The Tin-Plated Copper Busbar uses T2/TU1 electrolytic copper as the base material, with a 5-15 µm pure tin layer deposited through fully automated continuous electroplating.
- The tin layer isolates air and sulfurous gases, enhancing oxidation resistance and extending service life.
- Improves electrical contact performance, significantly reducing contact resistance.
- Enhances solderability, facilitating easier welding operations.
- Increases corrosion resistance, making it suitable for complex environments.
- Optimizes appearance and labeling for easier engineering applications.
- Balances cost and manufacturing processes, offering significant cost-performance advantages.
Tin-plated copper busbars are widely used in energy storage cabinets, EV battery busbars, distribution cabinets, and rail transit systems.


Tin Plating: The "Performance Enhancer" for Copper Busbars in the Electrical Field
Tin plating on copper busbars is not just a surface treatment, but a comprehensive optimization of material properties, electrical performance, environmental adaptability, and engineering practicality.
By tin plating, the copper busbar experiences significant improvements in oxidation resistance, electrical contact performance, solderability, and corrosion resistance. This is the core reason why it has become a standard configuration in industries such as power, electronics, and communications.
In practical applications, the appropriate tin layer thickness (e.g., 5–20 µm) and process (electroplating or hot-dip) can be chosen based on factors such as environmental humidity, current load, and maintenance requirements to achieve the best cost-performance ratio.
Tin Plating vs. Bare Copper vs. Silver Plating: Which Copper Busbar Offers the Lowest Maintenance Costs?
Property | Bare Copper Busbar | Tin-Plated Copper Busbar | Silver-Plated Copper Busbar |
Conductivity (% IACS) | 100 | 97 | 105 |
Coating Maximum Temperature (°C) | 85 | 120 | 200 |
72h Salt Spray ΔR (µΩ) | 32 | 8 | 3 |
Solderability | ★☆☆ | ★★★ | ★★★ |
Cost (Bare Copper = 1) | 1 | 1.25 | 3-4 |
Typical Industries | General Power Distribution | Energy Storage / UPS / EV | Data Centers / Military |
Recommended Temperature Range (°C) | −10~85 | −40~120 | −55~200 |
Tin-Plated Copper Busbar Specifications
Parameter | Typical Value / Standard | Description |
Conductivity | ≥ 97 % IACS | Nearly identical to bare copper performance |
Coating Thickness | 5-20 µm (ASTM B545) | Choose the coating thickness as needed |
Size Range | Width: 10-120 mm, Thickness: 2-12 mm | Custom bending and perforation based on drawings |
Surface Roughness | Ra ≤ 0.8 µm | Optional insulation coating |
Peel Strength | ≥ 6 N/mm (ISO 2409) | Electroplating adhesion exceeds industry average |
Environmental Compliance | RoHS / REACH | Each batch comes with a Certificate of Analysis (COA) |
Customer Case: Energy Storage Project Saves 18% in 5 Years with Tin-Plated Copper Busbars
Location: California, USA (Coastal Energy Storage Project)
Problem: Bare copper busbars accelerated oxidation due to humidity, requiring 3-4 maintenance checks per year.
Solution: Replaced with 10 µm tin-plated copper busbars (with insulating heat shrink).
Results:
- Average equipment voltage drop reduced by 5 mV.
- Maintenance hours per year reduced from 220 to 40 hours over 3 years.
- Over 5 years, total costs (including procurement, energy consumption, and maintenance) were 18% lower than using bare copper.
Quality and Certifications
SGS/UL Test Reports
Online X-Ray Thickness Measurement: Continuous scanning every 50 meters, with real-time data archiving.
72h Salt Spray Test: ΔR ≤ 10 µΩ; ΔE (color difference) ≤ 1.2.
Third-Party Reports: SGS, TÜV, UL 746B Insulation Test.
Certification Wall (Sample): ISO 9001 | ISO 14001 | UL Certification | CNAS Laboratory Accreditation.
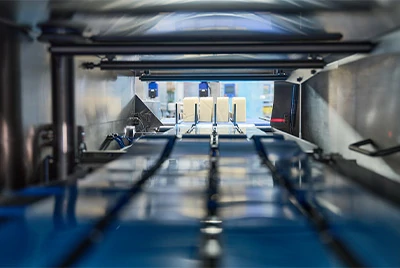
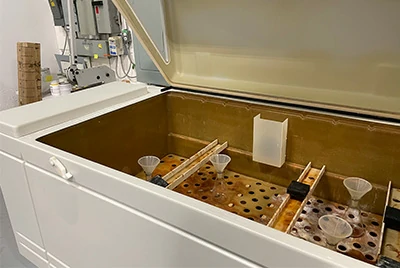
Why Over 680 Customers Choose Us for Tin-Plated Copper Busbars?
Strength Dimension | Data / Facts | Additional Materials |
Capacity & Delivery | Monthly production of 1500 km continuous electroplated copper busbars; standard sizes delivered in 7 days | 30s production line short video |
Process Level | Coating thickness uniformity ±1.2 µm; scrap rate < 0.5% | SPC control curve screenshot |
Global Customers | 48 countries, 680+ engineering projects; including BYD energy storage, Siemens UPS | Logo wall |
Industry Reputation | 2024 UL Motherboard Award – "Best Conductive Copper Busbar Supplier” | Award photo |
Delivery, Payment, and Return Commitment
7 Days Delivery + Worry-Free Trial
Packaging: Vacuum bags + Desiccants + Sulfur-Inhibiting Paper + Fumigation-Free Wooden Boxes.
1:1 Quality Guarantee: If the product does not meet specifications upon arrival, we will cover return shipping and the full refund.
30 Days Credit Term for first orders ≤500 kg (for customers with good credit).
Button A: Request 3 × 50 mm Free Samples Now
Button B: Upload Drawing and Get a Quote in 2 Hours
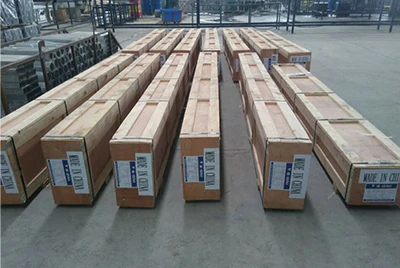
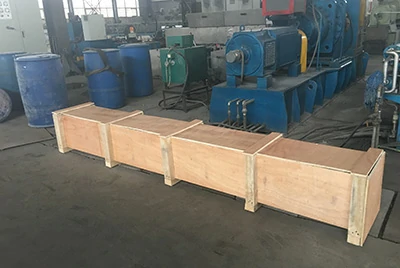