Aluminum panels are widely used in composite panels, honeycomb panels, insulated panels, signage, transportation, and interior decoration due to their lightweight, durability, excellent weather resistance, and versatile design options.
As a leading aluminum material supplier, Chalco provides high-quality aluminum coils and sheets suitable for a variety of panel types including ACP, honeycomb, insulated, and decorative panels. We offer a full range of aluminum alloys such as 1060, 1100, 3003, 3105, and 5005 with PE, PVDF, and FEVE coatings. Our products ensure stable lamination, strong coating adhesion, superior surface finish, and compliance with international fire safety standards, helping manufacturers deliver consistent quality and customized solutions across diverse industrial and commercial applications.
Product overview: brief introduction of Chalco's aluminum skin panel products
Available Alloys: 1100, 1060, 3003, 3105, 5005
Tempers: H14, H16, O
Thickness Range: 0.18 mm to 0.50 mm
Surface Options: Mill Finish, PE Coated, PVDF Coated, FEVE Coated
Coating Configuration: Single-side or double-side coating, optional backside primer
Standard Widths: 1000 mm, 1220 mm, 1250 mm, 1500 mm
Supply Form: Coil or Cut-to-Length Sheet
Compatibility: Suitable for lamination with LDPE, FR, and A2 cores
Specifications: ASTM B209, EN 485, GB/T 3880, AAMA 2605/2604
Alloy options for Chalco aluminum panel products
Chalco provides a variety of aluminum alloys engineered for optimal performance in composite, honeycomb, and other panel applications. Each alloy offers a tailored balance of strength, formability, corrosion resistance, and coating compatibility to meet diverse project needs.Quick Quote
-
1100 Aluminum sheet coil
Key Features: Excellent corrosion resistance, high ductility, soft texture.
Typical Applications: Interior decorative ACP panels, signage, where maximum formability is needed.
Advantages: Lightweight, easy to fabricate, excellent for creative shaping.
-
1060 Aluminum sheet coil
Key Features: Over 99.6% aluminum purity, exceptional conductivity and formability.
Typical Applications: ACP panels for indoor decoration, advertising boards, and applications requiring high flexibility.
Advantages: Economical choice with superior workability.
-
3003 Aluminum sheet coil
Key Features: Excellent corrosion resistance, good formability, moderate strength.
Typical Applications: Standard ACP panels for interior decoration, signage, and non-structural exterior facades.
Advantages: Cost-effective, easy for lamination and coating.
-
3004 Aluminum sheet coil
Key Features: Higher strength than 3003 with comparable corrosion resistance and formability.
Typical Applications: ACP panels requiring improved mechanical strength, especially in larger dimensions or more demanding environments.
Advantages: Better structural integrity while maintaining good formability.
-
3104 Aluminum sheet coil
Key Features: Higher strength than 3003 and 3004, with excellent formability and good corrosion resistance.
Typical Applications: ACP panels for high-rise building facades, transportation signage, and structural curtain walls.
Advantages: Stronger structural integrity, suitable for demanding architectural applications.
-
3105 Aluminum sheet coil
Key Features: Enhanced strength compared to 3003, improved surface finish for coating.
Typical Applications: High-strength ACP panels, exterior cladding subject to wind load, weather-exposed signage.
Advantages: Balances strength, corrosion resistance, and surface aesthetics.
-
5005 Aluminum sheet coil
Key Features: Excellent corrosion resistance, superior weatherability, color consistency after anodizing or PVDF coating.
Typical Applications: Premium-grade ACP panels for high-end architecture, curtain walls, and long-term outdoor installations.
Advantages: Ideal for projects requiring long-term durability and superior aesthetic performance.
Coating system and suface finish option for Chalco aluminum sheet coil panel
Chalco provides a complete range of surface treatment and coating solutions for aluminum coils and sheets used in ACP (Aluminum Composite Panel) manufacturing. Our finishing capabilities ensure excellent bonding performance, decorative effects, durability, and compatibility with a wide range of indoor and outdoor applications. Quick Quote
Coating Type | Full Name | Key Features | Typical Application |
PE Coating | Polyester | Bright colors, cost-effective, average weather resistance | Indoor decoration, signage, short-term outdoor use |
PVDF Coating | Polyvinylidene Fluoride | Excellent weather resistance, corrosion resistance, long-lasting color | Exterior walls, curtain walls, high-end architecture |
Nano Coating | Nanometer Coating | Self-cleaning, anti-fouling, oil-resistant, pollution-resistant | Hospital exteriors, high-end commercial buildings |
FEVE Coating | Fluoroethylene Vinyl Ether | Outstanding color retention, excellent durability | Premium building exteriors, exposed facades |
Chalco supports one-side and two-side coating options, customized coating thickness, and primer layers for enhanced composite strength.
- Color Customization: Pantone or customer-supplied sample matching
- Gloss Control: Matte, semi-matt, high gloss, mirror finish options
- Texture Customization: Pattern depth, orientation, and 3D effects available
- Proofing Service: Rapid sample preparation based on provided drawings or samples
Chalco offers a variety of surface finish solutions on aluminum coils and sheets, specifically engineered for ACP (Aluminum Composite Panel) production. Our finishing capabilities enable manufacturers to create panels with diverse decorative styles and reliable outdoor performance. Quick Quote
Color solid color/high gloss color
Wide color selection (Pantone matching available), adjustable gloss levels (matte, semi-gloss, high-gloss), good weatherability, easy to process.
Typical applications: Storefront ACP panels, billboard skins, interior partitions, industrial wall cladding.
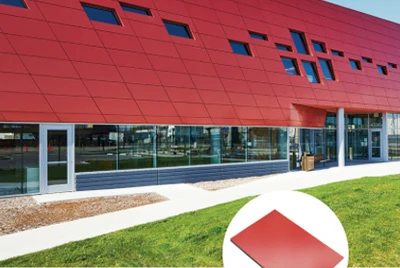
Wood & Stone Look
Through thermal transfer or lamination, the natural texture of wood or stone is reproduced on the surface of ACP board, achieving both visual simulation and actual lightness. It is an environmentally friendly alternative to traditional wood and stone decoration.
Typical applications: Residential ACP facades, commercial storefront coverings, hotel interiors.
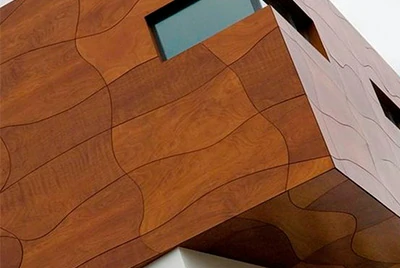
Mirror Finish
Mirror ACP uses a high-gloss coating or reflective film, which has a strong reflective effect and a modern feel, and is often used to create a space extension and technological atmosphere.
Typical applications: ACP panels in mall atriums, luxury store fronts, and exhibition spaces.
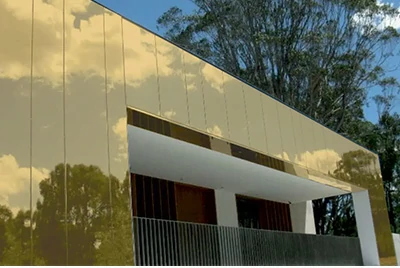
Brushed & Metallic Texture
The surface is mechanically brushed to show a delicate metal texture, and then protected with an anti-corrosion coating. It has a sense of technology and luxury, and looks calm and elegant.
Typical applications: Elevator interiors, corporate lobby walls, premium ACP architectural finishes.
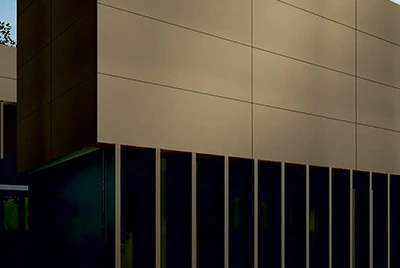
Creative & Textured Finishes
3D embossed patterns, customized relief textures, and partial printing technologies. Adds tactile dimension and visual depth to ACP aluminum skins.
Typical applications: Cultural buildings, branded commercial spaces, high-end customized ACP projects.
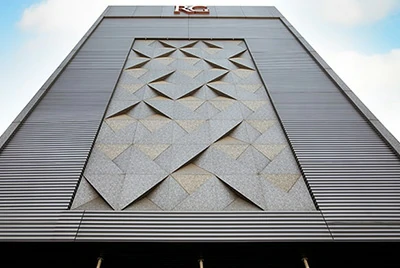
Chalco production capabilities for aluminum skin panel
As a professional supplier of aluminum materials for ACP panel manufacturing, Chalco combines advanced production lines, strict quality control, and flexible customization services to meet the evolving demands of global customers.Quick Quote
Aluminum coil rolling and processing
Chalco ACP sheets can provide standard sheets, and are more adept at responding to customized requirements such as multiple specifications, multiple core materials, and large and small batches, helping customers quickly implement engineering projects:
- Alloy Range: 1xxx, 3xxx, 5xxx series (1100, 1060, 3003, 3004, 3104, 3105, 5005, etc.)
- Thickness Capability: 0.18 mm – 0.50 mm
- Width Capability: Up to 1600 mm
- Flatness Control: Tolerance within ±0.5 mm across full width, ensuring excellent lamination results
- Cut-to-Length Service: Available for sheet production with precise dimensional control
Coating and surface finishing capabilities
- Coating Systems Supported: PE, PVDF, FEVE, Nano
- Coating Type: Single-side coating, double-side coating, service primer on backside
- Coating Thickness: Customized based on project requirements (Typical top coat 20–28 microns; primer 5–8 microns)
- Color Customization: Pantone matching, gloss level adjustment (matte, semi-gloss, high-gloss, mirror finish)
- Surface Effects: Solid colors, brushed, wood grain, stone texture, mirror reflection, embossed textures
Quality control and certification
- Base Material Standards: ASTM B209, EN 485-2, GB/T 3880
- Coating Standards: AAMA 2605 / 2604 compliance for PVDF-coated materials
- Process Control: Continuous annealing for mechanical property uniformity Online thickness and width monitoring
- Color consistency inspection (ΔE≤2.0 for architectural-grade panels)
- Cross-hatch adhesion tests for coating reliability
- Fire Safety Compliance Support: Materials suitable for LDPE, FR, and A2 ACP systems
10 typical applications of Chalco aluminum skin panel
Chalco's prepainted aluminum skin panels are designed for composite panel lamination and are widely used across architecture, transportation, industrial construction, and signage industries. With excellent flatness, coating durability, and compatibility with various core materials, these aluminum sheets serve as ideal facing materials for a wide range of functional and decorative applications.
-
Aluminum Composite Panels (ACP)
Used for building facades, cladding, interior wall panels, and signage, offering excellent aesthetics and weather resistance.Quick Quote
-
Aluminum Honeycomb Panels
Applied in curtain walls, ceilings, transportation interiors (trains, subways), combining lightweight with high structural strength.Quick Quote
-
Fire-Retardant Composite Panels (B1/A2)
Ideal for public buildings like airports, hospitals, and schools requiring strict fire compliance (EN 13501-1, ASTM E84, GB 8624).Quick Quote
-
Solid Aluminum Panel Systems
Used for building facades, cladding, interior wall panels, and signage, offering excellent aesthetics and weather resistance.Quick Quote
-
Corrugated Aluminum Panel
Widely used in industrial roofing, warehouse cladding, and internal partitions due to their structural stiffness and durability.Quick Quote
-
Insulated Sandwich Panels
Used in cold storage, cleanrooms, and modular containers by laminating with PU, PIR, or mineral wool cores for thermal insulation.Quick Quote
-
Decorative Aluminum Panels
Ideal for custom interior elements such as furniture panels, cabinetry, and feature walls in residential and commercial spaces.Quick Quote
-
Interior Decoration Panels
Used in ceiling panels, wall coverings, and modern furniture applications to provide clean aesthetics and functional surfaces.Quick Quote
-
Transportation Industry
Applied in truck bodies, trailer side panels, and railway interiors where lightweight and corrosion resistance are critical.Quick Quote
-
Signage and Advertising Boards
Provides a smooth surface with vivid colors and strong weatherability, perfect for outdoor signage and branding displays.Quick Quote
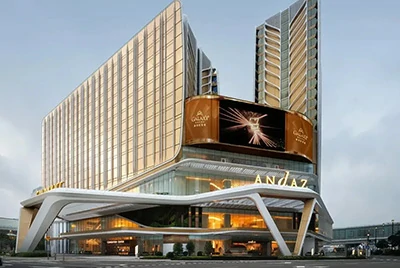
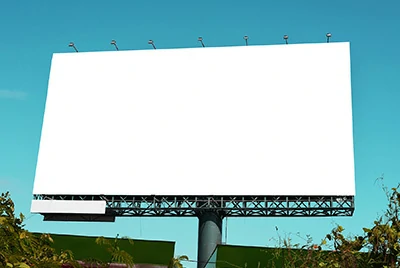
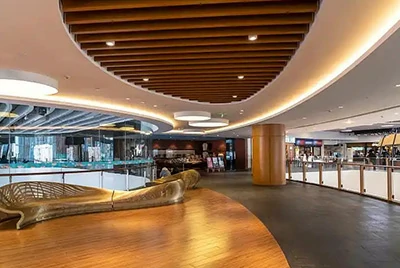
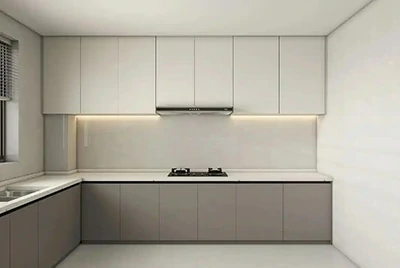
Pricing factors and selection guide for aluminum panel materials
Aluminum coils and sheets serve as key surface materials for a wide range of composite panels, including aluminum composite panels (ACP), honeycomb panels, insulated sandwich panels, corrugated panels, and decorative aluminum boards. Understanding the pricing factors behind aluminum skins enables manufacturers and project planners to make cost-effective, performance-driven material selections across various architectural, industrial, and interior applications.Quick Quote
Application | Recommended Alloy & Coating | Key Considerations |
Building Facade / ACP | 3003 / 5005 + PVDF | High durability, UV resistance, fire safety |
Interior Decorative Panels | 1100 / 3003 + PE or FEVE | Aesthetic finish, cost-effective, light-duty use |
Fire-Retardant Panels (FR, A2) | 3003 / 5005 + PVDF/Nano | Fire compliance (EN 13501-1), lamination adhesion |
Transportation Panels | 3003 + PE/PVDF | Lightweight, corrosion-resistant, vibration-resistant |
Signage and Advertising Boards | 1100 / 3003 + PE or FEVE | Bright colors, smoothness, UV/weather resistance |
Honeycomb & Corrugated Panels | 3003 + PVDF/PE | Structural stability, good flatness, compatibility |
Insulated Sandwich Panels | 1100 / 3003 + PE | Easy lamination with PU or mineral wool |
Practical selection advice for ACP manufacturers
- Match coating type to application lifespan (PE for interior, PVDF for outdoor).
- Use standard sizes/colors when possible to reduce lead time and cost.
- Discuss core compatibility (LDPE, FR, A2) early in design to avoid rework.
- Opt for batch orders to reduce per-unit cost through scale.
Performance advantages of Chalco aluminum coil & sheet for composite panel
Chalco offers high-quality color-coated panels ideal for lamination onto various composite boards such as ACP, honeycomb, and fire-retardant panels. Compatible with multiple core materials (LDPE, FR, A2), our panels provide reliable performance and versatile design options.
- Superior Flatness and Lamination Stability: Ensures smooth lamination and strong composite bonds without delamination.
- Excellent Coating Adhesion and Durability: Advanced coatings deliver strong adhesion, UV resistance, and weatherability.
- Fire Safety Compatibility: Materials fully compatible with LDPE, FR, and A2 cores, supporting compliance with EN 13501-1, ASTM E84, and GB 8624 fire standards.
- Fire Safety Compliance: Meets EN 13501-1, ASTM E84, and GB 8624 standards with suitable core compatibility.
- Customizable Specifications: Available in various thicknesses, widths, coatings, and gloss levels.
- Diverse Surface Finishes: Solid colors, wood grain, stone, metallic, and textured options available.
- Reliable Supply and Quality: Consistent quality and timely delivery for large projects.
Typical technical specifications for Chalco aluminum panel
Parameter | Unit | Typical Value |
Alloy | — | 1100, 1060, 3003, 3004, 3104, 3105, 5005 |
Temper | — | H14, H16, O |
Thickness | mm | 0.18 – 0.50 mm |
Width | mm | 1000 / 1220 / 1250 / 1500 (customizable) |
Surface Finish | — | PE / PVDF / FEVE / Nano coatings; solid, mirror, brushed, wood grain, stone textures |
Coating Thickness | μm | Top coat: 20–28μm, Primer: 5–8μm |
Gloss Level | GU | 20–80 (Matte to High Gloss) |
Standards Compliance | — | ASTM B209, EN 485-2, AAMA 2605/2604 |
FAQ – Frequently Asked Questions about aluminum panel skin purchasing
Can you supply customized colors and gloss levels?
Yes. Chalco supports Pantone color matching, gloss customization, and texture development for aluminum coils and sheets.
What is the minimum order quantity (MOQ)?
Standard MOQ starts from 3–5 tons, depending on alloy type and coating system. Small batch production can be supported for special projects.
Can you provide quality certifications?
Yes. We can supply inspection certificates (COC), ASTM/EN compliance reports, RoHS/REACH declarations, and project-specific quality reports.
How do you package aluminum coils for export?
Protective film + waterproof wrapping + reinforced wooden pallets, fully meeting export shipping standards.
What is your typical production lead time?
Generally 7–20 working days depending on order size and customization requirements.
Chalco can provide you the most comprehensive inventory of aluminum products and can also supply you customized products. Precise quotation will be provided within 24 hours.
Get a quote