The melting points, thermal conductivity, and expansion rates of copper and aluminum are very different. This makesbrazing between them technically challenging.
Differences in thermal expansion can cause joints to weaken or crack over time.
That's why choosing the right filler metal, flux, and brazing temperature is critical for a strong, long-lastingbond.
Why choose brazing to join aluminum and copper?
In industrial manufacturing, aluminum and copper each offer distinct advantages. But due to their physicaldifferences, direct welding between them is difficult. Brazing has become one of the most efficient andcost-effective ways to bond these two metals.
- Brazing creates a metallurgical bond between copper and aluminum using filler metal, making it ideal for joiningdissimilar metals with reliable strength.
- It uses lower temperatures than fusion welding, so it doesn't melt the base metals—this helps preserve materialproperties and is safer for heat-sensitive parts.
- The brazed joint has some ductility, which helps absorb stress caused by the metals' differing expansion rates,reducing the risk of cracking over time.
- Induction brazing offers fast, localized heating and high automation—perfect for high-volume, continuousproduction.
- Compared to pure copper systems, brazed copper-aluminum joints significantly reduce both cost and weight,especially in HVAC systems, batteries, and electrical assemblies where conductivity matters.
- It's also ideal for bonding thin-walled copper-aluminum busbars, often used in battery modules, busbars, andpower terminals.
Tip: While brazing aluminum to copper is economical and suitable for mass production, the joint's conductivity islower and it's not ideal for high-stress or corrosive environments. Smart design and surface protection areessential for long-term reliability.
Key parameters for brazing aluminum to copper
- The filler metal must have a melting point lower than both copper (1085°C) and aluminum (660°C). Filler alloyswith a melting range of 450–600°C, such as aluminum-silicon, are commonly used.
- The copper and aluminum surfaces must be thoroughly cleaned of oxides using mechanical abrasion or acidpickling, then coated with a flux based on ammonium fluoride or ammonium chloride.
- Heat the joint to the filler's melting point carefully—avoid overheating the base metals to prevent damage.
How to choose the right filler metal for brazing aluminum to copper
Choosing the right filler metal is critical when brazing aluminum to copper. It directly affects joint strength,conductivity, corrosion resistance, and process stability.
You need to consider filler type, melting point, wetting ability, flux compatibility, and the specific application.
Filler alloy type | Melting range | Key features | Recommended applications |
Aluminum-silicon alloys e.g. Al-Si 12 (AA4047), AlSi10 | 577–585°C | Excellent flow and wetting; helps avoid overheating aluminum and reduces brittle Cu-Al interface | Heat exchangers, thin copper busbars, battery modules |
Zinc-aluminum alloys e.g. ZnAl15, ZnAl22 | 380–420°C | Good conductivity, low cost, low melting point; rare earths can improve corrosion resistance | Low-voltage connections, power terminals, humid environments |
Super Alloy No.1 | Above 600°C | High joint strength, excellent pressure resistance and stability | High-pressure systems, HVAC circuits |
Sn-Zn alloys | 198–260°C | Lead-free, eco-friendly, good wetting, aluminum-like appearance | Electronics, light-duty electrical joints |
Sn-Pb alloys | 183–270°C | Proven performance, low cost, easy to process | General low-temp joints in non-corrosive settings |
Tin-coated filler | 232°C | Low melting point, easy to work with | Signal lines, low-stress sampling points |
Chalco offers a wide range of aluminum-silicon, zinc-aluminum, and flux products for brazing aluminum tocopper—widely used in heat exchangers, battery modules, and electrical assemblies.
Instant QuoteAluminum to Copper Brazing Rod
Chalco's aluminum to copper brazing rod ensures strong, reliable joints for HVAC and electrical use.
Contact us now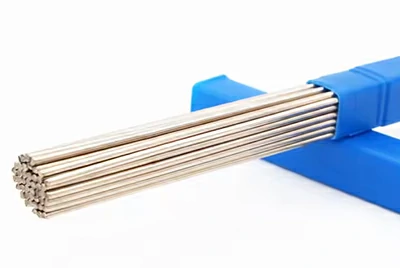
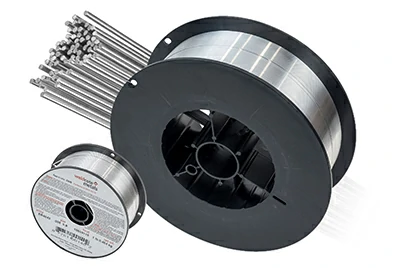
Aluminum Brazing Welding Material
Chalco's best-selling aluminum brazing materials include clad aluminum brazing alloys and self-fluxingaluminum products.
Contact us nowAL 822 Aluminum Brazing Rod
AL 822 aluminum brazing rod offers excellent flowability and wetting performance.
Contact us now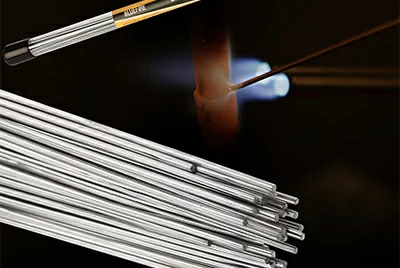

Brazing rings
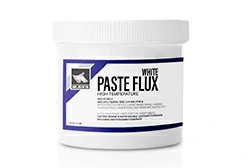
Flux
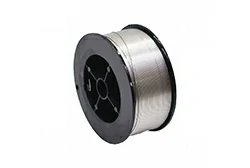
Welding wire
Preparation steps for brazing aluminum to copper
Oxide removal
Use mechanical abrasion or chemical cleaning (acid pickling) to remove oxides and contaminants from aluminum andcopper surfaces. This ensures proper metal-to-metal contact.
Flux application
Apply flux to improve wetting and bonding between the filler metal and base metals. It also prevents re-oxidationand helps form a clean, strong joint.
Surface cleaning
Thoroughly clean both aluminum and copper to remove dirt, grease, and any remaining oxides. A clean surface is keyto effective brazing.
Heat source selection
Choose from flame heating (flexible, ideal for small parts), resistance/induction heating (uniform and efficient forautomated or batch production), or oven heating (for simultaneous multi-joint brazing).
Methods and processes for brazing aluminum to copper
Flame brazing
- Uses aluminum-silicon filler metal (such as Al-Si 12 / AA4047), ideal for small parts and on-site operations.
- Focus the flame on the copper side to avoid overheating the aluminum.
- Advantage: Fast and efficient for light-duty joints, minimizes aluminum damage.
Super Alloy brazing (Super Alloy No.1)
Used in the refrigeration industry to join copper and aluminum tubes. It relies on a special liquid flux and brazingrod to create a strong, durable joint that withstands up to 20,000 PSI.
- Preheat the copper tube, apply heat and flux, then feed in filler metal.
- Advantage: Highly reliable and pressure-resistant, perfect for HVAC systems.
Friction welding
No filler metal needed. Minimal joint prep. The aluminum and copper surfaces are bonded by heat generated throughrotational friction.
Explosion welding
Copper and aluminum are bonded by a high-pressure explosive force that fuses the metals at the interface.
Alloy bonding method
During brazing, a controlled aluminum-copper alloy layer forms at the joint. A stainless steel sleeve may be addedto reinforce the structure.
We offer a full range of copper-aluminum joining solutions, including Al-Si brazing wire, Super Alloy rods,friction weld parts, and explosion bonding technology.
Contact us for technical support and custom product recommendations.
Instant QuoteChalco offers a one-stop copper clad aluminum solution, covering a full range of products includingplates, strips, wires, and busbars.
Contact us now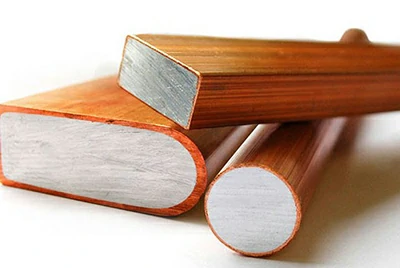
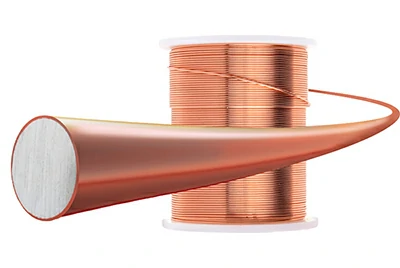
Combines the high conductivity of copper with the lightweight nature of aluminum. Widely used intelecommunications, cables, and electronic wiring.
Contact us nowCopper Clad Aluminium busbar CCA
Delivers excellent conductivity and reduced weight. Ideal for high-current transmission in new energysystems and electrical equipment.
Contact us now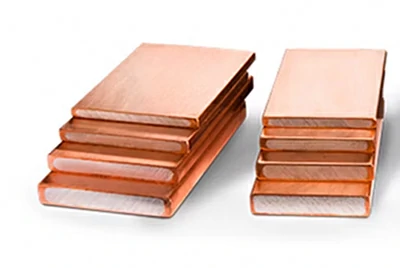
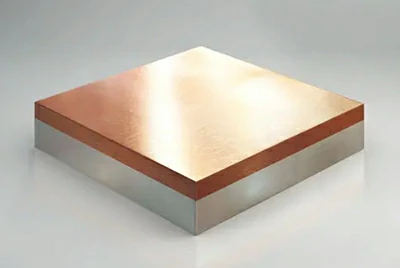
Integrates copper’s superior conductivity with aluminum’s light weight and cost efficiency.
Contact us nowUsed in connectors, grounding straps, and composite conductors—balancing performance and cost in bothelectrical and electronic applications.
Contact us now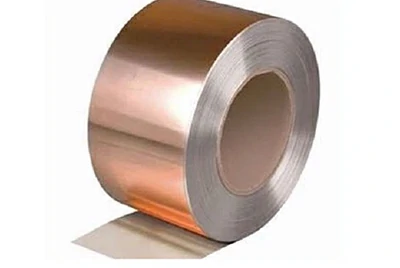
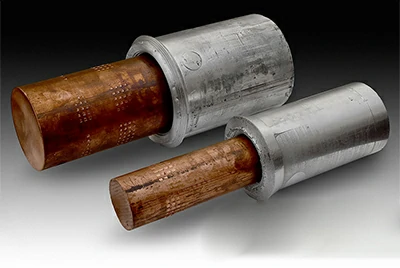
Large and medium-sized copper-aluminum friction welded components
Designed for high-strength applications, offering reliable bonding of dissimilar metals.
Contact us now0.5” ∅ x 2.5” copper-aluminum welded part
Compact friction-welded joint ideal for precision electrical or thermal connections.
Contact us now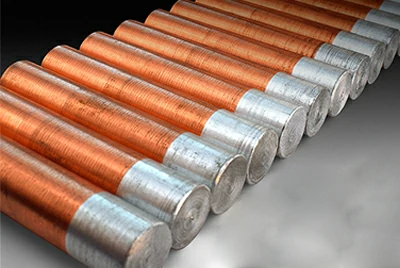
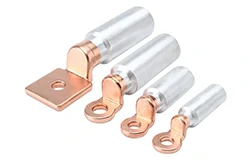
Copper-Aluminium Bimetal Clad Cable Lugs
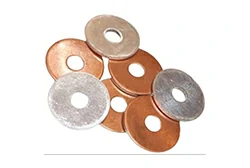
Copper-Aluminium Bimetal Clad Washer
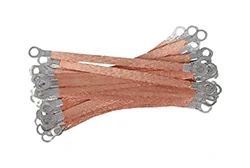
Copper Aluminum Flexible Connectors
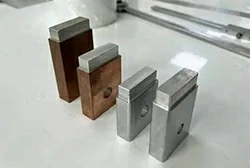
High Speed Rail Grounding Blocks
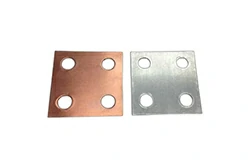
Copper Aluminum Composite Hardware Components
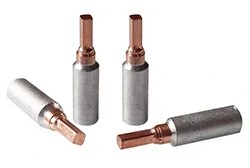
Copper aluminum bimetallic LiB terminal
Applications of brazing aluminum to copper
HVAC & Refrigeration
Brazing aluminum to copper is widely used in joining heat exchangers and refrigeration system tubing—foroutdoor units, condensers, evaporators, and more.
Contact us now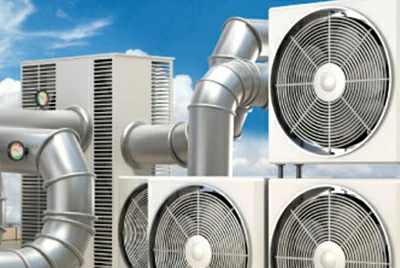
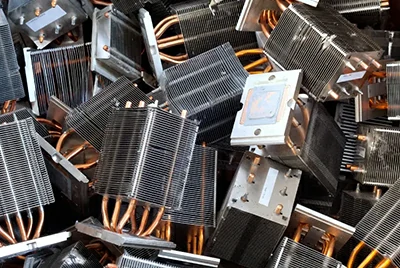
Automotive & Aerospace
Ideal for producing lightweight, high-performance parts such as fuel lines, radiators, and airconditioning modules.
Contact us nowElectrical & Construction
Plays a vital role in manufacturing electrical components and structural parts—used in wire tabs, cableterminals, and mechanical fittings.
Contact us now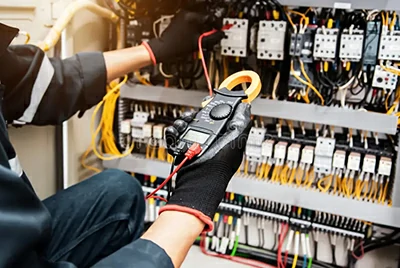
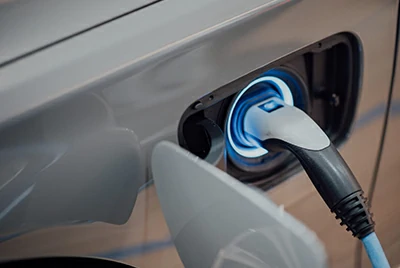
Electric Vehicles & Energy Storage
As EV, HEV, PHEV, and energy storage systems grow, so does the demand for reliable connections betweenaluminum cathodes and copper anodes.
Contact us nowCommon issues and solutions in brazing Aluminum to copper
By applying proper brazing techniques and process control, you can ensure strong, reliable copper-aluminum joints.Key factors include preventing galvanic corrosion, controlling heat input, and selecting the right filler materials.
Overheating the joint
Excessive heating can cause unwanted diffusion and lead to low-melting-point Al-Cu alloys (e.g., Al-Cu33, melts at548°C), which may result in perforation or corrosion.
Solution: Avoid direct flame contact with the joint. Use indirect heating to melt the filler metal, and remove theheat source immediately once flow begins.
Melting point difference between aluminum and copper
Aluminum melts at around 650°C, while copper exceeds 1000°C. Heat transfer from copper to aluminum can cause thealuminum to melt too quickly and damage its structure.
Solution: Aim the flame at the copper side to concentrate heat there. Remove heat as soon as the aluminum nearsmelting.
Poor filler metal wetting
Weak wetting and flow reduce joint integrity and coverage.
Solution: Adjust the temperature or joint gap. Use a filler alloy with better wetting performance for both metals.
Porosity in the joint
Pores can compromise joint strength and sealing.
Solution: Maintain precise temperature control and reduce air entrapment. Improve joint design for better fillerdistribution.
Galvanic corrosion
Copper and aluminum have different electrochemical potentials, which can cause corrosion over time.
Solution: Apply anti-corrosion coatings or isolation layers between the metals to prevent electrochemical reactions.
Chalco offers a complete range of materials, technical support, and solutions for aluminum to copper brazing.
Contact us to discuss your application and get customized recommendations.
Instant QuoteSafety and best practices for brazing aluminum to copper
- Keep the workspace well-ventilated to avoid inhaling harmful fumes.
- Wear heat-resistant gloves, safety goggles, and flame-retardant clothing.
- Use fume extraction or work in an area with proper airflow.
- Equip the area with fire extinguishers (dry powder or CO₂) and remove flammable materials. Provide a safecooling zone for hot tools and parts.
- After brazing, clean flux residues with warm water or solvents. Inspect joints for cracks, voids, or cold welds.
- Apply nickel plating or corrosion-resistant coatings to prevent galvanic corrosion between copper and aluminum.
User guide: practical tips and future outlook for brazing aluminum to copper
In practice, users should follow proven techniques: thoroughly clean and deoxidize the surfaces, select compatiblefiller metals like Al-Si or Zn-Al alloys, and aim the flame at the copper side to avoid overheating the aluminum.
Always follow personal protection guidelines and ensure proper ventilation to maintain safety and weld quality.
To improve brazing skills, users should practice on scrap materials, use appropriate tools and materials, and seekguidance from experienced professionals.
Stay up to date with industry innovations—such as low-temperature alloys and automated brazing systems—which cangreatly improve consistency and joint quality.
Mastering the brazing process takes time, refinement, and hands-on experience. For manufacturers and engineersaiming for high reliability and product performance, mastering aluminum-to-copper brazing is a key step towardcompetitive advantage.