Copper clad aluminum plates combine the excellent conductivity of copper with the lightweight, cost-effectiveproperties of aluminum. They offer high conductivity, good thermal performance, corrosion resistance, and arelightweight and cost-efficient.
They are an ideal alternative to copper conductors in the power industry, reducing costs while providing stableelectrical performance and strength.
Copper clad aluminum plate specifications
Standards: NB/T 47002.4-2009, GB/T 32468-2015, ASTM B898 / B891, ASTM B432 / EN 485-1/2/3, ASTM B734 / ISO 4521, EN573, ASTM B209
Certifications: IEC 60439, UL 486A/B, IEC 62660-2 / ISO 12405 / UN 38.3, ISO 9001, RoHS, REACH
Free samples available for customers to test conductivity, mechanical properties, and composite quality.
All products come with original manufacturer certificates (MTC) and third-party inspection reports (e.g., SGS, TÜV,BV).
Instant QuoteCopper clad aluminum plate product description
Product structure
- Single-sided copper clad aluminum plate (Cu/Al): Common thickness ratio is 15/85, but custom ratios from 5/95 to50/50 are available upon request.
- Double-sided copper clad aluminum plate (Cu/Al/Cu): Common ratio is 10/80/10, with copper layer thickness up to30%.
- Double-sided aluminum clad copper plate (Al/Cu/Al): Also available, with a common ratio of 10/80/10.
We offer full customization of copper clad aluminum plates, including thickness, copper layer ratio, and dimensions,to meet the specific needs of different projects.
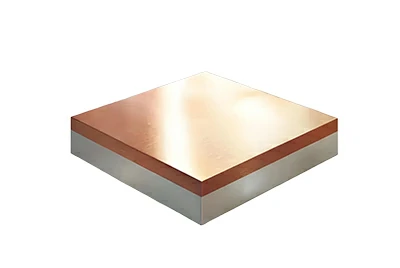
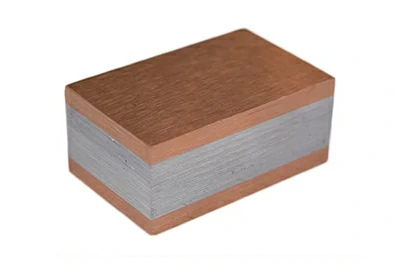
Product dimensions
- Total Thickness: 0.5 – 15.0 mm (custom specifications up to 20 mm or higher)
- Width: ≤1200 mm (can be customized up to 2000 mm)
- Length: ≤6000 mm (can be sliced)
- Composite method: Embedded composite, covered composite, welded composite
- Product types: Sheet, plate, foil, coil, discs, terminal connectors, bosses, washers, PG clips, grounding blocks(custom design and manufacturing)
- 90-degree bend: No cracking
- Copper cladding ratio: 100%
Alloy composition
Copper layer: T2, TU1, H62/H65, C11000, C10200, C70600 (ASME SB171 / SB152 / GB/T 2040)
Aluminum layer: 1050, 1060, 1070, 3003, 8011, LF21, L2 (GB/T 3880, GB/T 3190)
Popular copper clad aluminum plate products
We offer a variety of popular copper clad aluminum plates and bimetallic custom products, including single-sidedcopper plates, double-sided composites, embedded copper structures, CCA busbars, and more.
Feel free to contact us for free samples and tailored solutions.
Instant QuoteSingle-sided Copper Clad Aluminum Plate
Common sizes include 500×600, 600×1200, 1050×1250 mm, suitable for applications in electricalconductivity and thermal management, such as electric vehicles, LEDs, and power modules.
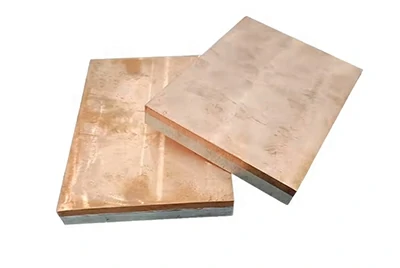

Double-sided Copper Clad Aluminum Plate
The common ratio is 10/80/10, with the copper layer thickness up to 30%, offering superior conductivityand thermal performance, ideal for high-demand power electronics and heat dissipation modules.
Single Inlay
Custom copper inlay width, thickness, and plate dimensions are available. Ideal for applicationsrequiring localized conductivity or heat dissipation, such as battery connectors and busbar systems.
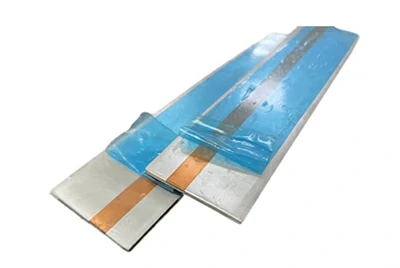
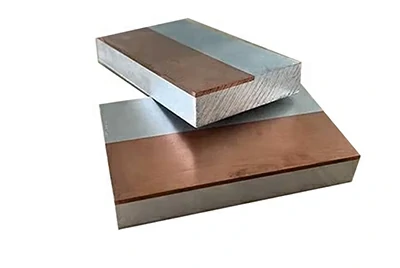
Single-sided Inlay
Custom copper layer positioning, size, and ratio are available based on your design. This effectivelyreduces material costs while meeting specific conductivity or welding performance requirements forcertain areas.
CCA busbar
Copper clad aluminum busbars offer excellent conductivity, support punching and customization ofdimensions and hole positions, and are widely used in power connections such as battery packs andinverters.
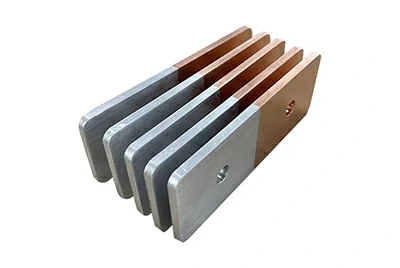
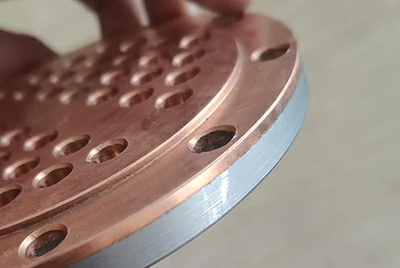
Copper Clad Aluminum Plate Tube Sheet
Copper clad aluminum plate tube sheets comply with ASTM B432, with thickness ranging from 3–600mm anddiameter from 450–5000mm. They are heat and pressure resistant, ideal for high-precision compositeconnections in heat exchange equipment.
Copper clad aluminum plate tube sheets comply with ASTM B432, with thickness ranging from 3–600mm and diameter from450–5000mm. They are heat and pressure resistant, ideal for high-precision composite connections in heat exchangeequipment.
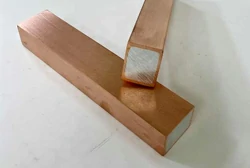
Copper Clad Aluminium Row
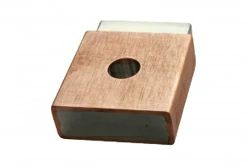
Copper Clad Aluminum Earthing Block
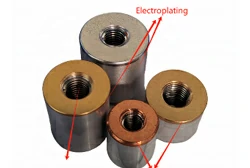
Copper Clad Aluminum Earthing Boss
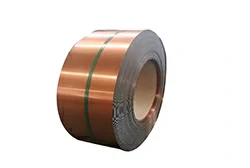
Copper Clad Aluminum Strips
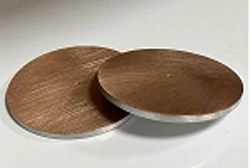
Cu-Al Composite Washer
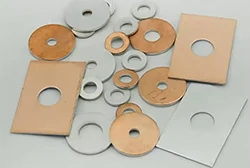
Copper-Aluminum Washer
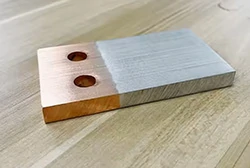
Copper Aluminum Transitional bar
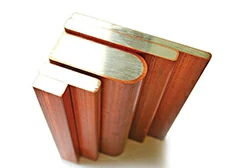
Copper Clad Aluminium flat bar CCA

Copper-Aluminum Bimetallic Cable Connector
In addition to copper-aluminum composite materials, we also offer many other bimetallic products. We accept customorders for various products.
Instant Quote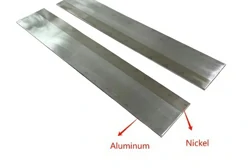
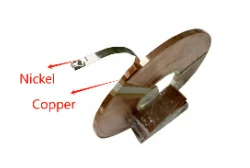
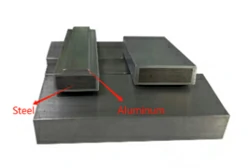
Copper clad aluminum plate stock sizes
Our in-stock products can be shipped within 24 hours.
If you don’t find the right size, contact us for custom options.
Instant QuoteAlloy | Temper | Specification | Size (mm) | Copper Content | Quantity |
1060/T2 | O | Plate | 2.0×605×1200 | 10% | 190 pics |
1060/T2 | O | Plate | 1.5×605×1200 | 10% | 278 pics |
1060/T2 | O | Plate | 1.0×605×1200 | 10% | 334 pics |
1060/T2 | O | Plate | 5.0×150×2000 | 10% | 205 pics |
3003/T2 | H18 | Plate | 1.5×600×1000 | 12.24% | 60 pics |
3003/T2 | H18 | Plate | 2.0×600×1000 | 10% | 2000 pics |
1060/T2 | O | Coil | 1.0×15 | 10% | - |
1060/T2 | O | Coil | 1.0×20 | 10% | - |
1060/T2 | O | Coil | 1.0×25 | 10% | - |
1060/T2 | O | Coil | 1.0×30 | 10% | - |
1060/T2 | O | Coil | 1.0×35 | 10% | - |
1060/T2 | O | Coil | 1.0×40 | 10% | - |
1060/T2 | O | Coil | 1.5×20 | 10% | - |
1060/T2 | O | Coil | 1.5×25 | 10% | - |
1060/T2 | O | Coil | 1.5×30 | 10% | - |
1060/T2 | O | Coil | 1.5×35 | 10% | - |
1060/T2 | O | Coil | 1.5×40 | 10% | - |
1060/T2 | O | Coil | 2.0×20 | 10% | - |
1060/T2 | O | Coil | 2.0×25 | 10% | - |
1060/T2 | O | Coil | 2.0×30 | 10% | - |
Copper clad aluminum plate mechanical and electrical properties
Below are key performance parameters of copper clad aluminum plates, offering a lightweight, cost-effective solutionfor high-conductivity electrical applications.
Type | Temper | Yield Stress MPa (Ksi) | Tensile Strength MPa (Ksi) | Elongation % min | Thermal Conductivity cal/cm/sec/°C | Electrical Conductivity %IACS |
Cu 10% Al 90% | Soft | 39-49 (5.7-7.1) | 83-110 (12-16) | 28 | 0.54 | 61-63 |
Cu 10% Al 90% | Hard | 124-152 (18-22) | 173-200 (25-29) | 5 | ||
Cu 20% Al 80% | Soft | 44-54 (6.4-7.8) | 97-117 (14-17) | 30 | 0.58 | 64-66 |
Cu 20% Al 80% | Hard | 152-179 (22-26) | 186-207 (27-30) | 5 | ||
Cu 10% Al 80% Cu 10% | Soft | 44-54 (6.4-7.8) | 97-117 (14-17) | 30 | 0.58 | 64-66 |
Cu 10% Al 80% Cu 10% | Hard | 152-179 (22-26) | 186-207 (27-30) | 5 | ||
Cu 30% Al 70% | Soft | 49-56 (7.1-8.1) | 117-138 (17-20) | 34 | 0.62 | 68-70 |
Cu 30% Al 70% | Hard | 167-186 (24.2-27) | 193-228 (28-33) | 6 | ||
Cu 15% Al 70% Cu 15% | Soft | 49-56 (7.1-8.1) | 117-138 (17-20) | 34 | 0.62 | 68-70 |
Cu 15% Al 70% Cu 15% | Hard | 167-186 (24.2-27) | 193-228 (28-33) | 6 |
Applications of copper clad aluminum plate
- Power Industry: Used for busbars, conductive connectors, and transition joints, providing stable conductivitywhile reducing energy consumption and cost.
- Electronics and Battery Industry: Used for lithium battery tabs, connectors, busbars, cable plugs, etc.,offering lightweight and high conductivity.
- LED and Heat Dissipation Systems: Used in LED substrates and heat sinks, enhancing thermal efficiency andextending service life.
- New Energy and Electric Vehicles: Used in inverters, IGBT modules, and heat dissipation structures for energystorage devices.
- Construction and Daily Goods: With an attractive appearance and low cost, suitable for decorative components andeveryday metal products.
Power Battery Negative Electrode Posts and Busbars
Power battery connectors use cast-rolled copper-aluminum composite plates, offering strong, non-peelingbonding, high strength, good machinability, and stable conductivity over the long term.
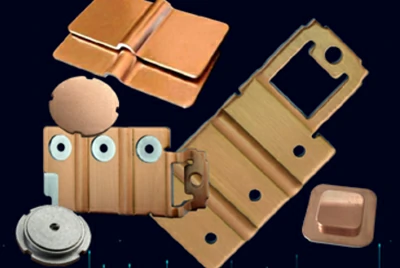
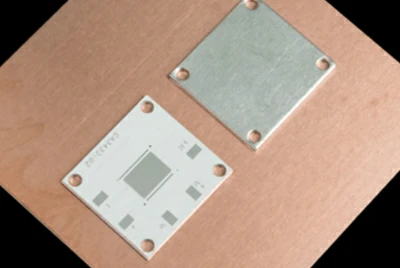
LED copper-aluminum composite
Thermoelectric separation LED copper-aluminum composite substrates combine copper's thermal conductivitywith aluminum's heat dissipation and lightweight properties, ideal for next-gen LEDs and communicationdevices.
Copper-Aluminum Connector
Featuring advanced composite molding, this connector offers excellent conductivity, high-temperatureresistance, and prevents electrochemical reactions, ideal for busbar and terminal connections.
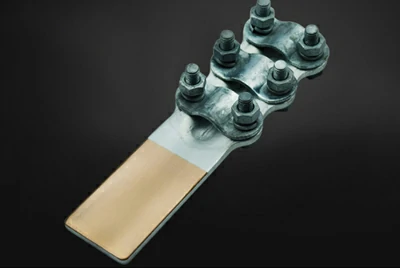
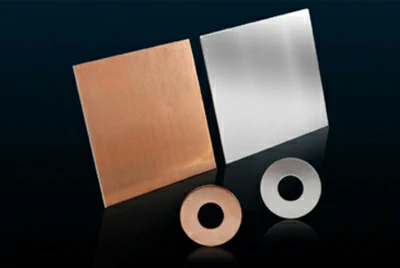
Copper-Aluminum Composite Washer
Used for copper-aluminum transitions, these washers prevent corrosion and overheating, widely applied inreactors and lithium batteries, with thickness 1.0–3.0mm and copper layer ratio of 10%–30%.
Copper-Aluminum Composite Heat Sink
Offering high thermal conductivity and lightweight properties, these heat sinks provide superiorefficiency and are widely used in high heat density applications like EV inverters, PLC chips, andhigh-power LEDs.
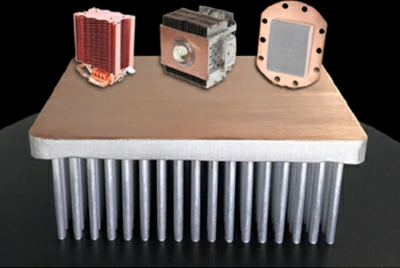
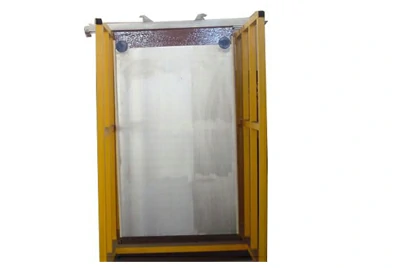
Copper-Aluminum Plate for Lithium Battery Connections
Copper-aluminum plates and aluminum-copper composites for lithium battery connections andhydrometallurgical systems, offering excellent conductivity, corrosion resistance, and long servicelife.
Electronic Chassis and Enclosures
Copper-aluminum material, lightweight, easy to form, with low-resistance shielding and electroplating,ideal for conductive and thermal components.
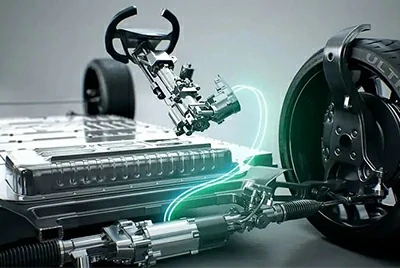
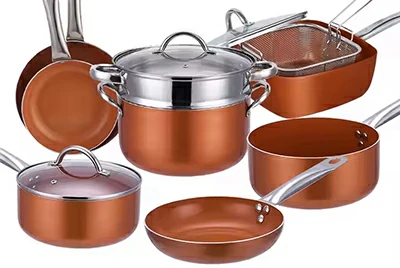
In food service and cookware
Copper-clad aluminum combines the classic appearance and excellent conductivity of copper with theconductivity, strength, and lightweight properties of aluminum.
Advantages of copper clad aluminum plate
- The copper layer provides high electrical conductivity (≥92% IACS), making it ideal for high-efficiencyelectrical transmission in applications such as power distribution, wiring, and PCBs.
- Excellent thermal conductivity and heat dissipation, suitable for heat sinks, heat exchangers, and otherhigh-heat devices.
- Metallurgically bonded for strong, durable joints, with high temperature resistance (up to 500°C withoutseparation) and corrosion resistance, ensuring long service life.
- Offers good stretchability, deep drawing, and bending properties, with no delamination at 90° bending.
- Supports secondary processing such as welding, electroplating, drilling, and tapping, compatible with automatedproduction lines.
- The aluminum core significantly reduces weight, cutting copper usage by up to 64% while maintaining the sameconductivity.
Chalco's copper clad aluminum plates are produced using advanced technology, greatly improving peel strength,ensuring no cracking or delamination during processing, shearing, bending, stretching, drilling, or stamping.
Instant Quote
Excellent formability for efficient processing
Copper clad aluminum plates feature outstanding ductility, making them ideal for deep drawing, stamping, andspinning. This formability helps manufacturers reduce processing complexity and improve yield in mass production.
For most applications, tempered or work-hardened materials are used instead of fully annealed plates—balancingstrength and flexibility. This reduces the risk of deformation or cracking during forming.
Meets Complex Shaping Needs Without Cracking
In many projects, buyers are concerned about whether composite materials can handle precise or deep-formed shapes.CCA plates solve this issue with stable forming performance.
With fewer forming defects, compatibility with automatic stamping, and excellent material flexibility, copper cladaluminum plates help enhance production capacity, reduce waste, and enable more flexible structural designs.
Instant Quote
Copper clad aluminum products people like to buy - Chalco stock

Copper-Clad Aluminum Bus Bar
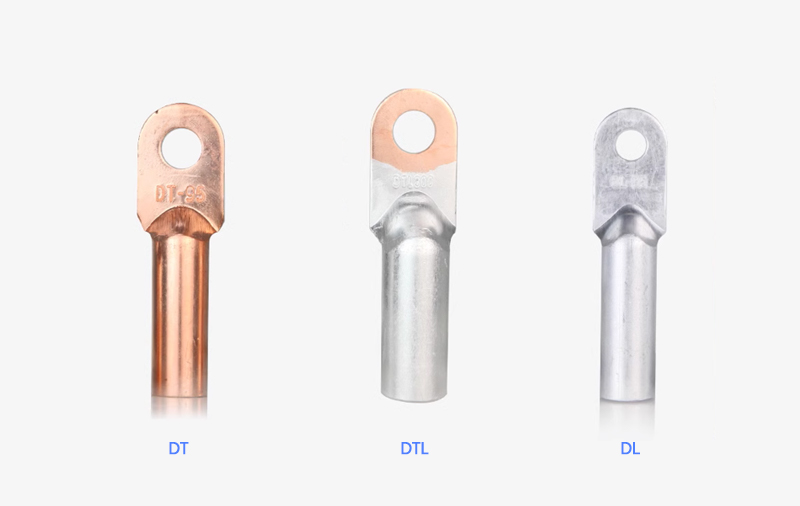
Copper-aluminum Connecting Terminals
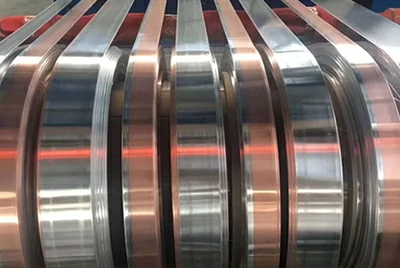
Copper Clad Aluminum Strip
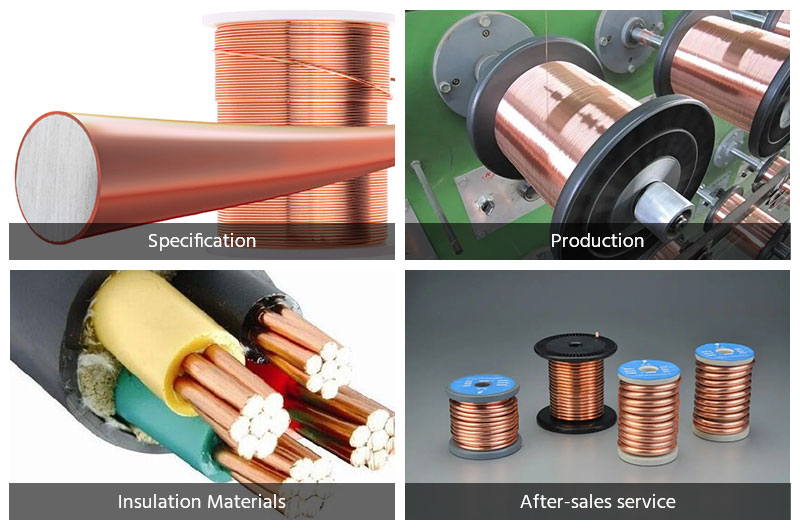
Copper Clad Aluminum Wire
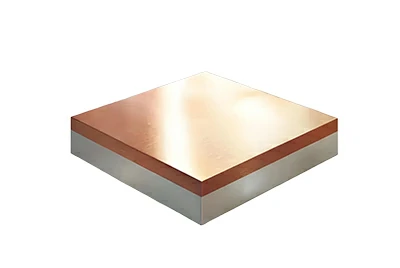
Copper Clad Aluminum Plate
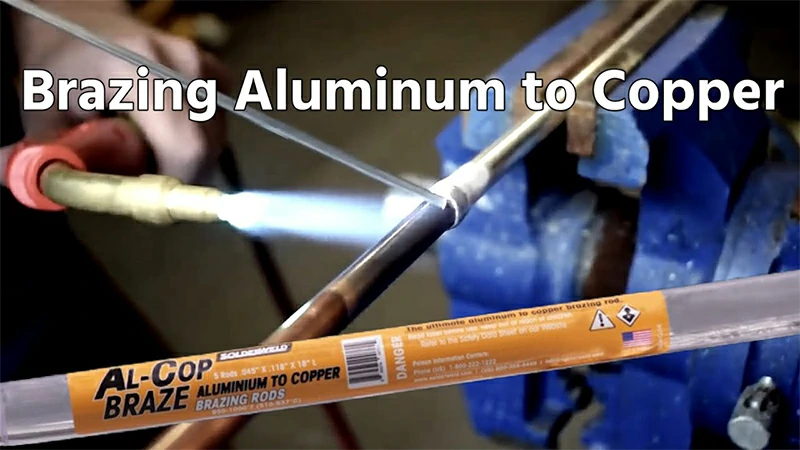
Brazing Aluminum to Copper
Reduce copper costs and improve overall cost-performance
Copper clad aluminum plates maintain excellent conductivity and thermal performance while significantly reducingcopper usage, effectively lowering raw material costs:
- Compared to solid copper, 10% copper clad aluminum only requires 372 kg to replace 1000 kg of copper, savingover 60% on copper material costs.
- The plate thickness can be increased without compromising functionality, offering a more cost-effectivesolution.
- The copper layer provides conductivity, while the lightweight aluminum core reduces overall material costs.
- Custom structural designs and standard connection methods (such as explosion welding, transition bars, boltconnections, etc.) reduce processing difficulties and additional costs associated with copper-aluminumconnections.
Multiple composite processes to meet different application needs
We offer a range of customizable copper clad aluminum composite processes and solutions to meet customer needs forconductivity, strength, accuracy, and cost control, from high strength to lightweight, and electrical to structuralapplications.
Explosion Welding
Ideal for producing large-area, thick composite plates with strong bonding, no delamination, andcorrosion resistance. Can achieve three-layer structures such as Cu/Al, Al/Cu/Al, and Cu/Al/Cu.
Contact us now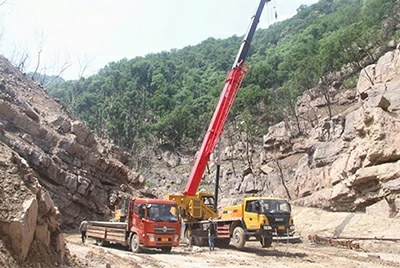
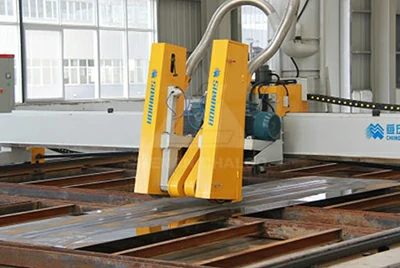
Roll Bonding
Bonds copper and aluminum through cold/hot rolling, ideal for precision processing and used inultra-thin plates and heat dissipation strips.
Contact us nowCast Rolling Composite
Enables efficient continuous production, ideal for large volumes with controllable thickness, widelyused in batteries, automotive, and photovoltaics.
Contact us now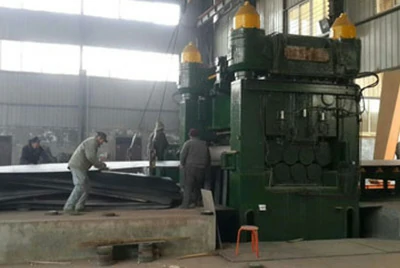
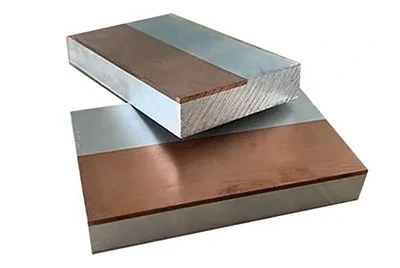
Partial Embedding Technology
Copper is partially embedded, effectively reducing costs while meeting specific conductivity or weldingrequirements. Ideal for battery connection tabs and electronic components.
Contact us nowAnnealing and cleaning of copper clad aluminum
The annealing temperature for copper clad aluminum depends on the thickness but should not exceed 343°C (650°F).
For example, for strip materials less than 0.75mm (0.030"), the annealing temperature can be set to 343°C (650°F).For 1.5mm (0.060") thick strip, if using the "fast" annealing process, the recommended temperature range is 260 to288°C (500-550°F).
If using a slow annealing process for more than an hour, the temperature range should be 232°C (450°F). Furnacetemperature must be carefully controlled to avoid overheating.
Slight discoloration of the copper layer after air annealing can be easily removed with a 10% sulfuric acid or 10%hydrochloric acid solution. The pickling time should be kept short to avoid unnecessary corrosion to the aluminum.
Strict quality control and performance testing
To ensure the quality of each batch of copper clad aluminum composite materials, Chalco conducts both destructiveand non-destructive testing, including:
- Destructive testing: Tensile, impact, bending, torsion, and fatigue tests to ensure material stability underhigh stress.
- Non-destructive testing: Electrochemical corrosion testing, microhardness testing, and corrosion resistancetesting to guarantee long service life and durability.
- Other performance tests: Including shear, peel, tensile shear, and compression tests to ensure bonding strengthand conductivity.
- Electrical performance testing: High-current impact and continuous current tests to ensure stable performance inthe power industry.
All tests comply with international standards and ISO9000 certification, ensuring product reliability andconsistency.
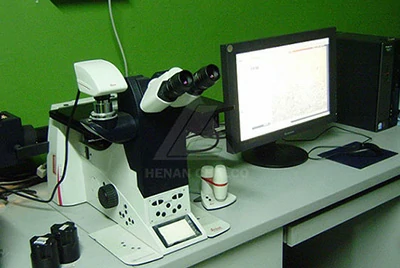
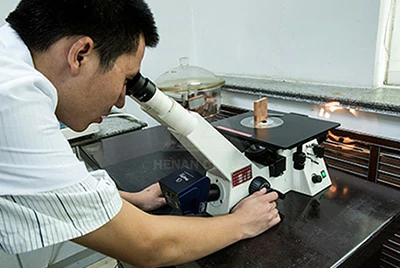
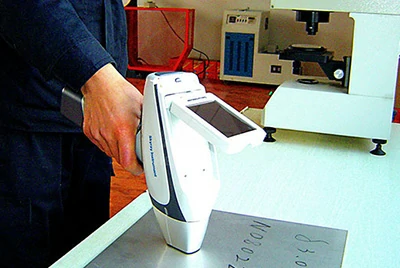
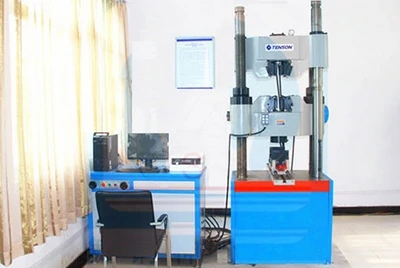
Copper vs aluminum vs copper clad aluminum – comparison
Item | Pure Copper | Pure Aluminum | Copper Clad Aluminum |
Conductivity | Excellent | Good | Close to pure copper |
Cost | High | Low | Significantly lower than pure copper |
Weight | Heavy | Light | Light |
Workability | Easy to process | Moderate | Easy to process |
Typical Uses | High-end electrical | Cost-sensitive projects | General applications like cables, batteries, and LEDs |
Copper Clad Aluminum Packaging and Shipping
Copper clad aluminum materials are packaged using fumigation-free wooden pallets to ensure safety and integrityduring transportation. Each batch undergoes strict quality inspection and is custom cut to customer specifications.Common packaging options include:
- Standard packaging: Each roll of material is wrapped in waterproof plastic film to prevent moisture andcontamination.
- Special packaging: For large or custom products, sturdy wooden boxes or steel straps are used to ensurestability during transport.
- Clear labeling: Each batch is clearly labeled with product information and precautions for easy verification bycustomers.
For shipping, we offer multiple options, including sea freight, air freight, and land transport, with deliverymethods based on customer requirements and urgency to ensure timely delivery.