Forged products play a vital role in structural connections, sealing, pressure containment, and power support across aerospace systems. Their high strength, continuous grain flow, and fatigue resistance make them indispensable in aircraft, rockets, satellites, and ground equipment.
Chalco specializes in aluminum alloy forgings, offering advanced heat treatments, ring rolling, and free forging. We also provide customized titanium, copper, and steel forgings to meet diverse structural and material requirements.
Forgings for aircraft manufacturing
Forgings are critical in civil and military aircraft for load-bearing, connection, and transmission parts like landing gear, wing frames, and engine mounts. They offer the strength, fatigue life, and corrosion resistance needed under dynamic loads and high-frequency vibrations, ensuring structural integrity and flight safety.
Contact us now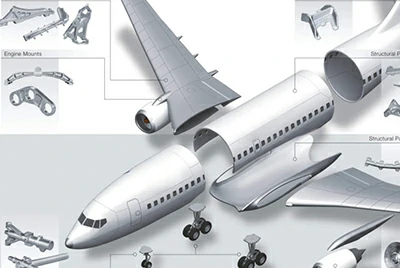
Forged shafts and forged blocks suitable for aircraft structures to mainstream aviation manufacturers such as Boeing, Airbus, Collins Aerospace Systems and their supporting supply chains.
Chalco has complete free forging and ring rolling capabilities, and are equipped with a variety of heat treatment state control and high-precision processing methods to ensure that the strict requirements of aviation standards in different countries and regions (such as AMS, QQ, GJB) in terms of size, performance and traceability are met, and support third-party testing.
Chalco aircraft manufacturing forgings adaptation product display
- Landing gear auxiliary support flange ring: 7050 / Ti-6Al-4V and other alloy materials; high strength and corrosion resistance, thick wall and good load-bearing performance
- Fuselage cabin section docking connection ring: 7075 / 2219 and other alloy materials; streamlined and continuous, excellent fatigue performance
- Door reinforcement frame: 6061 / 7075 and other alloy materials; good weldability and lightweight structure
- Engine bracket connection block: 2618 / Ti-6242 and other alloy materials; good high temperature strength and stability
- Wing root bearing ring: 7475 / 7050 and other alloy materials; high strength, crack resistance, good ductility
- Flight control shaft/connecting shaft: 2024/Ti-6Al-4V and other alloy materials; strong shock resistance and compact structure
- Cabin frame connection: 7075 / 2219 and other alloy materials; multi-axis matching structure, strong deformation resistance
- Aircraft rack support structure: 7050 / Ti-6Al-6V-2Sn and other alloy materials; high load parts, excellent fatigue resistance
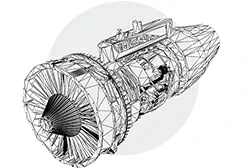
Jet Engine
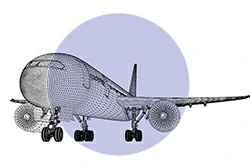
Aircraft Structure
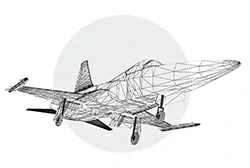
Military Aircraft
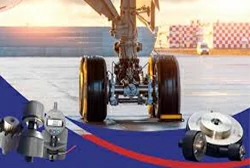
Landing Gear Flange
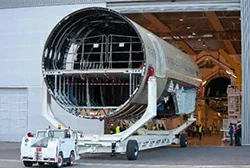
Fuselage Compartment Connection Ring
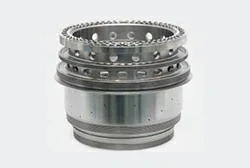
Engine Shaft
Forgings for rocket and launch vehicle systems
In liquid and solid rocket systems, forgings are key for sealing, support, and pressure transmission—used in tank rings, flanges, thrust rings, and nozzle bases. They withstand extreme heat, pressure, and vibration, demanding high density, fatigue resistance, and thermal stability.
Contact us now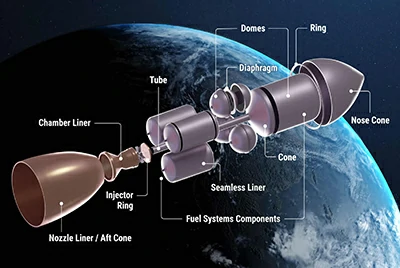
Chalco has participated in many rocket engineering projects, cooperating with model units to provide large-diameter high-strength aluminum alloy, titanium alloy and steel forging rings and shaft parts.
Chalco complies with aerospace material standards (such as HB, GJB, and YB) and provides supporting heat treatment and flaw detection services, ensuring rapid response from prototyping to mass production.
Chalco rocket and carrier system forgings adaptation product display
- Fuel tank connection ring: 2219 / 7050 and other alloys; excellent high temperature strength and good weldability
- Cabin flange: 7075 / Ti-6Al-4V and other alloys; high strength, light weight, excellent seismic resistance
- Thrust cylinder support forging ring: 2618 / Ti-6242 and other alloys; high temperature creep resistance, suitable for hot end structure
- Nozzle base structure block: Ti-6Al-6V-2Sn / 2219 and other alloys; high temperature strength + welding process compatibility
- Middle frame connecting shaft: 7050 / TC11 and other alloys; good dimensional stability and fatigue life
- Forgings for the star-rocket interface: Alloys such as 7075/2219; continuous streamlined forming and high service reliability
- Solid rocket tail section connection ring: Ti-6Al-4V / Gr2 and other alloys; good heat and corrosion resistance, suitable for sea-based and hot and humid environment service scenes
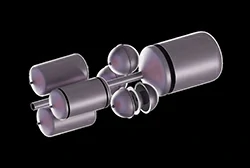
Fuel system components
Available in 2219, 6061, 7075, etc. Tubes Ø8"–24", formed parts up to Ø110".
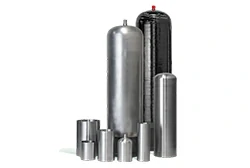
Pressure vessel parts
Seamless vessels and aluminum liners. Full units up to Ø23", halves Ø8"–50".
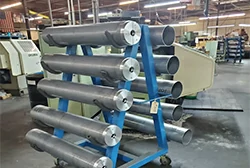
Solid rocket motor casing
Rotary forging and flow forming are used for optimal structural support, ensuring maximum strength and performance.
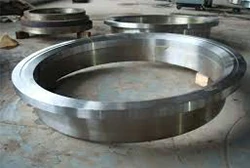
Thrust cylinder support forging ring
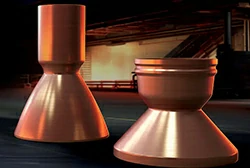
Combustion chamber
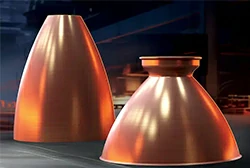
Cones and nozzles
Satellite platform and cabin structure forgings
Forgings in low/medium/GEO satellites serve as structural frames, connectors, and actuator bases, requiring high strength-to-weight ratio, precision, and stability—especially during launch.
Contact us now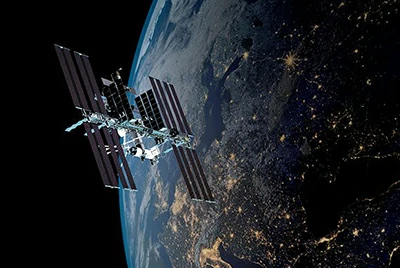
Chalco supports the customization and batch supply of a variety of high-strength and lightweight aluminum alloy and titanium alloy forgings, and has successfully supported communication satellites, remote sensing platforms, navigation constellations and other model projects.
The products can be processed and delivered according to aerospace standards such as HB/Z, GJB, AMS, etc., and have good structural consistency and batch stability.
Chalco satellite platform and cabin structure forgings adaptation product display
- Star frame connection flange: 7075 / 2219 and other alloys; high strength, good streamline continuity, suitable for the main load-bearing structure
- Attitude control system base forging block: Ti-6Al-4V / 2024 and other alloys; good seismic resistance, high dimensional stability
- Power supply compartment connection ring: 7050 / 6061 and other alloys; strong weldability, good electromagnetic compatibility structure adaptability
- Antenna platform mounting flange: 6061 / Ti-3Al-2.5V and other alloys; excellent formability, easy to control thin-walled lightweight structures
- Satellite cabin bulkhead/connectors: 7475/TC4 alloys; good toughness, strong crack propagation resistance, suitable for high reliability parts
- Propulsion cabin frame support shaft: Ti-6Al-6V-2Sn / 2219 and other alloys; high temperature resistance and fatigue resistance, suitable for electric propulsion and liquid attitude control system
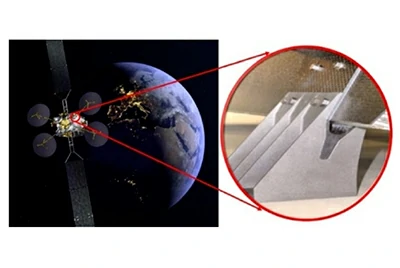
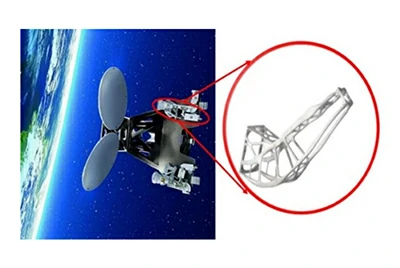
Aerospace engine system forgings
Rocket propulsion systems use forgings in core hot-end parts like nozzles and thrust frames, where extreme heat, pressure, and stress gradients demand top material performance.
Contact us now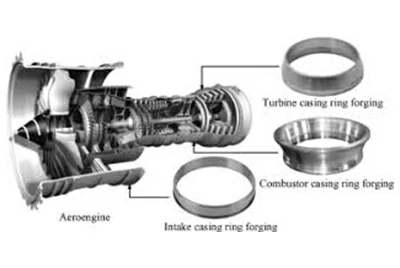
Chalco supplies high-temperature alloy and titanium alloy forgings for various propulsion systems. It has an integrated service system of free forging + ring rolling + heat treatment + rough and fine machining to ensure that the products meet extreme usage requirements in terms of organizational density, dimensional accuracy and service stability.
Chalco aerospace engine system forging adaptation product display
- Nozzle interface forging ring: Ti-6Al-4V / 2219 and other alloys; heat resistance and strength are both taken into consideration, suitable for liquid / solid fuel systems
- Thrust cylinder connection flange: Ti-6242 / 2618 and other alloys; good high temperature stability, excellent creep performance, heat and high pressure resistance
- Combustion chamber insulation support structure: Ti-6Al-6V-2Sn / 2219 and other alloys; meet the requirements of light weight and thermal strength at the same time, adapt to high combustion chamber temperature environment
- Nozzle frame structure: TC11 / 2618 and other alloys; excellent toughness and high temperature oxidation resistance, suitable for complex welding structures
- Multi-stage propulsion cabin connection forging block: Ti-3Al-2.5V / 7050 and other alloys; good formability, suitable for space-constrained and high-precision parts
- Liquid fuel injection port forgings: Gr.2 / Gr.5 alloys; high corrosion resistance, suitable for occasions with variable propellants and complex sealing requirements
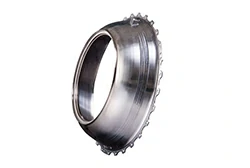
Tail nozzle connection ring
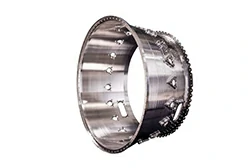
Combustion chamber casing
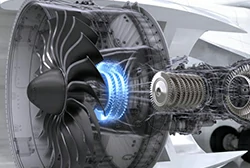
Turbine engine blades
Ground test and launch platform structural forgings
Ground systems for rockets and satellites rely on high-strength forgings in test benches and launch platforms. Components like flanges, rings, and sleeves require exceptional strength, fatigue life, and stability, while supporting fast assembly, reliable docking, and harsh environment tolerance.
Contact us now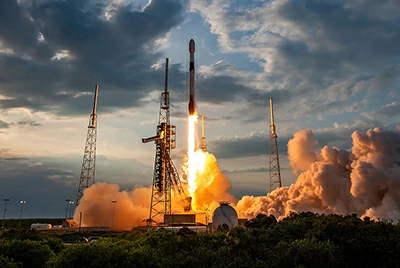
Chalco has the free forging and pre-machining capabilities with a maximum diameter of 2500mm and a single piece of ≤80 tons. It can provide key forging solutions such as integrated connection forgings, pre-assembled welded parts and modular docking flanges for various launch platforms . Combined with heat treatment + CNC pre-machining + third-party testing, it can achieve high-reliability delivery from raw materials to structural parts.
Chalco ground test and launch platform structural forgings adaptation product display
- Ground test platform main bearing flange
- Engine test bench forged connecting sleeve
- Multifunctional launch support frame connecting forging block
- Solid and liquid fuel assembly transfer platform rotating shaft ring
- Rocket guide rail ring segment
- Ground mobile loading thrust ring plate
- Rocket body docking bearing ring
- Antenna/tower lower buffer forging ring
New aircraft system forgings
Next-gen aircraft like hypersonic vehicles and reentry capsules demand forgings with greater structural complexity, thermal stability, and reliability. Used in hot-end frames, control shafts, and flanges, they must handle extreme temperatures and impacts while meeting lightweight, custom, and rapid delivery needs.
Contact us now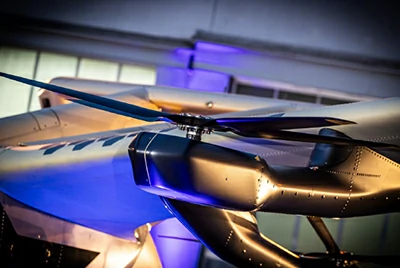
Chalco has complete free forging + ring rolling + CNC processing capabilities in the customization of high-temperature alloy, titanium alloy and high-strength aluminum alloy forgings. It has supported a number of cutting-edge aircraft verification projects and provides customers with a one-stop solution from material selection → heat treatment matching → special-shaped structure forging → processing and assembly docking.
Chalco's new aircraft system forgings adaptation product display
- Hypersonic aircraft inter-segment connection flange
- Reusable Propulsion System Forged Ring Assembly
- Return capsule hot end connecting barrel flange
- Thermal protection structure forgings for aerospace vehicle missiles
- Fuselage center section support forging ring /strengthening rib
- Attitude control system shaft, eccentric kit
- Missile-grade structural forging parts
- Reentry module positioning bearing ring structure
Overview of alloy standards and configurations for common aerospace forgings
In order to meet the multiple requirements of strength, fatigue, corrosion resistance and thermal stability of different aircraft structures, power systems and hot-end components, Chalco has a long-term inventory of a variety of aviation-grade forging alloys, and can provide cut-to-length processing and heat treatment state customization according to customer needs. All products support third-party inspection and standard traceability.
Aluminum alloy forgings
Type | Temper | Specifications |
2014 Aluminum | T6 / T651 | AMS4133, 4134, 4314, AMS-A-22771 |
2024 Aluminum | T4 / T42 / T6 | AMS-QQ-A-367 |
2219 Aluminum | T6 / T62 | AMS4143, 4144, AMS-QQ-A-367, AMS-A-22771 |
2618 Aluminum | T61 / T651 | AMS4132, AMS-QQ-A-367, AMS-A-22771 |
5083 Aluminum | O / H111 | ASTM B247 / GB/T 6892 / ISO 6361 |
6061 Aluminum | T6 / T651 | AMS4127, 4146, AMS-QQ-A-367, AMS-A-22771 |
6082 Aluminum | T6 / O | EN 586 / ISO 6361 / GB/T 6892 |
7049 Aluminum | T73 / T7351 | AMS4111, AMS-QQ-A-367, AMS-A-22771 |
7050 Aluminum | T74 / T76 | AMS4107, 4108, AMS-A-22771 |
7075 Aluminum | T6 / T73 / T76 | AMS4126, 4131, 4141, 4147, AMS-QQ-A-367 |
7175 Aluminum | T73651 / T7351 | AMS4148, 4149, 4179, AMS-A-22771 |
7475 Aluminum | T61 / T7351 | AMS 4085 / HB |
Titanium alloy forgings
Type | Specifications |
CP-GRADES 1, 2, 3, 4 | AMS4921, ASTM-B348 |
6Al-4V | AMS4928, 4931, 4965, AMS-T-9047, C50TF12 |
6Al-4V ELI | AMS4930, 4931, 6932, BMS-7-269 |
6Al-2Sn-4Zr-2Mo | AMS495, 4976, B50TF22 |
6Al-6V-2Sn | AMS4978 |
8Al-1Mo-1V | AMS4972, 4973, C50T81 |
10V-2Fe-3Al | AMS4983 |
Aviation general forgings product types
Used for sealing connections, fuselage section reinforcement, fuel tank interfaces
High-strength support, bracket anchor point, control system carrier
Landing gear struts, control shafts, transmission systems
Engine flange, tail nozzle connection, wheel rim structure
Bulkheads, support panels, structural reinforcements
Fuel pipe interface, cooling system accessories, support insulation sleeve
Why choose Chalco: Manufacturing guarantee and service advantages of aerospace forgings
In aviation manufacturing, forgings are usually subjected to high stress, complex fit and extreme environment service requirements. Chalco has built a high-precision, high-consistency and strong traceability manufacturing system around aluminum alloy and titanium alloy forgings for aviation, ensuring that each forging meets engineering-grade standards in terms of structural integrity, dimensional accuracy and performance stability.
High-performance forging capabilities (supporting large-size customization requirements of aviation OEMs)
- Free forging + CNC ring rolling integrated process, maximum outer diameter Ø2500mm, maximum thickness 1000mm, adaptable to various needs such as structural connection, load-bearing/rotating parts, etc.
- Closed die forging capability (aircraft die forging): Maximum die forging size can reach 950mm × 3000mm, weight ≤ 5 tons, supporting complex geometric structures and precise fiber streamline directional control;
- Multi-stage die forging and forming is suitable for complex-shaped precision components such as aircraft cabin node structures, engine tail nozzle rings , and landing gear docking kits;
- Titanium alloy exclusive heating and low-pollution forging system, supporting vacuum forging and inert atmosphere protection, ensuring β grain consistency and mechanical properties, meeting aviation standards.
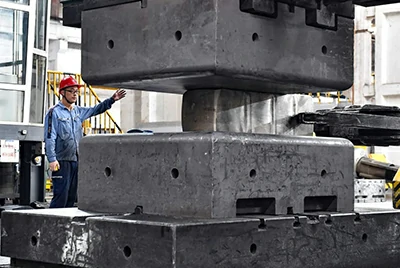
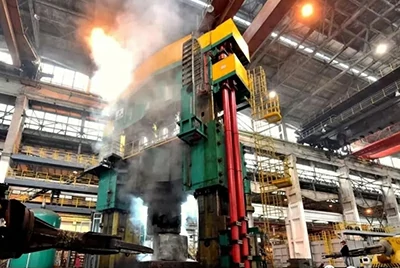
Advanced Heat Treatment & Precision Machining
- Aluminum heat treatment states: T6, T651, T42, O, with furnace uniformity ±3 ℃
- Titanium alloy treatments: β annealing, double annealing with precise curve control
- NADCAP-level support: full records of curves, hardness, tensile reports
- Machining tolerance: up to ±0.05 mm for flanges, coaxial holes, rotating parts
- Processes include turning, milling, drilling, keyways, and custom aviation interfaces
- Surface roughness controlled to Ra 0.8 μm to meet aerospace specs
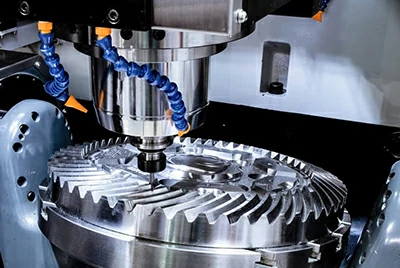
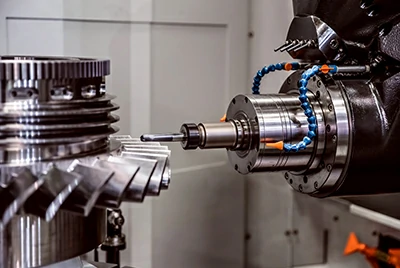
Testing and standard implementation guarantee
- UT ultrasonic flaw detection, metallographic analysis, grain rating (titanium alloy β grains can be controlled to level 3), mechanical properties testing
- Implementation standards: AMS 4045 / AMS 4127 / HB/Z140 / GJB 1438A / ASTM B247, etc.
- Can provide third-party inspection reports (SGS, BV, TÜV, etc.) and factory certificates
Reference for aerospace forgings | ||||
Product Type | Maximum outer diameter/width | Maximum length/height | Maximum unit weight | Process Description |
Forged shaft (including hollow shaft) | Ø1500 mm | 11, 000 mm | ≤80 tons | Free forging, stepped shaft/flange shaft structure |
Forged rods / round bars | Ø1500 mm | 11, 000 mm | ≤50 tons | Including hexagonal bars and special-shaped bars |
Forging Block / Flat Steel/ Billet | 3500 mm × 3500 mm | 1000 mm | ≤80 tons | Die forging or free forging, support special-shaped slotting |
Forged discs / round discs/ wheel hubs | Ø4000 mm | Thickness 500 mm | ≤75 tons | Hot die forging/free forging/precision machining |
Seamless Forged Rings /Ring Rollings | Ø4000 mm | Height 800 mm | ≤50 tons (depending on material) | CNC ring rolling, radial and axial synchronous rolling |
Barrel Forgings/ Sleeve Forgings | Ø2500 mm | 5000 mm | ≤50 tons | Suitable for pressure vessels/ propulsion shells, etc. |
Closed Die Forgings/ Precision Structures | Width 950 mm (or Ø 1500 mm) | Length 3000–4000 mm | ≤5 tons | Die forging / multi-stage forming / minimum wall thickness 1.4 mm |
Post extrusion forgings/cup parts | Ø1000 mm | 1500 mm | ≤3 tons | For nozzle structure/sealed container parts |
FAQ
Which aerospace components can be forged?
Chalco can forge a variety of aerospace structural parts and power components, including landing gear supports, engine connecting rings, cabin flanges, sealing flanges, transmission sleeves, etc., while providing closed die forging and free forging/ring rolling processes to adapt to different shapes and performance requirements.
What key materials are available for aviation forgings?
We mainly provide aluminum alloy and titanium alloy forgings, typical grades include:
- Aluminum alloy: 6061, 7050, 7075, 2024, 2219, 7475, etc.
- Titanium alloy: Gr.2 (TA2), Gr.5 (TC4), Ti-6242, Gr.9, etc.
We can also customize high-strength steel and copper alloy forgings, providing complete material reports and industry standard support.
What are the advantages of aviation forgings over castings and welded parts?
Forgings have higher density, grain continuity and streamlined structure, higher strength, better fatigue resistance and corrosion resistance than castings and welded parts, and are more suitable for use in key load-bearing parts of aircraft.
Can you provide Nadcap and other certification support?
Yes. Chalco aviation forgings can be used in conjunction with Nadcap, AMS, HB, GJB and other certification system standards, support full-process quality traceability and third-party inspection (SGS, TÜV, BV, etc.), and help smooth project acceptance.
Can you provide heat treatment and processing services?
such as T6, T651, annealing, tempering, and solution treatment, and provide precision machining such as turning, drilling, chamfering, and keyways, which can be customized according to drawings to meet the needs of near-net- shape forming and high assembly accuracy.
What is aviation closed die forging?
Closed die forging is a forging process in which heated billets are placed in precision molds for forming. It is suitable for manufacturing aviation components with complex geometry, precise dimensions and extremely high-performance requirements, such as landing gear connecting blocks, tail nozzle sections, etc.
Do you support customized development cooperation?
Of course. Chalco supports the whole process of customized services from structure collaborative design, mold development, material recommendation, sample proofing to mass production delivery, and can sign a confidentiality agreement to support scientific research/experimental project support. Can it support customized development cooperation in the aerospace field?
Of course. Chalco supports the whole process of collaboration from material recommendation, structure collaborative design, mold development, forging process formulation, trial production and sampling to mass production delivery. It can cooperate with customers to participate in R&D or scientific research projects, and provide confidentiality agreements and special support services.
If you need to obtain product catalogs, material certificates or drawing quotations, please click Quick Quote to submit your requirements and we will contact you as soon as possible.
Chalco can provide you the most comprehensive inventory of aluminum products and can also supply you customized products. Precise quotation will be provided within 24 hours.
Get a quote