When welding aluminum alloys, which one should you choose between 4043 and 5356?
In aluminum alloy welding projects, whether it is manufacturing engineers, welding technicians, or purchasing personnel, the most common technical selection question they face is: "4043 or 5356?"
These two alloys are among the most commonly used aluminum welding wire materials, commonly used for MIG welding and TIG filling. However, they have obvious differences in chemical composition, welding performance, weld appearance, crack resistance, strength performance and anodizing compatibility. If they are not properly selected, it will not only affect the quality of the weld, but may also shorten the service life of parts or cause post-processing failure.
This article will help you quickly determine which alloy is more suitable for your project needs by systematically comparing the technical parameters and actual application scenarios of 4043 and 5356 welding wires, and attach specific product recommendations to help you select aluminum welding materials more professionally and efficiently.
Comparison of chemical composition and basic properties
Although both 4043 and 5356 are classified as aluminum welding wires, they are essentially two different types of aluminum alloy systems, and their chemical composition and metallographic properties directly determine their behavior during the welding process.
Chemical composition comparison (typical values) Standard reference: AWS A5.10, ISO 18273 | ||
Composition elements | 4043 (AlSi5) | 5356 (AlMg5) |
Silicon | 4.5–6.0% | ≤ 0.25% |
Magnesium | — | 4.5–5.5% |
Manganese Mn | — | 0.05–0.20% |
Iron | ≤ 0.8% | ≤ 0.4% |
Copper | ≤ 0.3% | ≤ 0.1% |
Zinc | ≤ 0.1% | ≤ 0.25% |
Titanium | ≤ 0.2% | ≤ 0.2% |
Other impurities | ≤ 0.15% | ≤ 0.15% |
Aluminum | margin | margin |
4043 belongs to the Al-Si series alloys. Its high silicon content gives it good fluidity and crack resistance, making it the preferred choice for welding 6 series aluminum (such as 6061).
series aluminum welding (such as 5083 and 5052) with higher structural strength requirements .
Welding performance comparison: crack resistance, fluidity, strength, anodizing performance
Although 4043 and 5356 are both common aluminum welding wire alloys, in actual welding operations, they have significant differences in molten pool performance, weld strength, crack sensitivity, and subsequent processing.
Molten pool fluidity
Alloy | Molten pool fluidity | Weld seam performance |
4043 | ✅Excellent | Wide and smooth weld seam for easy handling |
5356 | Poor | The weld is "harder", the fluidity is slightly poor, and the forming is slightly rough |
Note: 4043's high silicon content lowers its melting point (about 573°C), making welding easier to control; 5356 has a higher melting point (about 630°C), but is stronger.
Crack resistance
Alloy | Hot crack sensitivity | Recommended base material |
4043 | ✅Strong crack resistance | Recommended for highly crack-sensitive materials such as cast aluminum, 6061, 6082 |
5356 | Slightly worse (when magnesium content is higher) | Applicable to 5xxx series and some heat treatable aluminum alloys |
Weld strength
Alloy | Weld tensile strength (reference) | Ductility |
4043 | 170–190 MPa | Medium ( extension about 6–10%) |
5356 | ✅ 250 – 280 MPa | Higher (elongation can reach 11–18%) |
Note: If the project has high strength requirements (such as structural parts and containers), 5356 is preferred; if crack resistance is required, 4043 is preferred.
Weld color and anodizing compatibility
Alloy | Weld color | Effect after anodizing |
4043 | Gray black | ❌Not suitable for anodizing, the color difference is obvious |
5356 | Silver | ✅Close to the base material color, suitable for decorative applications after anodizing |
Note: If the welded parts need anodizing treatment (such as building curtain walls, decorative panels), 5356 is recommended; if no surface treatment is involved, 4043 is easier to weld.
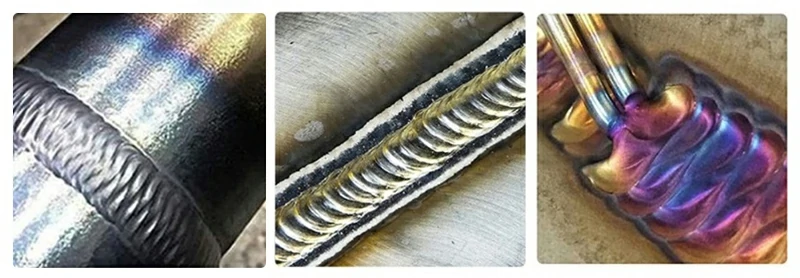
Comparison of typical application scenarios and parent material recommendations
In order to help you more intuitively judge the applicability of 4043 and 5356 aluminum welding wires, the following is a systematic comparison and recommendation based on common aluminum alloy base materials, welding scenarios and project types.
Common aluminum base material recommended adaptation table | ||
Base material type | Recommended welding wire | Recommended reason |
6061 / 6063 (6 series aluminum) | 4043 / 4943 | Good welding crack resistance and high process stability; suitable for structural parts, industrial frames, etc. |
5052 / 5083 (5 series aluminum) | 5356 / 5183 | High strength, corrosion resistance, suitable for ships, fuel tanks, rail transit parts |
Cast aluminum ( A356 / 319, etc.) | 4043 | Excellent crack resistance, the first choice welding wire for casting repair |
Decorative parts that require anodizing | 5356 | The weld color is close to the base metal, and the anodizing effect is more consistent |
Load-bearing parts with strength requirements | 5356 / 5183 | Higher tensile strength, suitable for industrial equipment, brackets and other structural parts |
Need machining after welding | Both | 4043 is recommended, which has good fluidity, regular shape and is easy to cut. |
Recommended application scenarios for Chalco 5356 welding wire and 4043 welding wire
If the welding object requires both aesthetics and certain strength and corrosion resistance, you can consider using a variety of welding wires in combination, or upgrading to enhanced alloys such as 4943 and 5183.
Automobile fuel tank and body parts welding
Recommended welding wire: 5356
It has good corrosion resistance and structural strength, is suitable for welding thin-walled profiles, and is widely used in lightweight components for commercial vehicles and new energy vehicles.
Ship hull and marine engineering component welding
Recommended welding wire: 5356 / 5183
Magnesium alloy welding wire has excellent salt spray resistance and strength retention ability, suitable for continuous welding, high reliability structural parts, and meets offshore and heavy load requirements.
Aluminum door and window frames and anodized decorative parts welding
Recommended welding wire: 5356
The color of the weld is close to that of the base material, and the overall appearance is consistent after anodizing, which is suitable for architectural aluminum structures with high aesthetic requirements.


Welding of cast aluminum housing and aluminum casting repair (such as motor housing)
Recommended welding wire: 4043
It has a low melting point and strong crack resistance, and is particularly suitable for welding and structural repair of cast aluminum parts. It has a wide welding process window and is easy to operate.
Precision instrument housing, small aluminum structure welding
Recommended welding wire: 4043
The molten pool has good fluidity and regular formation, and is a commonly used filling material for TIG precision welding.
TIG welding thin plate butt welding
Recommended welding wire: 4043 / 4943
In the TIG process, the weld is beautifully formed and the heat-affected zone is small. 4943 has fluidity while also improving weld strength, making it suitable for 6061 thin plates, etc.


Comparison of weld appearance and anodizing compatibility
In addition to welding strength and crack resistance, many projects also consider the color matching of the weld and the uniformity after anodizing. Especially in applications such as aluminum doors and windows, decorative panels, elevator panels, and display racks, whether the welding is "visible" becomes an important criterion for material selection.
Weld color contrast
Alloy | Weld color (untreated after welding) | Proximity to parent material |
4043 | Gray black/ dark gray silver | ❌Obvious color difference |
5356 | Silvery white/similar to the original color of the base material | ✅ Smaller color difference |
Since 4043 contains a high silicon content, the weld tends to form a dark gray alloy structure during the cooling process, while 5356 contains magnesium and can present a bright metallic color, which is close to typical aluminum profiles.
Anodizing compatibility
Alloy | Performance after anodizing | Is it suitable for anodizing? |
4043 | The color difference is further amplified, and the oxide film adsorption is uneven | ❌Not recommended for anodizing projects |
5356 | Can form an oxide film consistent with the base material with small color difference | ✅Recommended for scenes requiring surface treatment |
Some customers in the market who have extremely high requirements for anode consistency will also choose laser welding + 5356 or combined with 4045 cladding alloy materials for welding to improve the consistency of anode effects.
Practical suggestions for material selection
- If the weld needs to be anodized in the end (such as building decorations, elevator panels, etc.), 5356 welding wire should be preferred, or the weld should be shielded within the allowable range of the structure.
- If the project does not require surface treatment or focuses on process stability (such as equipment welding, internal structure), 4043 can be given priority, as it is more weld-friendly.
Procurement suggestions and welding wire selection recommendations
Judging from the parent material
- Welding 6061, 6063, cast aluminum → 4043 is recommended (good crack resistance)
- Welding 5052, 5083, 5 series aluminum alloys → 5356 is recommended (high strength, corrosion resistance)
- Anodizing required → 5356 is recommended (color is more consistent)
Judging from the process/usage scenario
- TIG process, small parts, need to be formed regularly → 4043 or 4943 is recommended
- MIG high efficiency welding / strong structural parts → Recommend 5356
- Batch manufacturing/Automated welding → 4043/5356 are both available in coils, suitable for mainstream equipment on the market
Product form options
- ER4043 / ER5356 welding wire, available in TIG and MIG specifications
- Conventional wire diameters: 0.8mm, 1.0mm, 1.2mm, 1.6mm, 2.4mm, etc.
- Packaging: 1kg~15kg reel/bucket/sample supply
If you are not sure about alloy selection, welding base material or have special requirements for packaging and customized ratio, please contact Chalco technical sales team directly, we will provide you with one-to-one welding material solution support.
Instant Quote