The Nickel-Plated Copper Busbar is coated with a dense nickel layer of 1–20 µm on the surface of T2-grade red copper substrates. This double protection is achieved through electroplating or chemical plating processes, providing high-temperature oxidation resistance and long-lasting corrosion resistance. Compared to traditional tin-plated or silver-plated copper busbars, nickel-plated copper busbars offer a more reliable solution for specific conditions such as corrosion protection, wear resistance, and contact stability.
Comparison of Coated Copper Busbars
Property | Bare Copper Busbar | Nickel-Plated Copper Busbar | Tin-Plated Copper Busbar | Silver-Plated Copper Busbar |
Conductivity (% IACS) | 100 | ≥98 | 97 | 105 |
Maximum Temperature of Coating (°C) | 85 | 300 | 120 | 200 |
Salt Spray Test (72h ΔR, µΩ | 32 | ≤2 | 8 | 3 |
High-Frequency Loss (≤30 kHz) | 1.00× | 0.94× | 0.96× | 0.85× |
Cost (Bare Copper = 1) | 1 | 1.5–2 | 1.25 | 3–4 |
Typical Industries | General Power Distribution | Aerospace / Rail Transport / Energy Storage | Energy Storage / UPS / EV | Data Centers / Military |
Technical Specifications
Parameter | Typical Value / Standard | Description |
Base Material | T2/TU1 Pure Copper | Resistivity ≤0.018 Ω·mm²/m |
Coating Thickness | 1–20 µm (ASTM B487) | Electroplating / Chemical plating available, thickness uniformity ±0.5 µm |
Conductivity | ≥98 % IACS | Overall measurement after hot rolling + coating |
Salt Spray Test | 500 h (ASTM B117) | ΔR ≤2 µΩ, no discoloration |
Operating Temperature | −55 °C ~ +300 °C | Coating does not crack or peel off |
Size Range | Width 10–200 mm × Thickness 2–20 mm | Custom sizes available based on drawing, supports bending and perforation |
Adhesion Strength | ≥6 N/mm (ISO 2409) | Exceeds industry average |
Environmental Compliance | RoHS / REACH | Lead-free, Cadmium-free |
Typical Application Scenarios
- Aerospace busbars can maintain the integrity of the coating under continuous high temperatures of 300 °C and strong vibrations, and are certified by the AS 9100D quality system.
- Rail transit traction systems remain rust-free after long-term exposure to sulfur and high humidity environments, significantly extending maintenance intervals.
- Outdoor energy storage cabinet DC busbars pass a 500-hour salt spray test without developing red rust, making them suitable for long-term operation in coastal and high-salt areas.
- Hydrogen fuel cell stacks naturally resist hydrogen embrittlement, preventing hydrogen-induced corrosion and extending the stack's lifespan.
- High-frequency power modules maintain low contact resistance and good heat dissipation under conditions of <30 kHz, reducing overall temperature rise.


Process and Quality Control
A composite process using electroplating and chemical plating is employed to form a dense, pinhole-free coating.
Online XRF equipment detects 50 measurement points per meter, recording coating thickness in real-time and automatically archiving data.
All products undergo ASTM B117 salt spray and ASTM B487 coating thickness tests to ensure corrosion resistance and uniformity.
The production system is ISO 9001, SGS, and UL certified, with full traceability and the option for third-party witnessed inspections.
Customer Case
European Tier-IV Data Center Busbar Retrofit
Problem: The original silver-plated busbars generated heat under 15 kHz harmonic frequencies, with a PUE of 1.42.
Solution: Replaced with 7 µm nickel-plated copper busbars and brazed heat sinks.
Result: Busbar temperature rise decreased by 5.2 °C, and PUE dropped to 1.37. Annual energy savings of approximately €60,000, with payback within two years.
Packaging and Logistics
Multi-layer packaging consisting of vacuum bags, desiccants, anti-sulfur paper, and non-fumigated wooden boxes prevents coating scratches and oxidation.
Global shipping insurance is provided with sea or air freight options, and a temperature and humidity indicator card is included in the packaging.
An online tracking link is generated immediately after shipment, allowing real-time tracking of logistics.

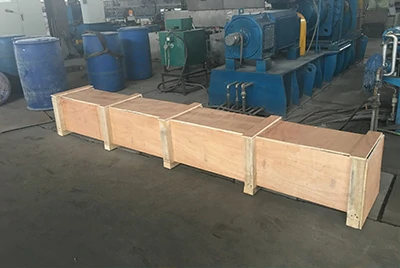
Delivery and Service Guarantee
First batch orders of ≤500 kg will be shipped within 7 days.
30-day payment terms are offered to customers with good credit.
If the product fails inspection, we will cover the return shipping costs and provide a full refund.
A 30-day worry-free trial is offered, with free returns and exchanges during this period.
Frequently Asked Questions(FAQ)
Q1: Can nickel-plated copper busbars directly replace existing tin-plated busbars?
A: The dimensions and mechanical properties are identical, and it is safe to replace them as long as contact resistance and reflow soldering processes are re-verified.
Q2: Will the nickel layer increase losses in high-frequency applications?
A: Nickel layers ≤10 µm have a negligible impact on frequencies ≤30 kHz. For frequencies >100 kHz, we recommend evaluating flexible tin-plating or pure copper solutions.
Q3: How do we assess the durability of the nickel layer?
A: We provide ASTM B117 salt spray and IPC-TM-650 soldering reliability test reports, and we also support third-party on-site inspections.