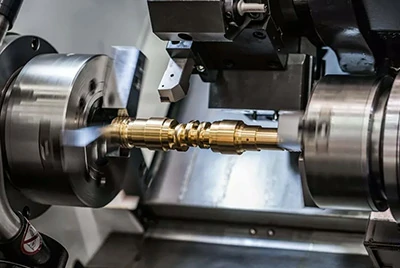
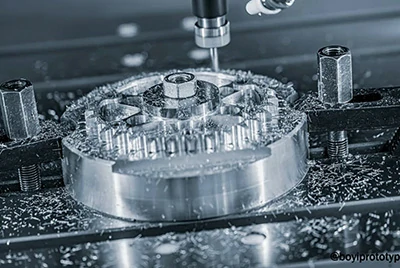
Quality inspection + standard certification system, serving the global automotive manufacturing chain
Complete detection capabilities: support ultrasonic flaw detection (UT), metallographic analysis, mechanical properties testing, and dimensional accuracy testing;
Full process traceability: raw materials → heat treatment → finishing → testing, full link archiving;
Implementation of international standards: Products can meet the requirements of ISO/TS 16949, EN, GB, ASTM and other standards;
Third-party certification support: Supports SGS, TÜV, BV and other certification tests to help customers successfully pass global OEM and first /second-tier supplier reviews.
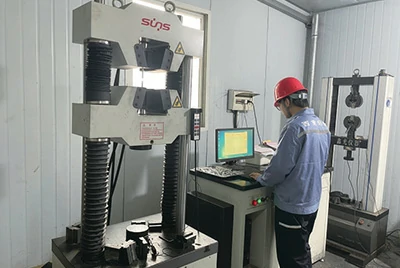
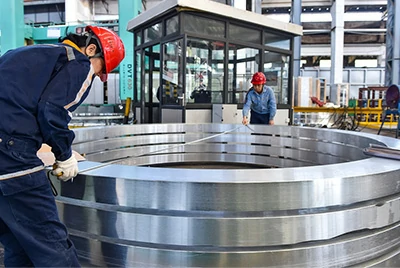
FAQ
Which parts of the car often use forgings?
Forgings are widely used in engines, transmissions, suspensions, chassis, steering, braking systems, etc., such as connecting rods, gear shafts, flanges, control arms, steering knuckles, etc., especially structural components with high requirements for strength and impact resistance.
What automotive alloy forgings do you offer?
We mainly supply high-strength aluminum alloy (6061, 2024, 7075, 7050, 7475, 6082, etc.) and titanium alloy (TA2, TC4, Ti-6Al-2Sn-4Zr-2Mo, etc.) forgings. We can also provide high-strength steel and stainless steel forgings on demand, and support status processing and material certification documents.
Does it support drawing customization and small batch trial production?
Support. We provide one-stop services from drawing design review, mold development, process simulation, sample trial production to batch delivery, which is particularly suitable for the forging development needs in the vehicle R&D stage or modification verification stage.
Can heat treatment and finishing be completed in one go?
Yes. Chalco supports T6, T651, T73 and other heat treatment processes and a variety of CNC processing capabilities. It can deliver semi-finished or near-net-size products, reducing customers' processing costs and assembly errors.
Can it meet the quality and certification requirements of the automotive industry?
We implement international standards such as ISO/TS 16949, EN, GB, ASTM, etc. Our products can provide third-party test reports such as SGS, TÜV, BV, and full-process material traceability to meet the needs of global vehicle manufacturers and parts supply chains.
With the trend of lightweight automobiles, what are the advantages of aluminum alloy forgings?
Aluminum forgings have low density, high specific strength, excellent formability and fatigue resistance. They can effectively reduce the weight of the vehicle without sacrificing structural strength. They are a key material for achieving energy conservation and high efficiency of electric drives.
Chalco can provide you the most comprehensive inventory of aluminum products and can also supply you customized products. Precise quotation will be provided within 24 hours.
Get a quote