With the growing demand for lightweight structures, noise reduction, safety protection, and multifunctional materials, foam aluminum has become widely used across industrial and architectural applications. Thanks to its unique combination of low weight, high strength, energy absorption, thermal insulation, soundproofing, and electromagnetic shielding, it serves critical roles in various environments. Chalco offers a full range of foam aluminum products, including closed-cell foam aluminum panels, open-cell foam panels, foam aluminum sandwich panels, decorative panels, and custom-shaped components—to meet structural, functional, and aesthetic requirements across diverse use cases.
Our foam aluminum solutions have been successfully applied in industries such as automotive, rail transit, aerospace, architectural decoration, electronics & telecommunications, defense, and environmental engineering. Based on your project requirements, you can explore targeted product solutions and access tailored technical support for your specific application.
Application of foam aluminum sheet plate in construction and architectural Decoration
In modern architecture, materials with lightweight, fire-resistant, acoustic, and thermal performance are increasingly favored for both exterior and interior applications. Foam aluminum, with its metallic texture, aesthetic versatility, Class-A fire resistance, excellent acoustic insulation, and high design adaptability, has been widely used in curtain wall systems, acoustic ceilings, wall panels, commercial interiors, exhibition installations, and even metallic furniture, offering a balance between functional performance and visual appeal.
Material advantages & technical performance
Class-A fire resistance, non-combustible and high-temperature resistant, compliant with fire codes for high-rise and public buildings
NRC ≥ 0.75 sound absorption, ideal for theaters, auditoriums, conference rooms, and commercial spaces
Lightweight (~1.5–2.5g/cm³), supports dry-hanging, modular assembly, and fast installation
Non-hygroscopic, anti-mildew, corrosion-resistant, suitable for humid or polluted environments, indoor and outdoor
Various surface finishes available, including anodizing, sandblasting, coloring, perforation, and artistic textures
Flexible installation methods, including adhesive bonding, light steel frames, and screw mounting, adaptable to different wall/ceiling structures
Recommended products & processing capabilities
Chalco offers a full range of architectural foam aluminum materials, including:
- Closed-cell decorative foam aluminum panels (thickness 5–30mm), customizable in pattern, pore size, color, and surface finish
- Double-perforated light-transmitting panels, ideal for lighting walls, signage, and interactive art installations
- High-performance acoustic foam aluminum panels, for ceilings, partition walls, and architectural noise control
- Full support for custom cutting, shaping, 3D design consultation, and installation recommendations
Typical applications & case studies
- Beijing Winter Olympics Ice Hockey Arena – interior wall finishing
- Shanghai Fuxing Plaza, Shenzhen Grand Theater – acoustic ceiling systems
- Hangzhou Baoyi Center, Beijing Chenggao Building – metal accent walls and interior panels
- PRADA Foundation, ADIDAS Suzhou HQ – exterior foam aluminum wall cladding
- High-speed railway stations, airport lounges, hospital auditoriums – used as ceiling panels and acoustic wall boards
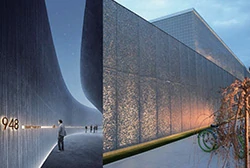
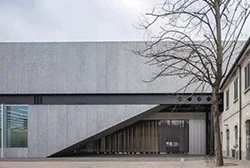
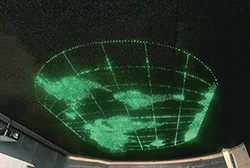
Application of foam aluminum in aerospace
In aerospace engineering, materials must withstand extreme mechanical stress, thermal environments, and space constraints. Foam aluminum is increasingly applied in this field for its unique combination of ultra-lightweight, high energy absorption, flame resistance, vibration damping, and multifunctional structural capabilities. It has been used in spacecraft buffer systems, re-entry module bottoms, rocket structures, satellite housings, thermal protection components, and even missile packaging and air-drop crates.
Material advantages & technical performance
Excellent shock absorption and buffering under extreme impact, ideal for soft-landing systems and module protection
Thermal insulation and fire resistance, effective in high-temperature re-entry and ignition environments
Low weight-to-strength ratio, critical for spacecraft payload and fuel efficiency
Electromagnetic shielding properties, applicable in space communications and avionics protection
Customizable pore structure and composite integration, suitable for multi-functional aerospace parts
Recommended products & processing capabilities
Chalco provides aerospace-grade closed-cell foam aluminum plates and structural blocks, featuring:
- Tailored density and mechanical performance (e.g., 0.25–0.45 g/cm³)
- CNC machining, contour cutting, and composite sandwich bonding
- Support for curved parts, layered integration, and thermal management design
- Surface treatment options for corrosion resistance and bonding performance
Typical applications & case studies
- Spacecraft shock absorbers: used in the bottom of re-entry capsules for safe landing and astronaut protection
- Rocket and satellite housings: lightweight shell structures for thermal insulation and EMI shielding
- Lunar rover and Shenzhou re-entry module components: foam aluminum used for energy absorption and internal packaging
- Airdrop equipment boxes and payload crates: combining lightweight and protective performance under combat conditions
- Aviation heat exchangers and fin structures: enhancing heat dissipation in aircraft engine systems and control modules
- Electromagnetic protection: applied in high-power pulse shielding for carrier-based electromagnetic catapults
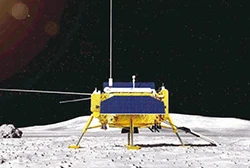

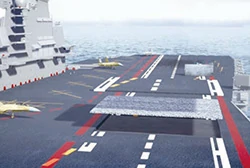
Application of foam aluminum in auto industries
As the automotive industry advances toward lightweight design, energy efficiency, and enhanced safety, foam aluminum has emerged as a new-generation material for structural optimization and multi-functional integration. With a density of only 3%–8% of steel, high energy absorption, and versatile physical properties, foam aluminum is now widely used in crash energy-absorbing modules, battery protection structures, engine brackets, door soundproofing layers, and underbody fillers, playing a vital role in both weight reduction and safety enhancement.
Material advantages & technical performance
Energy absorption efficiency reaches 70%–90%, far exceeding that of steel (30%–50%), providing superior crash protection.
Thermal conductivity is only 1/10 that of solid aluminum, making it ideal for EV battery thermal management.
Excellent acoustic insulation with NRC values up to 0.8 and noise reduction of 20–40dB, enhancing vehicle NVH performance.
Customizable density (0.25–0.5 g/cm³) to meet varied stiffness and strength requirements.
Easily bonded with metal skins or composite panels for sandwich structures, supporting integrated design of weight reduction and functionality.
Recommended products & processing capabilities
Chalco offers closed-cell foam aluminum panels, sandwich structures, and custom-shaped blocks tailored for automotive applications, with the following services:
- Customized density, thickness, and shape per project needs
- CNC cutting, forming, and composite lamination
- 3D structural support and energy absorption simulation
- Optional surface treatments: anti-corrosion coatings, anodizing, flame-retardant finishes
Typical applications & case studies
- BMW engine bracket: integrated noise reduction and weight reduction
- Audi A8 energy-absorbing body structures: foam aluminum plates enhance crash safety
- EV battery pack protective panels: combining heat dissipation, shielding, and protection
- Low-speed impact bumpers and door inner reinforcements: replace traditional steel for better safety and comfort
- Special vehicles: applied in explosion-proof, crash-resistant, and EMC-sensitive structures
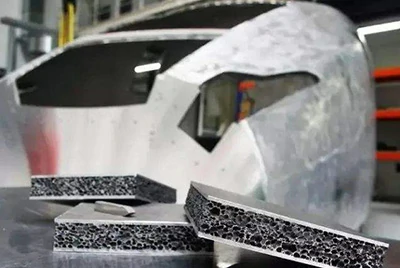
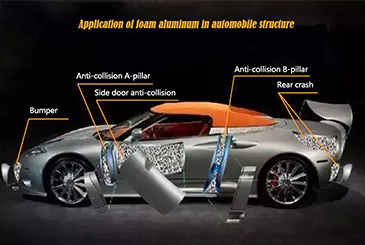
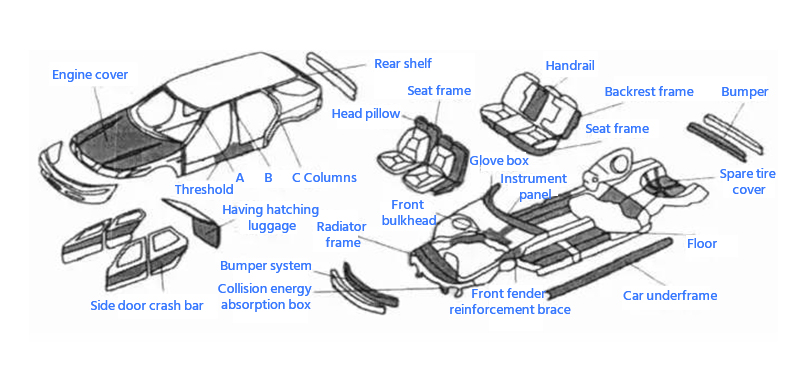
Application of foam aluminum in highway and bridge sound barriers
With increasing concern over noise pollution along expressways, urban viaducts, and rail-adjacent roads, there is a growing demand for high-performance sound barrier materials that offer acoustic efficiency, structural safety, weather resistance, and aesthetic flexibility. Foam aluminum, with its lightweight structure, wideband sound absorption, corrosion resistance, and fire safety, is widely adopted in central dividers, bridge edges, ramp walls, and urban noise control projects.
Material advantages & technical performance
High sound absorption: NRC ≥ 0.75, effective across mid-to-low frequency traffic noise bands
Lightweight structure: Approx. 1/5 the weight of concrete or traditional metal panels, reducing foundation loads
Class-A fire resistance: Complies with Chinese and EN standards for urban and public area fire protection
Excellent durability: Non-corrosive, mildew-resistant, and suitable for year-round outdoor exposure
Wind pressure resistance certified: Passed ±2.0 kPa wind load deformation test; residual deflection ≤ 0.58mm per JT/T 646.4-2016 standard
Aesthetic versatility: Supports anodizing, coloring, sandblasting, perforation, and artistic finishes for architectural integration
Recommended products & processing capabilities
- Chalco supplies closed-cell foam aluminum sound-absorbing panels and composite noise barrier modules, offering:
- Single-layer, perforated dual-layer, or sandwich panel options
- Custom density, pore size, and thickness combinations for target frequency tuning
- Structural compatibility with aluminum frames or steel supports
- Modular installation support for rapid deployment in field conditions
Typical applications & case studies
- Urban expressway bridge edge barriers: perforated + foam aluminum composite structure for effective noise suppression
- Central divider sound-absorbing modules: lightweight panels reduce foundation requirements
- Tunnel entrance noise mitigation: high structural performance and acoustic insulation under variable airflow
- Pilot projects deployed in multiple cities, including Henan, Jiangsu, and Chongqing, with verified acoustic and structural outcomes
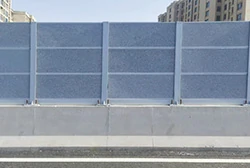
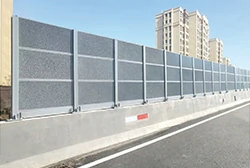
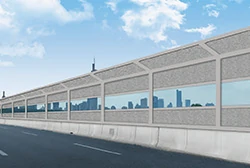
Application of foam aluminum in railway and transportation
With the continuous expansion of high-speed rail, metro, and light rail systems worldwide, the demand for lightweight, high-strength, and multifunctional interior materials is rising. Foam aluminum has proven to be an ideal solution in rail transit, widely used in train floor structures, wall panels, acoustic ceilings, partition systems, and under-floor support layers, where fire safety, sound absorption, weight reduction, and modularity are all essential.
Material advantages & technical performance
High strength-to-weight ratio, effectively reducing train body weight while maintaining structural integrity
Excellent acoustic performance, NRC ≥ 0.75, helps control internal noise and enhance passenger comfort
Fire-resistant and flame-retardant, complies with GB 8624-2012 and EN 13501 standards (Class A)
Thermal insulation, improving HVAC efficiency and maintaining temperature stability in compartments
Anti-corrosion, anti-vibration, and moisture-resistant, ensuring long-term durability in rail environments
Passed structural safety tests, including ±2.0 kPa wind pressure deformation test (max residual deflection: 0.58mm) per JT/T 646.4-2016
Recommended products & processing capabilities
- Chalco supplies closed-cell foam aluminum panels and structural blocks specifically for rail transit applications, with:
- Standard panel sizes for underfloor, sidewall, ceiling systems
- Support for laminated structures: foam aluminum + aluminum plate, honeycomb, or decorative surfaces
- CNC precision cutting, thermal insulation design, and fireproof coating
- On-site installation support and lightweight assembly component supply
Typical applications & case studies
- High-speed rail floor sandwich structures: combining foam aluminum core with aluminum or steel skins for strength and vibration reduction
- Metro ceiling acoustic panels: NRC≥0.75, improving passenger environment and reducing ambient noise
- Train wall partition cores: used in modular composite interior systems
- Battery compartment thermal protection (new energy trains): ensuring safety and temperature stability
- Noise-reduction structures under bogie areas and driver cabins: improving structural safety and acoustic isolation
- Products have been applied in multiple metro systems including Beijing, Shanghai, Shenzhen, and Chengdu, with excellent in-service performance
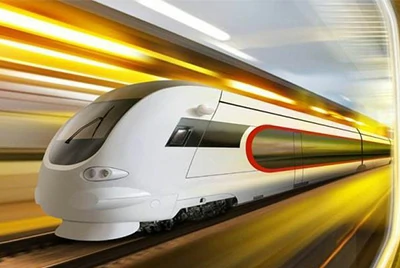
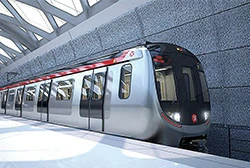
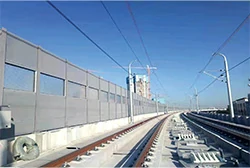
Application of foam aluminum in military and defence
In modern defense applications, materials must combine lightweight properties with outstanding structural strength, energy absorption, flame resistance, and electromagnetic shielding. Foam aluminum has been widely deployed in military scenarios including missile bodies, armored vehicles, composite armor systems, airdrop containers, command centers, and naval ships, offering performance benefits for both structural and protective components.
Material advantages & technical performance
- High energy absorption, used for blast protection, bullet resistance, and impact mitigation
- Weight reduction for vehicles and missiles, improving mobility and payload capacity
- Excellent thermal insulation and low heat transfer, suitable for electronic shielding and equipment housing
- Fire retardant, corrosion-resistant, and durable, even in harsh environments
- Effective electromagnetic shielding, applicable in sensitive communication and control centers
Recommended products & defense applications
Chalco supplies military-grade foam aluminum plates, blocks, and composites, capable of integration with armored steel, ceramics, and aramid fiber. Key applications include:
- Missile bodies and engine housings: reduce weight and improve heat resistance
- Composite armor panels: combine foam aluminum with high-strength materials for lightweight protection
- Anti-mine bottom plates: armored steel + foam aluminum + steel sandwich for riot vehicles and transports
- Mobile command shelters & containers: lightweight, soundproof, shielded rooms for rapid deployment
- Naval engine compartments & partitions: noise reduction, fire resistance, vibration damping
- Submarine acoustic panels: reduce engine room noise by over 20 dB, improving stealth
- Electromagnetic shielding for aircraft carriers and command posts
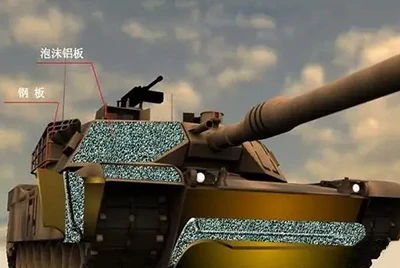
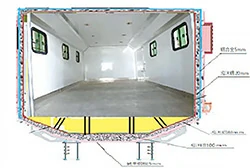
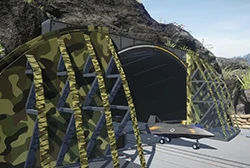
Application of foam aluminum in nuclear power & strategic equipment
In the nuclear power and strategic equipment sectors, safety, shielding, and structural reliability are paramount. Foam aluminum is applied in nuclear fuel transport containers, shielding rooms, protective doors, and satellite equipment, where it contributes to energy absorption, electromagnetic shielding, and significant structural weight reduction.
Material advantages & technical performance
- Class A fire resistance and excellent temperature stability
- Significant weight reduction for large equipment doors and shields (e.g., 90t → 18t)
- Outstanding electromagnetic shielding performance, used in critical containment and control environments
- Good compression strength, shock resistance, and low rebound response under impact
- Corrosion-resistant and non-hygroscopic, ideal for radioactive and high-humidity environments
Key applications & case studies
- Artificial Sun Project (Fusion Reactor): foam aluminum solved AC electromagnetic shielding under extreme field strength
- China National Nuclear Corporation (CNNC): qualified supplier; foam aluminum used in nuclear fuel transportation protection
- Protective command shelters: fireproof, soundproof, and EMI-shielded modular rooms
- Ballistic missile component buffers: used in shock-absorbing packaging and support structures
- Electromagnetic shielding rooms and machine housings: prevent interference and leakage
- Nuclear facility containment structures: thermal and mechanical protection with structural integrity
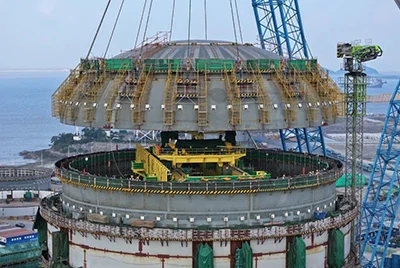
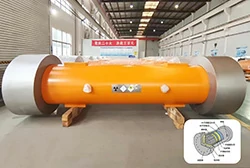
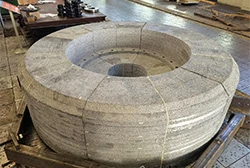
Performance specifications supporting multi-industry applications
To ensure performance reliability across such diverse industries and applications, foam aluminum must meet strict standards in structural strength, sound absorption, thermal insulation, and fire resistance. The following key specifications provide a technical overview of Chalco’s foam aluminum materials, helping you evaluate suitability for your specific project needs.
Parameter | Typical Range / Value | Notes |
Density | 0.20 – 0.60 g/cm³ | Adjustable per application |
Porosity | 60% – 90% | Open-cell or closed-cell |
Compressive Strength | 2 – 8 MPa | Depends on density and structure |
Sound Absorption Coefficient (NRC) | ≥ 0.75 | Up to 0.9 for acoustic panels |
Thermal Conductivity | 0.04 – 0.1 W/m·K | ~1/10 of solid aluminum |
Flame Resistance | Class A (non-combustible) | Meets ASTM / EN fire standards |
Standard Thickness | 5 – 200 mm | Custom sizes available |
Maximum Panel Size | Up to 2400 × 1200 mm | Custom shaping supported |
Surface Finish Options | Anodizing, coating, perforation | Decorative or functional |
Chalco – your trusted partner in foam aluminum manufacturing
To meet the diverse demands of various industries—such as energy absorption, structural light-weighting, acoustic control, and thermal protection—Chalco has established a comprehensive foam aluminum production system, covering everything from material preparation and pore structure control to surface finishing and composite processing. We provide stable batch production, multi-spec customization, and engineering-grade deep processing, fully supporting applications across rail transit, automotive, construction, defense, and nuclear sectors.
Diversified manufacturing methods for stable performance
Chalco utilizes a variety of advanced foam aluminum manufacturing techniques to ensure consistent material performance and structural stability. These processes are tailored to meet different application requirements in terms of pore size, density, mechanical strength, and acoustic behavior.
- Direct Gas Injection: Molten aluminum is foamed by injecting inert gases to produce a uniform closed-cell structure.
- Powder Metallurgy Foaming: Aluminum powder mixed with a foaming agent is compacted and expanded by heat treatment.
- Cast Ingot Extrusion / Die Casting Expansion: Large ingots are foamed through casting or extrusion processes to create thick or large-format foam structures.
Want to know how our foam aluminum is made? Click here to view [detailed manufacturing processes]
Extensive processing and customization capabilities
In addition to raw material production, Chalco offers a full range of post-processing services, covering everything from basic forming to integrated structural fabrication.
- Available density range: 0.20–0.60 g/cm³
- Standard thickness range: 5–200 mm (custom ultra-thick and oversized panels available)
- Structure types: closed-cell, open-cell, perforated-surface with foam core, sandwich, and multilayer composite panels
- Processing methods: CNC cutting, slotting, precision bending, aluminum profile bonding, powder coating, electrophoresis, anodizing, perforation decoration
- Customization services: drawing-based fabrication, project-based design, mechanical and acoustic simulation support
Quality assurance and certification support
We prioritize product consistency, performance traceability, and project-level compliance, supported by a complete testing and certification system.
- Test reports are provided with every batch (including density, pore size distribution, compressive strength, sound absorption coefficient, etc.)
- Third-party testing supported (SGS, CNAS, etc.)
- Compliant with ASTM, EN, ISO, GB/T and other major international and industry standards
- Proven performance in rail acoustic systems, architectural facades, military-grade components, and more
Industry applications and expanding reach
With strong production and engineering capabilities, Chalco's foam aluminum materials are widely applied across:
- Automotive: energy-absorbing structures, floor fillers, EV battery thermal shielding
- Rail Transit: ceiling systems, wall panel cores, acoustic modules
- Architecture: decorative facades, metal curtain walls, soundproof ceilings
- Defense: blast-resistant panels, missile structures, anti-mine vehicle underlayers
- Nuclear Energy: EMI shielding panels, lightweight radiation-proof doors, thermal insulation units
Foam aluminum manufacturing techonology
1. Solid metal sintering method
Most of the foam aluminum produced by this method has a through-hole structure. This is due to the fact that most of the aluminum particles are connected with each other through sintering, and the aluminum is always kept solid.
1.1 Powder metallurgy foaming method
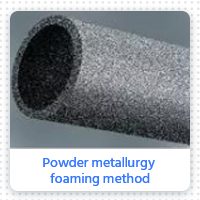
The process principle is to mix aluminum powder and foaming agent powder and compress them to obtain a preform with a gas tight structure. Heating the preform will cause the foaming agent to decompose and release gas, forcing the preform to expand to obtain foam aluminum.
Process flow of powder metallurgy foaming method:
Features: First, compared with other methods, the available alloy composition is more extensive, which is conducive to improving the mechanical properties of foam aluminum; Second, it can directly manufacture components with complex shapes.
The disadvantage is that the process parameter range of this method is narrow, the cost is high, and the size of foam aluminum produced is limited.
1.2 Loose powder sintering
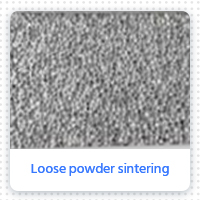
This method is mostly used to prepare foam copper. Because the dense oxide film on the surface of aluminum powder will prevent the particles from sintering together, it is relatively difficult to prepare foam aluminum by loose powder sintering method. At this time, the oxide film can be destroyed by means of deformation to make the particles stick together more easily; Or add magnesium, copper and other elements to form eutectic alloy when sintering at 595~625 ℃.
This production method includes three processes:
Features: The advantages are simple process and low cost. The disadvantages are low porosity and low material strength. If fiber is used instead of powder, porous materials can also be obtained.
1.3 Slurry molding method
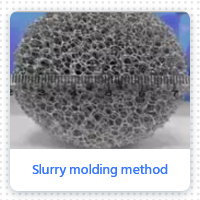
The slurry forming method is to form a suspension of metal aluminum powder, foaming agent (hydrofluoric acid, aluminum hydroxide or orthophosphoric acid), reaction additive and organic carrier. Stir it into a state containing foam, and then put it into the mold for heating and roasting. Then the slurry starts to become sticky, and with the gas generated, it starts to expand, and finally gets foam aluminum with certain strength.
If the slurry is directly poured into the polymer foam, the polymer material can be pyrolyzed by heating up, and the open cell foam material can also be made after sintering.
This production method includes:
Features: The foam aluminum produced has low strength and cracks.
1.4 Sintering dissolution method
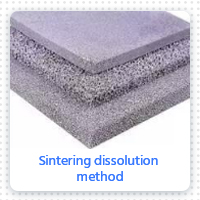
The aluminum powder and salt powder are evenly mixed and pressed into billets. During the pressing process, the salt powder basically keeps its original appearance. The aluminum powder undergoes plastic deformation and fills the gap between the salt particles to form a continuous network matrix. Then, the billets are sintered to combine the reticulated aluminum matrix into a whole. Finally, the sintered billet sample is placed in hot water, and the salt particles in the billet are filtered out to obtain uniform open cell foam aluminum parts.
The process includes:
Features: The advantage is that by selecting the shape and particle size of the salt powder, the shape and size of the holes can be controlled within a certain range; The porosity can be precisely controlled by the volume ratio of mixed powder; Can produce gradient foam materials; It can manufacture net products; The equipment is simple and easy to realize mass production.
The limitation is that only medium density foam aluminum with a pore range of 50%~80% can be obtained; Sodium chloride is easy to remain in the finished product, causing local corrosion of aluminum base; The process cycle is long.
1.5 Hollow three-dimensional skeleton method
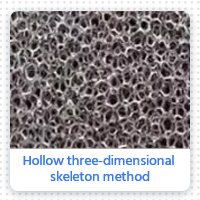
The liquid metal is diecasted into a ceramic with a hollow skeleton 3D mesh structure, cooled, and then the skeleton is removed.
The process includes:
Features: The porosity of foam is adjustable, the operation is cumbersome, the cost is slightly high, and the product range is limited, so its promotion and application are limited.
1.6 Fiber sintering
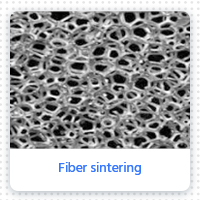
The process of this method is to first obtain aluminum wire by mechanical drawing or other methods, then make aluminum wire into felt ring by slurry casting or mechanical felt ring, and then sinter it to achieve the required strength and porosity.
The process is as follows:
The advantage of fiber sintering method is that it can obtain higher porosity than powder sintering. The structural properties of the material are maintained at the maximum porosity. At the same porosity, the strength and toughness of foam aluminum produced by this method are higher than those by powder metallurgy method. However, the cost of this method is high.
1.7 Slurry soaked sponge sintering method
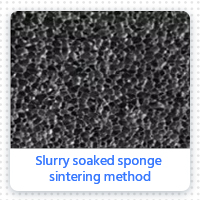
The method is to make spongy organic substances into organic precursors of the desired shape, and then use the slurry containing the metal aluminum powder to be processed to penetrate (the carrier of the suspension is water and organic liquid). The soaked organic precursor is dried to remove solvent, sintered and cooled to obtain foam aluminum with high porosity and three-dimensional structure.
The process flow is roughly as follows:
Features: It is mainly affected by the selection and pretreatment of organic precursors, the composition of slurry, the selection of additives, sintering temperature and other factors.
2. Solidification of liquid metal
This method is to produce foam structure through liquid aluminum. It can be directly foamed through aluminum liquid; Porous materials can also be obtained by casting foam materials or closely packed pore forming agents.
2.1 Direct blowing foaming method
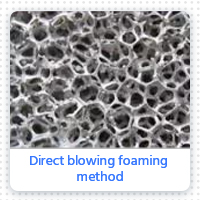
First, add the SiC, Al2O3, etc. into the molten metal, and uniformly dispersed to improve the melt viscosity. Then blow gas (such as nitrogen, inert gas, etc.) into the bottom of the melt. A large number of pores are formed in the liquid metal and then cooled and solidified.
Features: continuous preparation of products can be realized; Simple requirements for equipment; The porosity of the product is controllable; Low cost.
2.2 Foaming agent foaming method
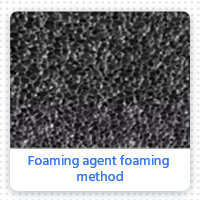
Add foaming agent into the aluminum melt and stir it evenly. Heat it to make the foaming agent decompose to produce gas. The gas expands and foams. After cooling, foam metal is obtained. The foaming agent used is usually metal hydride such as TiH2 or ZrH2.
Features: simple equipment requirements, low cost, and continuous product preparation. Short foaming time interval, difficult control of foaming temperature, uneven bubble distribution, poor product reproducibility, etc.
2.3 Seepage casting
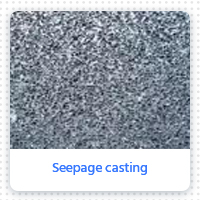
Percolation casting is to stack removable particles (such as NaCl) in the mold, press them into billets, pour metal after preheating, and then remove the particles to prepare a through-hole foam structure with interconnected holes.
Process principle:
Schematic Diagram of Vacuum Seepage Method Device
Features: The preparation process has controllable pore diameter parameters, high through-hole ratio, large specific surface area, low cost, and is suitable for large-scale industrial production. The disadvantage is that due to the high surface tension of liquid metal, the particles can not be completely wetted, so the gap between particles can not be completely filled.
2.4 Investment casting
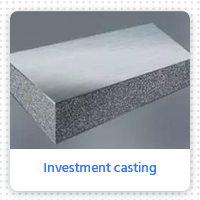
The investment casting method is to immerse the molded polymer foam material into the liquid refractory to fill the gap of the refractory. After the refractory is hardened, heating will vaporize and decompose the foam material to form a three-dimensional framework with the shape of the original foam material. Pour the molten aluminum into the casting mold, remove the refractory after solidification, and then obtain foam aluminum with three-dimensional mesh through holes.
Schematic diagram of process principle:
Schematic Diagram of Porous Materials Prepared by Investment Casting
Advantages: various foam metals can be prepared; Opening structure, good production repeatability and relatively stable density.
Disadvantages: low output; high price.
2.5 Solid-gas eutectic solidification
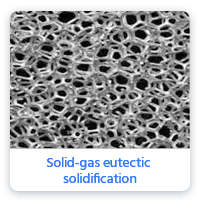
Many metal liquids can form eutectic systems with gases (such as hydrogen). If these metals are melted in a high-pressure hydrogen atmosphere, a uniform melt containing supersaturated hydrogen can be obtained. In the subsequent cooling and solidification process, the melt will undergo eutectic transformation and decompose into solid and gas phases. During directional solidification, because the solubility of hydrogen in the solid phase and liquid phase differs greatly, the supersaturated hydrogen will separate from the solid phase to form bubbles, thus obtaining the required foam aluminum.
Schematic Diagram of Process Principle:
Schematic Diagram of Solid Gas Eutectic Solidification Process for Preparing Porous Materials
Features: High porosity foam aluminum with isotropic and anisotropic pore shapes can be obtained by precisely controlling cooling conditions (pressure, cooling rate, heat dissipation direction).
2.6 Ball feeding method
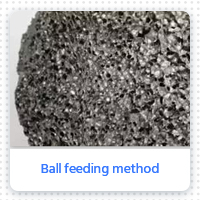
The method of adding ball material is to add particles or hollow balls into the aluminum alloy melt and strengthen the stirring. And casting while the melt is still in relative flow to obtain the composite of aluminum alloy and particles. Then the soluble particles in the aluminum alloy collective are dissolved and removed, and finally a connected porous foam aluminum is obtained.
The process flow is roughly as follows:
Features: The surface tension of liquid metal is high, and the particles or hollow balls cannot be completely wetted, so the gaps between particles cannot be completely filled. The structural continuity of the obtained foam aluminum is poor.
3. Metal deposition
3.1 Electrodeposition
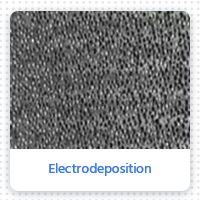
The principle is that foam aluminum is electroplated in alkyl aluminum solution with pretreated foam plastic as cathode and industrial pure aluminum plate as anode.
Process flow of electrodeposition method:
Features: easy to control pore structure, small pore size, uniform pore size, high porosity, and its heat insulation and damping characteristics are better than that of foam aluminum produced by casting method. However, this method has long process, complicated operation, slightly high cost and limited product thickness, so its popularization and application are limited.
3.2 Vapor phase evaporation deposition method
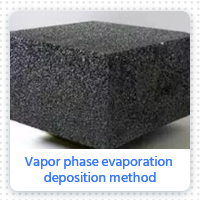
This method is to slowly evaporate the metal aluminum in a high inert atmosphere (102~104Pa). The evaporated metal atoms collide and scatter with the inert gas molecules, rapidly losing kinetic energy. This process is shown in the macroscopic view as the metal vapor temperature decreases. Then the evaporated metal atoms combine with each other to form atomic clusters before reaching the substrate, so "metal smoke" can be seen in the evaporation process. These clusters continue to cool down and deposit on the substrate with inert gas. Because atoms at low temperature are difficult to migrate or diffuse, "metal smoke" particles are loosely stacked to form a hollow foam structure.
Schematic Diagram of Process Principle:
Schematic Diagram of Vapor Phase Evaporative Deposition Process
Features: The formation of metal foam is affected by many factors, such as metal materials, heating power, inert gas pressure, type of vaporization source heater and its distance from the substrate, and substrate materials. The heating power, inert gas pressure and inert gas flow rate are the most important control parameters.
3.3 Splash deposition
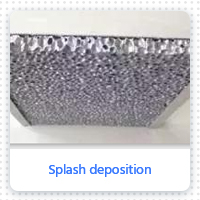
Splashing deposition is to evenly spray the powder with inert gas onto the aluminum alloy metal by using the spraying technology. Then it is heated to the melting point of the metal, so that the gas added to the metal expands and forms uniformly distributed and dense holes. After cooling, it is made of foam aluminum products with dense network.
Schematic diagram of process principle:
Schematic Diagram of Splash Deposition
Features: By controlling the partial pressure of inert gas in deposition, the volume fraction of pores of the obtained product can be controlled.
3.4 Molten salt electroplating
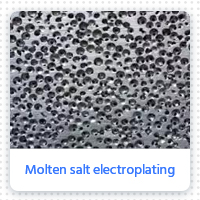
Foam aluminum is prepared by electrodeposition in molten salt with foamed plastic as cathode and aluminum plate as anode.
Schematic diagram of process principle:
Schematic Diagram of Electroplating Process Principle
Features: foam aluminum has high porosity and even pores.
4. Others
The following methods are mainly used for scientific research or small batch trial production, and are not widely used in industrial production.
4.1 Secondary foaming method
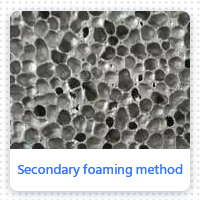
The secondary foaming method is a preparation method of foam aluminum that combines the advantages of powder metallurgy foaming method and melt foaming method. The technical process is to add viscosity increasing agent (Ca, Al2O3, etc.) into the aluminum melt and stir it evenly. Add foaming agent (pretreated TiH2) under appropriate temperature and viscosity conditions. It is uniformly dispersed, and the melt is cast into the mold for rapid cooling and solidification before TiH2 is decomposed to obtain foaming precursor. When the foaming precursor is heated to a certain temperature, TiH2 in the precursor begins to decompose and foam, and finally foam aluminum is prepared.
4.2 Metal hollow ball method
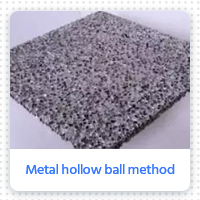
The method is to form a porous structure by bonding metal hollow spheres together through sintering. Metal hollow spheres can be obtained by chemical synthesis and electrodeposition of a layer of metal on the surface of polymer spheres, and then the polymer spheres are removed.
There are many preparation processes of foam aluminum, and each method has its own advantages and disadvantages. In practical production, melt foaming method, percolation casting method, powder metallurgy foaming method and electrochemical method are widely used. Other processes are mainly used for scientific research or small batch trial production.
Chalco can provide you the most comprehensive inventory of aluminum products and can also supply you customized products. Precise quotation will be provided within 24 hours.
Get a quote