ER5356 aluminum welding wire is a general-purpose aluminum-magnesium filler metal containing approximately 5% magnesium. It is specifically designed for welding 5xxx series aluminum alloys and is also compatible with certain 6xxx series alloys. Featuring good mechanical properties, excellent corrosion resistance, and outstanding welding stability, it is widely used in the fabrication and repair of aluminum components in shipbuilding, pressure vessels, transportation equipment, and architectural structures. Quick Quote
ER5356 welding wire specifications
- ANSI/AWS A5.10 ER5356
- ASME SFA-5.10 ER5356
- ISO 9001:2000
Types of ER5356 welding wire available from Chalco
5356 welding wire
Most common type, suitable for TIG or MIG welding. Can be matched with various base metal thicknesses according to wire diameter. Widely used in structural welding, shipbuilding, automotive, and architectural aluminum fabrication.
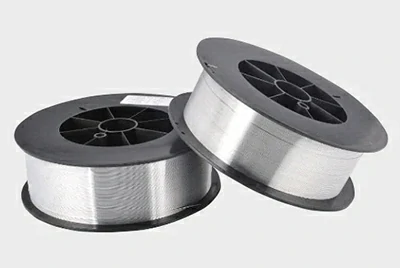
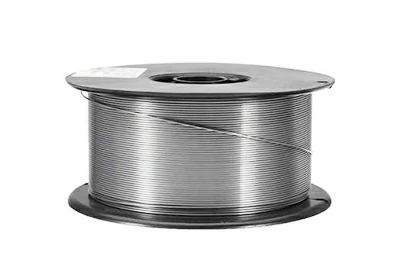
5356 MIG wire
Used for GMAW (MIG) welding processes, commonly paired with semi-automatic welding guns. Suitable for welding medium to thick aluminum alloy plates, often seen in applications such as automotive trailers, storage tanks, and structural frames.
5356 aluminum filler rod
Used for GTAW (TIG) welding processes, suitable for precision welding scenarios such as thin sheets and workpieces requiring high weld appearance quality, including decorative panels and pressure vessels.
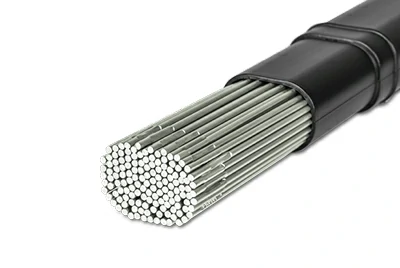
Main features of 5356 welding wire
- Good strength: weld tensile strength can reach approximately 38, 000 psi (262 MPa), meeting high structural strength requirements.
- Excellent corrosion resistance: suitable for marine and chemical environments, with strong weld corrosion resistance.
- Stable welding performance: excellent arc stability, low spatter, and smooth welding process.
- Anodizing-friendly: welds appear white, making them suitable for post-weld anodizing, with color close to the base metal.
- Wide compatibility: recommended for welding 5050, 5052, 5083, 5356, 5454, 5456 aluminum alloys, and also applicable for structural welding of some 6xxx series alloys such as 6061 and 6063.
The main applications of ER5356 welding wire
- Shipbuilding: welding structural components such as hulls, bulkheads, and railings, resisting seawater corrosion.
- Pressure vessels: used for manufacturing aluminum oil tanks, water tanks, liquid containers, and other equipment.
- Automotive and trailer structures: welding lightweight aluminum components such as frames, chassis, and boxes.
- Building structures: welding and assembling architectural aluminum profiles, decorative structures, etc.
- Sports equipment and industrial components: welding aluminum tubes, brackets, mechanical parts, etc.


Chalco 5356 welding wire sizes and packaging
Wire Diameter | Metric Size | Welding Method | Packaging Type | Typical Weight Options | Typical Length per Unit |
0.030" | 0.8 mm | MIG | Spool | 0.5 kg / 2 lb / 5 kg | ~400–500 m / spool |
0.035" | 0.9 mm | MIG | Spool | 0.5 kg / 2 lb / 5 kg | ~350–450 m / spool |
0.040" | 1.0 mm | MIG | Spool | 1 kg / 5 kg | ~300–400 m / spool |
3/64" | 1.2 mm | MIG / TIG | Spool / Cut Length | 2 kg / 7 kg / 15 kg | Spool: ~250 m / Cut: 1 m/rod |
1/16" | 1.6 mm | MIG / TIG | Spool / Cut Length | 5 kg / 15 kg | Spool: ~160 m / Cut: 1 m/rod |
3/32" | 2.4 mm | TIG | Cut Length (straight rod) | 5 kg / box | ~1 m/rod, ~80–100 rods/box |
1/8" | 3.2 mm | TIG | Cut Length (straight rod) | 5 kg / box | ~1 m/rod, ~50–70 rods/box |
5/32" | 4.0 mm | TIG | Cut Length (straight rod) | 5–10 kg / box | ~1 m/rod, ~40–60 rods/box |
If you cannot find the suitable size, please contact us promptly. Quick Quote
Chalco 5356 welding wire's physical properties
- Solidus temperature: 1060°F (571°C)
- Liquidus temperature: 1175°F (635°C)
- Density: 0.096 lbs/in³ (approximately 2.66 g/cm³)
- Anodized color: White
- Thermal conductivity: approximately 130 W/m·K
- Electrical conductivity: approximately 34% IACS
Typical GMAW Welding Procedures for 5356 Aluminum Wire (DCEP)
Wire Diameter (in) | Amperage (A) | Voltage (V) | Travel Speed (ipm) | Argon Flow (cfh) |
0.03 | 60 – 175 | 15 – 24 | 25 – 45 | 25 – 30 |
0.035 | 70 – 185 | 15 – 27 | 25 – 40 | 30 – 35 |
3/64 | 125 – 260 | 20 – 29 | 24 – 35 | 35 – 45 |
1/16 | 170 – 300 | 24 – 30 | 28 – 38 | 45 – 55 |
3/32 | 275 – 400 | 26 – 31 | 14 – 20 | 60 – 75 |
Typical GTAW Welding Procedures for 5356 Aluminum Wire
The following is a typical welding parameter table for 5356 aluminum welding wire in GTAW (Tungsten Inert Gas Welding) process, suitable for ACHF (Alternating Current High-Frequency Start), using pure tungsten or zirconium tungsten electrodes with a hemispherical electrode tip.
Filler Wire Size (in) | Tungsten Size (in) | Amps | Volts | Gas Cup Size | Argon Flow (cfh) | Base Thickness (in) |
1/16" | 1/16" | 60 – 80 | 15 | 3/8" | 20 | 1/16" |
3/32" | 3/32" | 125 – 160 | 15 | 3/8" | 20 | 1/8" |
1/8" | 1/8" | 190 – 220 | 15 | 7/16" | 20 | 3/16" |
5/32" | 5/32" | 200 – 300 | 15 | 1/2" | 25 | 1/4" |
3/16" | 3/16" | 330 – 380 | 15–20 | 5/8" | 25 | 3/8" |
1/4" | 1/4" | 400 – 450 | 25 | 5/8" | 25 | 1/2" |
Analysis of weld seam performance of 5356 welding Wire
Weld seam strength: The welds produced by ER5356 welding wire have medium to high strength, with tensile strength typically ranging from 260 to 300 MPa, meeting the structural load-bearing requirements of applications like shipbuilding and tanks.
Ductility and toughness: With moderate elongation (~17%), the weld seams are less prone to brittle fracture, making them suitable for applications that need to withstand impact and vibration loads.
Crack resistance: Due to its high magnesium content and good plasticity, the weld seams have a low tendency for hot cracking, making it particularly suitable for thick plates and multi-pass welding.
Anodizing compatibility: After anodizing, the weld seams appear "silver-white, " closely matching the parent material, making them suitable for workpieces with high appearance requirements.
Fatigue performance: Better than 4043 welding wire, making it ideal for structures subjected to cyclical loads, such as trailers and compression vessels.
Base material compatibility and matching of ER5356 welding wire
Base Material Alloy (Recommended) | Description |
5052, 5056, 5083 | Optimal match, magnesium-based alloys with a balance of strength and corrosion resistance. |
5454, 5456, 5356 | Same-series welding, excellent compatibility. |
6061, 6063 | Usable, but 6061 requires control of hot cracking tendency. |
Cast Aluminum (e.g., A356) | Not recommended, prone to hot cracking. |
High Zinc 7xxx Series | High crack sensitivity, recommend using ER5556 or 4643 |
Recommendation: When welding 6061 and other 6xxx series alloys, control heat input, perform preheating, and avoid large transitions between thick and thin sections.
Performance differences of ER5356 welding wire in different welding processes
Item | MIG Welding (GMAW) | TIG Welding (GTAW) |
Suitable Applications | Medium to thick plate welding, mass production | Precision parts, small size, high appearance requirements |
Operating Efficiency | High, suitable for automatic/semi-automatic welding | Slow, manual control with high weld quality |
Weld Appearance | Average, requires polishing | Smooth and aesthetically pleasing, suitable for decorative parts |
Recommended Wire Diameter | 0.030" ~ 3/64" | 3/64" ~ 1/8" |
Heat Affected Zone Control | Relatively large | Precise control, low heat input |
Typical defects and prevention suggestions
Defect Type | Possible Causes | Prevention Methods |
Hot Cracking | Base material and weld metal composition difference or stress concentration | Match appropriate filler wire, control heat input, multi-pass welding |
Porosity | Moisture, oxide film, or contaminants | Clean base material surface, store filler wire dry |
Weld Inclusions | Improper operation, metal spatter | Stabilize current and voltage, control travel speed and weaving |
Lack of Fusion | Insufficient welding energy, incorrect angle | Adjust torch angle, increase current or welding speed |
Comparison of properties of different aluminum welding wire alloys
Alloy | Strength | Corrosion Resistance | Anodized Color | Hot Cracking Tendency | Recommended Base Materials |
ER5356 | Medium-High | Excellent | White | Low | 5xxx series alloys, some 6xxx (e.g., 6061) |
ER4043 | Medium | Fair | Dark Grey | Very Low | 6xxx series (6061/6063), some cast aluminum |
ER5183 | High | Excellent | Silver Grey | Low | 5083, 5086, and other high-strength corrosion-resistant aluminum alloys |
ER5556 | High | Excellent | Grey-White | Moderate | High-stress structures, ships, thick plate welding |
Frequently asked questions about ER5356 welding wire
What is the price of ER5356 aluminum welding wire?
The price will vary depending on the wire diameter, packaging specifications, order quantity, and fluctuations in the aluminum ingot market. It is typically priced per kilogram or per coil. Please contact us for real-time pricing and discount policies. Quick Quote
What are the packaging forms for ER5356 welding wire?
- MIG welding wire: Packaged in plastic or metal spools, with common specifications of 1kg, 5kg, 7kg, 15kg, 20kg, etc.
- TIG welding rods: Packaged as straight rods (36 inches or 1 meter) in paper boxes or shrink-wrapped tubes, with labeled identification.
All packaging can be customized according to export requirements, including moisture-proofing, desiccants, and label customization.
Can ER5356 welding wire be used for anodizing surface treatment?
Yes. The welds made with ER5356 welding wire are white in color and closely resemble the base material after anodizing, making it suitable for decorative welding projects.
What aluminum alloys is ER5356 suitable for welding?
It is recommended for welding 5052, 5083, 5454, 5356, and other 5xxx series aluminum alloys. It can also be used for some 6xxx alloys (such as 6061), but caution is needed when welding cast aluminum or high-zinc alloys. It is advised to use other wires for these.
What is the difference between ER5356 and ER4043 welding wire?
ER5356 welding wire offers higher strength and corrosion resistance, making it suitable for structural components and marine applications. ER4043 welding wire has better fluidity and a lower tendency for hot cracking, making it ideal for welding cast aluminum and base materials like 6061. The anodized color of ER4043 is darker.
Do you provide samples? What is the MOQ?
Yes, we support small batch sample requests for testing. The minimum order quantity for most specifications is 5–10 kg, and for special or custom specifications, the MOQ can be negotiated.
Is the welding wire certified?
Yes. Our ER5356 welding wire complies with AWS A5.10 / ASME SFA-5.10 standards and can provide certifications such as ISO 9001, RoHS, REACH, MTC, etc.
What should be considered when storing ER5356 welding wire?
It should be stored in a dry, ventilated area to prevent moisture exposure. TIG rods are recommended to be kept in their original packaging, while MIG welding wire should be sealed with a desiccant if not used shortly after opening.
Can the packaging or labels be customized for a project?
Yes. We support custom labels with content such as brand, specification, batch number, barcode, anti-counterfeit signs, and can also apply English labels or customer logos based on export requirements.
What after-sales services do you provide?
We offer technical support, alloy selection advice, welding process parameter guidance, and assist in providing third-party testing reports. If there are quality issues, we will respond and address them promptly.