In the modern metal processing industry, laser cutting has become an important process for precision processing of aluminum alloy products. Compared with traditional cutting methods, its advantages such as high precision, contactless processing, and smooth incision make it widely used in the processing of aluminum plates, aluminum tubes, aluminum profiles and complex special-shaped parts. It can accurately realize a variety of shapes such as circles, rectangles, gear structures, hollow patterns, and perforated grids to meet diverse design needs.
As a professional aluminum alloy production and processing company, we provide customized laser cutting services, which are widely used in aerospace, automobile manufacturing, electronic equipment, architectural decoration and other fields. With advanced technology, we can accurately cut large-format aluminum plates, special-shaped aluminum tubes, and complex aluminum profiles, and support engraving, hollowing, and logo customization to meet the needs of precision mechanical parts, decorative panels, industrial structural parts, etc., ensuring high-quality and efficient processing solutions.
Advantages of aluminum laser cutting
As the demand for high-precision and high-efficiency processing grows, laser cutting has been widely used in industries such as aerospace, automobile manufacturing, electronic equipment, and architectural decoration due to its high precision, fast speed, and strong adaptability.
Aluminum alloy has become an important material for industrial structures and precision parts due to its advantages of light weight, high strength and corrosion resistance. Laser cutting can be processed without contact, with smooth incisions and stable precision, meeting the requirements of complex shapes and high quality.
- High precision: cutting error can be controlled within ±.005'', meeting the needs of precision processing.
- High speed and high efficiency: Faster than traditional cutting methods (such as plasma and water jet), suitable for mass production.
- Smooth cuts: Cut edges are neat and burr-free, and in most cases no additional grinding is required.
- Flexible and diverse: supports processing of complex shapes such as straight lines, curves, hollowing, carvings, and special-shaped parts.
- Small heat-affected zone: reduces material deformation and maintains the mechanical properties and appearance quality of aluminum alloy.
- Non-contact processing: no mechanical stress, no deformation of workpiece or surface scratches.
Aluminum sheet laser cutting
Laser cutting of aluminum alloy plates is a processing method that uses a high-power laser beam to perform high-precision and efficient cutting of aluminum alloy plates. The laser beam is focused on the surface of the aluminum alloy to produce high-temperature molten material, and high-pressure gas (such as nitrogen and oxygen) is used to blow away the molten metal, thereby forming a smooth cut surface. Compared with mechanical cutting (such as stamping, sawing) and water jet cutting, laser cutting has higher precision, faster speed and less material loss.
- Applicable thickness: Conventional 1mm-30mm aluminum plates can be processed, and larger specifications can be customized.
- Cutting quality: no oxidation, no burrs, the surface is smooth after cutting and can be directly used for assembly or welding.
- Application scenarios: aerospace, automobile manufacturing, electronic equipment, architectural decoration, mechanical parts, etc.
- Common alloys: 6061 T6, 2024 T3, 5052 H32, 7075 T6
6061 T6 aluminum plate laser cutting
Laser cut 6061 aluminum is corrosion resistant, strong and durable, making it an ideal choice for a variety of applications in the automotive, aerospace and robotics sectors. 6061 aluminum is also known for its weldability while maintaining strong shock load performance. So, no matter what your next custom laser cutting project is, 6061 will meet all your requirements.
Thickness: .040" – .500"
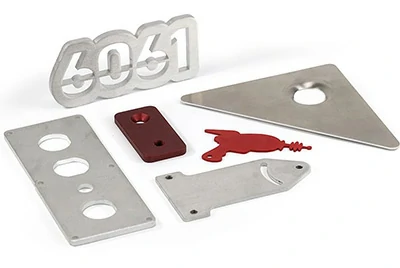
Many aluminum alloys are able to withstand significant vibration (also known as fatigue strength), making them ideal for high -shock applications such as transportation and robotics. For any of these applications, 6061 aluminum is a good intermediate alloy, combining the strength of 7075 with the ductility of 5052.
- Construction
- Automotive
- Industrial Applications
- Pressure-bearing Components
- Aerospace Structural Parts
- Robotics
- Electronic Enclosures
- Bicycle Frames
2024 T3 aluminum plate laser cutting
Laser cut 2024 T3 Aluminum is one of the strongest materials Chalco offers. With unmatched tensile strength, 2024 T3 Aluminum is the best alloy for projects that require the highest structural integrity and sturdiness.
Thickness: 0.025 inch
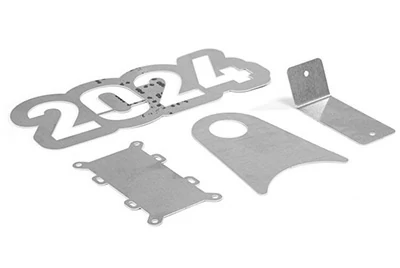
Unlike our other aluminum alloys, 2024 aluminum is alloyed with copper, which makes it stand out in terms of tensile strength. This unique combination of materials and the capabilities they create make laser cut 2024 aluminum useful for structural, architectural, aerospace, and automotive applications.
- Aircraft accessories
- Computer components
- Fastening device
- Gears and shafts
- Couplings
- Ammunition
- Watch Parts
- Hydraulic valve body
5052 H32 aluminum plate laser cutting
Laser Cutting 5052 Aluminum is one of our most popular metals. Used in a variety of applications including aerospace, automotive, and robotics, 5052 H32 aluminum is the perfect combination of high performance and affordability.
Thickness Range: .040" – .500"
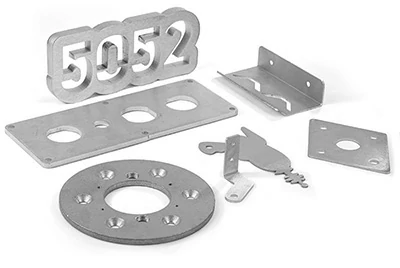
5052 aluminum has a high relative ultimate strength (and fatigue strength) and has a variety of practical uses. It is not heat treatable, which means it requires cold working to achieve medium to high strength properties. If higher strength is required, 6061 series aluminum can be used.
- Robot
- Fences
- Signage
- Hinge
- Marine Applications
- Heat Exchanger
- Signage
- Panel
7075 T6 aluminum plate laser cutting
7075 aluminum has nearly twice the tensile and shear strength of 6061, and is laser cut, making it one of the best choices when high strength and low weight are important.
Available in thicknesses: .125", .190 ", .250" , etc.
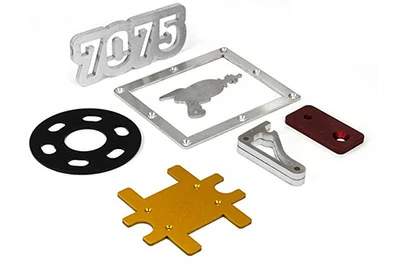
7075 sacrifices some of the machinability, formability, and weldability of 5052 aluminum to increase hardness, strength, and overall toughness. 7075 aluminum still has the advantages of other aluminum alloys, such as light weight and high fatigue strength, so it has the highest strength-to-weight ratio of all aluminum alloys.
- Construction Angle
- Car frame
- Bicycle frame
- Aerospace components
- Highly stressed structures
- Electronics
- Heat sink
- Climbing equipment
Aluminum pipe laser cutting
Laser tube cutting is a process that uses high-precision laser technology to cut and process metal tubes. It is suitable for tubes of various shapes, including round tubes, square tubes and rectangular tubes. This process can accurately cut holes, slots and design patterns of various shapes on the tube, and is widely used in many industries .
- Cutting type: Perpendicular to the surface
- Edge to Edge Tolerance: +/- .010" on the inside surface of the tube
- Minimum Feature Size: Typically no larger than tube thickness.
- Strong flexibility: Suitable for cutting various complex shapes, no molds are required, shortening the production cycle and reducing costs .
- Wide applicability: It can process round tubes, square tubes, special-shaped tubes and other aluminum alloy tubes of different specifications and thicknesses to meet diverse design needs.
Aluminum round tube laser cutting
Cutting outer diameter range: 0.5 inches (12.7mm) ~ 6 inches (152.4mm).
Wall thickness support: 0.035 inches (0.89mm) ~ 0.500 inches (12.7mm).
Contact us now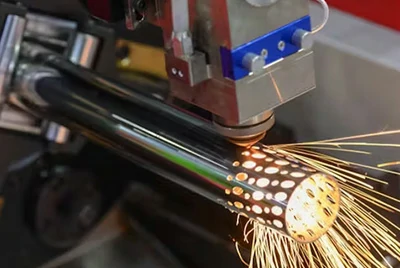
Supported cutting shapes:
- Straight cutting, bevel cutting,
- Round hole, long hole, oval hole,
- Special shaped patterns,
- Welding reserved groove, etc.
- Structural support parts
- Fluid transport pipeline
- Sports Equipment
- Electronic devices
- Auto Parts
- Rail transit components
- Industrial equipment parts
- Ship parts
- Medical device components
- Solar and wind energy equipment
Aluminum alloy square tube/rectangular tube laser cutting
Minimum tube size: 0.5 inches (12.7mm)
Maximum tube size: 6 inches (152.4mm)
Wall thickness support: 0.035 inches (0.89mm) ~ 0.500 inches (12.7mm)
Contact us now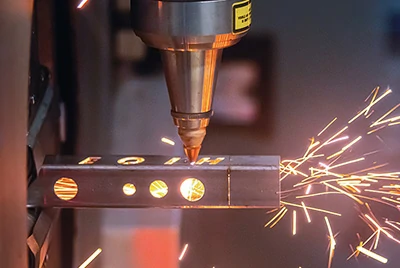
Supported cutting processes:
- End cutting: Precise cut-off for assembly connection.
- Welding slotting: used to optimize welding position and reduce weld errors.
- Hole/slot processing: supports round holes, square holes, long holes, nested slots, pattern engraving, etc.
- Bevel cutting: suitable for structural frame splicing to improve matching accuracy.
- Framework
- Fences and guardrails
- Mechanical Components
- Rail transit components
- Automobile and motorcycle structure
- Signs and Displays
- Solar and wind power support
- Building structural parts
- Medical equipment parts
- Industrial Equipment
Aluminum profile laser cutting
Aluminum alloy profiles are widely used in many industries such as construction, industrial equipment, rail transportation, aerospace, etc. due to their high strength, light weight, corrosion resistance and good processability. Laser cutting technology can accurately process complex cross-section profiles, special-shaped structural parts, connection notches, splicing holes, etc. to meet high-precision assembly requirements.
- Applicable to various aluminum profile specifications: supports laser cutting processing of T-type, L-type, U-type, C-type, H-type and other customized profiles.
- Professional design optimization support: We can customize cutting solutions according to customer CAD drawings and provide design optimization suggestions to improve structural stability and assembly accuracy.
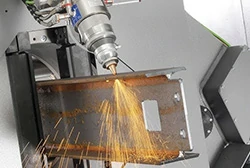
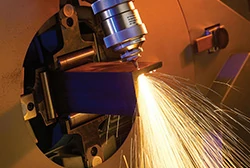
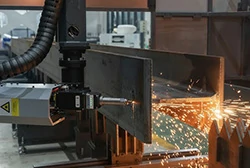
Aluminum special-shaped parts and customized parts
Aluminum alloys are ideal materials for customized parts in aerospace, automobile manufacturing, architectural decoration, electronic equipment, etc. due to their light weight, high strength, good corrosion resistance and machinability. Laser cutting technology can accurately process complex shapes, fine structures and high-precision parts, and is suitable for a variety of customized needs.
- Support complex geometric shapes: suitable for high-precision processes such as hollow engraving, curve cutting, micro-hole processing, and detail engraving.
- Suitable for small batch or mass customization: flexible production mode, no need to open molds, lower production costs and shorten delivery cycle.
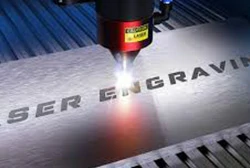
Engraving
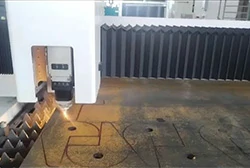
Curve cutting
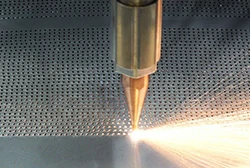
Micro hole processing
Other alloy laser cutting
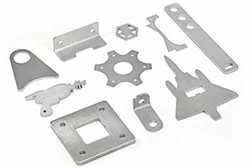
304 stainless steel sheet metal
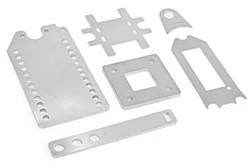
Laser cut 316 stainless steel sheet metal parts
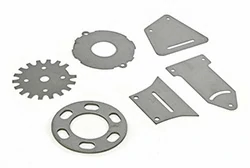
Laser cut grade 5 titanium sheet metal parts
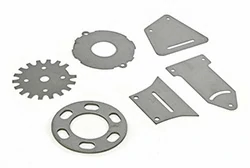
Laser cut grade 2 titanium sheet metal parts
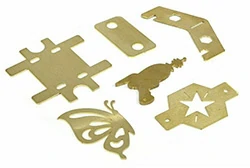
Laser cut brass sheet metal parts
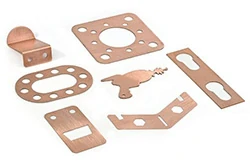
Laser cut copper sheet metal parts
Chalco aluminum alloy laser cutting service advantages
Chalco provides one-stop aluminum alloy laser cutting services throughout the entire process, including high-precision laser cutting, additional processing technology and surface treatment, ensuring that customers receive high-quality and efficient solutions. Whether it is material supply, precision processing, or surface treatment, we can meet your needs and become your most reliable partner.
High-precision laser cutting
We use advanced fiber laser cutting technology to efficiently process aluminum plates, aluminum tubes, and aluminum profiles to meet the high-precision needs of multiple industries.
- Imported fiber laser cutting equipment ensures high cutting precision, smooth incision and no burrs.
- Supports cutting of complex geometric shapes, achieves precise detail processing, and reduces the need for subsequent processing.
- Wide range of processing sizes: It can cut aluminum alloy materials with a thickness of 0.5mm - 30mm, and supports ultra-large size plates of 3000mm × 1500mm.
- Strict precision control: the error can be controlled within ±0.1mm to ensure assembly matching.
- Strong batch production capability: Provide large-volume, stable, and highly consistent processing, suitable for industrial- grade manufacturing needs.
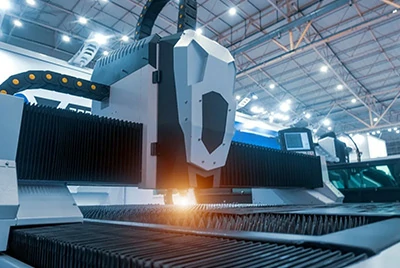
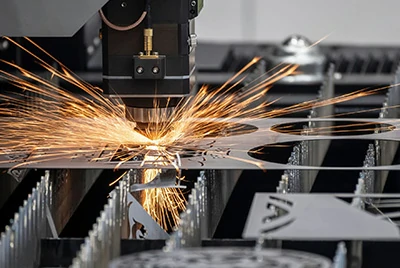
Rich additional processes to meet diverse needs
Laser cut aluminum parts often require further processing to improve surface quality, assembly performance or to meet specific usage requirements. Chalco offers a full range of additional processes to ensure your products meet higher standards.
- Deburring - Remove burrs left after laser cutting to improve edge smoothness and avoid rough feel or assembly problems.
- Tumbling - Reduces surface scratches and improves overall texture through vibration or drum grinding.
- Countersinking - Creating a chamfer around a hole to allow screws and nuts to sit flush with the surface, reducing wear.
- Tapping - Adding threaded holes to aluminum parts to facilitate bolt or nut connection and improve assembly efficiency.
- Hardware Insertion - Press-fit nuts, studs, and spacers to improve product stability and ease of assembly.
- Support customized processing - carry out precision processing according to the CAD drawings provided by customers, and provide design optimization services to improve structural stability and production efficiency.
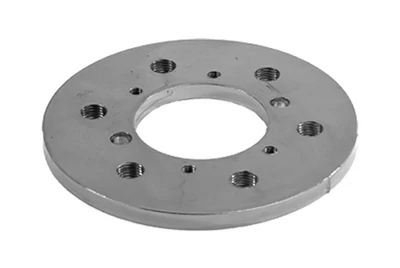
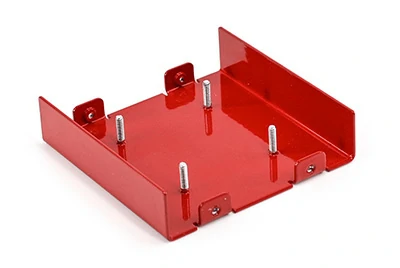
Surface treatment to improve durability and aesthetics
To meet the corrosion resistance, wear resistance and appearance requirements of different application fields, we provide professional surface treatment processes to make laser cut parts more competitive.
- Surface customization service - To meet the needs of specific industries, we can provide special treatments such as brushing, sandblasting, and electrolytic polishing to enhance visual effects and durability.
- Anodizing - forms a hard protective layer of aluminum oxide, improving corrosion resistance, wear resistance, and providing a variety of color options.
- Powder Coating - Creates a thick, impact-resistant coating that enhances part durability and is available in a variety of color options.
- Dimple Forming - Forming a dimple structure on the surface of a material to enhance strength and improve overall mechanical properties.
Chalco laser cutting product cooperation case
Aerospace industry
Project requirements: High-strength, lightweight aluminum alloy special-shaped brackets and cabin structural parts require high-precision cutting to reduce assembly errors and improve product performance.
Chalco Solution: Using high-precision fiber laser cutting technology, we provide precision cutting of 7075-T6 and 2024-T3 aviation-grade aluminum alloys, ensuring the error is controlled within ±0.1mm, and provide anodized surface treatment to enhance corrosion resistance.
Rail transit industry
Project requirements: High-strength aluminum profile support structure requires high cutting precision to ensure error-free assembly inside the high-speed rail carriage and meet the lightweight standards of rail transit.
Chalco Solution: We provide precision laser cutting of 6061-T6 aluminum alloy profiles to ensure accurate docking of profile interfaces, and provide additional processes such as deburring, tapping, and welding pretreatment to improve assembly convenience.
Automobile manufacturing industry
Project requirements: The customer wants to customize a lightweight aluminum alloy frame for use in new energy vehicle battery compartments, and requires the cutting edges to be smooth and burr-free to reduce subsequent machining costs.
Chalco Solution: We use high-precision fiber laser cutting + deburring to ensure that the battery compartment structure meets high-precision assembly requirements. At the same time, we provide anodizing treatment to enhance corrosion resistance and increase the service life of the battery compartment.
Electronic equipment industry
Project requirements: The customer requires high-precision aluminum alloy panels and rack support structures with stable dimensions and no scratches on the surface to meet the appearance and performance requirements of high-end servers and electronic equipment.
Chalco solution: Provide 5052-H32 aluminum plate laser cutting + drum polishing to remove processing marks and ensure the surface of the chassis is smooth. At the same time, provide powder coating to make the frame more wear-resistant and corrosion-resistant.
Building decoration industry
Project requirements: The customer needs to customize aluminum alloy decorative screens and building curtain wall profiles, involving complex hollow patterns, requiring high-precision processing to ensure the aesthetics of the design.
Chalco solution: High-precision laser engraving + anodizing surface treatment is used to ensure that the screen has delicate patterns and smooth cuts, and customized colors are available to meet customers' personalized design needs.
New energy industry
Project requirements: The customer needs an aluminum alloy photovoltaic bracket with strong weather resistance and stable structure, and requires high-precision cutting to ensure that the bracket perfectly matches the solar panel.
Chalco Solution: Provide laser cutting + powder coating treatment of 6061-T6 and 5052-H32 aluminum alloy brackets to enhance corrosion resistance and ensure that the components will not oxidize or rust in long-term outdoor use.
Laser cutting project tips: how to choose the right technology and partner?
When carrying out a laser cutting project, you may face multiple choices - which laser cutting technology is the most suitable? How to choose a reliable processing supplier? How to optimize costs? These factors directly affect the quality, delivery efficiency and final cost of the product. Here are some key tips to help you make wise decisions in your laser cutting project!
1. Choose the right laser cutting technology
Different laser cutting technologies are suitable for different materials and processing requirements. Understanding their respective characteristics can help you make the right choice.
Fiber Laser Cutting
- Applicable materials: aluminum alloy, stainless steel, carbon steel, copper, titanium and other metals
- Cutting accuracy: extremely high (error controlled within ±0.1mm)
- Cutting speed: fast, especially suitable for thin plates and high-precision processing
- Energy consumption: energy saving (photoelectric conversion efficiency 30%-40%)
- Applicable industries: aerospace, automobile manufacturing, rail transportation, electronic equipment, etc.
CO₂ Laser Cutting
- Applicable materials: wood, plastic, glass, acrylic and other non-metals and some metals
- Cutting accuracy: High, but not as fine as fiber laser
- Cutting speed: suitable for thick plates (>10mm), but slower for thin plates
- Energy consumption: High (photoelectric conversion efficiency is about 10%-15%)
- Applicable industries: advertising production, furniture decoration, handicraft manufacturing, etc.
YAG Laser Cutting
- Applicable materials: metals and some non-metals (mainly used for welding)
- Cutting accuracy: moderate, suitable for small parts processing
- Cutting speed: Slow, suitable for precision electronics manufacturing
Tips: If your project mainly involves aluminum alloys and other metal materials, and has high requirements for precision, speed and cost, then fiber laser cutting is undoubtedly the best choice!
2. Choose the right laser cutting partner
A reliable laser cutting supplier can help you improve production efficiency, reduce costs, and ensure stable product quality. When choosing a supplier, focus on the following points:
Equipment and processing capabilities
- Is fiber laser cutting equipment used?
- Is the processing accuracy controllable (error within ±0.1mm)?
- Can complex geometric shapes, special-shaped parts, and microporous structures be processed?
One-stop processing capabilities
- Do you have the integration capabilities of material supply + laser cutting + additional processes + surface treatment?
- Are additional processes such as deburring, tapping, weld pretreatment, etc. available?
- Does it support surface treatments such as anodizing and powder coating to avoid multiple outsourcing?
Production Capacity & Delivery Time
- Does it support small-batch trial production & large-scale mass production to ensure stable supply?
- Do you have an efficient production management process to ensure on-time delivery?
- Is the quality control system complete and can ensure the consistency of batch products?
Industry Experience & Customer Cases
- Do you have experience in cooperation with industries such as aerospace, automobile, rail transit, electronic equipment, and new energy?
- Can you provide technical optimization support to help you improve product performance?
Tips: The supplier should not only have high-precision cutting capabilities, but also be able to provide complete services from materials to surface treatment to ensure high quality and high efficiency!
3. Reduce costs & improve project cost performance
The cost of laser cutting is not just the cost of a single processing link, but also involves material utilization, processing efficiency and long-term cooperation model. Optimizing the following points can reduce the total cost:
Optimize cutting paths
Does the supplier offer material optimization solutions to reduce waste and improve cutting utilization?
Choose the right material specification
- Are there multiple aluminum alloy materials available (such as 6061, 5052, 2024, 7075)?
- Can you provide the appropriate plate thickness and pipe size to avoid unnecessary processing?
Long-term cooperation discount
- Are there discounts for bulk orders?
- Does it provide inventory management support, fast delivery, and reduced stocking pressure?
Tips: The price depends not only on a single order, but also on the supplier's material procurement, production management and delivery efficiency. Long-term cooperation can provide more cost-effective services!